Search
robotics automation and control
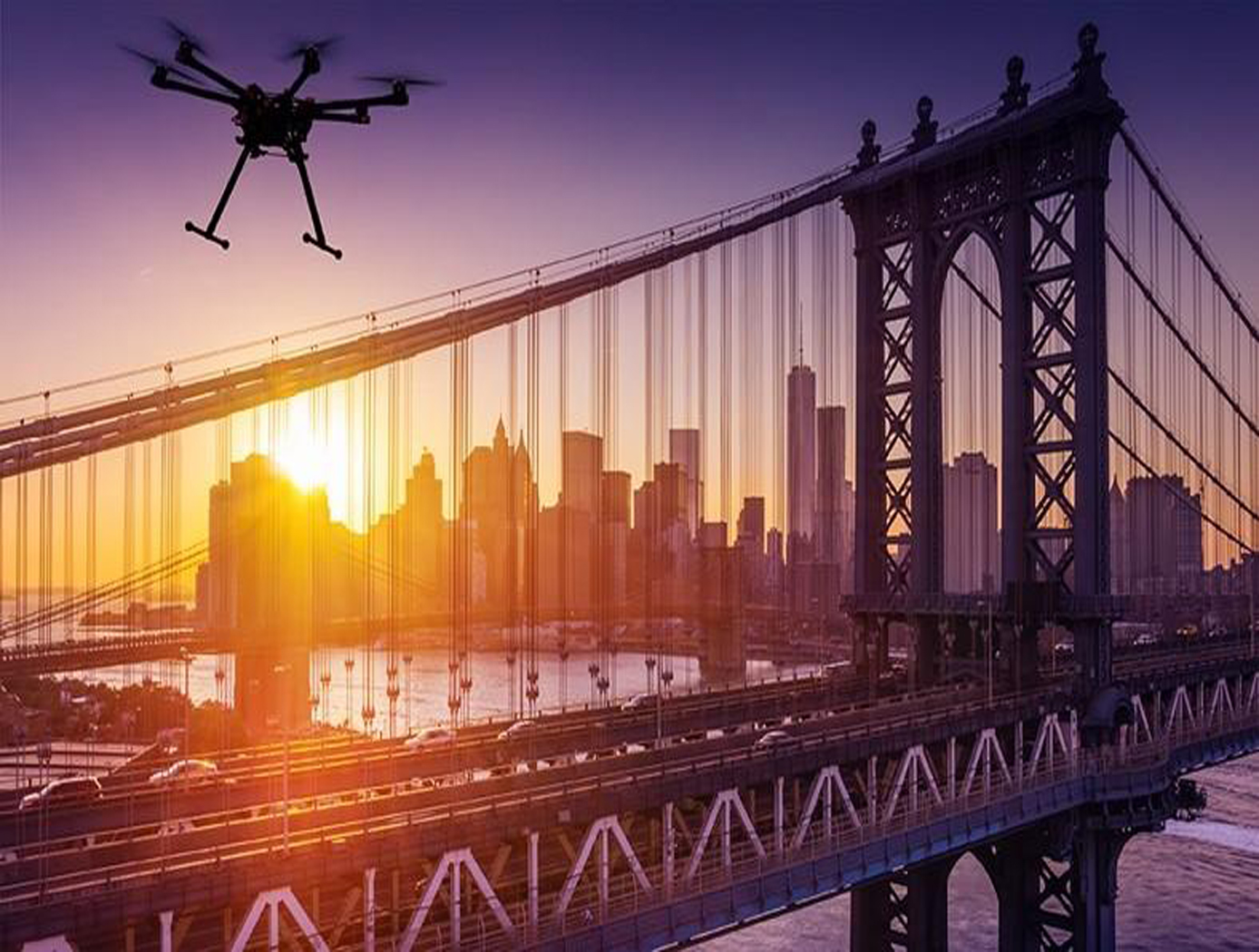
Airborne Machine Learning Estimates for Local Winds and Kinematics
The MAchine learning ESTimations for uRban Operations (MAESTRO) system is a novel approach that couples commodity sensors with advanced algorithms to provide real-time onboard local wind and kinematics estimations to a vehicle's guidance and navigation system. Sensors and computations are integrated in a novel way to predict local winds and promote safe operations in dynamic urban regions where Global Positioning System/Global Navigation Satellite System (GPS/GNSS) and other network communications may be unavailable or are difficult to obtain when surrounded by tall buildings due to multi-path reflections and signal diffusion. The system can be implemented onboard an Unmanned Aerial Systems (UAS) and once airborne, the system does not require communication with an external data source or the GPS/GNSS. Estimations of the local winds (speed and direction) are created using inputs from onboard sensors that scan the local building environment. This information can then be used by the onboard guidance and navigation system to determine safe and energy-efficient trajectories for operations in urban and suburban settings. The technology is robust to dynamic environments, input noise, missing data, and other uncertainties, and has been demonstrated successfully in lab experiments and computer simulations.
Aerospace
Method And System for Enhancing Vehicle Performance and Design Using Parametric Modeling and Gradient-Based Control Integration
The parametric modeling system allows for the integrated design and optimization of aerospace vehicles by unifying physical and control subsystems within a single computational model. The system includes representations of the vehicle’s geometry, structural load, propulsion, energy storage, and GNC systems. The system performs sensitivity analysis on key performance metrics (e.g., fuel consumption, heat load, and mechanical forces) to determine how changes in design parameters affect overall performance. By incorporating real-world conditions, such as wind variations and sensor noise, the system allows for the use of real-time feedback to refine vehicle designs. The optimization process uses a gradient-based algorithm to iteratively adjust parameters so that constraints such as structural integrity, thermal protection, and fuel capacity are met. The system generates a Pareto front representing trade-offs between performance metrics that allow engineers to visualize optimal designs for different mission profiles, which enhances design accuracy while reducing the need for expensive physical testing.