Robotic gripper for satellite capture and servicing
robotics automation and control
Robotic gripper for satellite capture and servicing (GSC-TOPS-190)
An essential tool for autonomous rendezvous and capture of satellites
Overview
The robotic gripper was developed at NASA Goddard Space Flight Center as part of a robotic satellite servicing mission. The gripping device can be used to autonomously or remotely grasp and control an out-of-fuel or otherwise disabled satellite. Specifically, the gripper interfaces to the separation ring (marman ring) of the client spacecraft and when closed is sufficient to constrain all six degrees of freedom of motion between the servicing spacecraft and the client. The jaws are designed with a conformable geometry which allows the same Gripper to interface to all spacecraft separation rings commonly used with Atlas V and Delta IV launch vehicles.
The Technology
The Gripper is located at the end of a robotic system consisting of a robotic arm equipped with a Tool Drive or End Effector comprising the input actuator to the Gripper as well as the structural, power and data link between the Gripper and the robotic arm. In a notional concept of operations, a Servicer would approach the Client in an autonomous rendezvous and capture (AR&C) maneuver. When the Servicers sensor suite confirms that the distance, orientation, and relative translational and angular rates with respect to the Client are within an acceptable range, the Servicer enables the grasping sequence, where the robotic arm, equipped with Gripper, extend forward to the Client. When the Gripper/ Servicer sensors indicate that the Client marman ring is sufficiently within the capture range of the Gripper, a trigger signal is sent to the robot control system that commands the End Effector to drive the mechanism of the Gripper and affect closure around the marman ring. The Gripper consists of a pair of jaws which are driven by an internal transmission. The transmission receives input torque from the End Effector and converts the torque to appropriate motion of the jaws.
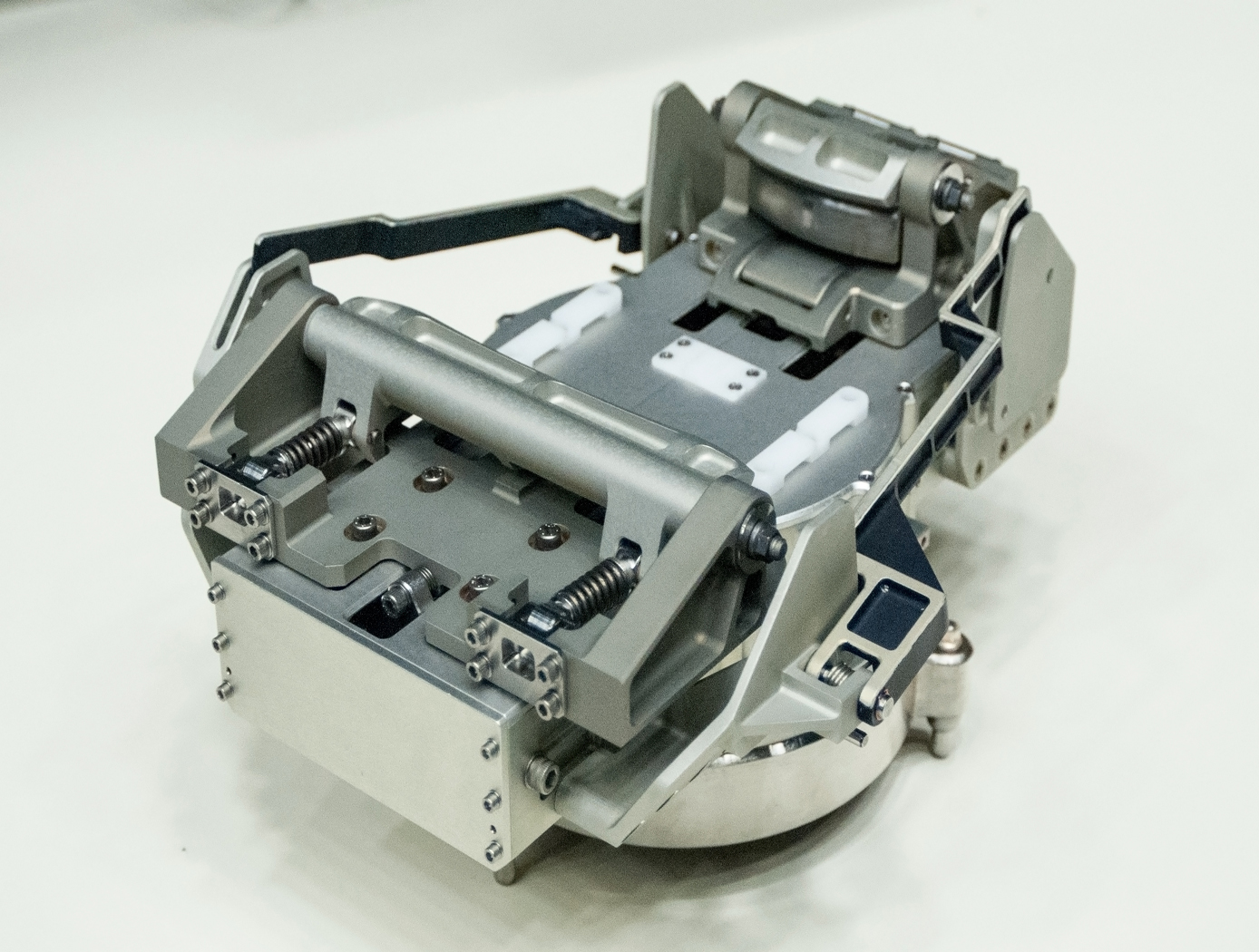
Benefits
- Satellite capture and constraint for servicing or refueling
Applications
- Sufficient to constrain all six degrees of freedom of motion of a client spacecraft
- Enables servicing craft to perform primary attitude control for the dual vehicle stack
- Compatible with all spacecraft separation rings commonly used with Atlas V and Delta IV launch vehicles
Technology Details
robotics automation and control
GSC-TOPS-190
GSC-16932-1
Similar Results

