Hyper-Distributed RFID Antenna (HYDRA) System
Sensors
Hyper-Distributed RFID Antenna (HYDRA) System (MSC-TOPS-111)
Novel multiplexing RFID antenna system improves range while reducing cost and complexity
Overview
Innovators at NASA Johnson Space Center have developed a method and apparatus to multiplex Radio Frequency Identification (RFID) signals efficiently. The resulting Hyper-Distributed RFID Antenna (HYDRA) system enhances distribution of the RFID reader signal, providing improved coverage for large areas as well as for small, fixed regions requiring a high density of reader antennas. This greater coverage translates into better RFID sensing capabilities, higher localization accuracy, and enhanced logistics awareness.
Many conventional RFID applications require adding more readers and antennas to increase coverage in existing areas and to improve localization. Employing conventional multiplexer switches can reduce the need for additional readers but require additional control and power cabling. Both conventional options will increase mass, size, and cost of the overall infrastructure to improve sensing performance. The HYDRA system, which uses microprocessor-based low-mass multiplexers, reduces the need for additional readers and cabling over the conventional prior art, and it operates with smaller-sized antennas. As a result, the advantages of the HYDRA system include the ability to transmit data at low power, improve coverage performance, increased capability to localize RFID tags, along with reduced cost, complexity, and mass.
The Technology
Components of the HYDRA system include an RFID reader (aka an RFID transceiver or interrogator), RF cables, antennas, and one or more Intelligent Multiplexer Modules (IMMs). The IMM is the core building block of the HYDRA system. In one of its basic embodiments, the IMM comprises an RF directional coupler, RF switch, RFID chip, micro-controller, and power generation and management hardware. In this basic implementation, a single RF port from the RFID reader is attached to the IMM and transfers power thereto. Internally within the IMM, the RF directional coupler diverts a small amount of RF power to rectification and power management circuitry for conversion to DC power that drives the RFID chip, microcontroller, and RF switch. The RFID chip enables communication with the RFID reader and allows the reader to administer changes to the microcontroller‘s embedded software. The microcontroller controls the RF switch, which passes power along to one or more output channels. Connections to the output channels can include antennas, additional IMMs, or other sensors.
The HYDRA system may include numerous alternate embodiments to enhance and customize the basic functionality. In one embodiment, the microcontroller is replaced with a simple timer. In another embodiment, the switch has multiple output ports to connect to a distributed chain of HYDRA system or local antennas. Also, the entirety of RF power exiting a HYDRA module can be rectified and used to power a local sensor node, which could be implemented via WiFi or Bluetooth Low Energy (BLE). Features of the HYDRA system include the ability to cover both open regions and enclosures, the ability to switch RF power to an unused load for assisting in the resolution of tag antenna ambiguities, and the ability to accept plug-and-play add-ons such that the reader’s software can use the system without requiring any embedded modifications.
The HYDRA system is technology readiness level (TRL) 7 (system prototype demonstrated in an operational environment) and is now available for patent licensing. Please note that NASA does not manufacture products itself for commercial sale.
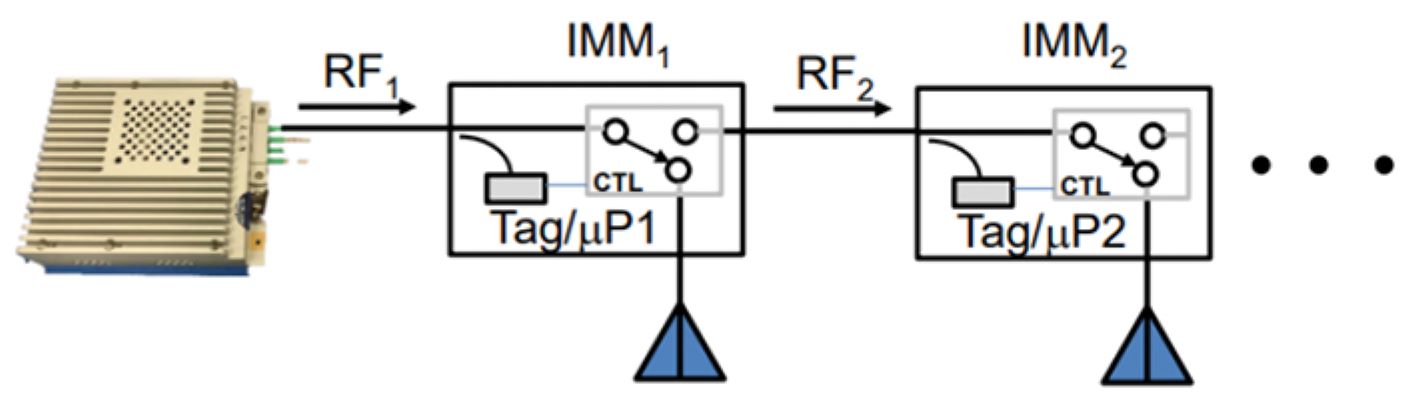
Benefits
- Plug-and-play installation allows direct drop-in replacement for existing antennas in many RFID systems.
- Improved functionality over conventional RFID antenna systems by extending sensing range of RFID readers and improving location accuracy.
- Lower cost for enhanced performance: reduces overall costs by eliminating the need for multiple RFID readers and additional cabling infrastructure.
- Small form-factor requires minimal space for implementation including number of cables and connections.
- Versatile: adaptable functionality provided by numerous alternate configurations and embodiments.
Applications
- Aerospace: locates inventory of mission items in and around vehicle
- Agriculture: helps farmers determine health condition of produce: technology allows supply chain to add information remotely to tag
- Medical: helps staff manage medical devices and supplies; can track patients
- Retail: tracks inventory and shipment check-in, automates ordering
Tags:
|
Similar Results

