Search
mechanical and fluid systems
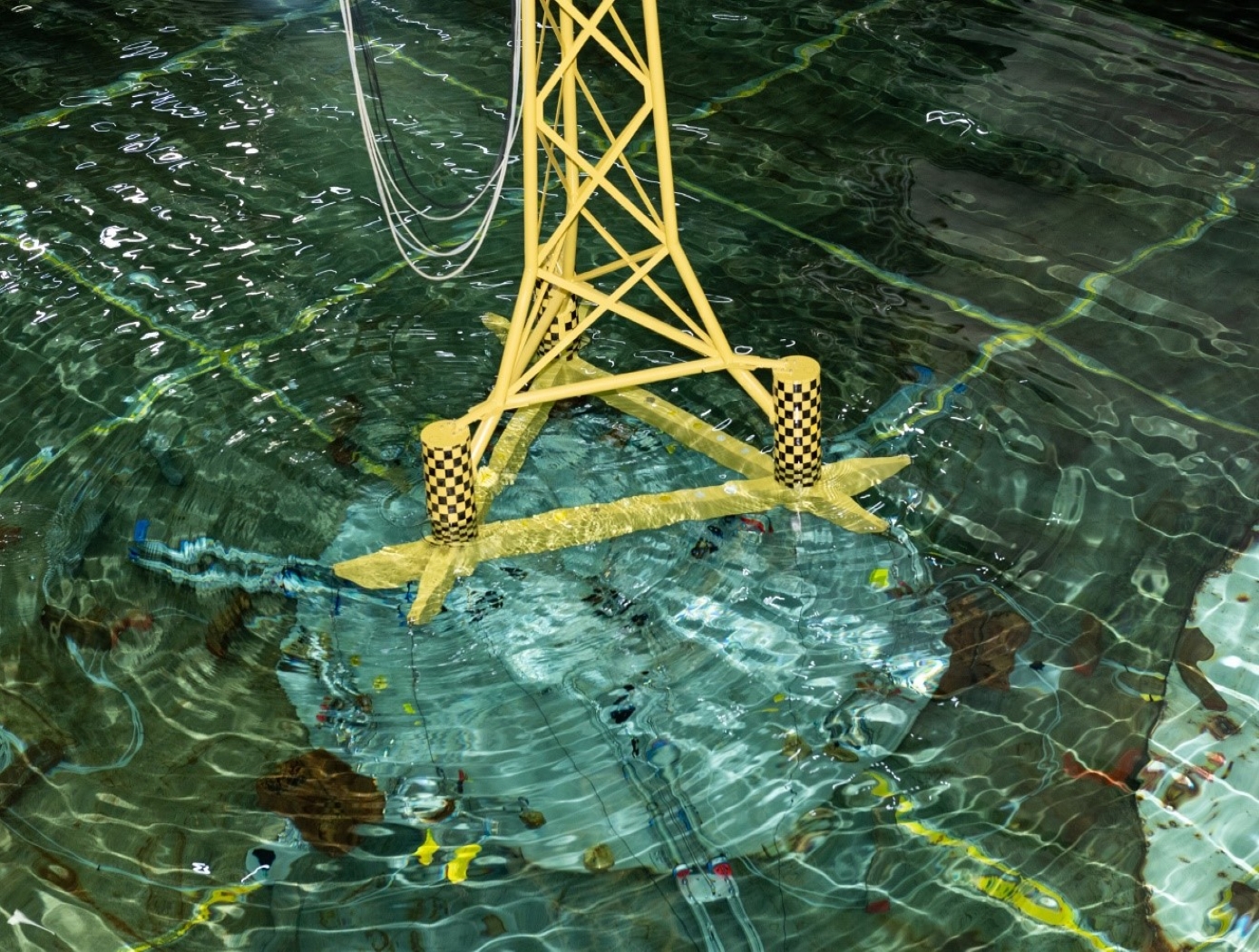
Tension Element Vibration Damping
NASAs Tension Element Vibration Damping technology presents a novel method of managing the dynamic behavior of structures by capturing the vibrational displacement of the structure via a connecting link and using this motion to drive a resistive element. The resistive element then provides a force feedback that manages the dynamic behavior of the total system or structure. The damping force feedback can be a tensile or compressive force, or both. Purely tensile force has advantages for packaging and connection alignment flexibility while combined tensile/compression forces have the advantage of providing damping over a complete vibratory cycle.
This innovation can be readily applied to existing structures and incorporated into any given design as the connecting element is easily affixed to displacing points within the structure and the resistive element to be located in available space or a convenient location. The resistive element can be supplied by any one of either hydraulic, pneumatic or magnetic forces. As such the innovation can provide a wide range of damping forces, a linear damping function and/or an extended dynamic range of attenuation, providing broad flexibility in configuration size and functional applicability.
NASA-built prototypes have been shown to be highly effective on a 170-foot long wind turbine blade in test beds at the University of Maine.
