Silicon Oxide Coated Aluminized Polyimide Film Radiator Coating
materials and coatings
Silicon Oxide Coated Aluminized Polyimide Film Radiator Coating (GSC-TOPS-249)
A thermal coating by tailoring the absorptance and emittance of silicon oxide (SiOx) coated aluminized polyimide film for CubeSat thermal management
Overview
A miniature satellite, or CubeSat, has deployable solar arrays and/or body mounted solar cells to generate adequate electrical power to meet mission power requirements. The CubeSats internal components dissipate heat. In order to maintain the component temperatures within allowable flight limits, the waste heat needs to be radiated from its exterior to deep space. Depending on the orbit parameters, one or more of the exterior surfaces could be exposed to sunlight, planet albedo (reflection of solar radiation from Earth), or infrared radiative flux. Additionally, lithium ion batteries, often used on CubeSats, are required to be above 0 C during charging. Conventionally, a combination of radiator thermal coatings, multilayer insulation (MLI) blankets, and active heater control are used to meet component thermal requirements, which are all relatively expensive. Furthermore, MLI blankets not only increase the volume of the CubeSat, but also increase the risk of entanglement during solar array deployment. The SiOx Coated Aluminized Polyimide Film Radiator Coating regulates temperature for CubeSats without these drawbacks.
The Technology
The SiOx Coated Aluminized Polyimide Film Radiator Coating uses all the exposed surfaces on the six sides of a CubeSat as radiators. All the internal components are thermally coupled to the radiators. Waste heat from the internal components is transferred by conduction to the radiators through its aluminum structure or frame. SiOx thin film coated aluminized polyimide film is used as the radiator coating. Its total thickness is approximately 0.05 mm, which is predominately the polyimide film thickness. Polyimide film is known commercially as Kapton. The coating is bonded to the CubeSat exterior by using an acrylic transfer adhesive.
SiOx Coated Aluminized Polyimide Film Radiator Coatings absorptance and emittance can be tailored to meet the component thermal requirements by altering the SiOx thickness. Since the SiOx is a thin film, altering its thickness has no significant effect on the total thickness of the radiator coating. An indium tin oxide (ITO) thin film can be added to make the coating conductive, if needed, without affecting the absorptance or emittance. This coating, with or without ITO, can be used for various CubeSat applications. By tailoring the absorptance and emittance of this coating, external MLI blankets and active heater control are eliminated. The thermal connection between heat generating components and the battery eliminates the need for a battery heater.
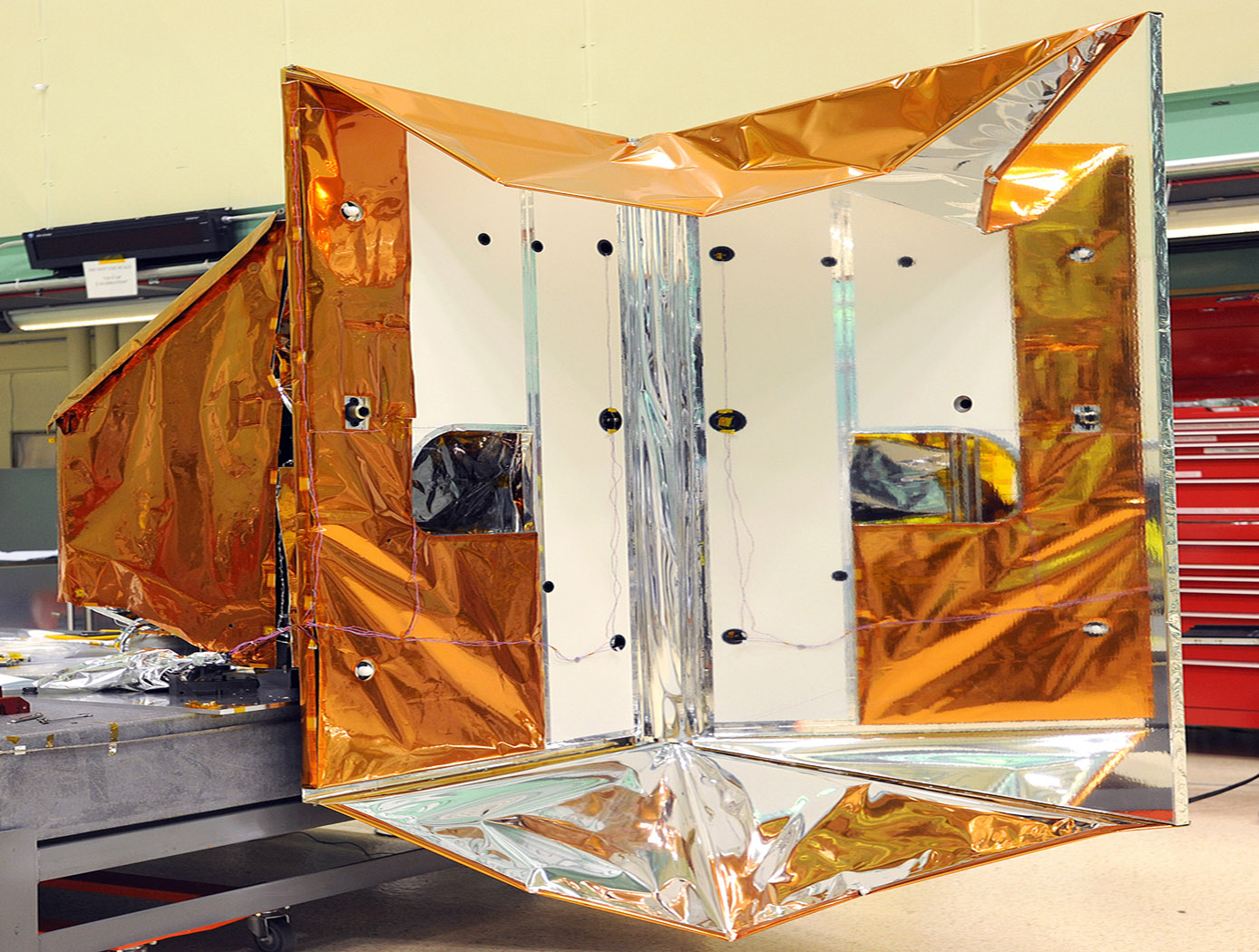
Benefits
- Lowers power demand
- Eliminates the need for voluminous heat regulation
Applications
- Satellite manufacturing
- Thermal management and regulation
Technology Details
materials and coatings
GSC-TOPS-249
GSC-18217-1
Similar Results

