Cryogenic Hydraulically Actuated Isolation Valve
mechanical and fluid systems
Cryogenic Hydraulically Actuated Isolation Valve (MFS-TOPS-94)
Actuation requires only upstream pressure and 22-watt DC power supply
Overview
Researchers at NASA's Marshall Space Flight Center have developed a cryogenic isolation valve that utilizes the upstream line pressure of cryogenic fluids for actuation. Previously, the use of cryogenic fluids for actuation systems had been too difficult to control and resulted in unsafe operating conditions due to the cryogenic fluid used for actuation being separated from the main body of the valve. Once separated, the cryogenic fluid would heat too quickly and vaporize, resulting in high, volatile pressures. To avoid these issues, cryogenic fluid had historically been controlled and redirected using either electromechanical or pneumatic actuation systems. By using the upstream line pressure of the cryogenic fluid for actuation, NASA's cryogenic isolation valve eliminates the need for the complex support systems that are necessary with electromechanical and pneumatic actuation systems.
The Technology
NASA's cryogenic isolation valve technology uses solenoid valves powered by direct current (DC) electrical energy to control and redirect the energy stored in the upstream line pressure. Powering the solenoid valves only requires a DC power source capable of supplying 22 watts that can be distributed and controlled in an on/off manner. By achieving actuation using only upstream line pressure and a 22-watt DC power source, many additional support systems that are required for electromechanical and pneumatic actuation are eliminated. This reduction of parts results in several benefits, including reduced footprint, weight, and potential cost of the valve in addition to lower energy consumption.
NASA fabricated several operational prototype valves using this technology for a rocket company. The table below shows the results of tests performed on these valves under cryogenic conditions. Please contact the NASA MSFC Technology Transfer Office for additional information.
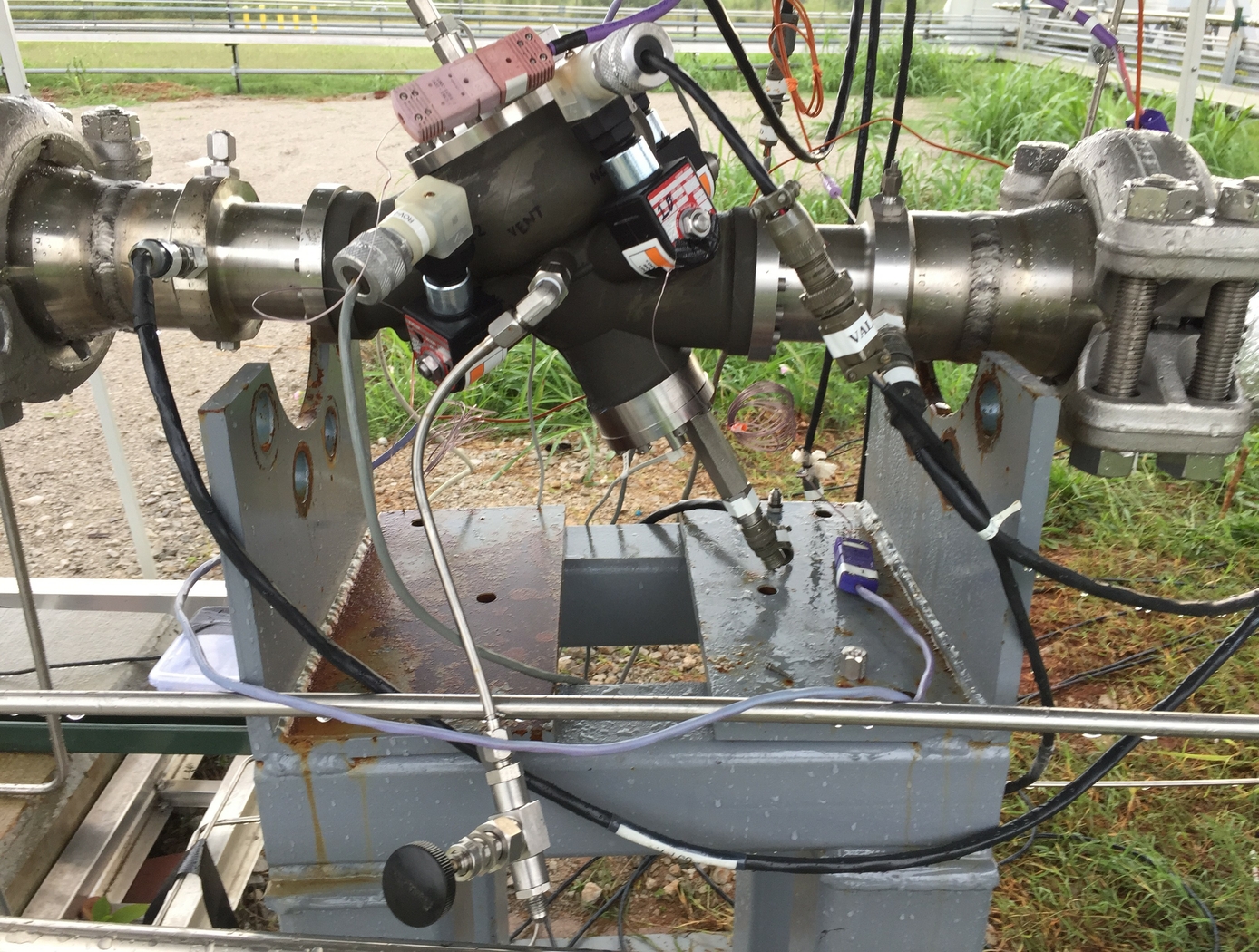
.jpg)
Benefits
- Requires only upstream line pressure and DC power source capable of 22 watts for actuation, eliminating the need for support systems; reducing footprint, energy consumption, and cost; and reducing weight by up to 63%
- Has no external dynamic seals and no external actuation device
- Contains only one moving flow element
- Designed to be serviceable and rebuilt in-line
- Performed an Oxygen Hazards Analysis (OHA) to guide the design and selection of materials, design volumes, and other necessary criteria to ensure the valve is safe for use in high pressure oxygen applications
Applications
- Commercial Space
- Liquified natural gas
- Air separation
- HVAC refrigerant
- Semiconductor manufacturing
- Pharmaceutical processing
Tags:
|
Similar Results

