Fuel Cell Power Management
power generation and storage
Fuel Cell Power Management (LEW-TOPS-23)
Produces multiple power levels from a single fuel cell stack
Overview
An innovation from NASA's Glenn Research Center increases the efficiency and versatility of fuel cell stacks for power generation. When there is a large increase in the power demand from a fuel cell system, the voltage of the fuel cell system decreases, sometimes below the lowest acceptable threshold. To meet the requirements of a fuel cell system, engineers have typically added direct-current-to-direct-current (DC-to-DC) converters that boost the voltage produced at the ends of the fuel cell stack or added additional fuel cell systems to manage the increased power demand. However, adding DC-to-DC converters or additional fuel cell systems increases cost, reduces efficiency, and adds both mass and volume. NASA's innovative technique features multiple power points that connect different numbers of cells in an electrical series to a device connected to the fuel cell system, allowing the fuel cell system to maintain the desired voltage to the device under very large electrical power demand changes. This capability eliminates DC-to-DC converter electronics, thereby reducing cost and simplifying the system.
The Technology
In general, individual fuel cells produce relatively small electrical potentials, so fuel cells are "stacked" or placed in series (anode to cathode) to increase the combined voltage and meet the application's requirements. The current is drawn off by connection points, which typically are at the extreme ends of the fuel cell stack. DC power converters reduce or boost the voltage produced at the ends of the stack into a voltage that can be used by attached device. However, these converters add cost, mass, volume, and potential failure points into the fuel cell system.
