Fast & Accurate Composite Bond Strength Measurement
instrumentation
Fast & Accurate Composite Bond Strength Measurement (LAR-TOPS-332)
Nondestructive Test Compatible with Assembly & Repair Facilities
Overview
Innovators at the NASA Langley Research Center, in conjunction with the National Institute of Aerospace and the University of Virginia, have developed a method for evaluation of adhesive bond strength via swept-frequency ultrasonic phase measurements. In recent years, the use of advanced composites has increased as modern designs strive for lighter weight, higher performance, and greater durability. Adhesive bonding is the preferred method of joining composite structures, requiring a nondestructive evaluation (NDE) method for ensuring adequate bonded joint strength. Conventional NDE methods have been used to detect gross bonding defects, but such methods have proven insensitive to weak adhesion. Current NDE methods that claim sensitivity to interfacial bond strength require complex, bulky, and time-intensive measurement procedures that are often not adaptable to the shop floor. NASA's new measurement system quickly and accurately measures interfacial bond strength and is easily compatible with assembly line and repair facilities.
The Technology
NASA's Method of Evaluating Adhesive Bond Strength is an accurate, robust, quantitative, and nondestructive bond strength measurement method that meets an immediate need in composite manufacturing. Even with careful control of the bonding procedure, destructive testing has shown that bonded joint strength shows substantial variation. Prior art in the field is insensitive to weak interfacial bonding, which leads to poor service life and potential catastrophic failure. Using NASA's method, phase measurements are acquired at a single frequency and then swept to obtain measurements at other frequencies. Narrowband filtering removes extraneous frequencies, which allows for much lower phase measurement uncertainty than other methods. Digital sine wave generation allows for better phase measurement resolution. The resultant system is a phase-based ultrasonic measurement tool for interrogating bonded joints and detecting weak adhesion with superior sensitivity than the state of the art. This new method models adhesive interfaces as a distributed spring system, where the interfacial stiffness constants of the joint can be determined from the zero- crossing frequency of the phase response and the "sharpness" or slope of the phase response. Previous theoretical research has shown that a linear correlation exists between interfacial