Multilayered Fire Protection System
materials and coatings
Multilayered Fire Protection System (LAR-TOPS-212)
New heat retardant materials based on vehicle reentry thermal protection systems
Overview
NASA Langley has developed a flexible, light weight and portable thermal protection system. The flexible thermal protection systems are multilayer thermal blankets that are designed to handle external temperatures of up to 2000 degrees Fahrenheit. Flight tests clearly demonstrate how these new heat retardant materials can protect from the extreme conditions. This system creates an environment for protecting equipment, facilities, and people from a high intensity incident heat source, such as a fire. The system can be formed as a sleeping bag, a tent, a blanket, a vertical barrier, a curtain, a flexible rollup doorway, or a wrap.
The Technology
The Multilayered Fire Protection system uses technology from the space craft flexible heat shield for future planetary missions. By optimizing this material for the fire environment, utilizing heat shield test methods, and experimenting with different materials, the NASA team developed a multilayered fire protection system. This system includes an outer textile layer which reflects over 90 percent of the radiant heat, an insulated layer which protects against convective heat and hot gases, and a non-porous film layer which is a gas barrier layer.
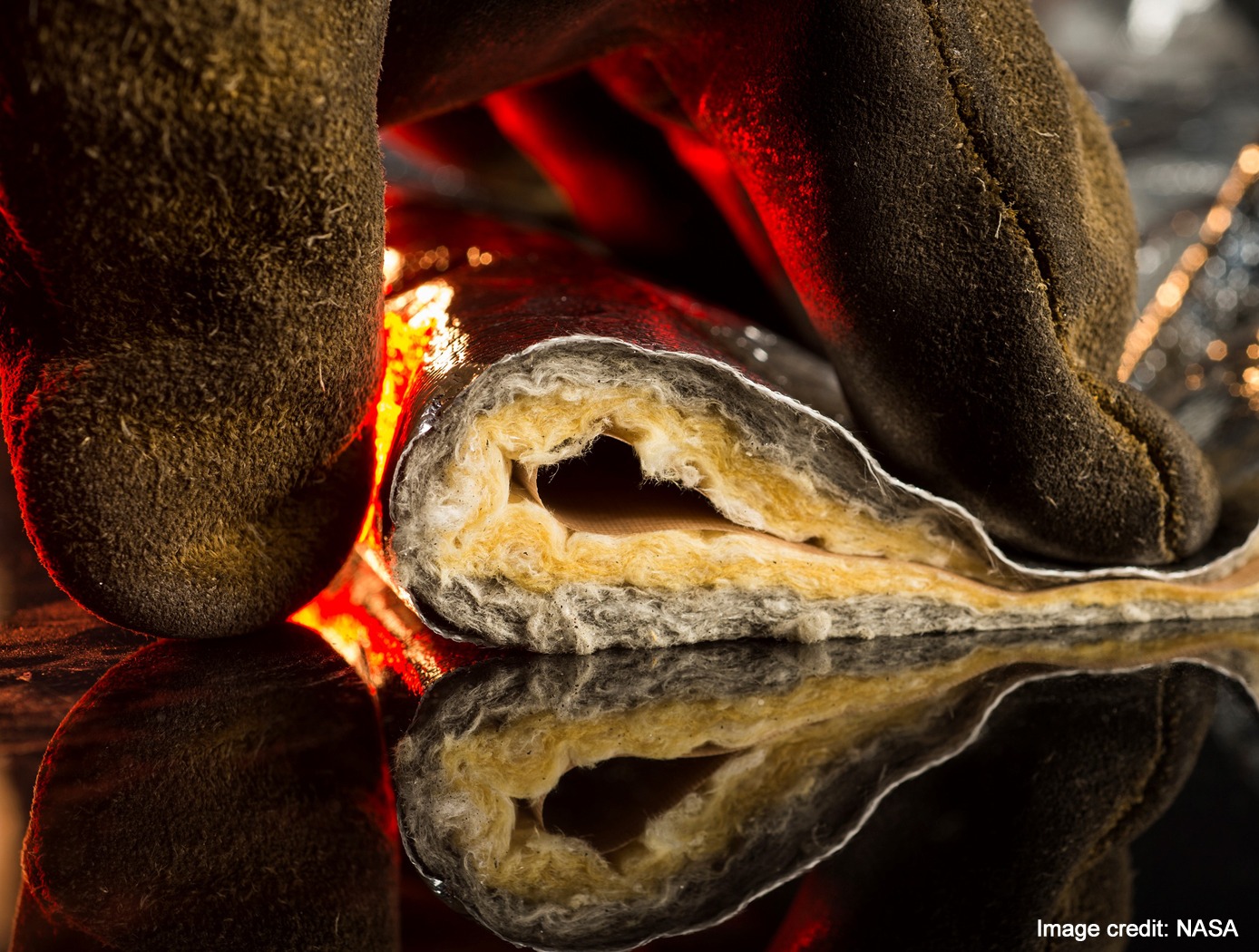
Benefits
- Light weight
- Withstanding temperatures up to 2,000 degrees Fahrenheit
- Portable
- Prevents the transfer of heat
- Flexible
- Safe
Applications
- Insulation for walls
