Self-Healing Wire Insulation
electrical and electronics
Self-Healing Wire Insulation (KSC-TOPS-51)
Microcapsules release healant that repairs minor cuts, nicks, and abrasions
Overview
NASA's Kennedy Space Center is seeking commercial partners for licensing or further development of a novel high performance, flexible, low-melt polyimide film with self-healing properties. The self-healing properties of the film are provided by embedded microcapsules containing a solvent soluble polyimide. When cut or otherwise damaged, these capsules release their contents which dissolve and heal the damaged area.
Aerospace and ground vehicles often contain miles of high performance electrical wire insulation which are prone to damage from abrasion and cuts during vehicle operation and maintenance. Large portions of this wire are often buried within the vehicle framework, making it very difficult and time consuming to locate and repair damage. Incorporation of a self-healing capability in the insulation of this wire would provide self-repair of minor nicks, cuts, and abrasions without maintainer intervention and help reduce the danger of electrical shorts that could lead to sparking and fires.
The Technology
Insulation is necessary on electrical wires in order to protect electrical systems from shorting. In high voltage systems such shorting can lead to sparking and fires. Many lives have been lost due to electrical wire insulation failure. Many man hours are also expended in the repair and inspection of electrical wiring in order to attempt to prevent wire failure. Wire insulation with a built in "self-healing" capability would greatly improve the safety of systems containing electrical wiring. Such insulation would require far less inspection and repair time over the lifetime of the system.