3D-Printed Injector for Cryogenic Fluid Management
NASA's TVS Augmented Injector includes an internal heat exchanger, a fluid injector spray head, and an external surface condensation heat exchanger - all combined with multiple intertwined flow paths containing liquid, two-phase, and gaseous working fluid. The TVS provides a source of coolant to the injector, which chills the incoming fluid flow. This cooled flow promotes condensation of the tank ullage dropping pressure and maintains incoming fluid flow. The system eliminates the potential for a stalled fill condition and reduces tank pressure during cryogenic fluid transfer. During fill operations, the tank vent can be closed early in the process before fluid is introduced, and, in some cases, the tank vent may not even need to be opened. Furthermore, the TVS Augmented Injector can remove sufficient thermal energy to reach a 100% liquid level in the receiver tank. A cryo-cooler can be used in place the TVS flow circuit for a zero-loss system. The TVS Augmented Injector couples internal fluid flow cooling and external surface ullage gas condensation into a single, compact package that can be mounted to small tank flanges for minimal impact insertion into any vessel. The injector is printed as one part using additive manufacturing, resulting in part count reduction, improved reproducibility, shorter lead times, and reduced cost compared to conventional approaches.
The injector may be of particular interest in applications where cryogenic fluid is expensive, fluid loss through vents is problematic, and/or achieving high filling levels would be helpful. The injector can benefit typical cryogenic fluid transfer between containers or, alternatively, can serve as a tank pressure control device for long-term storage using a fluid recirculation system that pumps fluid through the injector and sprays cooled liquid back into the tank. Additionally, where ISRU processes are employed, the injector can be used to liquefy incoming propellant streams.