Method and Associated Apparatus for Capturing, Servicing, and De-Orbiting Earth Satellites Using Robotics
This method begins with the optical seeking and ranging of a target satellite using LiDAR. Upon approach, the tumble rate of the target satellite is measured and matched by the approaching spacecraft. As rendezvous occurs the spacecraft deploys a robotic grappling arm or berthing pins to provide a secure attachment to the satellite. A series of robotic arms perform servicing autonomously, either executing a pre-programmed sequence of instructions or a sequence generated by Artificial Intelligence (AI) logic onboard the robot. Should it become necessary or desirable, a remote operator maintains the ability to abort an instruction or utilize a built-in override to teleoperate the robot.

Robo-Glove
Originally developed by NASA and GM, the Robo-Glove technology was a spinoff of the Robonaut 2 (R2), the first humanoid robot in space. This wearable device allows the user to tightly grip tools and other items for longer periods of time without experiencing muscle discomfort or strain. An astronaut working in a pressurized suit outside the space station or an assembly operator in a factory might need to use 15 to 20 lbs of force to hold a tool during an operation. Use of the Robo-Glove, however, would potentially reduce the applied force to only 5 to 10 lbs.
The Robo-Glove is a self-contained unit, essentially a robot on your hand, with actuators embedded into the glove that provide grasping support to human fingers. The pressure sensors, similar to the sensors that give R2 its sense of touch, are incorporated into the fingertips of the glove to detect when the user is grasping an object. When the user grasps the object, the synthetic tendons automatically retract, pulling the fingers into a gripping position and holding them there until the sensor is released by releasing the object. The current prototype weighs around two pounds, including control electronics and a small display for programming and diagnostics. A lithium-ion battery, such as one for power tools, is used to power the system and is worn separately on the belt.

Lunar Surface Manipulation System
NASA Langley developed the LSMS because of the need for a versatile system capable of performing multiple functions on the lunar surface, such as unloading components from a lander, transporting components to an operational site and installing them, and supporting service and replacement during component life. Current devices used for in-space operations are designed to work on orbit (zero g) only and thus do not have sufficient strength to operate on planetary surfaces. Traditional cranes are specialized to the task of lifting and are not capable of manipulator-type positioning operations.
The innovations incorporated into the LSMS allow it to lower payloads to the ground over a significant portion of the workspace without use of a hoist, functioning like a robot manipulator, thus providing a rigid connection and very precise control of the payload. The LSMS uses a truss architecture with pure compression and tension members to achieve a lightweight design. The innovation of using multiple spreaders (like spokes in a wheel) allows the LSMS to maintain its high structural efficiency throughout its full range of motion. Rod portions of the tension members automatically lift off and re-engage the spreaders as the joint articulates, allowing a large range of motion while maintaining mechanical advantage. In addition, the LSMS uses a quick-change device at the tip end that enables automated acquisition of end effectors or special purpose tools to increase its versatility.

Circumferential Scissor Spring Enhances Precision in Hand Controllers
The traditional scissor spring design for hand controllers has been improved upon with a circumferential spring controller mechanism that facilitates easy customization, enhanced durability, and optimum controller feedback. These advantages are partially facilitated by locating the spring to the outside of the mechanism which allows for easier spring replacement to adjust the deflection force or for maintenance.
The new mechanism is comprised of two rounded blades, or cams, that pivot forward and back under operation and meet to form a circle. An expansion spring is looped around the blade perimeter and resides in a channel, providing the restoring force that returns the control stick to a neutral position. Due to the use of a longer circumferential spring, the proportion of spring expansion is smaller for a given distance of deflection, so the forces associated with the deflection remain on a more linear portion of the force deflection curve.
The Circumferential Scissor Spring for Controllers is at technology readiness level (TRL) 8 (actual system completed and flight qualified through test and demonstration) and is available for patent licensing. Please note that NASA does not manufacture products itself for commercial sale.

Foot Pedal Controller
The Foot Pedal Controller enables an operator of a spacecraft, aircraft, or watercraft, or a simulation of one in a video game, to control all translational and rotational movement using two foot pedals. This novel technology allows control across all six degrees of freedom, unlike any technology on the market. The components of the technology are a support structure, a left foot pedal, a right foot pedal, and supporting electronics. The Foot Pedal Controller is intuitive, easy to learn, and has ergonomic features that accommodate and stabilize the operator's feet. A working prototype is available to demonstrate key technology features to potential licensees.
The Foot Pedal Controller technology could be used in designs for the flight deck of the future, video game controls, drone operations and flight simulators. This technology can be useful in any application where it is preferred or desirable to use the feet to control motion rather than using the hands. A potential market could be foot control of equipment by people with arm or hand disabilities. A unique aspect of the innovation is the consideration of natural foot mechanics in the design and placement of the sensors and actuators to reduce operator fatigue. The axes of rotation of the Controller align with the joints of the foot so the foot moves naturally to control the movement of the craft. NASA seeks collaborations with companies interested in licensing and partnering to further develop and commercialize the technology.