- Fire containment
- Insulation for flammable trailers cargo
- Vertical barrier
- Personal emergency fire shelter
- Blanket
- Protecting property
- Fire protection system for apartments
Technology Details
materials and coatings
LAR-TOPS-212
LAR-18403-1
LAR-18835-1
Convective Heating Improvement for Emergency Fire Shelters - Composition and Performance of Fire Shelter Concepts at Close-Out. Joshua M. Fody, Kamran Daryabeigi, Walter E. Bruce III, John M. Wells, Mary E. Wusk, and Anthony M. Calomino, and Steve D. Miller. NASA/TM2018-219813. https://ntrs.nasa.gov/api/citations/20180002094/downloads/20180002094%20updated.pdf.
The Development of a Thermally Enhanced Emergency Fire Shelter. Joshua M. Fody, Anthony M. Calomino, Kamran Daryabeigi, Walter E. Bruce III, John M. Wells, Mary E. Wusk, and, Stephen D. Miller. 47th International Conference on Environmental Systems ICES-2017-77, 16-20 July 2017, Charleston, South Carolina. https://ntrs.nasa.gov/api/citations/20170007490/downloads/20170007490.pdf.
NASA's Wildfire Monitoring and Protection Technology Webinar You Tube. https://www.youtube.com/watch?v=ww8Fmclp6jo.
The Development of a Thermally Enhanced Emergency Fire Shelter. Joshua M. Fody, Anthony M. Calomino, Kamran Daryabeigi, Walter E. Bruce III, John M. Wells, Mary E. Wusk, and, Stephen D. Miller. 47th International Conference on Environmental Systems ICES-2017-77, 16-20 July 2017, Charleston, South Carolina. https://ntrs.nasa.gov/api/citations/20170007490/downloads/20170007490.pdf.
NASA's Wildfire Monitoring and Protection Technology Webinar You Tube. https://www.youtube.com/watch?v=ww8Fmclp6jo.
Similar Results