Agile RFID Antenna System
Current RFID readers, such as the EPC Global Class 1 Gen 2, are limited by narrow bandwidth restrictions, maximum transmit power, and a limited number of RF ports, which results in relatively coarse ranging resolution and accuracy, limited techniques for localization, and limited antenna functionality. Some of the currently available solutions, such as using larger antennas or adding switched multiplexers, often result in unacceptable cost, volume, aesthetics and mass penalties. The Agile RFID Antenna System integrates a frequency multiplexer into the RFID reader antenna system to provide greater antenna functionality without requiring additional reader RF ports, resulting in improvements in reader-tag communications read accuracy, read range, and localization.
The Agile RFID Antenna System is at a TRL 8 (Technology has been proven to work in its final form and under expected conditions) and has been used on the International Space Station to support logistics management and it is now available for your company to license and develop into a commercial product. Please note that NASA does not manufacture products itself for commercial sale.

Low Mass Antenna Boosts RFID Device Performance
NASA’s HYDRA system enables a new approach in routing the RFID signal, greatly increasing extensibility and the number of antennas that can be served by a single reader. However, increasing the number of antennas in any environment is often undesirable unless the antenna size is inconspicuous. Basing this RFID dual mode antenna on a quarter-wavelength structure allows it to be smaller than an antenna designed for half-wavelength structure, reducing overall mass.
NASA’s RFID dual mode antenna is enabled by utilizing two different types of resonance modes – a “slot” mode and a microstrip “patch” mode. An innovative feed architecture allows for coupling from the RFID reader into both modes, with the impedance of each mode approximately equal at respective resonant frequencies. The antenna is designed such that each mode resonates at a different portion of the operating bandwidth, and further with each mode radiating an orthogonal polarization to the other. Frequency-hopping RFID protocols, used in conjunction with this antenna, result in the polarization diversity required for readers to reliably communicate with arbitrarily oriented RFID tags.
Numerous commercial applications exist for this RFID dual mode antenna. Examples may include usage in a multiple antenna architecture that is connected to a single reader in an open-air region, in a small, enclosed region such as a cabinet drawer, or through a combination of open and closed regions.
This RFID dual mode antenna has a technology readiness level (TRL) 7 (system prototype demonstrated in an operational environment) and is now available for patent licensing. Please note that NASA does not manufacture products itself for commercial sale.

