High Flow Differential Cleaning
manufacturing
High Flow Differential Cleaning (MFS-TOPS-99)
Clean Complex Additively Manufactured Parts in Minutes - Not Hours or Days
Overview
Powder-based AM methods typically require post-fabrication component cleaning to remove residue powder from the surface and crevices of the part, a task that becomes increasingly difficult and time consuming with part complexity. Methods currently available to clean AM parts have significant drawbacks. Immersive cleaning using solvents or solutions can cause powder clumping. Forms of blasting (e.g., wet, bead, hydro, bristle, vacuum, etc.) work on line-of-site surfaces but are ineffective for recessed cavities. Such cleaning is typically manual, highly time consuming, and requires careful use of personal protective equipment to avoid powder inhalation. Thus, the AM market would benefit from a more automated, rapid, and effective method for cleaning complex parts.
The Technology
NASA developed this High Flow Differential Cleaning technology in response to in-house needs for a more automated and effective method to remove stubborn particles from complex parts fabricated using powder-bed-fusion equipment. The invention uses a large volume of pressurized air to quickly enter a cleaning chamber. Based on the Bernoulli principle and Continuity equation, the high flow results in significant air velocity and a decrease in pressure when airflow passes through smaller component orifices, which in turn removes remnant powder from the part. In one embodiment, the invention consists of a (1) high-pressure air compressor with ISO 8573 Class 2 drying capability, (2) a large pressure chamber with a fast-actuated valve system to, (3) a cleaning chamber containing various sensors, injection systems, (4) a test fixture designed for easy orientation adjustments, and (5) an expansion chamber allowing air to expand and drop in velocity, particles to settle, and filtered air to re-enter the room. This NASA technology can be implemented as a standalone cleaning system for powder bed fusion additively manufactured parts, or could be integrated into a packaged post-processing system offering. CT scans of complex NASA parts cleaned using a proof-of-concept system based upon the invention revealed very promising results.
NASA welcomes industry to test the cleaning speed and efficacy of the technology under an evaluation license.
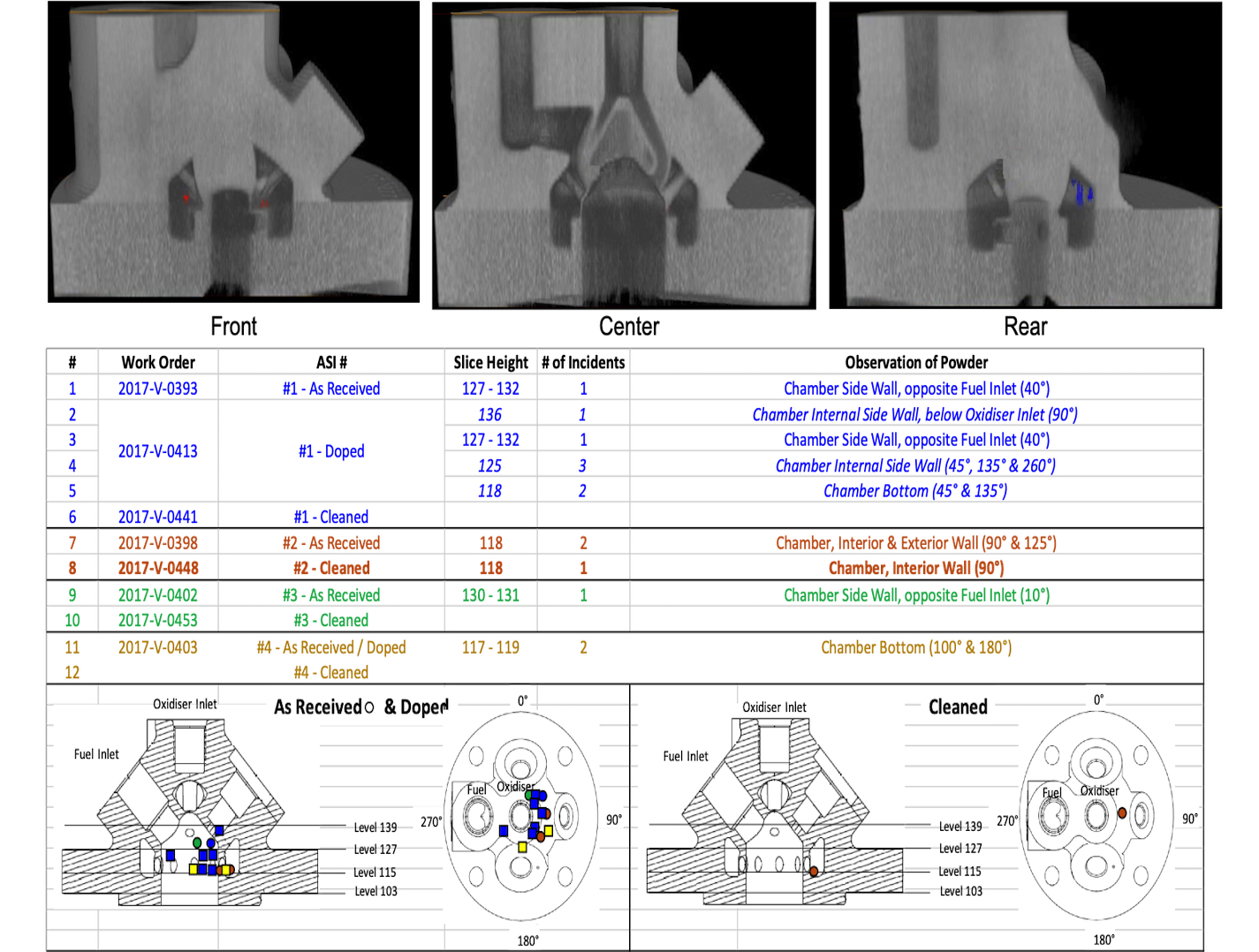
Benefits
- Fast, automated process: Parts are cleaned in seconds (minutes when including load/unload time), instead of hours or days
- Effective cleaning: CT-scans of cleaned parts revealed effective particle removal
- Works on complex parts: Removes remnant powder lodged in small channels and passageways found in complex AM parts
Applications
- Powder-based additive manufacturing, including direct metal laser sintering (DMLS), electron beam melting (EBM), selective heat sintering (SHS), selective laser melting (SLM), and selective laser sintering (SLS)
- Post-processing of complex additively manufactured parts
Technology Details
manufacturing
MFS-TOPS-99
MFS-33553-1
MFS-33553-1-PCT
Similar Results