With NASA Glenn's groundbreaking technique, the fuel cell stack includes a plurality of connection points to the device instead of having a fixed number of individual fuel cells. By connecting additional cells in the same stack to the device the system power can be to be tailored to produce the required voltage for the connected device. Initially, this plurality includes a ground, a first connection point, and a second connection point. Additional connection points to the device can be added as needed, resulting in various powers that are available for use. Each connection point allows power to be drawn the combined voltages of the fuel cells located between the connection point and the ground. This configuration permits the voltage to be adjusted to the system power requirements of the device without the need to add DC power converters to the fuel cell system to add additional fuel cell systems to meet the power demand of the device. For larger fuel cell configurations in particular, NASA's innovative technique results in a far less costly, more efficient means of power generation.
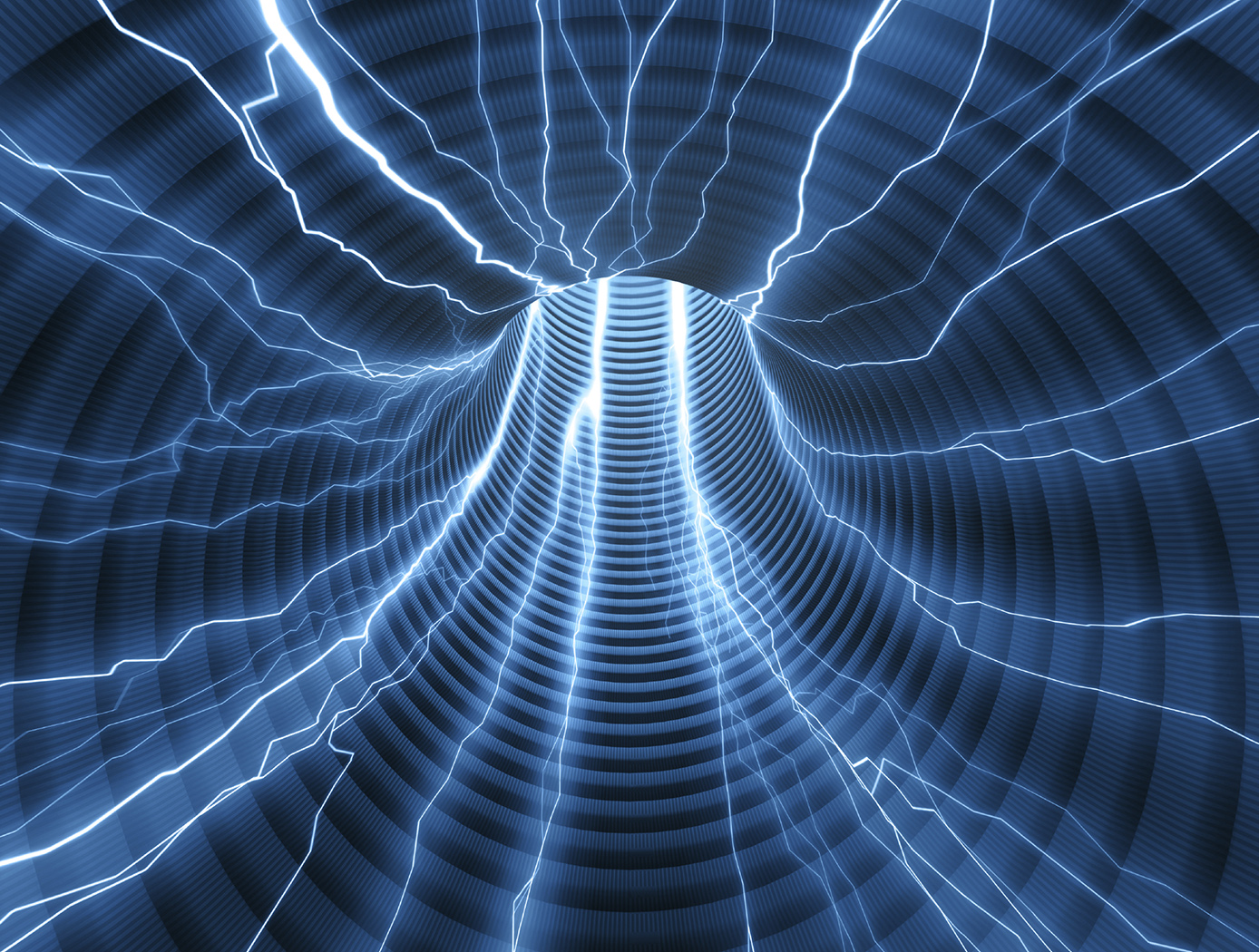
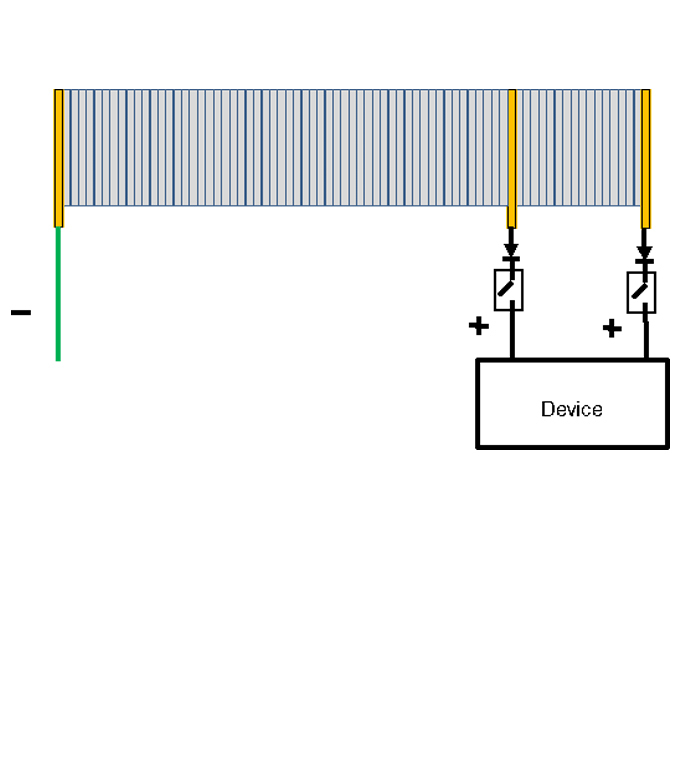
Benefits
- Less costly: Fuel cell systems can be built without the added cost of converters
- More efficient: This technique eliminates the need for an additional step in the process of generating usable power from fuel cells
- More reliable: This improvement decreases the part count within the design, thus reducing the number of potential points of failure in the system
- Reduced size: Removing the converters or additional fuel cell systems decreases the mass and volume of the overall system
Applications
- Power (e.g., energy generation and storage, emergency power, uninterrupted power systems)
- Aerospace (e.g., aircraft, spacecraft, weather stations)
- Communications (e.g., remote or back-up power)
- Military (e.g., portable field deployment, naval, submarines)
- Unmanned vehicles
- Turbines (e.g., cogeneration for residential and commercial use)
- Industrial machinery
Similar Results

