Search
manufacturing

Predicting Plug Weld Quality
Friction plug welding is a process in which there is a small rotating part (plug) being spun and simultaneously pulled (forged) into a larger part to fill or repair a hole or join two pieces (functioning like a rivet). Learning from 1,500+ quality "known" plug welds, NASA’s experts build a load curve that, when combined with the welders’ knowledge of strain size, predicts the properties of a plug weld. The software monitors load, spindle speed, torque, displacement speed and distance, and the material properties and dimensions of the sample. The software correlates changes in the process parameters to mechanical testing of ultimate tensile strength. The software works for several Aluminum alloys such as 2015, 2195, and 2219. NASA is using the technology in its current work for closing out the termination hole of some friction stir welds. FPW is also used for repairs and as a potential replacement for rivets.
Environment
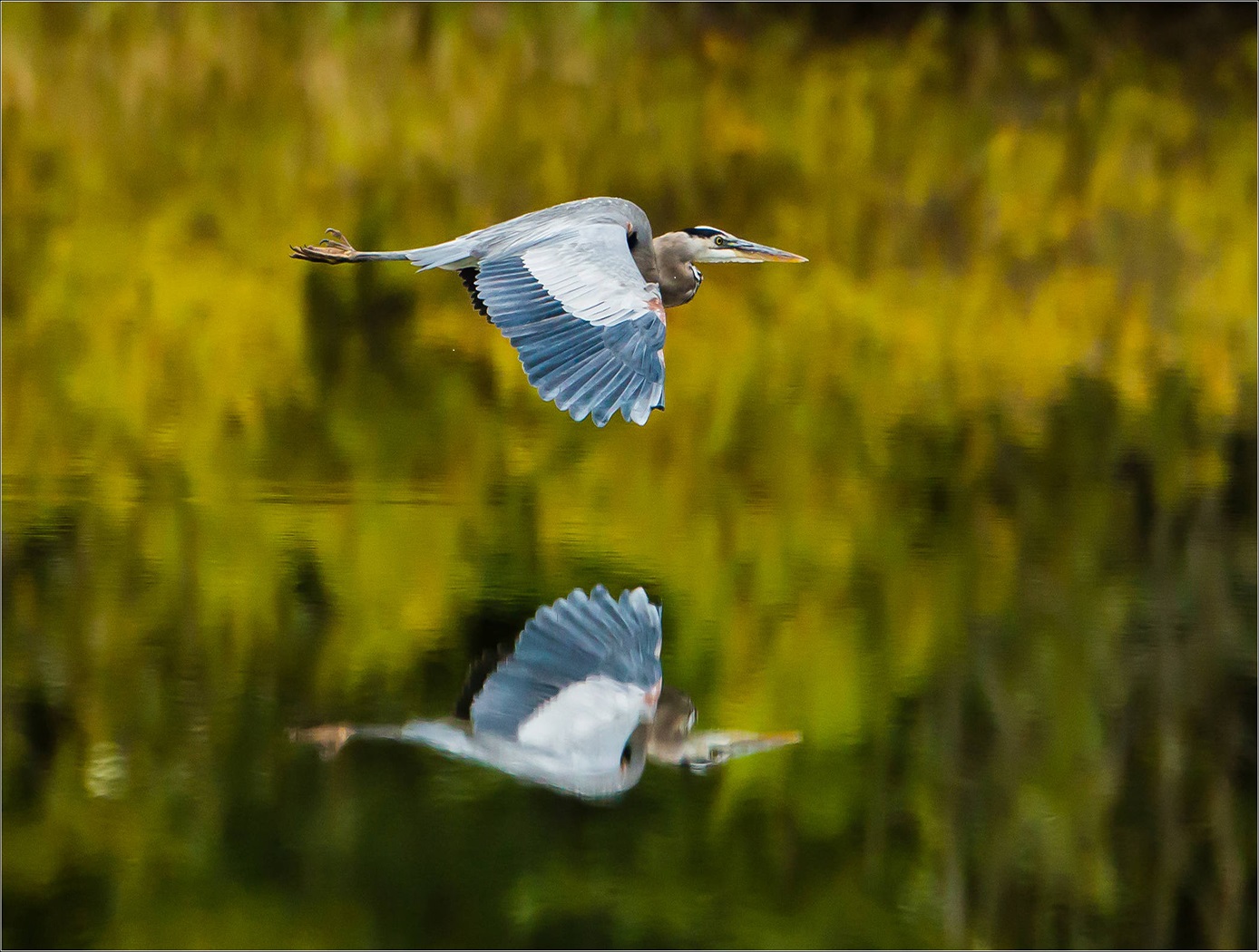
Wastewater Treatment and Remediation
NASA's system was developed for smaller-scale, space-based applications. However, the technology is scalable for larger industrial and municipal water treatment applications. Implementation of the Ammonia Recovery System could significantly reduce nitrogen content from water treatment processes, meaningfully improving the quality of water. This system offers a novel way to reduce nitrogen water pollutants, while allowing for the nitrogen to be collected and reused- reducing environmental and public health risks and providing an environmentally friendly fertilizer option. NASAs environmental solutions work to sustain life on earth through space based technology
The adaptable nature of this system gives it potentially broad applications in a wide variety of industries; it is particularly ideal for on-site remediation of wastewater in places like condo complexes, hotels and water parks. Current methods of ammonia recovery could not meet NASAs mission requirements, so a new process was devised to optimize for high ammonia selectivity, simplicity, low volume , low power usage and zero contaminants in the effluent. To do this, NASA designed a novel regenerable struvite-formation system for the capture of ammonia. This system has three primary functions:
