Improving Formability of Al-Li Alloys
manufacturing
Improving Formability of Al-Li Alloys (MFS-TOPS-61)
Novel heat treatment enables spin forming and stretch forming of Al-Li 2195
Overview
NASA scientists have designed a novel heat treatment process that significantly improves the formability of high-performance aluminum-lithium (Al-Li) 2195 alloy plate stock. The heat treatment process dramatically reduces cracking and also improves the yield and range of product sizes/shapes that can be spin/stretch formed. The improved yields also provide lower costs.
The NASA innovation enables the use of Al-Li 2195 alloy for large structures like rocket domes or fuel tanks of much lighter weights than if made using a conventional aluminum-copper (Al-Cu) alloy. While specifically designed to address Al-Li 2195 alloy, similar heat treatments may possibly improve the formability of other high-performance Al-Li alloys as well.
The Technology
Via this NASA innovation, a product is first heated to a temperature within the range of 204 to 343 degrees C for an extended soak of up to 16 hours. The product is then slowly heated to a second temperature within the range of 371 to 482 degrees C for a second soak of up to 12 hours. Finally, the product is slowly cooled to a final soak temperature of 204 to 343 degrees C before cooling to room temperature. The product so treated will exhibit greatly improved formability.
To date, the low formability issue has limited the use of lightweight Al-Li alloys for large rocket fuel tank dome applications. Manufacturing a dome by stretch forming typically requires multiple panels as well as multiple welding and inspection steps to assemble these panels into a full-scale fuel tank dome. Complex tensile and bending stresses