Flow Control Devices
mechanical and fluid systems
Flow Control Devices (LAR-TOPS-36)
Two fluidic oscillators with no moving parts optimize flow control for better system performance
Overview
NASA's Langley Research Center develops innovative technologies to control fluid flow in ways that will ultimately result in improved performance and fuel efficiency. Often called fluidic oscillators, sweeping jet actuators or flip flop oscillators, these flow control devices work based on the Coanda effect.
They can be embedded directly into a control surface (such as a wing or a turbine blade) and generate spatially oscillating bursts (or jets) of fluid to improve flow characteristics by enhancing lift, reducing drag, or enhancing heat transfer. Recent studies show up to a 60% performance enhancement with oscillators.
NASA offers two new fluidic oscillator designs that address
two key limitations of these oscillators: coupled frequency--amplitude
and random oscillations. One oscillator effectively
decouples the oscillation frequency from the amplitude. The
other design enables synchronization of an entire array. The new
oscillators have no moving parts oscillation, decoupling, and
synchronization are achieved entirely via internal flow dynamics.
The Technology
Both oscillators are flow control devices based on novel geometric designs. They have no moving parts and produce spatially oscillating jets. Each was designed to address a particular limitation of current oscillators.
Gaining control authority by decoupling frequency and amplitude:
Existing oscillators are limited in that the frequency of oscillation is controlled by input pressure or mass flow rate--the frequency and amplitude (mass flow rate) are coupled, limiting control authority over the oscillators. The new oscillator design decouples the frequency from the amplitude by employing a novel design featuring a main oscillator that controls the amplitude and a small oscillator that controls the frequency of the oscillations (see Figure 1). The decoupled oscillator delivers high (or low) mass flow rates without changing the frequency and vice versa.
Gaining control authority by synchronizing the entire oscillator jet array:
Existing oscillators in an array oscillate randomly. While this is useful for mixing enhancement, synchronized flow may be more beneficial for active flow control applications. The simple design of the new Langley synchronized oscillator achieves synchronization without having electro/mechanical or any other moving parts. The new oscillator enables synchronization of an entire array by properly designing the feedback loops to have one unique feedback signal to each actuator. Once each actuator has the same feedback signal, each main jet attaches to one side of the Coanda surface at the same time, allowing synchronized oscillation, as shown in Figure 2.
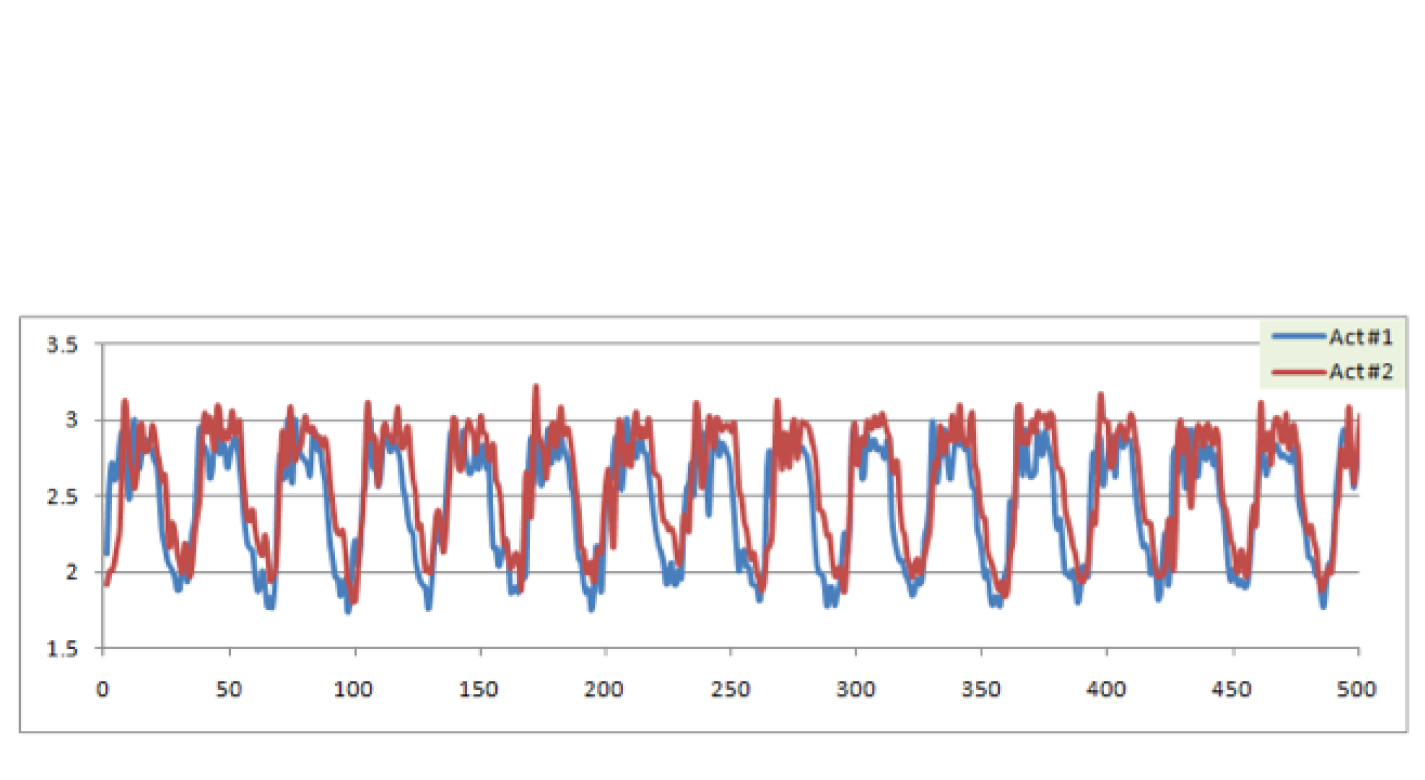
Benefits
- Maintenance-free - no moving parts, simple design
- Rugged - applicable to harsh environments
- Scalable - from micro to macro scale
- No added drag oscillators can be machined as embedded arrays
- Improved control authority - can vary frequency with very little mass flow compared to previous oscillators
- Synchronized oscillations
Applications
- Aerospace - -- Boundary layer control -- Separation control -- Lift enhancement -- Drag reduction -- Mixing
- Shipbuilding - flow control
- Gas turbines - -- Heat transfer enhancement -- Separation control
- Hydrotherapy equipment - different modes of massaging.
Similar Results