RFID Tags Collaborate for Data Retrieval
Commonly used RFID protocols are widely accepted because they are inexpensive and easy to implement. However, the associated low transmit power and narrow bandwidth typically result in coarse local-ization estimates. Often it is desirable to know the precise location of assets without reverting to an entirely different and more expensive protocol. Additionally, many industrial and other applications may desire technology that confirms the mating of components. This new program-mable sensor tag technology facilitates both precise localization and mating confirmation in-part by allowing the RFID sensor tag to become a type of distributed low-cost reader.
To determine a tag attachment, this innovation utilizes a fixed location RFID sensor tag that incorporates a receptacle node to measure an electrical “influence” through resistance, capacitance, inductance, etc. Assets for which localization is desired are outfitted with “influence tags” – devices that produce a set of distinguishable responses when placed in the receptacle region of the RFID sensor tag. Mating or connections are confirmed when electrodes from an influence tag become attached to matching electrodes on a sensor tag’s receptacle node. Information obtained by the RFID sensor tag is stored in its local memory bank through which a dedicated reader can retrieve influence tag information.
Potential applications exist for this technology where specific assets need to be precisely located and/or confirmation is needed when two parts have been correctly connected or attached. This RFID tag technology allows the retrieval of inventory status information in an energy efficient manner from inexpensive, small form factor hardware. Robotic retrieval of assets can be more easily facilitated with this innovation.

RFID Range Extension and Priority Data Forwarding
This novel technology builds upon a previously (NASA-developed) store-and-forward overlay architecture using COTS RFID protocols for BAP devices. It enables the range-extension and priority forwarding of critical sensor-collected data, even when an RFID interrogator is not in range. With this method, an RFID sensor maintains data queues of varying priority, maintaining at least one high priority queue.
When high priority data is collected, the RFID sensor activates a BAP mode that enhances the effective range of the RFID link to the interrogator. After high priority queues are cleared, BAP mode is deactivated to preserve onboard battery life and passive RFID operations resume for proximity-based data delivery.
This technology may deliver the most value in applications where long battery lifetime and remote sensing/data collection are essential and when regularly scheduled data transfer may not be available or possible if the target is out of the normal coverage area. The RFID sensor tags described here can operate in a low to no power mode and collect data until a trigger or threshold value is measured. At this time, the critical data can be transmitted from outside passive RFID coverage areas to the nearest interrogator.
Although this technology was developed to enhance the effective range of CO2 sensors worn by astronauts aboard the International Space Station, it could find additional applications in food, pharmaceutical, and other industries whose perishable and/or fragile goods rely on a stable climate throughout the transport and storage lifecycle.

RFID Tag for Long Range and Wide Coverage Capabilities
The RFID Tag with Long Range and Wide Coverage Capabilities technology allows a RFID tag to direct a RFID reader beam signal back in the direction of arrival. This technology requires no added power to provide telemetry for long range readers by using multiple beams instead of one narrow beam signal. Each of the predetermined number of beams is typically associated with a unique identification number to derive bearing information. This innovation is suited for IC-based RFID tags as well as Surface Acoustics Wave (SAW) tags, which are useful for extreme environments.
The technology improves the ability to obtain telemetry (quantity, location, or sensor information) without GPS over a distant range. When the tag reports its identification, it also provides angular information to the source, which makes this technology useful for navigation and mapping applications. Because the technology provides an estimated angle between the signal antenna and the surface of each tag, the technology is able to triangulate the position of a mobile item identified with a RFID tag. The same innovation can be integrated to a RFID reader in order to enhance its range and distribute power to passive tags. The innovation has commercial applications in construction, oil and gas, seaport/harbor management, Internet of Things (IoT) and many more industries.