Self-Cleaning Germicidal Door Handle
As previously mentioned, doorknobs, levers, and handles are commonly manufactured using plastic or stainless-steel materials. Since bacteria and viruses can survive for extended periods of time on such materials, these objects can facilitate the transmission of pathogens between users. Furthermore, it is burdensome and costly for organizations to implement cleaning protocols where door handles are cleaned continuously. To address this issue, UV sterilization systems have been used for door handles. However, such systems often require bulky mounting equipment, possess sub-optimal aesthetics, and are high price point products leaving significant room for improvement.
To overcome the limitations of using cleaning agents, sprays, or bulky high-cost sterilizing systems, NASA developed an Ultraviolet Germicidal Door Handle. This invention largely resembles a conventional doorhandle; however, it contains a compact, far UV-C LED light device that attaches to the handle via mounting threads and disinfects surfaces (i.e., kills or inactivates pathogens). The device is controlled by a sensor that activates the UV-C light for a specified time to disinfect the surface after each use. After disinfection is completed, a timer sequence switches the light off and prepares for the next use. Due to the simple, thread-based mounting system, the UV-C LED is easily removable from the door handle. The UV-C LED has several convenient features including a USB charging port, I/O switch, and low battery indicator light.
The Ultraviolet Germicidal Door Handle greatly minimizes the risk of harmful pathogens, such as SARS-CoV-2, being transmitted between people using the same door. Various versions of the Ultraviolet Germicidal Door Handle could be marketed to accommodate different designs of door handles and levers.