stiffness constants and mechanically-measured interfacial bond strength. As such, the ultrasonic phase measurement method identifies intermediate bond strengths, rather than simply detecting good or bad bonds. This technique verifies bond quality in metal and composite joint systems, including those commonly found in aerospace, automotive, and many other transportation and infrastructure designs. The demonstrated ultrasonic phase method is applicable to a variety of bonding material systems.
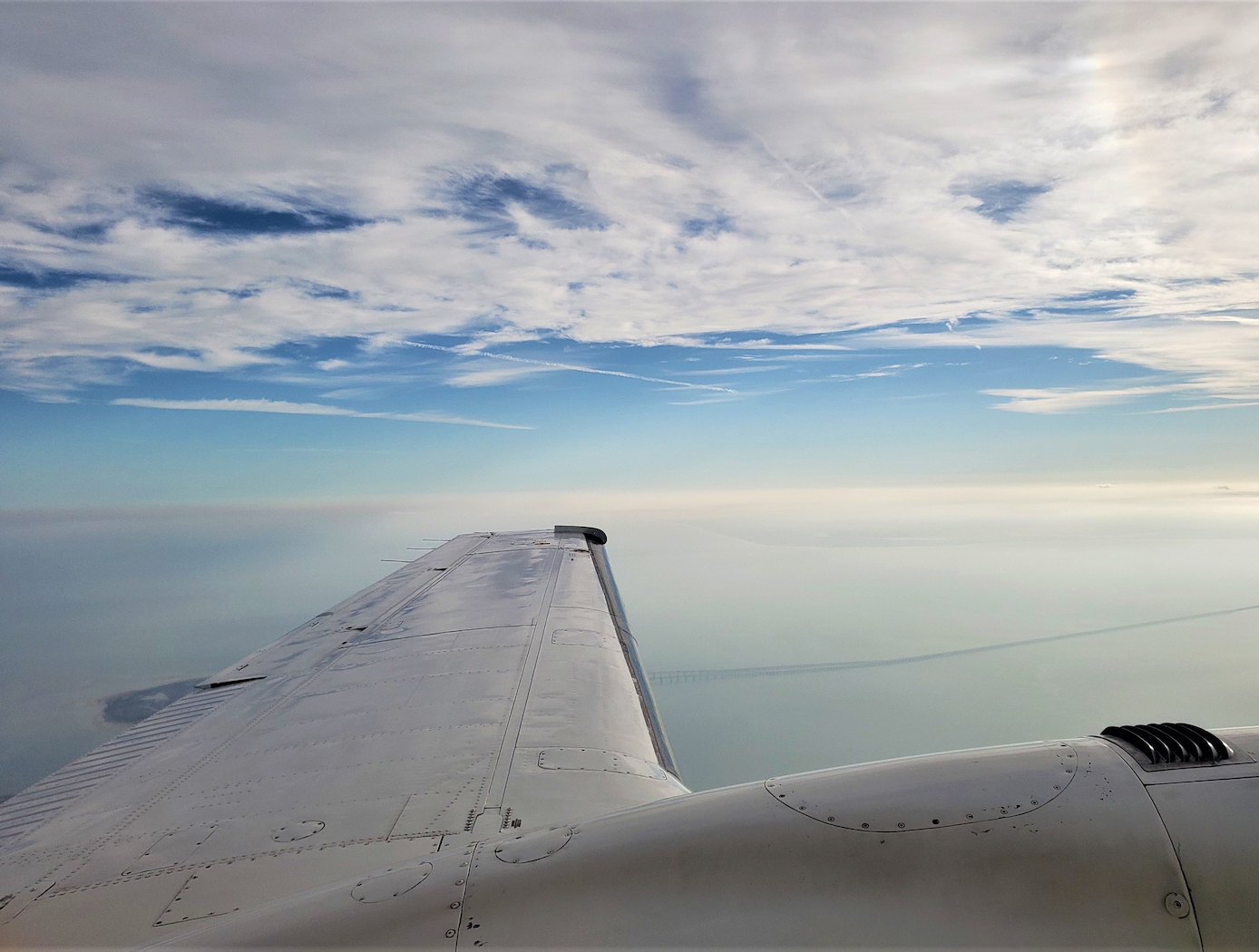
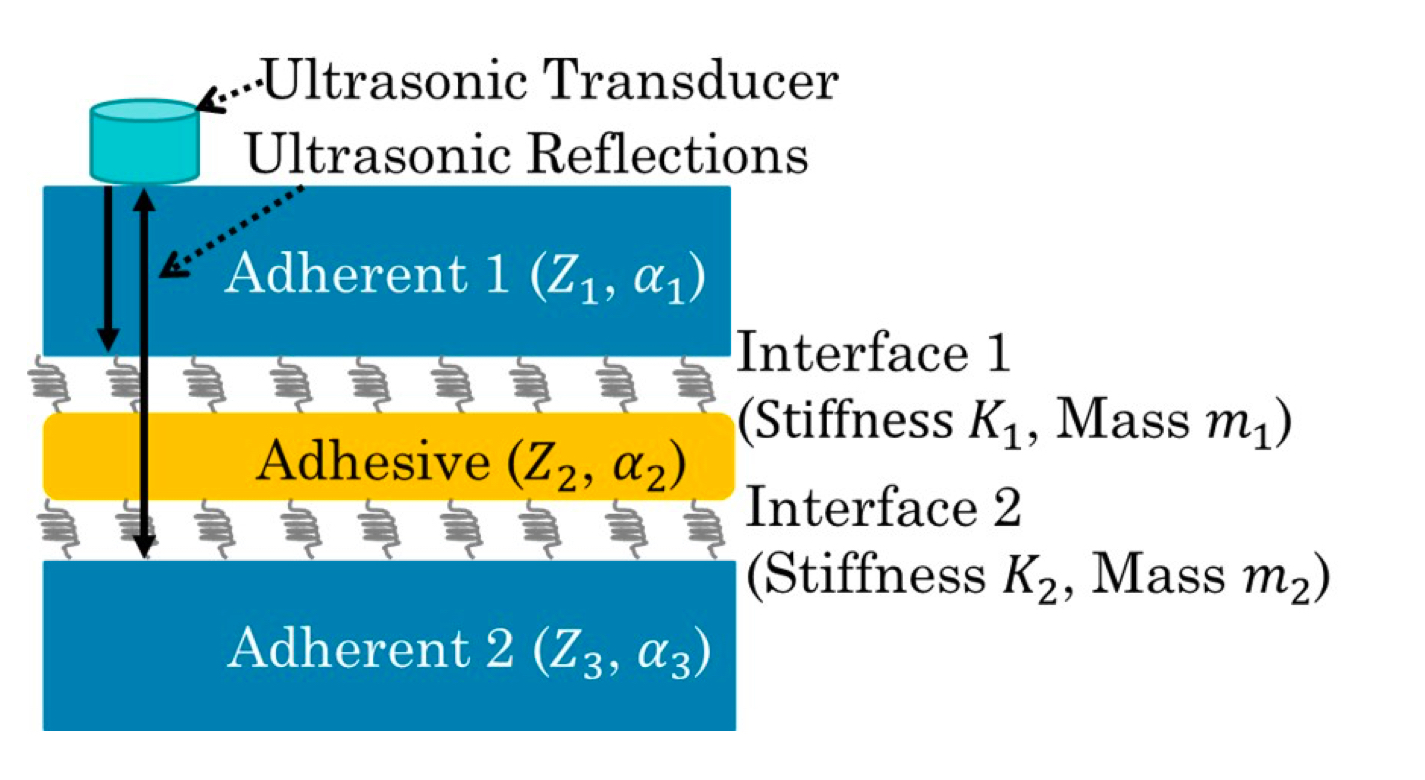
Benefits
- Superior method for interrogating bonded joints and detecting weak adhesion: provides a highly accurate and sensitive NDE method with marked improvements over existing technology that can be used for detecting interfacial bond strength after fabrication, following bonded repairs, and throughout a joint's service life
- Lab tested and verified: proven performance using glass adherends, aluminum adherends, and UV curable adhesives
- Shop and production floor friendly: can be built with COTS transducers, enabling a simple, compact measurement device that takes quick measurements and is compatible with assembly line and repair facilities
Applications
- Aerospace: aircraft manufacturing (e.g., carbon fiber composites for wing and fuselage surfaces bonded together as well as to aluminum air frames)
- Architecture and construction: building construction
- Automotive: composite parts for automobile manufacturing
- Composites: NDE method for measuring adhesive bond strength
- Electronics: printed circuit fabrication
- Marine: ship building
- Semiconductors: semiconductor fabrication
Tags:
|
Similar Results

Method of Non-Destructive Evaluation of Composites
Guided wavefield techniques require excitation of guided waves in a specimen via contact or noncontact methods (such as attached piezoelectric transducers or laser generation). The resulting wavefield is recorded via noncontact methods such as laser Doppler vibrometry or air-coupled ultrasound. If the specimen contains damage, the waves will interact with that damage, resulting in an altered wavefield (compared to the pristine case). When guided wave modes enter into a delaminated region of a composite the energy is split above/below delaminations and travels through the material between delaminations. Some of the energy propagates beyond the delamination and re-emerges as the original guided wave modes. However, a portion
of the wave energy is trapped as standing waves between delaminations. The trapped waves slowly leak from the delaminated region, but energy remains trapped for some time after the incident waves have propagated beyond the damage region.
