NASA is at the forefront of advanced polymer research, developing innovative materials that can withstand extreme conditions in space. This research is not only crucial for the successful exploration of the cosmos, but it also has numerous applications on Earth. With its focus on developing high-performance, durable, and environmentally friendly materials, NASA is paving the way for a more sustainable and innovative future. Through technology licensing and commercialization, these materials can give businesses a competitive edge. Below, we've highlighted a small sample of industry-applicable advancements in our patent portfolio.
Micro-Scale Surface Molding using Soft Lithography for Polymer and Composite Parts
NASA researchers have developed a "soft-lithography" technology to mold micro-scale structures into polymer and composite parts. This method involves using an elastomer mold and liquid resin to create a rigid inverse replica of the mold. The resulting micro-scale structures have many benefits and applications, including super-hydrophobic surfaces, improved adhesion between composite parts, and reduced drag in aerodynamic and hydrodynamic applications. These features provide protection against contamination and environmental degradation, improve overall performance and efficiency, and offer solutions for various industrial and scientific applications.

Single-Walled Carbon Nanotubes in Polymer Matrices
Researchers at NASA's Langley Research Center have developed a method for stabilizing carbon nanotubes (CNTs) in a polymer matrix. This process uses electrostatic interactions between the polymer and the nanotubes, which results in a strong, stable bond without damaging the CNTs. This technology provides a simple and efficient method for mass-producing multifunctional nanocomposites with a wide range of potential commercial applications.
Low Creep, Low Relaxation Fiber-Reinforced Polymer Composites
NASA has developed a fiber-reinforced polymer composite that reduces viscoelastic creep and improves the molecular integrity of polymer-based beams over time. The researchers achieved this by tailoring the molecular structure of epoxy resins, incorporating secondary additives, and adjusting composite architecture. The technology reduces relaxation in the modified molecular structure to as low as 5% after two years, compared to 49% for commercially available options. The technology can have significant benefits for industries using inflatable and deployable beams and masts.
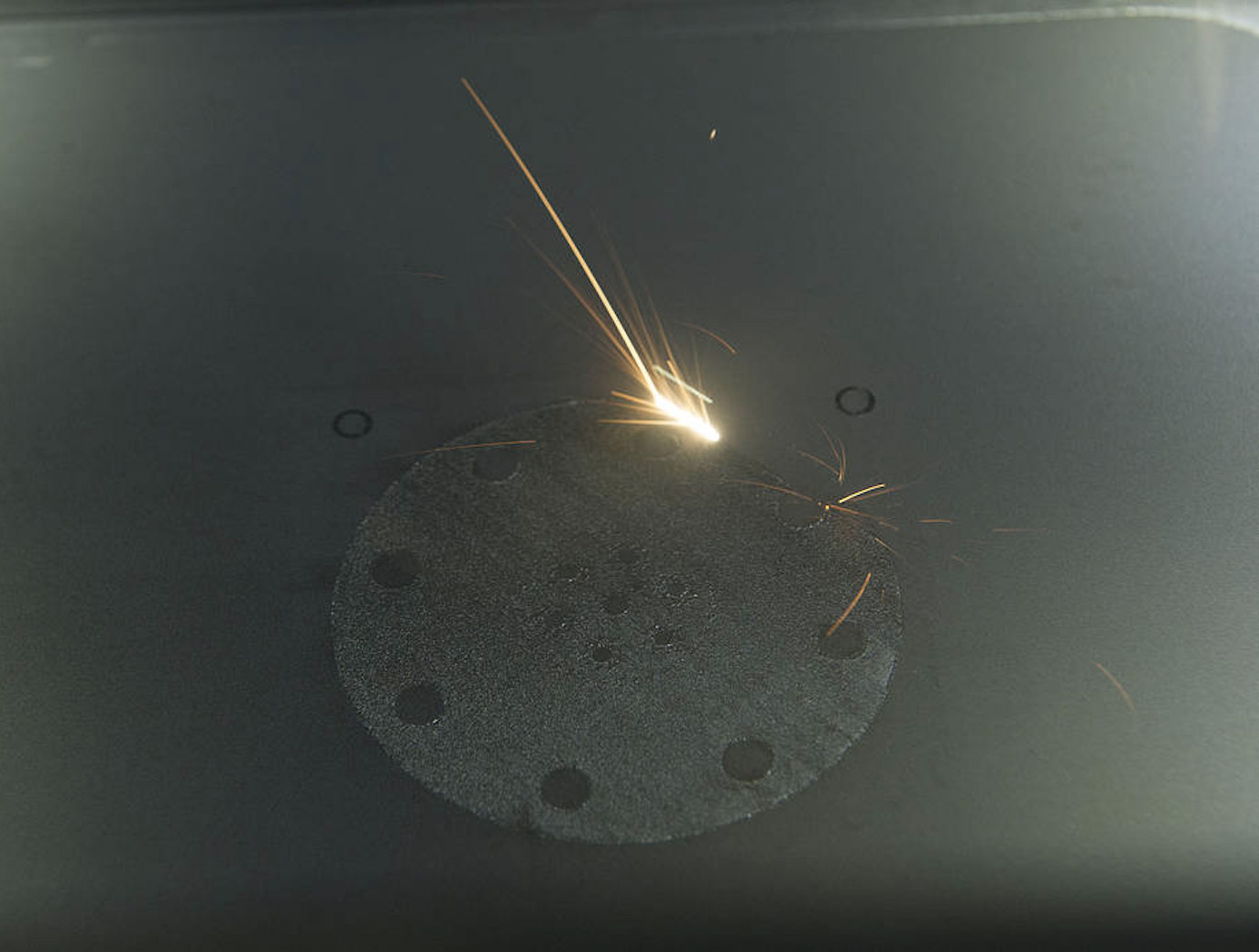
3D-Printed Composites for High Temperature Uses
In partnership with the University of Louisville and the U.S. Air Force, NASA Glenn Research Center has created an advanced additive manufacturing method to produce composite parts with high-temperature endurance. The technology uses a special thermoset polyimide resin called RTM370 imide resin that is filled with carbon fibers and processed with selective laser sintering (SLS) to produce a high-performance composite part. The end result can withstand temperatures over 300°C and is suitable for high-temperature aerospace applications. This new SLS process is a game-changer in the field of additive manufacturing as it offers a low melting temperature solution to produce high-performance composites with complex geometries.
Stay connected and stay informed with NASA Tech Transfer! Follow us on LinkedIn, Facebook, and Twitter to stay on top of all our new technology offerings and industry updates. And if you want to ensure you never miss a beat, sign up for our newsletter and receive exclusive announcements about our upcoming events.