induced during the stretch forming operations of Al-Li alloys have resulted in high rates of failure for this process. To spin form a large rocket dome, the spin blank must be prepared by joining smaller plates together using friction stir welding. However, friction stir welding produces a distinct metallurgical structure inside and around the friction stir weld that makes it very susceptible to cracking during spin forming.
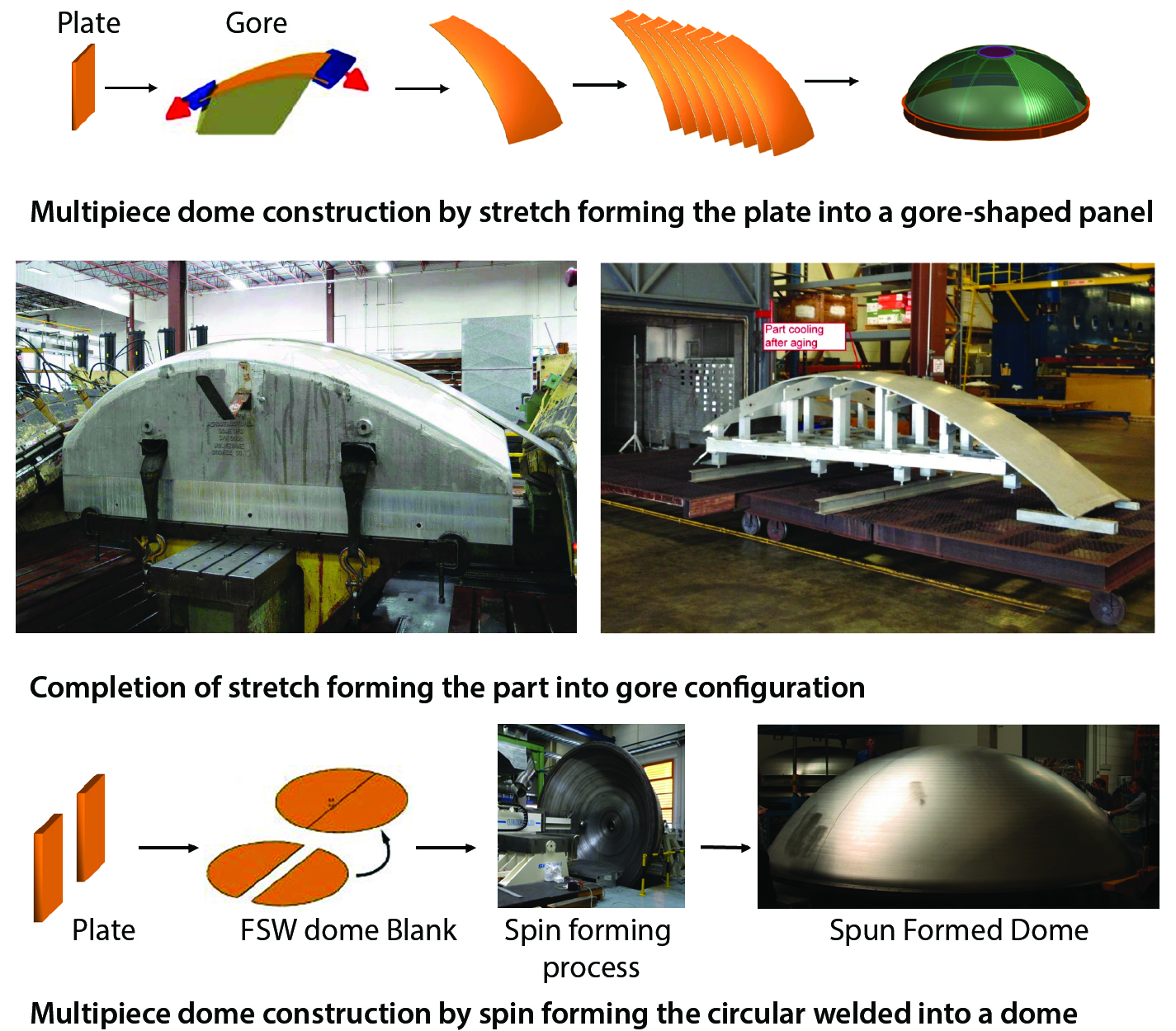
Benefits
- Enables the use of Al-Li alloys (Al-Li 2195) for the manufacture of large, lightweight aerospace structures via spin forming or stretch forming of a plate or extruded alloy.
- Dramatically reduces cracking during forming, thereby increasing yields and lowering costs.
- Has been used for producing actual parts; it is a proven technology ready for commercial implementation.
Applications
- Al-Li alloys are used in aerospace for rocket and fuel tank domes and other large panels or extruded structures produced by stretch forming or spin forming. Improving heat treatments for other Al-Li alloys would expand potential applications in aerospace as well as in recreation, transportation, and other industries in which high-strength, lightweight structures are needed.
Technology Details
manufacturing
MFS-TOPS-61
MFS-32954-1
Chen, P., & Russell, C. (2012, May 15). Mitigating Abnormal Grain Growth for Friction Stir Welded Al-Li 2195 Spun Formed Domes. NASA Technical Reports.
Martin, P. V., Chen, P., Gorti, S., & Salvail, P. (2014, January 14). Al 2195 T8 Gore Development for SLS Core and Upper Stage. NASA ADO Report.
Martin, P. V., Chen, P., Gorti, S., & Salvail, P. (2014, January 14). Al 2195 T8 Gore Development for SLS Core and Upper Stage. NASA ADO Report.
Tags:
|
Similar Results