Polyimides such as Kapton are an integral part of high performance electrical wire insulation. Traditional polyimides are very inert to solvents and do not melt. A new set of polyimides, developed for use as films for the manual repair of high performance electrical wire insulation, have a low melting point and can be dissolved in special solvents. These properties can be taken advantage of in self-healing polyimide films. Microcapsules containing a solvent soluble polyimide are prepared using industry standard inter-facial or in situ polymerization techniques. These capsules are then incorporated into a low melt polyimide film for use as either a primary electrical wire insulation or as one of several layers of a composite wire insulation. The low melt polyimide film substrate in which the microcapsules are incorporated has good solubility with the solvent used to dissolve the polyimide which makes up the fluid inside the microcapsule. Such a capsule filled insulation, when cut or otherwise damaged, will result in the release of the capsule contents into the cut or damage area. The solvent then dissolves a small amount of the surrounding polyimide insulation but will also begin the process of evaporation. The combination of these two processes allows for excellent intermingling of the healant and the surrounding substrate, resulting in a repair with superior bonding and physical properties.
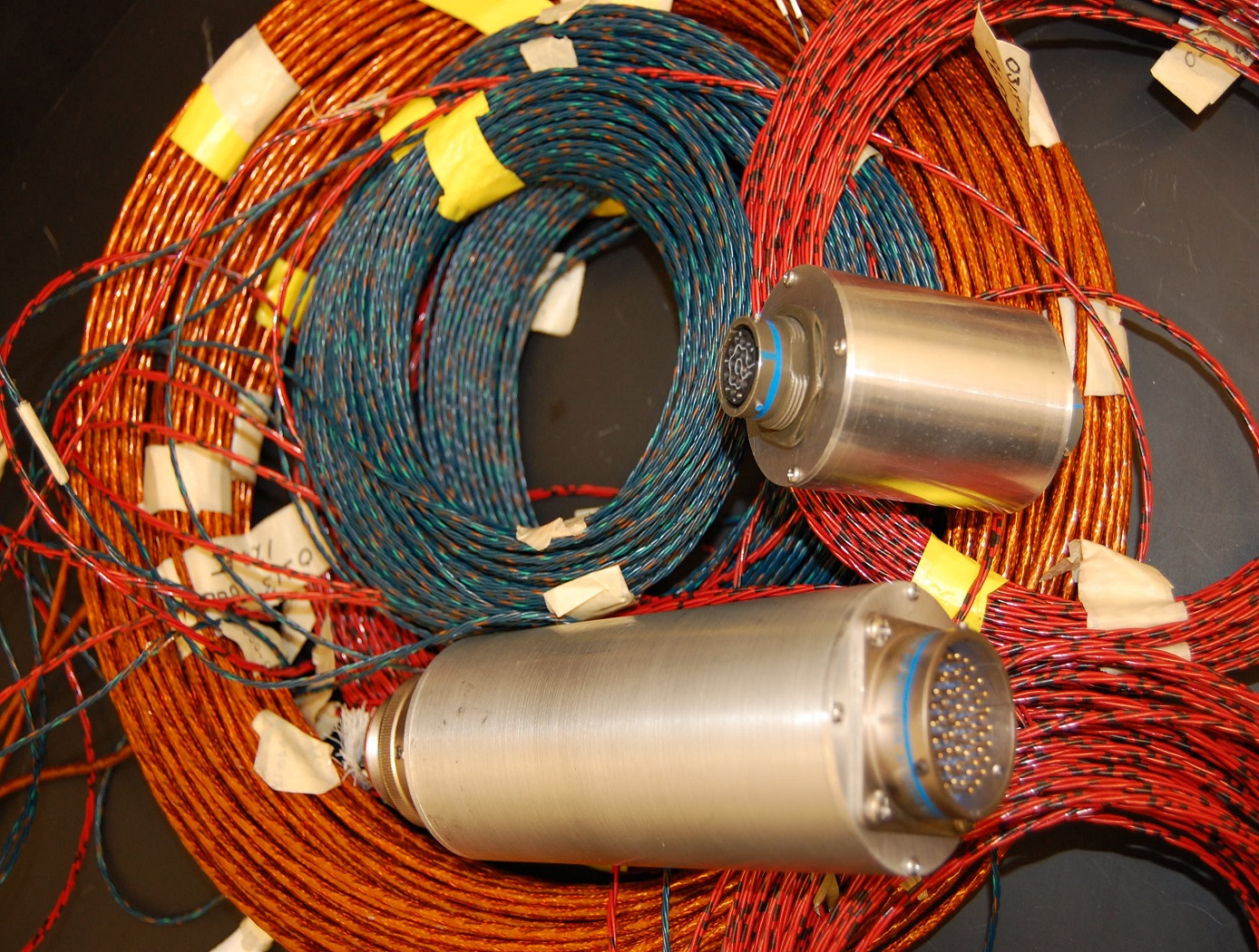
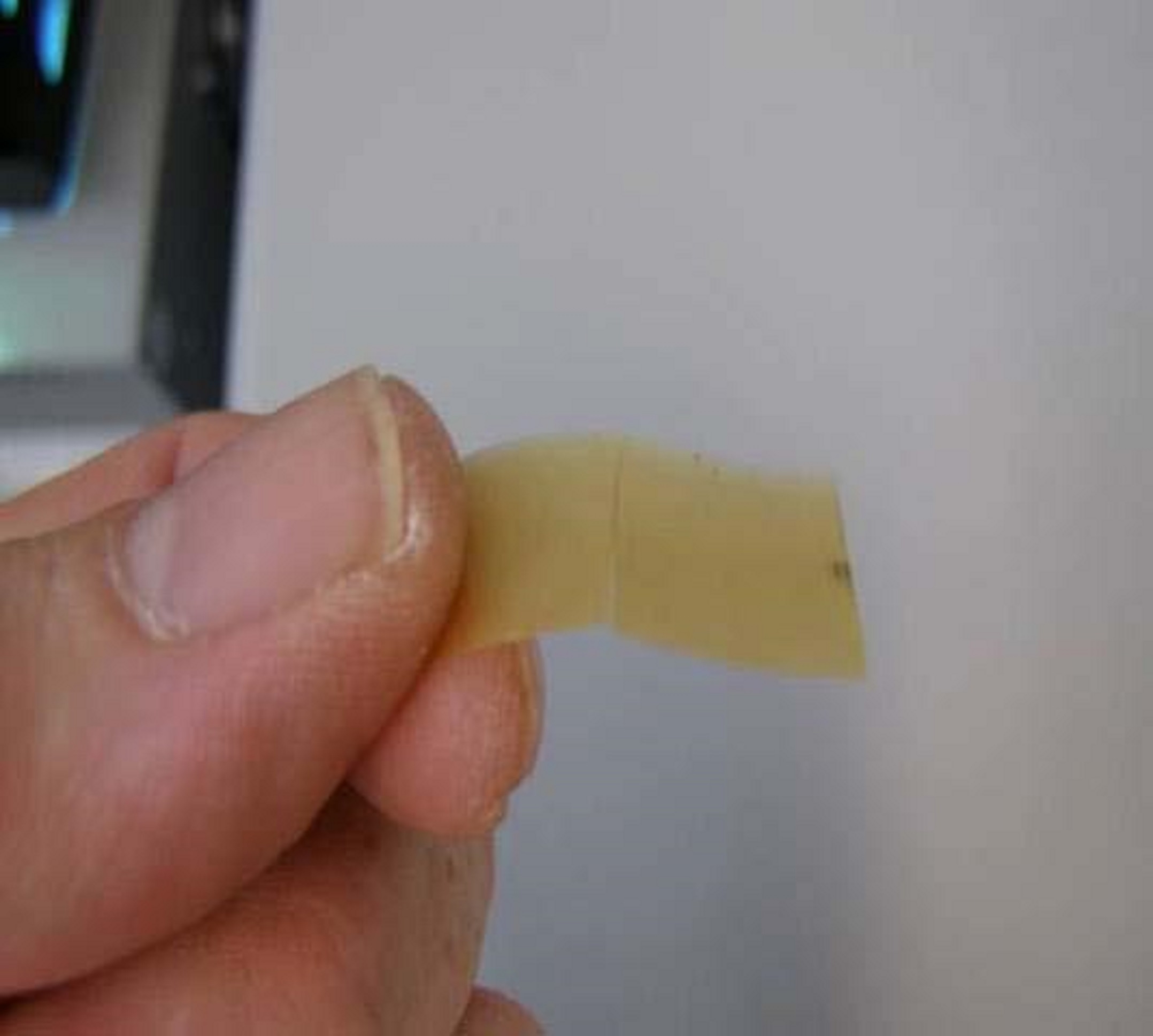
Benefits
- Reduced Maintenance - Self-healing of minor cuts, nicks, and abrasions on wire insulation can substantially reduce the need to perform inspection, troubleshooting, repair, and/or replacement of damaged wiring.
- Reduced Cost - Installation of wire with self-healing insulation can greatly reduce the cost of materials and labor required for the repair or replacement of damaged wiring.