Low-Cost, Long-Lasting Valve Seal
NASA's technique simplifies the seat installation process by requiring less installation equipment, eliminating the need for unnecessary apparatus such as fasteners and retainers. Multiple seals can be installed simultaneously, saving both time and money.
NASA has tested the long-term performance of a solenoid actuated valve with a seat that was fitted using the new installation technique. The valve was fabricated and tested to determine high-cycle and internal leakage performance for an inductive pulsed plasma thruster (IPPT) application for in-space propulsion. The valve demonstrated the capability to throttle the gas flow rate while maintaining low leakage rates of less than
10-3 standard cubic centimeters per second (sccss) of helium (He) at the beginning of the valves lifetime. The IPPT solenoid actuated valve test successfully reached 1 million cycles with desirable leakage performance, which is beyond traditional solenoid valve applications requirements. Future design iterations can further enhance the valve's life span and performance.
The seat seal installation method is most applicable to small valve instruments that have a small orifice of 0.5 inches or less.

Variable-Aperture Reciprocating Reed (VARR) Valve
The VARR valve has been designed to provide a variable-size aperture that proportionately changes in relation to gas flow demand. When the pressure delta between two chambers is low, the effective aperture cross-sectional area is small, while at high delta pressure the effective aperture cross-sectional area is large. This variable aperture prevents overly restricted gas flow. As shown in the drawing below, gas flow through the VARR valve is not one way. Gas flow can traverse through the device in a back-and-forth reversing flow manner or be used in a single flow direction manner. The contour shapes and spacing can be set to create a linear delta pressure vs. flow rate or other pressure functions not enabled by current standard orifices. Also, the device can be tuned to operate as a flow meter over an extremely large flow range as compared to fixed-orifice meters. As a meter, the device is capable of matching or exceeding the turbine meter ratio of 150:1 without possessing the many mechanical failure modes associated with turbine bearings, blades, and friction, etc.

Self-aligning Poppet
Without improvements in valve technologies, propellant and commodity losses will likely make long-duration space missions (e.g., to Mars) infeasible. Cryogenic valve leakage is often a result of misalignment and the seat seal not being perpendicular relative to the poppet. Conventional valve designs attempt to control alignment through tight tolerances across several mechanical interfaces, bolted or welded joints, machined part surfaces, etc. However, because such tight tolerances are difficult to maintain, leakage remains an issue.
Traditional poppets are not self-aligning, and thus require large forces to “crush” the poppet and seat together in order to overcome misalignment and create a tight seal. In contrast, NASA’s poppet valve self-aligns the poppet to the valve seat to minimize leakage. Once the poppet and seat are precisely self-aligned, careful seat crush is provided. Owing to this unique design, the invention substantially reduces the energy required to make a tight seal – reducing size, weight, and power requirements relative to traditional valves. Testing at MSFC showed that NASA’s poppet reduces leakage rates of traditional aerospace cryogenic valves (~1000 SCIM) by three orders of magnitude, resulting in leakage rates suitable for long-duration space missions (~1 SCIM).
NASA’s self-aligning poppet was originally targeted for aerospace cryogenic valve systems, especially for long-duration manned space missions – making the invention an attractive solution for aerospace valve vendors. The invention may also find use in the petrochemical or other industries that require sealing to prevent critical or hazardous chemicals from leaking into the environment. Generally, the invention may be suitable for any application requiring low-leak and/or long duration storage of expensive or limited resource commodities (e.g., cryogenic gases, natural gas, nuclear engines, etc).

Magnetically Damped Check Valve
NASA's Magnetically Damped Check Valve invention is a damping technology for eliminating chatter in passive valves. Because valve failure in space missions can cause catastrophic failure, NASA sought to create a more reliable check valve damper. The new damper includes the attachment of a magnet to the poppet in a check valve to provide stabilizing forces that optimize flow and pressure conditions. Test results have proven that the Magnetically Damped Check Valve offers substantial benefits.
The Magnetically Damped Check Valve works over a wide range of flow dynamics and eliminated chatter under all flow conditions tested, allowing valves to operate under various flow rates and pressures without a risk of degradation or total destruction from chatter. This technology could provide a more simple and cost-effective solution for valve manufacturers and system designers than solutions currently available in the market.
Applications for the new valve include use in aerospace or industrial processes. NASA's damping technology was originally designed for check valves, but could also benefit pressure regulators, relief valves, shuttle valves, bellows sealed valves or other passive valves.