A New Family of Low-Density, Flexible Ablators
The invention provides a family of low density, flexible ablators comprising of a flexible fibrous substrate and a polymer resin. The flexible ablators can withstand a wide range of heating rates (40-540 Watts/cm2) with the upper limit of survivable heat flux being comparable to the survivable heat flux for rigid ablators, such as PICA and Avcoat. The amount and composition of polymer resin can be readily tailored to specific mission requirements. The material can be manufactured via a monolithic approach using versatile manufacturing methods to produce large area heat shields, which provides a material with fewer seams or gaps. The goals of the work are primarily twofold: (i) to develop flexible, ablative Thermal Protection System (TPS) material on a large, blunt shape body which provides aerodynamic drag during hypervelocity atmospheric entry or re-entry, without perishing from heating by the bow shock wave that envelopes the body; and (ii) to provide a relatively inexpensive TPS material that can be bonded to a substrate, that is unaffected by deflections, by differences in thermal expansion or by contraction of a TPS shield, and that is suitable for windward and leeward surfaces of conventional robotic and human entry vehicles that would otherwise employ a rigid TPS shield. This technology produces large areas of heat shields that can be relatively easily attached on the exterior of spacecraft.

Creating Low Density Flexible Ablative Materials
The low density flexible ablator can be deployed by mechanical mechanisms or by inflation and is comparable in performance to its rigid counterparts of the same density and composition. Recent testing in excess of 400W/cm2 demonstrated that the TPS char has good structural integrity and retains similar flexibility to the virgin material, there by eliminating potential failure due to fluttering and internal stress buildup as a result of pyrolysis and shrinkage of the system. These flexible ablators can operate at heating regimes where state of the art flexible TPS (non-ablative) will not survive. Flexible ablators enable and improve many missions including (1) hypersonic inflatable aerodynamic decelerators or other deployed concepts delivering large payload to Mars and (2) replacing rigid TPS materials there by reducing design complexity associated with rigid TPS materials resulting in reduced TPS costs.

Highly Thermal Conductive Polymeric Composites
There has been much interest in developing polymeric nanocomposites with ultrahigh thermal conductivities, such as with exfoliated graphite or with carbon nanotubes. These materials exhibit thermal conductivity of 3,000 W/mK measured experimentally and up to 6,600 W/mK predicted from theoretical calculations. However, when added to polymers, the expected thermal conductivity enhancement is not realized due to poor interfacial thermal transfer.
This technology is a method of forming carbon-based fillers to be incorporated into highly thermal conductive nanocomposite materials. Formation methods include treatment of an expanded graphite with an alcohol/water mixture followed by further exfoliation of the graphite to form extremely thin carbon nanosheets that are on the order of between about 2 and about 10 nanometers in thickness. The carbon nanosheets can be functionalized and incorporated as fillers in polymer nanocomposites with extremely high thermal conductivities.

Thermal protection supplement for reducing interface thermal mismatch
The invention includes an exposed surface cap with a specially formulated coating, an insulator base adjacent to the cap with another specially formulated coating, and one or more pins that extend from the cap through the insulator base to tie the cap and base together through ceramic bonding and mechanical attachment. The cap and insulator base have corresponding depressions and projections that mate and allow for differences in thermal expansion of the cap and base. The cap includes a high-temperature, low density, carbonaceous, fibrous material whose surface is optionally treated with a High Efficiency Tantalum-based Ceramic Composite (HETC) formulation, the fibrous material being drawn from the group consisting of silicon carbide foam and similar porous, high temperature materials. The insulator base and pin(s) contain similar material. The mechanical design is arranged so that thermal expansion differences in the component materials (e.g., cap and insulator base) are easily tolerated. It is applicable to both sharp and blunt leading edge vehicles. This extends the possible application of fibrous insulation to the wing leading edge and/or nose cap on a hypersonic vehicle. The lightweight system comprises a treated carbonaceous cap composed of Refractory Oxidation-resistant Ceramic Carbon Insulation (ROCCI), which provides dimensional stability to the outer mold line, while the fibrous base material provides maximum thermal insulation for the vehicle structure. The composite has graded surface treatments applied by impregnation to both the cap and base. These treatments enable it to survive in an aero-convectively heated environment of high-speed planetary entry. The exact cap and base materials are chosen in combination with modified surface treatments and a specially formulated surface coating, taking into account the duration of exposure and expected surface temperatures for the particular application.

Woven Thermal Protection System
Going farther, faster and hotter in space means innovating how NASA constructs the materials used for heat shields. For HEEET, this results in the use of dual-layer, three-dimensional, woven materials capable of reducing entry loads and lowering the mass of heat shields by up to 40%. The outer layer, exposed to a harsh environment during atmospheric entry, consists of a fine, dense weave using carbon yarns. The inner layer is a low-density, thermally insulating weave consisting of a special yarn that blends together carbon and flame-resistant phenolic materials. Heat shield designers can adjust the thickness of the inner layer to keep temperatures low enough to protect against the extreme heat of entering an atmosphere, allowing the heat shield to be bonded onto the structure of the spacecraft itself. The outer and inner layers are woven together in three dimensions, mechanically interlocking them so they cannot come apart. To create this material, manufacturers employ a 3-D weaving process that is similar to that used to weave a 2-D cloth or a rug. For HEEET, computer-controlled looms precisely place the yarns to make this kind of complex three-dimensional weave possible. The materials are woven into flat panels that are formed to fit the shape of the capsule forebody. Then the panels are infused with a low-density version of phenolic material that holds the yarns together and fills the space between them in the weave, resulting in a sturdy final structure. As the size of each finished piece of HEEET material is limited by the size of the loom used to weave the material, the HEEET heat shield is made out of a series of tiles. At the points where each tile connects, the gaps are filled through inventive designs to bond the tiles together.