Battery Charge Equalizer System
The innovation consists of a transformer array connected to a battery array through rectification and filtering circuits. The transformer array is connected to a drive circuit and a timing and control circuit, which enables individual battery cells or cell banks to be charged. The timing and control circuit connects to a charge controller that uses battery instrumentation to determine which battery bank to charge. The system is ultra lightweight because it uses much fewer than one transformer per battery cell. For instance, 40 battery cells can be balanced with an array of just five transformers. The innovation can charge an individual cell bank at the same time while the main battery charger is charging the high-voltage battery system.
Conventional equalization techniques require complex and costly electrical circuitry to achieve cell monitoring and balancing. Further, such techniques waste the energy from the most charged cells through a dummy resistive load (regulator), which is inefficient and generates excess heat. In contrast, this system equalizes battery strings by selectively charging cells that need it. The technology maintains battery state-of-charge to improve battery life and performance. In addition, the technology provides a fail-safe operation and a novel built-in electrical isolation for the main charge circuit, further improving the safety of high-voltage Li-ion batteries.

High-Voltage Power System for Hybrid Electric Aircraft Propulsion
Glenn's novel system supports the NASA Aeronautics Research Mission Directorate (ARMD) strategic plan to leverage advancements in technologies over the next 25 years and beyond, leading to new aircraft configurations with enhanced performance, improved energy efficiency, and reduced CO2 emissions. The electric system is a multi-megawatt micro-grid that converts mechanical energy to electric via generators, and electric energy to mechanical via motor-driven fans. This innovation would use the variation in aircraft throttle settings to produce a high-voltage (20 kilovolts), variable-frequency 9-phase AC distribution system. Using doubly fed electric machines (generator, propulsor, and flywheel) allows for field excitation that can cause variable-frequency or variable speed operation around the commanded throttle setting. The flywheel enables an energy storage system that recovers and reuses energy, while the flywheel slews with the throttle control using the electromagnetic torque produced by the doubly fed electric machine. This design permits both sub-synchronous and super-synchronous operation using limited field excitation power provided through power converters. Finally, the reduced switchgear mass facilitated through the use of a high-frequency AC system, setting-less protection zones, and simplified switches for fault clearance provides enhanced operational capability. This system can be controlled so that fault energy is minimized, preventing collateral damage to aircraft structures even with high voltage distribution. Glenn's innovative system adds performance, efficiency, reliability, and cost savings to cutting-edge hybrid electric technology.
This is an early-stage technology requiring additional development, and Glenn welcomes co-development opportunities.

Power Processing Unit (PPU) for Small Spacecraft Electric Propulsion
Key subsystems of a scalable PPU for low-power Hall effect electric propulsion have been developed and demonstrated at NASA GRC. The PPU conditions and supplies power to the thruster and propellant flow control (PFC) components. It operates from an input voltage of 24 to 34 VDC to be compatible with typical small spacecraft with 28 V unregulated power systems. The PPU provides fault protection to protect the PPU, thruster, PFC components, and spacecraft. It is scalable to accommodate various power and operational requirements of low-power Hall effect thrusters. An important subsystem of a PPU is the discharge supply, which processes up to 95% of the power in the PPU and must process high voltage to accelerate thrust generating plasma. Each discharge power module in this PPU design is capable of processing up to 500 W of power and output up to 400 VDC. A full-bridge topology operating at switching frequency 50 kHz is used with a lightweight foil transformer. Two or more modules can operate in parallel to scale up the discharge power as required. Output voltage and current regulation controls allow for any of the common thruster start-up modes (hard, soft or glow).

Stirling Thermoacoustic Power Converter and Magnetostrictive Alternator
Glenn's thermoacoustic power converter reshapes the conventional Stirling engine from a toroidal shape into a straight colinear arrangement. Instead of relying on failure-prone mechanical inertance and compliance tubes, this design achieves acoustical resonance by using electronic components. In a typical Stirling engine, the acoustical wave travels around a toroid and reflects back, forming a standing wave. In Glenn's device, by contrast, the wave instead travels in a straight plane where a transducer receives the acoustical wave and electrical components modulate the signal. A second transducer on the diametrically opposed side reintroduces the acoustic wave with the correct phasing to achieve amplification and resonance. Glenn's design allows the transducers to operate at high frequency while presenting a mass rather than stiffness impedance.
Glenn's magnetostrictive alternator uses stacked magnetostrictive materials under a biased magnetic and stress-induced compression. The acoustic energy from the engine travels through an impedance-matching layer (which can be formed from aerogel materials) that is physically connected to the magnetostrictive mass. Compression bolts keep the structure under compressive strain, allowing for the micron-scale compression of the magnetostrictive material and eliminating the need for bearings. The alternating compression and expansion of the magnetostrictive material creates an alternating magnetic field that then induces an electric current in a coil wound around the stack. This alternator produces electrical power from the acoustic pressure wave and, when the resonant frequency is tuned to match the engine, can replace the linear alternator to great effect.

Novel, Solid-State Hybrid Ultracapacitor Battery
The subject technology is an extension of closely related, solid-state ultracapacitor innovations by the same team of inventors. The primary distinction for this specific technology is the addition of co-dopants to affect the dielectric behavior of the barium titanatebased perovskite materials. These co-dopants include lanthanum and other rare earths as well as hydroxyl ions. The materials are processed at the nano scale, and are subjected to carefully designed thermal treatments as well.
The presence of the hydroxyl ions has been shown to provide several orders of magnitude increase in the capacitance of the dielectric material. Additionally, these high capacitance values are obtained at relatively low voltages found in current consumer and industrial electronics.
The capacitors tested to date are simple, single-layer devices. Ultimately, a range of manufacturing methods are possible for making commercial devices. Features of the technology enable manufacturing via traditional thick-film processing methods widely used in the capacitor industry, or via advanced printing methods for state-of-the-art printed electronics.
Future efforts will be made to advance the manufacturing and packaging processes to increase device energy density, including multilayer devices and packages