Simulation results show changes in the trapped energy at the composite surface when
additional delaminations exist through the composite thickness. The results are a
preliminary proof-of-concept for utilizing trapped energy measurements to identify
the presence of hidden delaminations when only single-sided access is available to a
component/vehicle. Currently, no other single-sided field-applicable NDT techniques
exist for identifying hidden delamination damage.

Large Area Structural Damage Nondestructive Evaluation
This technology provides a methodology to measure damage onset and grow at multiple locations in a composite structure during fatigue loading. The thermography inspection is non-contact and can cover very large areas. The acoustic emission sensors require contact at only the sensor attachment points and can cover large areas. The acoustic emission measurement is very sensitive to damage formation events such as matrix cracking, fiber breaks, and delamination, however the event location is approximate. An infrared camera is able to detect damage growth and location at areas of heating (due to fiber breaks, rubbing of disbond areas and matrix cracks) and thus confirm the acoustic emission measurements. If the loading is cyclic the infrared camera is also able to detect the relative depth of the damage. Combining both technologies helps to reduce false indications, confirm damage growth areas and where ultimate failure will occur. This provides a measurement capability to detect growing damage (location and size) for improved structures testing or during in-service applications. Multiple infrared (IR) cameras and multiple acoustic emission sensors can be employed internally or externally for full coverage of the structure. When significant damage growth is detected, the structure can be taken out of service for repair or for further inspections. This technology has been demonstrated for structures testing. In-situ NDE inspections are necessary to provide structural engineers a tool to incrementally control and document damage growth as a function of fatigue cycles before failure. This allows for the comparison of NDE results to develop and validate progressive damage analysis (PDA) models. The ultimate goal is to use the validated PDA models to decrease the time required to certify composite structures and therefore save development costs. Real time NDE can document the progression of damage and provide the documentation of ultimate failure mechanisms.