Mechanical and Fluid Systems
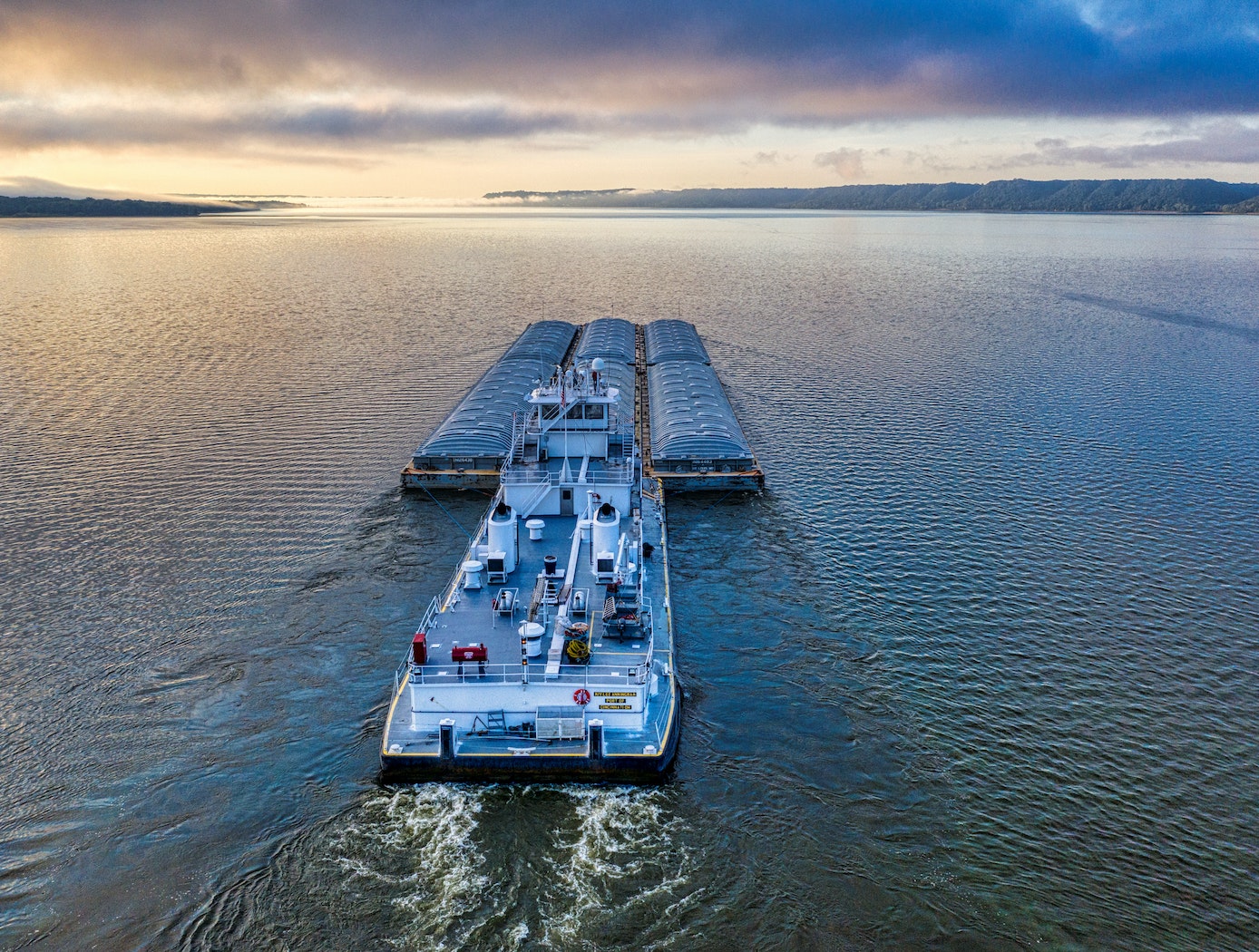
Ocean Platform Motion Control
The NASA innovation leverages existing ballast fluid of a maritime structure to proactively mitigate undesirable resonant response characteristics of the platform or vessel. Essentially, this innovation couples water ballast as a functional working mass to the dynamic motion of a floating structure in order to provide passive motion management of the primary structure.
The system can be implemented pre-design or post manufacture. The systems are simple and are easily manufactured, transported, and implemented onto a primary structure.
The NASA technology has been designed (patents applied for) for a range of platform designs and can be further customized depending on the final application requirements. Prototypes have been built and tested in a wind-wave tank test bed at the University of Maine.
mechanical and fluid systems
.jpg)
Fluid-Filled Frequency-Tunable Mass Damper
NASA MSFC’s Fluid-Filled Frequency-Tunable Mass Damper (FTMD) technology implements a fluid-based mitigation system where the working mass is all or a portion of the fluid mass that is contained within the geometric configuration of either a channel, pipe, tube, duct and/or similar type structure. A compressible mechanism attached at one end of the geometric configuration structure enables minor adjustments that can produce large effects on the frequency and/or response attributes of the mitigation system.
Existing fluid-based technologies like Tuned Liquid Dampers (TLD) and Tuned Liquid Column Dampers (TLCD) rely upon the geometry of a container to establish mitigation frequency and internal fluid loss mechanisms to set the fundamental mitigation attributes. The FTMD offers an innovative replacement since the frequency of mitigation and mitigation attributes are established by the compressible mechanism at the end of the container. This allows for simple alterations of the compressible mechanism to make frequency adjustments with relative ease and quickness.