1) Removal of ammonia from wastewater using a media that is highly selective for ammonia
2) Capture of the ammonia for later use (e.g., as a fertilizer)
3) Regeneration of the capture media for reuse in the system
instrumentation
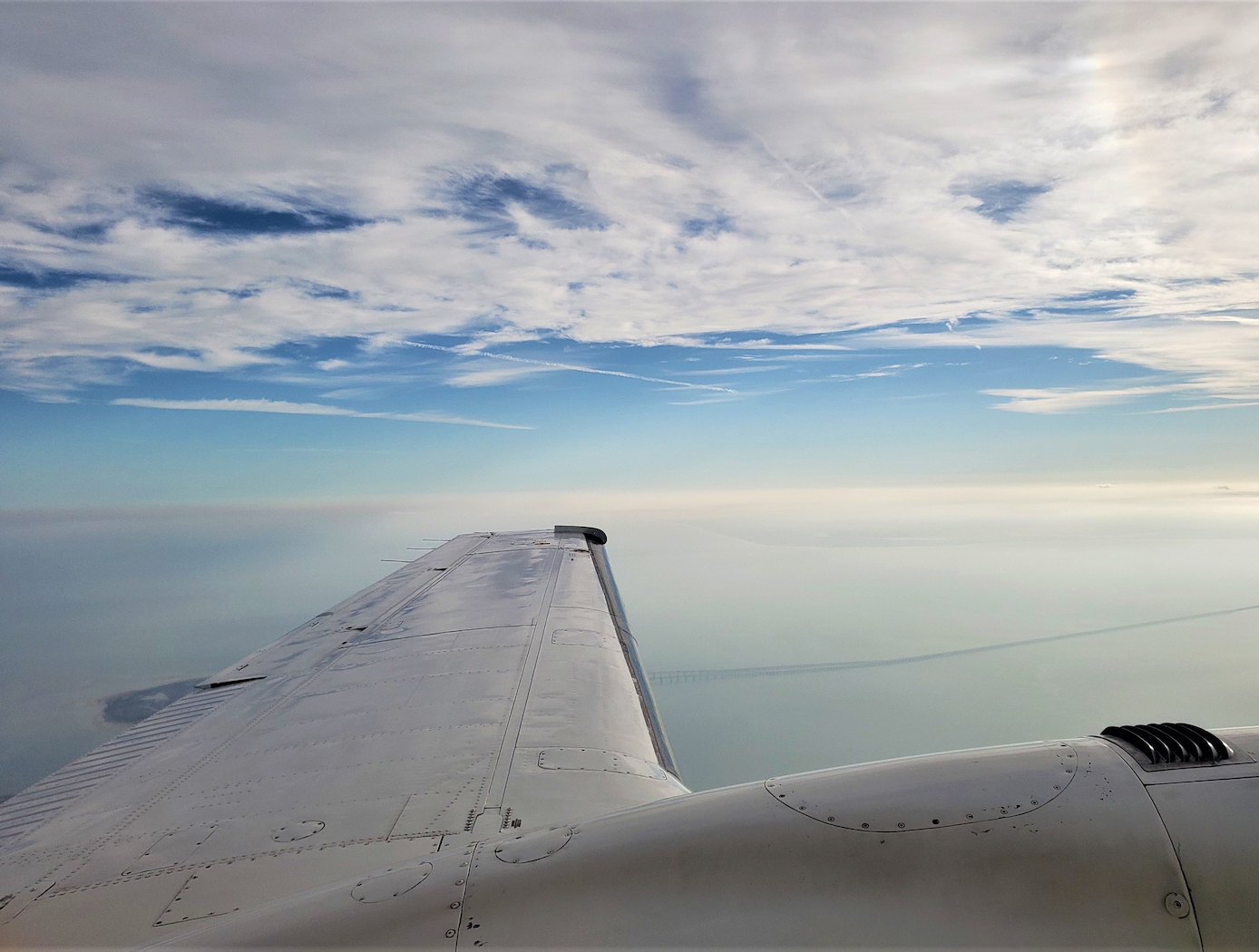
Fast & Accurate Composite Bond Strength Measurement
NASA's Method of Evaluating Adhesive Bond Strength is an accurate, robust, quantitative, and nondestructive bond strength measurement method that meets an immediate need in composite manufacturing. Even with careful control of the bonding procedure, destructive testing has shown that bonded joint strength shows substantial variation. Prior art in the field is insensitive to weak interfacial bonding, which leads to poor service life and potential catastrophic failure. Using NASA's method, phase measurements are acquired at a single frequency and then swept to obtain measurements at other frequencies. Narrowband filtering removes extraneous frequencies, which allows for much lower phase measurement uncertainty than other methods. Digital sine wave generation allows for better phase measurement resolution. The resultant system is a phase-based ultrasonic measurement tool for interrogating bonded joints and detecting weak adhesion with superior sensitivity than the state of the art. This new method models adhesive interfaces as a distributed spring system, where the interfacial stiffness constants of the joint can be determined from the zero- crossing frequency of the phase response and the "sharpness" or slope of the phase response. Previous theoretical research has shown that a linear correlation exists between interfacial stiffness constants and mechanically-measured interfacial bond strength. As such, the ultrasonic phase measurement method identifies intermediate bond strengths, rather than simply detecting good or bad bonds. This technique verifies bond quality in metal and composite joint systems, including those commonly found in aerospace, automotive, and many other transportation and infrastructure designs. The demonstrated ultrasonic phase method is applicable to a variety of bonding material systems.