Abnormal Grain Growth Suppression in Aluminum Alloys
Heat treatment of the deformed welds is desirable in order to restore the properties of the alloy negatively affected in the weld region. In these alloys, abnormal grain growth frequently occurs in friction stir welds during solution heat treatment, and is known to degrade key materials properties, such as strength, ductility and toughness. The innovation of inserting an intermediate annealing step covered here reduces abnormal grain growth during post-welding heat treatment, thereby allowing optimum mechanical properties. This is important where Al-Li alloys (and other heat treatable alloys) are friction stir welded followed by deformation processing and high performance, high reliability structural components are required for aerospace vehicles.

Precipitation Strengthened
Ni-Ti-Pd Shape Memory Alloys
Shape memory alloys (SMAs) are metals that can return to their original shape following thermal input and are largely used as actuators for various applications across industries including space, aeronautics, automotive, and biomedical. These alloys can require long processing times to stabilize through repeated training cycles and suffer from loss of strength and stability during use. Precipitation strengthening (using heat treatments to grow small nanoscale regions of distinct metal phases within the base alloy) is one way to mitigate these issues.
The NASA inventors have combined a modification of typical NiTi compositions by introducing Palladium (Pd) and small amounts of other metals and specific heat treatments to produce a novel SMA with improved properties. Specifically, the alloy is inherently stable, reducing both the need for extended processing times to stabilize the metal and the possibility of failure during high numbers of actuation cycles. Further, the SMA is specifically designed to have significantly lower hysteresis (the temperature difference between the heating and cooling) than current state of the art SMAs, i.e., at or below 10°C compared to 20°C or above. These properties combine for a SMA with enhanced properties usable across various industries and applications for reliable actuation.
The related patent is now available to license. Please note that NASA does not manufacturer products itself for commercial sale.

Economical, On-Demand GRCop Alloy Production
In-situ alloyed, additively manufactured GRCop components are produced by mixing elemental copper, chromium, and niobium powders and then selectively laser melting the powder mixture using powder bed fusion additive manufacturing. During laser melting, the chromium and niobium powders react to form Cr2Nb precipitates in the molten state, which are then dispersed in the pure copper matrix upon solidification. This dispersed precipitate phase is encapsulated within the pure copper matrix upon solidification, resulting in the characteristic microstructure of GRCop alloys with high thermal conductivity from the copper combined with superior mechanical properties from the precipitates. Optimization of process parameters like laser power has enabled up to 89% conversion of the constituent elements into Cr2Nb precipitates. The achieved rapid cooling rates of ~10^4-10^6 K/s enable formation of fine Cr2Nb precipitates around 0.1-1 micrometers in size. The technology is currently at a TRL 4, and NASA has developed and tested coupons of material using the new process. The related patent is now available to license. Please note that NASA does not manufacturer products itself for commercial sale.

High-Temperature Ni-Based Superalloy Composition
NASA's new Ni-based superalloy uses a powder metallurgy (PM) composition that inhibits the deleterious gamma-prime to gamma-phase transformation along stacking faults during high temperature creep deformation. Ni-base superalloys have excellent high temperature properties, mostly due to the presence of coherent precipitates. At higher temperatures, these precipitates are defeated by the diffusional shear dislocations producing intrinsic and extrinsic faults. Recent studies have found that, during deformation of turbine disk alloys at high temperature, Co, Cr, and Mo segregate to these faults (removing Ni and Al) inside the strengthening precipitates of these alloys. This represents a local phase transformation from the strengthening precipitate to the weaker matrix phase. Therefore, this elemental segregation significantly weakens the ability of a precipitate to withstand further deformation, producing faster strain rates in the alloy at higher temperatures. This invention presents a solution to prevent this type of segregation along these two faults to improve the creep properties of turbine disks and similar Ni-based alloys. By alloying a specific amount of eta phase formers (Ti, Ta, Nb, and Hf), the phase transformation to can be eliminated along 2-layer extrinsic stacking faults (SESFs) in precipitates without precipitating bulk eta phase. Also, by adding a certain amount of D019 formers (Mo and W), the phase transformation to can be mitigated along 1-layer intrinsic stacking faults (SISFs) without producing bulk sigma phase. This alloy composition incorporates both strengthening methods for use in jet turbine disks, though the composition has applications in other high-stress and/or high-temperature environments as are found in power plants, space launch systems, and other critical structural applications.

Creating Low Density Flexible Ablative Materials
The low density flexible ablator can be deployed by mechanical mechanisms or by inflation and is comparable in performance to its rigid counterparts of the same density and composition. Recent testing in excess of 400W/cm2 demonstrated that the TPS char has good structural integrity and retains similar flexibility to the virgin material, there by eliminating potential failure due to fluttering and internal stress buildup as a result of pyrolysis and shrinkage of the system. These flexible ablators can operate at heating regimes where state of the art flexible TPS (non-ablative) will not survive. Flexible ablators enable and improve many missions including (1) hypersonic inflatable aerodynamic decelerators or other deployed concepts delivering large payload to Mars and (2) replacing rigid TPS materials there by reducing design complexity associated with rigid TPS materials resulting in reduced TPS costs.