Search
Robotics Automation and Control

Method for discrete assembly of Cuboctahedron Lattice Materials
The novel technology is a method for the design, manufacture, and assembly of modular lattice structure based mechanical metamaterials composed of cuboctahedron unit cells. The main parameters for determining the behavior of an architected lattice material are 1. Lattice geometry: base unit cell topology defines joint connectivity and informs general lattice behavior (e.g. bending or stretch dominated), which can then be used for performance prediction relative to constituent material and density. Cell size (edge length) and edge thickness (cross section) can be used to calculate relative density; 2. Base constituent material: solid properties (mechanical, thermal, electrical, etc.) are used to calculate effective properties of resulting lattice, as well as to inform manufacturing processes.
The invention relates particularly to a cuboctahedral lattice geometry, which can be decomposed into face connected cuboctahedrons. The material used is determined by the manufacturing process, such as injection molding. This offers a range of high-performance options such as glass fiber and carbon fiber reinforced polymer (GFRP, CFRP) composites. The size of the lattice can vary based on the application. Molded individual faces (bottom left figure) are then assembled into the cuboctahedron voxel building block (bottom right figure). This assembly can be achieved with a number of methods, including permanent methods such as welding or gluing, or reversible methods such as bolting or riveting.
manufacturing
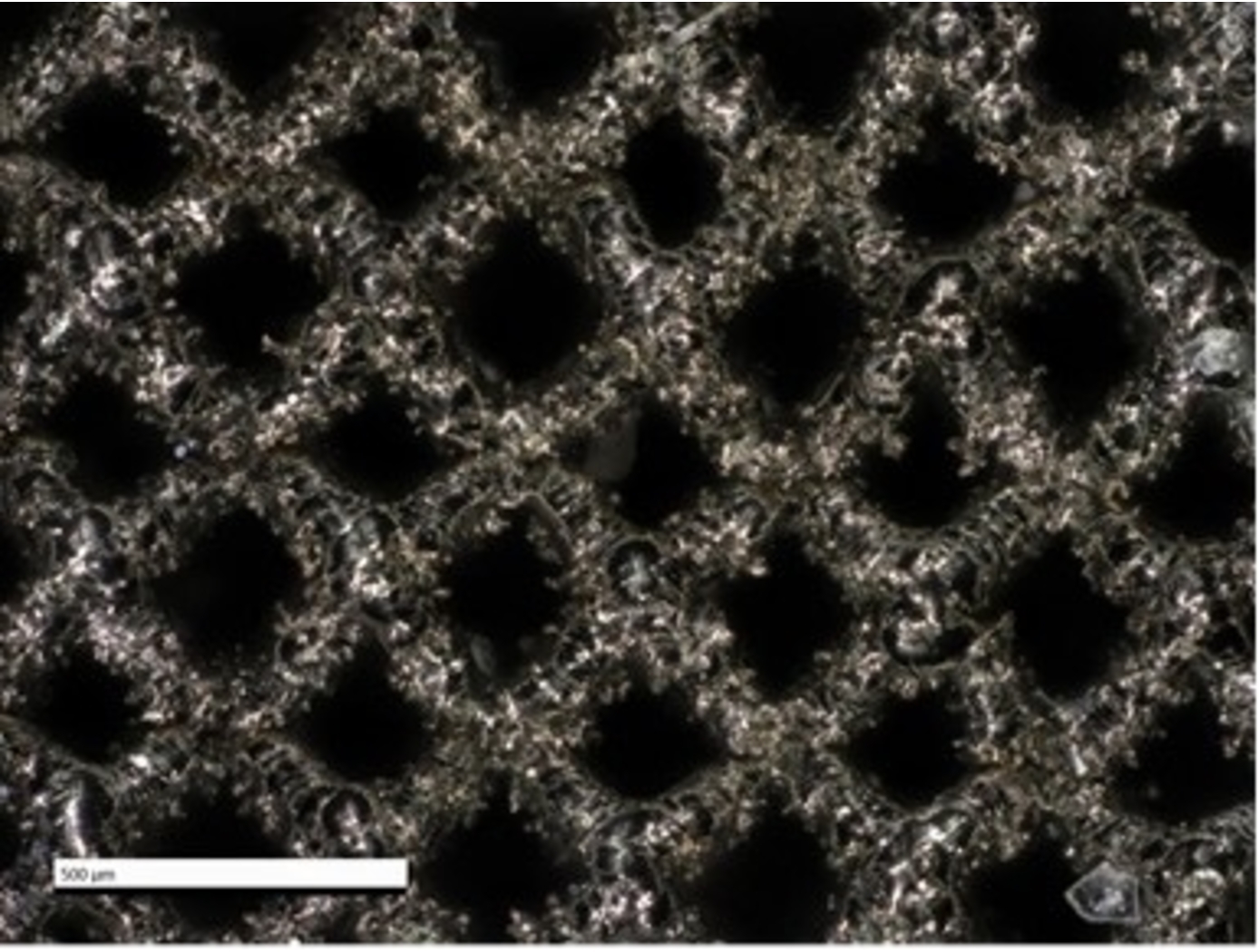
Additively Manufactured Propulsion Catalysts
Working with EOS, a market leader in additive manufacturing (AM) technology, NASA has pioneered the use of AM to achieve improved performance and cost reduction of propulsion catalyst systems. As mentioned above, conventional mono-propulsion catalysts are comprised of ceramic or graphite foams, which possess thousands of irregular pores