- Improved Safety - Self-healing capability in wire insulation helps prevent shorts which can lead to sparking and conditions conducive to fires.
Applications
- Aerospace (Aircraft, Helicopters, Rockets, etc.)
- Defense (Missiles, Ground Vehicles, Ships, Submarines, Unmanned Aerial Vehicles, etc.)
- Automotive
Technology Details
electrical and electronics
KSC-TOPS-51
KSC-12539-2
KSC-13366
Tags:
|
Similar Results

Self-Healing Low-Melt Polyimides
There are multiple space-related systems that can benefit from high performance, thin film, self-healing/sealing systems. Space vehicles and related ground support equipment can contain miles of wire, much of which is buried inside structures making it very difficult to access for inspection and repair. Space-based inflatable structures, solar panels, and astronauts performing extra-vehicular activities are subject to being struck by micrometeoroids and orbital debris. Self-healing or sealing layers on inflatables, solar panels and spacesuits would increase the safety and survivability of astronauts as well as the survivability and functionality of inflatables and solar panels. Self-healing insulation on wiring would greatly improve the reliability and safety of systems containing such wiring and reduce inspection and repair time over the lifetime of those systems. This technology combines the use of a self-sealing low melt, high performance polyimide film that exhibits the ability, when cut, for separated edges to slowly flow back together and seal itself, with the options of a laminate system and the inclusion of healant microcapsules that, when broken, release healant which can then additionally assist in the healing process. Combinations of the healing approaches can be enabling to the healing process proceeding at a much greater rate and dual mode healing approach can also allow for healing of a larger area.

