Photo-Acoustic Sub Part-Per-Billion Chemical Sensing
sensors
Photo-Acoustic Sub Part-Per-Billion Chemical Sensing (LAR-TOPS-214)
Photo-acoustic sensing based laser vibrometer for the measurement of ambient chemical species
Overview
NASA Langley Research Center has developed a photo-acoustics sensing based laser vibrometer for the measurement of ambient chemical species. The technology allows for detection of sub part-per-billion (ppb) levels of ambient trace gases and chemical species, with an order of magnitude more sensitivity than similar technologies. Among other applications, the technology could be used for the detection of explosives and hazardous or toxic chemicals.
The Technology
The technology is a sensor for remotely detecting sub part-per-billion (ppb) levels of ambient trace gases and chemical species. The system includes a high-repetition-rate, pulsed laser module that is spectrally tuned to a desired chemical species. The photons from the laser are absorbed by the target chemical, creating an acoustic vibration that impacts a diaphragm (which acts like a speaker). A highly sensitive, photo-emf detector is then used to measure the magnitude of the vibration, which corresponds to the concentration of the target chemical. The technology is being developed for NASA's trace-gas measurement needs for validation and ground truth studies to support airborne and space-based LIDAR operations. The technology has application as a chemical sniffer to detect hazardous or toxic chemical species in the vicinity of IEDs, explosives, or other chemical agents. In such an application the sensor could detect chemical species hidden inside closed containers, bags, or car trunks.
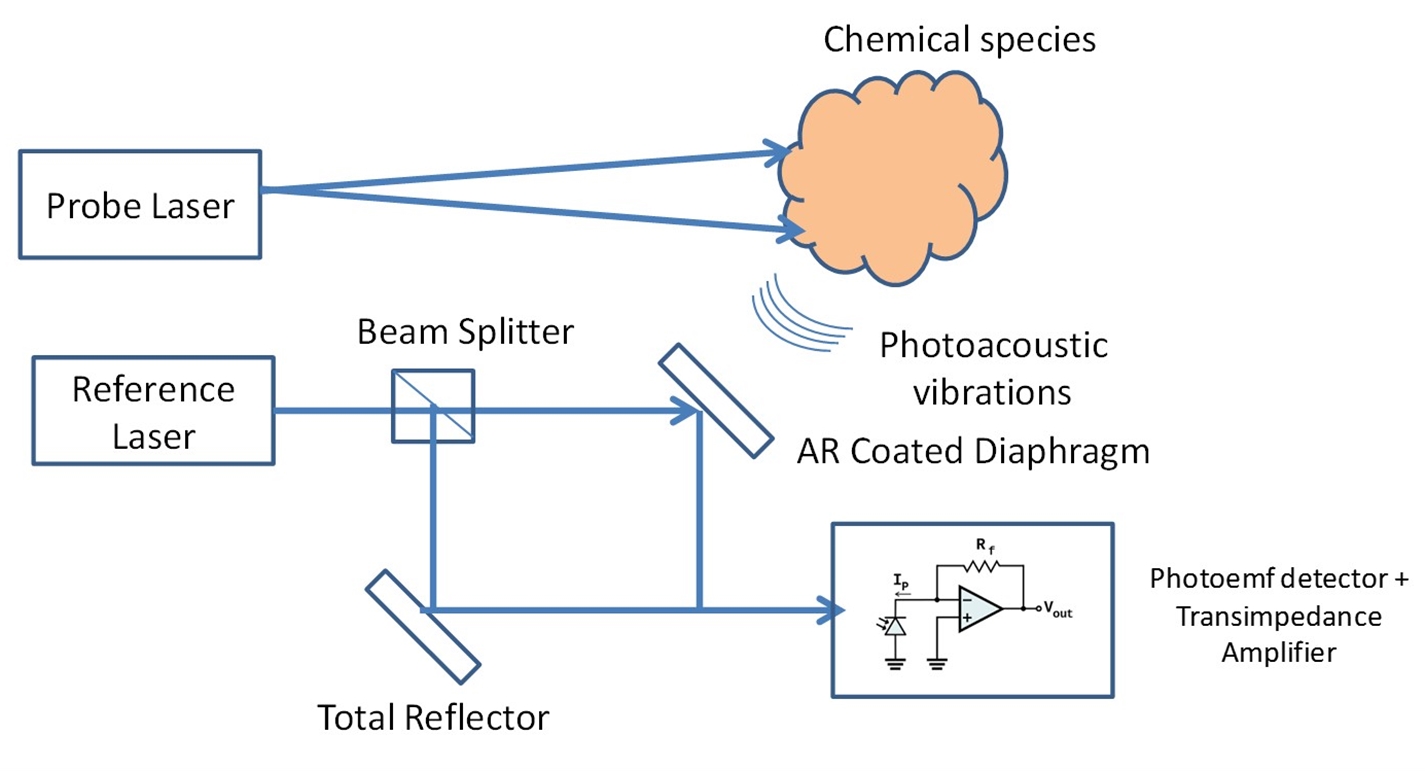
Benefits
- Allows for measurement of sub-ppb level concentrations of chemical species over wide temperature ranges and high altitudes
- Provides an order of magnitude more sensitivity than similar technologies
- Will be a compact/hand-held device
Applications
- Airborne and space based chemical detection
- Hand-held chemical detection
Similar Results