Variable-Aperture Reciprocating Reed (VARR) Valve
The VARR valve has been designed to provide a variable-size aperture that proportionately changes in relation to gas flow demand. When the pressure delta between two chambers is low, the effective aperture cross-sectional area is small, while at high delta pressure the effective aperture cross-sectional area is large. This variable aperture prevents overly restricted gas flow. As shown in the drawing below, gas flow through the VARR valve is not one way. Gas flow can traverse through the device in a back-and-forth reversing flow manner or be used in a single flow direction manner. The contour shapes and spacing can be set to create a linear delta pressure vs. flow rate or other pressure functions not enabled by current standard orifices. Also, the device can be tuned to operate as a flow meter over an extremely large flow range as compared to fixed-orifice meters. As a meter, the device is capable of matching or exceeding the turbine meter ratio of 150:1 without possessing the many mechanical failure modes associated with turbine bearings, blades, and friction, etc.

Improved Fixed-Wing Gust Load Alleviation Device
Gust loads may have detrimental impacts on flight including increased structural and aerodynamic loads, structural deformation, and decreased flight dynamic performance. This technology has been demonstrated to improve current gust load alleviation by use of a trailing-edge, free-floating surface control with a mass balance. Immediately upon impact, the inertial response of the mass balance shifts the center of gravity in front of the hinge line to develop an opposing aerodynamic force alleviating the load felt by the wing. This passive gust alleviation control covering 33% of the span of a cantilever wing was tested in NASA Langleys low speed wind tunnel and found to reduce wing response by 30%.
While ongoing experimental work with new laser sensing technologies is predicted to similarly reduce gust load, simplicity of design of the present invention may be advantageous for certification processes. Additionally, this passive technology may provide further gust alleviation upon extending the use of the control to the entire trailing edge of the wing or upon incorporation with current active gust alleviation systems.
Importantly, the technology can be easily incorporated into to the build of nearly all fixed wing aircrafts and pilot control can be maintained through a secondary trim tab. Though challenging to retrofit, passive gust alleviation could enable use of thinner, more efficient wings in new plane design.

Supersonic Laminar Flow Control
This technique injects precisely defined stationary transient growth disturbances into the free air slipstream over a wing that develop into streamwise elongated "streaks." These streaks are created with an alternating pattern of low and high streamwise velocity in the boundary layer flow adjacent to the aerodynamic surface of interest. Judicious selection of streak wavelength, amplitude, and profile allows the first-mode instability waves responsible for transition via oblique mode breakdown to be damped while the remaining, uncontrolled waves are kept below an amplification threshold. A similar control concept is also applicable to second mode transition at hypersonic Mach numbers.

Fluid Transfer Coupler
The Fluid Transfer Coupler has a compensatory mechanism for alignment. All alignment is achieved within the coupler and alignment features are removed from the actuator. The coupler has a launch lock, which engages features on the coupler body and requires a hard
connection to the actuator body or the bracket. The gimbal has a clamshell spherical bearing between the lock collar and the radial bearing collar. It has larger clearances than a typical bearing of this type. This joint can potentially be eliminated if a lock is implemented. The thrust bearing allows and limits free movement. Marcel expander springs keep retainers centered, keeps the coupling centered, and prevents chatter. A hard stop limits ball loads under pressure. Wavy washer keeps ball bearings under enough pressure to prevent chatter. The alignment bell has a passive coupler which engages to align. The materials and coatings can be chosen to preclude galling and particle generation.
An active poppet seal provides debris seal at the nose and pressure seal further back. A passive poppet seal is provided by the seal cover to provide double duty. Various types of seals can be used, such as O-rings, spring-energized seals, and solid seals.

Fluid Structure Coupling Technology
FSC is a passive technology that can operate in different modes to control vibration:
Harmonic absorber mode: The fluid can be leveraged to act like a classic harmonic absorber to control low-frequency vibrations. This mode leverages already existing system mass to decouple a structural resonance from a discrete frequency forcing function or to provide a highly damped dead zone for responses across a frequency range.
Shell mode: The FSC device can couple itself into the shell mode and act as an additional spring in a series, making the entire system appear dynamically softer and reducing the frequency of the shell mode. This ability to control the mode without having to make changes to the primary structure enables the primary structure to retain its load-carrying capability.
Tuned mass damper mode: A small modification to a geometric feature allows the device to act like an optimized, classic tuned mass damper.