CubeSat Form Factor Thermal Control Louvers
Thermal control of small spacecraft, including CubeSats, is a challenge for the next era of NASA spaceflight. Science objectives and components will still require strict thermal control while smaller volumes will inherently absorb and shed heat more quickly than a larger body. Thus, game-changing technologies must be developed to stabilize the thermal environment inside of small spacecraft.
The CubeSat louver assembly of the present invention is based upon the proven designs of full-sized louvers for large spacecraft. Internal spacecraft components are thermally coupled to the side of the spacecraft. Bimetallic springs serve as a passive control mechanism for opening and closing flaps. As the spacecraft heats up the springs expand due to the difference in thermal expansion rates of their two fused metals (hence bimetallic). This opens the flaps, changing the thermal radiation properties of the exterior surface. As the spacecraft cools the flaps close and return the exterior surface to the previous emissivity. These temperature-driven adjustments create a more stable thermal environment for components.
The power dissipated via the thermal louvers shows a substantial difference between fully closed and fully open louvers at the high temperatures significant for electrical components.

Portable Compact Thermionic Power Cell
This compact thermionic cell (CTI) technology can be manufactured efficiently and economically using existing semiconductor fabrication technology. Its design consists of a top electron collector, separated by a vacuum gap from an electron emitter adjacent to the heat source, a thin plate of 238Pu enclosed by a thin-film insulator to protect the emitter and collector layers from overheating by the 238Pu. For a smart phone battery size, the invented compact thermionic (CTI) cell requires about 5 g maximum of 238Pu. Such small quantities are more readily available and producible, and could be reused for recycling when the CTI cell is dismantled. The emitter surface is topologically modified to have array of spikes, achievable using current semiconductor microfabrication technology. Various other geometries of emitter plates may also be used, such as an array of ridges. The smaller the emitter tips, the higher the voltage concentration.

Novel Radiation Shielding Material for Dramatically Extending the Orbit Life of Cubesats
A high density metal, such as tantalum or tungsten is coated onto thin aluminum sheet in precise ratios and thicknesses. The combined sheet is then easily formed into standardized enclosures compatible with CubeSat design and performance specifications.

Diminutive Assembly for Nanosatellite deploYables (DANY)
SmallSat designers seek to employ restraints and release mechanisms of minimal size and weight, often placing each on the outside of the SmallSat structure. Surprisingly, "fishing line" (released via burn through) is often used to secure and release deployables. Vibrations and forces generated during launch can stretch the fishing line, thus allowing these precious deployables to become damaged or otherwise not release properly later on. While these small sats are less expensive than their larger counterparts, satellite owners must minimize the chance that deployables are damaged or that deployment is unsuccessful.
Five years ago, engineers at NASA GSFC faced these SmallSat deployment challenges and knew a better way must exist to prevent equipment damage and ensure successful release. Investigating a host of designs to minimize size, weight, and cost while maximizing communication and mechanical reliability, NASA's engineers created DANY (the Diminutive Assembly for Nanosatellite deploYables). NASA's DANY technology uses spring-loaded metal pins, a reliable burn-through mechanism, efficient bracketing, and a circuit board - all within a 3.0" x 1.3" x 0.2" volume (smaller than a stack of 10 business cards) - to reliably stow and release deployables on command. Using DANY, stowed deployables are securely fastened using the spring-loaded locking pins. Upon receiving a deployment signal, a plastic restraining link is burned through which allows the spring-loaded pins to release the deployable and simultaneously trigger a switch to signal a successful deployment event.

CubeSat Compatible High Resolution Thermal Infrared Imager
This dual band infrared imaging system is capable of spatial resolution of 60 m from orbit and earth observing expected NEDT less than 0.2o C. It is designed to fit within the top two-thirds of a 3U CubeSat envelope, installed on the International Space Station, or deployed on other orbiting or airborne platforms. This infrared imaging system will utilize a newly conceived strained-layer superlattice GaSb/InAs broadband detector array cooled to 60 K by a miniature mechanical cryocooler. The camera is controlled by a sensor chip assembly consisting of a newly developed 25 m pitch, 640 x 512 pixel.