System for In-situ Defect Detection in Composites During Cure
NASA's System for In-situ Defect (e.g., porosity, fiber waviness) Detection in Composites During Cure consists of an ultrasonic portable automated C-Scan system with an attached ultrasonic contact probe. This scanner is placed inside of an insulated vessel that protects the temperature-sensitive components of the scanner. A liquid nitrogen cooling systems keeps the interior of the vessel below 38°C. A motorized X-Y raster scanner is mounted inside an unsealed cooling container made of porous insulation boards with a cantilever scanning arm protruding out of the cooling container through a slot. The cooling container that houses the X-Y raster scanner is periodically cooled using a liquid nitrogen (LN2) delivery system. Flexible bellows in the slot opening of the box minimize heat transfer between the box and the external autoclave environment. The box and scanning arm are located on a precision cast tool plate. A thin layer of ultrasonic couplant is placed between the transducer and the tool plate. The composite parts are vacuum bagged on the other side of the tool plate and inspected. The scanning system inside of the vessel is connected to the controller outside of the autoclave. The system can provide A-scan, B-scan, and C-scan images of the composite panel at multiple times during the cure process.
The in-situ system provides higher resolution data to find, characterize, and track defects during cure better than other cure monitoring techniques. In addition, this system also shows the through-thickness location of any composite manufacturing defects during cure with real-time localization and tracking. This has been demonstrated for both intentionally introduced porosity (i.e., trapped during layup) as well processing induced porosity (e.g., resulting from uneven pressure distribution on a part). The technology can be used as a non-destructive evaluation system when making composite parts in in an oven or an autoclave, including thermosets, thermoplastics, composite laminates, high-temperature resins, and ceramics.

AERoBOND: Large-scale Composite Manufacturing
This technology (AERoBOND) enables the assembly of large-scale, complex composite structures while maintaining predictable mechanical and material properties. It does so by using a novel barrier-ply technology consisting of an epoxy resin/prepreg material with optimal efficiency, reliability, and performance. The barrier-ply materials prevent excessive mixing between conventional composite precursors and stoichiometrically-offset epoxy precursors during the cure process by forming a gel early in the cure cycle before extensive mixing can occur. The barrier ply is placed between the conventional laminate preform and the stoichiometrically-offset ply or plies placed on the preform surface, thus preventing excessive mass transfer between the three layers during the cure process. In practice, the barrier ply could be combined with the offset ply to be applied as a single, multifunctional surfacing layer enabling unitized assembly of large and complex structures. The AERoBOND method is up to 40% faster than state-of-the-art composite manufacturing methods, allows for large-scale processing of complex structures, eliminates the potential for weak bond failure modes, and produces composites with comparable mechanical properties as compared with those prepared by co-cure.
Multidimensional Damage Detection System
The Damage Detection System consists of layered composite material made up of two-dimensional thin film damage detection layers separated by thicker, nondetection layers, coupled with a detection system. The damage detection layers within the composite material are thin films with a conductive grid or striped pattern. The conductive pattern can be applied on a variety of substrates using several different application methods. The number of detection layers in the composite material can be tailored depending on the level of damage detection detail needed for a particular application. When damage occurs to any detection layer, a change in the electrical properties of that layer is detected and reported. Multiple damages can be detected simultaneously, providing real-time detail on the depth and location of the damage.
The truly unique feature of the System is its flexibility. It can be designed to gather as much (or as little) information as needed for a particular application using wireless communication. Individual detection layers can be turned on or off as necessary, and algorithms can be modified to optimize performance. The damage detection system can be used to generate both diagnostic and prognostic information related to the health of layered composite structures, which will be essential if such systems are utilized to protect human life and/or critical equipment and material.