Particle Contamination Mitigation Methods
The following methods can be used individually or in combination to generate superhydrophobic surfaces:
Synthesis of novel copolyimide oxetanes with unique surface properties
The technology is the synthesis of a polyimide coating or film with a modified surface chemistry shown in Figure 1. A minor amount of an oxetane reactant containing fluorine is added to the polyimide, and the oxetane preferentially migrates to the surface, enabling relatively high concentrations of fluorine at the surface, without compromising the functional performance of the bulk of the polymide coating/film.
The copolymers exhibit mitigation of particle adhesion and fouling from exposure to various particulate and biological contaminants and exhibit reduced surface energy and increased surface fluorine content at extremely low oxetane loadings relative to the imide matrix (see Figure 2). Additionally, the short fluorinated carbon chains do not bioaccumulate, reducing the environmental impact of these materials.
Modifying surface energy via laser ablative surface patterning
This method uses a laser to create nanoscale patterns in the surface of a material to increase the hydrophobicity of the surface (see Figure 2). The benefits of hydrophobic surfaces include decreases in friction and increases in self-cleaning properties. This is an advantageous method of surface modification because it is fast and single-step, promises to be scalable, requires no chemicals, could be applied to a variety of materials, and does not require a planar surface for patterning.

Activated Metal Treatment System (AMTS) for Paints
PCBs have been shown to cause cancer in animals and to have other adverse effects on immune, reproductive, nervous, and endocrine systems. Although the production of PCBs in the United States has been banned since the late 1970s, many surfaces are still coated with PCB-laden paints. The presence of PCBs in paints adds complexity and expense for disposal. Some treatment methods (e.g., use of solvents, physical removal via scraping) are capable of removing PCBs from surfaces, but these technologies create a new waste stream that must be treated. Other methods, like incineration, can destroy the PCBs but destroy the painted structure as well, preventing reuse.
To address limitations with traditional abatement methods for PCBs in paints, researchers at NASAs Kennedy Space Center (KSC) and the University of Central Florida have developed the Activated Metal Treatment System (AMTS) for Paints. This innovative technology consists of a solvent solution (e.g., ethanol, d-limonene) that contains an activated zero-valent metal.
AMTS is first applied to the painted surface either using spray-on techniques or wipe-on techniques. The solution then extracts the PCBs from the paint. The extracted PCBs react with the microscale activated metal and are degraded into benign by-products. This technology can be applied without removing the paint or dismantling the painted structure. In addition, the surface can be reused following treatment.

Alternative Transparent Coating Lotus Suitable for Optics with Vacuum Deposition Layer
In addition to previous LOTUS coating formulations, an additional optical formulation may be applied via vacuum deposition. This coating forms a top layer and may be applied in different thicknesses that serve to enhance its hydrophobic properties. The vacuum deposited material may comprise fluorinated ethylene propylene or a similar material. This coating is transparent and can be used on optical components or any other applications requiring a clear coating.

Novel Process to Create Structured Membrane Films for Micromachining Applications
The technology is an innovative process for creating metal-patterned, structured membranes for micromachining applications. The method uses potassium hydroxide to remove silicon, in combination with XHRiC. Hafnium metal is first patterned onto a silicon nitride wafer, which serves as the starting substrate. XHRiC is then applied to the wafer, followed by patterning with photoresist and etching using O2 plasma to define cut slots in the membrane. The photoresist is then removed.
Next, the wafer is bonded to a Pyrex carrier wafer with wax, and the backside of the silicon nitride is patterned and reactive-ion etched. The wafer is then placed in hot potassium hydroxide for 16 hours to remove the silicon layer, creating a silicon nitride membrane. The wafer is subsequently placed in acetone to dissolve the wax. The wafer is resecured to the Pyrex carrier wafer, and the topside of the silicon nitride membrane is subjected to reactive-ion etching. Finally, the XHRiC layer is removed using O2 plasma, and the Pyrex handle wafer is released, resulting in a metal-patterned silicon nitride membrane with cut slots.
This novel process supports the creation of structured membranes with a wide range of applications in MEMS fabrication. The use of XHRiC as a patterned hard mask and/or etch protection material enables its application in various MEMS devices. The process can be used to fabricate cut membranes, micro/nano structures, and ultra-thin films for device applications, making it an excellent candidate for MEMS foundry companies and accelerometer manufacturers. It has reached a Technology Readiness Level (TRL) 5 (component validation in a relevant environment) and is now available for patent licensing.