Multi-layered Self-healing Material System for Impact Mitigation
This innovation utilizes a tri-layered structure, comprised of solid plastic front and back layers sandwiching a viscous, reactive liquid middle layer. Combined, this system provides rapid self-healing following high velocity ballistic penetrations. Self-healing in the front and back layers occurs when the puncture event creates a melt state in the polymer materials and the materials melt elasticity snaps back and closes the hole. The viscous middle layer augments the self-healing properties of the other layers by flowing into the gap created by a ballistic puncture and concurrently solidifying due to the presence of oxygen. Thus, this innovation has two tiers of self-healing: a puncture-healing mechanism triggered by the projectile and a second mechanism triggered by the presence of oxygen.

Puncture-healing Engineered Polymer Blends
Puncture healing melt blends were developed by melt blending self-healing polymers with non self-healing polymeric materials. The self-healing polymeric materials consisted of Surlyn® 8940, Affinity™ EG 8200 G, and poly(butadiene)-graft-poly(methyl acrylate-co-acrylonitrile) or Barex® 210 IN. The non-self-healing polymeric materials consisted of poly(ether ether ketone) (PEEK), LaRC phenyl ethynyl terminated imide 330 (LaRC PETI 330), and Raptor Resins Bismaleimide-1 (BMI-1). Puncture healing blends were also prepared with chopped glass and chopped carbon fibers. The overall goal was to develop a product with superior properties relative to either of the starting materials. The melt blends were prepared in varying compositions to optimize desired properties of the resulting matrix. Ballistic testing was conducted to determine the self-healing characteristics of several developmental polymers subjected to micrometeoroid type damage.

Mechanoresponsive Healing Polymers
The method chemically introduces mechanically sensitive chemical groups into the structure of a resin. By introducing mechanoresponsive functional groups to a polymer, it is possible to induce self-healing through the transformation of such chemical groups to where mechanical properties of a structure are almost completely restored. The forces imparted by a damage event can therefore be used to enable healing or repair of the structure.

Durable Polyimide Aerogels
Aerogels are highly porous, low-density solids with extremely small pore sizes, fabricated by forming a gel from a solution in the wet-gel state that is then converted to the dry-solid state without compaction of the porous architecture. Aerogels make excellent electrical, thermal, and acoustic insulators. However, most inorganic silica aerogels are fragile and shed dust. The NASA Glenn team is the first to synthesize three-dimensional polymer aerogel networks of polyimides cross-linked with multifunctional amine monomers. Compared to silica aerogels, these aerogels retain small pore sizes and low thermal conductivities, but are distinguished by their flexibility. Polyimide aerogels are not brittle, fragile, or dusty like silica aerogels. Plus, polyimide aerogels possess the beneficial characteristics and strength of polyimide materials. The results are cross-linked polyimide aerogels with little shrinkage, low densities, high compression and tensile strengths, and good moisture resistance. They can be fabricated or machined into net shape parts, which are strong and stiff, or cast as thin flexible films with good tensile properties. Extremely customizable, polyimide aerogels can be formed into any configuration (e.g., wrapped around a pipe, sewn into protective clothing, or molded into a panel to act as a heat shield in a car). In short, Glenn's innovation improves the performance, adaptability, and affordability of aerogels in a broad number of applications.