with non-uniform size and distribution. Due to the lack of granular control in the manufacturing process, such foams are limited in terms of feasible designs. These foams also exhibit anisotropic mechanical properties and inconsistent fluid flow behavior. Furthermore, such catalysts are produced by a limited number of vendors, constraining availability and inflating cost. As with several other aerospace structures, AM of mono-propulsion catalysts enables increased manufacturing capabilities (e.g., granular geometric control, repeatability) while reducing cost and lead time.
NASA and EOS leveraged AM to generate ultra-fine lattice structures repeating unit cells with ligament thickness as small as 100 microns to replace coated ceramic or graphite foam catalysts. These AM lattice structures offer several advantages including increased control of structure topology, unconstrained designed flexibility, improved compressive strength, and fluid flow optimization all printed into a single component from a preferred refractory platinum metal. Granular control of structure topology allows for tailored percent relative density (%RD), which in turn allows manufacturers to control the mechanical and fluid flow properties of the final catalyst structure. In other words, NASAs AM ultra-fine lattice catalyst structures significantly improve upon the drawbacks of conventional catalysts by offering a higher degree of control over the structure, enabling the generation of catalysts with customized material properties. In addition, the use of AM ensures the catalysts exhibit high spatial symmetry and can be generated in a repeatable (non-stochastic) manner, all while reducing cost and lead times.
While NASA and EOS' ultra-fine lattice structures were originally developed for mono-propellant systems (e.g., green propellant thruster catalysts), the same structures and manufacturing technologies can be applied to liquid or gas permeable rigid materials, evaporative film cooling heat exchangers, filtering, and other applications.