FTMDs were recently successfully installed on a building in Brooklyn, NYC as a replacement for a metallic TMD, and on a semi-submersible marine-based wind turbine in Maine.
The FTMD technology is available for non-exclusive licensing and partially-exclusive licensing (outside of building construction over 300 feet).
mechanical and fluid systems
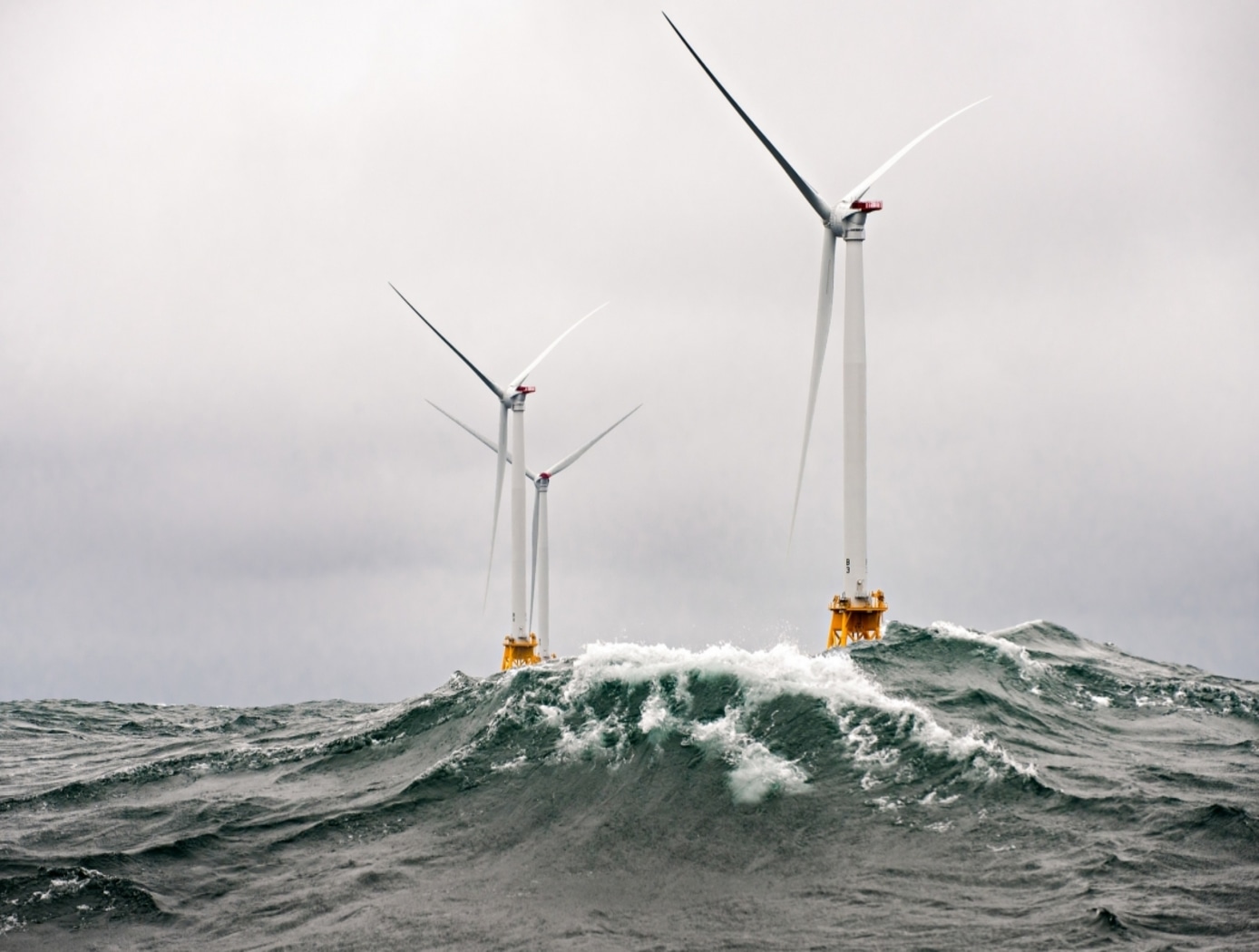
Tension Element Damping (TED) With Hydraulics for Large Displacements
The Rotational Tension Element Damper (RTED) uses a controlled tension line, backed by hydraulics, to damp large displacements in large structures. NASA built RTED prototypes that have been successfully tested on a 170-foot long wind turbine blade in test beds at the University of Maine. In this case, the RTED device damps the vibration of the large, tall turbine blades relative to a stationary anchor structure on the ground using a line and spring coupled to both the blade and the anchor, and controlled by a spool fitted with a one-way clutch. When force is applied, from heavy wind for example, the resulting movement of the tall structure triggers the necessary tension and compression cycles in the system to engage the rotating damper. The reaction force interferes with the rotation speed of the spool and disrupts and damps the vibration in the tall structure. The figure below shows test data for the RTED used on the wind turbine.