Fast and widely tunable monolithic optical parametric oscillator for laser spectrometer
NASA Goddard Space Flight Center has developed a faster and widely-tunable monolithic optical parametric oscillator for use in laser spectrometers. This technology provides a continuously-tunable spectrum across any target, adding flexibility to the overall instrument. In addition, only 1 nonlinear crystal and oscillator pump source are used, greatly simplifying the spectrometer system.

Remote, Noninvasive, Cardiac Activity Tracer (RENCAT)
Blood circulation carries vibrations due to heart beat to every part of the body. These vibrations result in minute displacements that are measured by the detector. Defective closures lead to backflow of blood into chambers leading to heart beat slowdown. Displacement strength is indicative of vibration strength which in turn is indicative of heart beat. Weak vibrations at toes, for example, indicate poor circulation of blood as in the case of diabetic issues. Similarly, in other parts of the body, this unit would help in early detection of diabetes and other diseases by noninvasively monitoring blood circulation at various regions of a human body. As such, this unit would detect precursors for diseases. For astronauts and other operatives, this device could remotely provide the status of their cardiac cycles during physical activities.
The device consists of a laser transmitter, photo-EMF detector and interferometric architecture which provides motion detection. Motion detection aids in measuring displacements. There is also a "speckle tolerant" property allowing data to be collected from conformal and rough target surfaces such as garments. Surface preparation is not needed such as in ECG and other cases. The novel Photo-EMF detector will be able to measure displacements of less than 1 pm.

Multi-Parameter Aerosol Scattering Sensor
Originally developed to demonstrate a highly accurate, low-false-alarm, early fire detection system in space, this advanced technology level system utilizes a durable, low-cost, compact laser source and detector array, similar to CD/DVD player technology, to analyze the interaction of light with particles. The smart system is ideal for detecting a diverse range of particles found in pollution, emissions, fire and other atmospheric toxins while introducing a flexibility that enables its use in multiple environments, especially when coupled with UAVs or other remote platforms.
The MPASS contains a number of features that allow users to make the most of its pioneering capabilities. The self-contained system is lightweight and has been miniaturized and packaged to easily fit into the palm of your hand. A USB port enables the system to be powered, configured, and accessed through its onboard central processing unit. The advanced graphical user interface, custom software, and optimized algorithm allows the user to select known properties when applicable, and to program the system for maximum performance. The dashboard also provides visual feedback through graphical displays, making it easy to analyze the data and make real-time decisions. The system is designed with Bluetooth expansion capability, adding flexibility and communication through potential custom cellular phone applications. Once programmed, the battery-powered wireless sensor system opens the door to monitoring remote areas and extreme environments never thought possible.

Miniaturized Laser Heterodyne Radiometer
This instrument uses a variation of laser heterodyne radiometer (LHR) to measure the concentration of trace gases in the atmosphere by measuring their absorption of sunlight in the infrared. Each absorption signal is mixed with laser light (the local oscillator) at a near-by frequency in a fast photoreceiver. The resulting beat signal is sensitive to changes in absorption, and located at an easier-to-process RF frequency. By separating the signal into a RF filter bank, trace gas concentrations can be found as a function of altitude.

Solid State Carbon Dioxide (CO2) Sensor
The technology is a solid state, Carbon Dioxide (CO2) sensor configured for sensitive detection of CO2 having a concentration within the range of about 100 Parts per Million (ppm) and 10,000 ppm in both dry conditions and high humidity conditions (e.g., > 80% relative humidity). The solid state CO2 sensor achieves detection of high concentrations of CO2 without saturation and in both dynamic flow mode and static diffusion mode conditions. The composite sensing material comprises Oxidized Multi-Walled Carbon Nanotubes (O-MWCNT) and a metal oxide, for example O-MWCNT and iron oxide (Fe2O3) nanoparticles. The composite sensing material has an inherent resistance and corresponding conductivity that is chemically modulated as the level of CO2 increases. The CO2 gas molecules absorbed into the carbon nanotube composites cause charge-transfer and changes in the conductive pathway such that the conductivity of the composite sensing material is changed. This change in conductivity provides a sensor response for the CO2 detection. The solid state CO2 sensor is well suited for automated manufacturing using robotics and software controlled operations. The solid state CO2 sensor does not utilize consumable components or materials and does not require calibration as often as conventional CO2 sensors. Since the technology can be easily integrated into existing programmable electronic systems or hardware systems, the calibration of the CO2 sensor can be automated.