Robotics Automation and Control
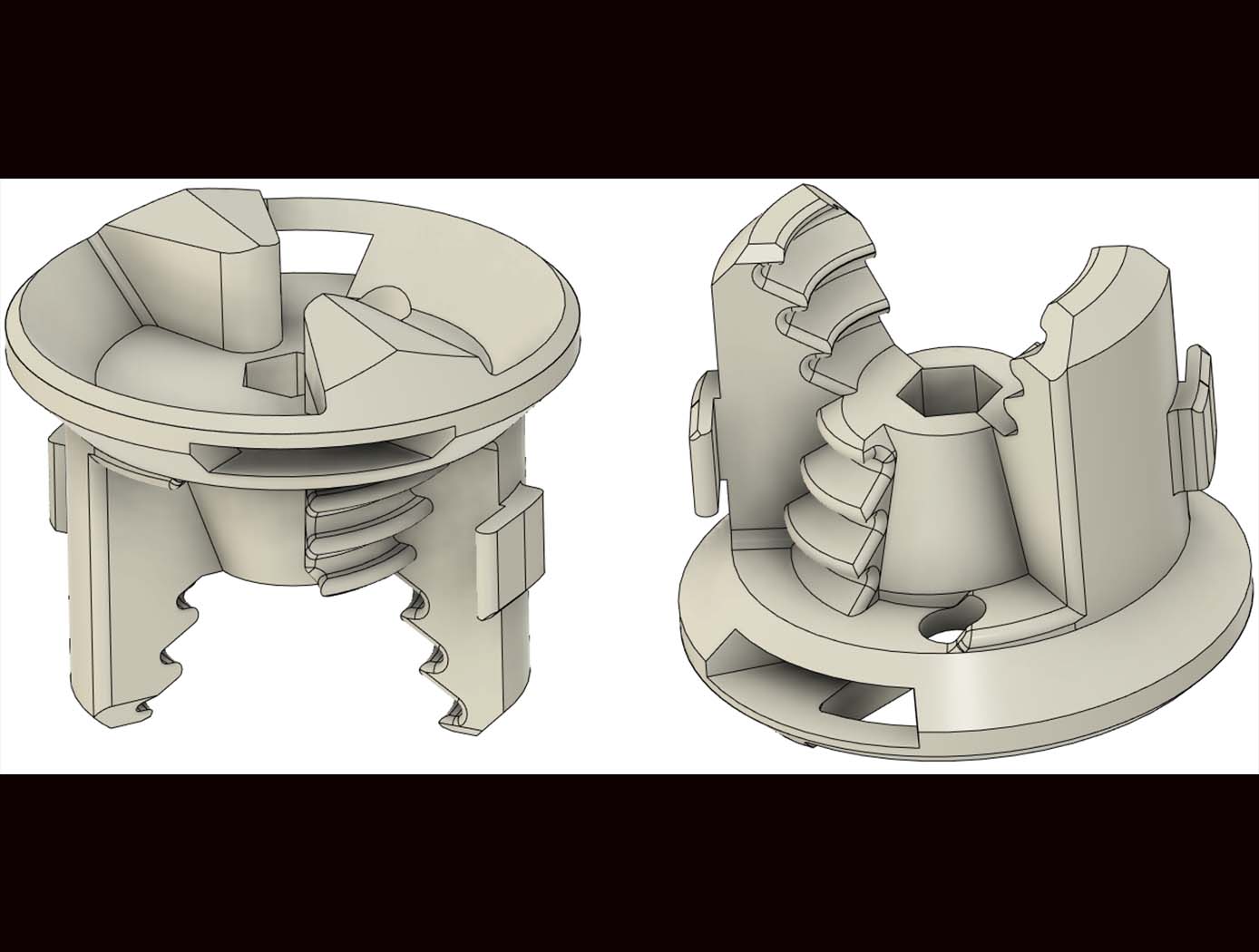
Reversible Androgynous Mechanical Fastener
The androgynous fastener is lightweight and facilitates assembly through simple actuation with large driver-positioning tolerance requirements. This fastener provides a high-strength, reversible mechanical connection and may be used in high strength-to-weight ratio structural systems, such as lattice structure systems. The androgynous fastener resists tensile and shear forces upon loading of the lattice structure system thereby ensuring that the struts of the lattice structure system govern the mechanical behavior of the system. The androgynous fastener eliminates building-block orientation requirements and allows assembly in all orthogonal build directions. This androgynous fastener may be captive in building-block structural elements thereby minimizing the logistical complexity of transporting additional fasteners. Integration of a plurality of the androgynous fasteners into a high performance, robotically managed, structural system reduces launch energy requirements, enables higher mission adaptivity and decreases system life-cycle costs. The androgynous fastener is beneficial in any application where robotic end effectors are used to join structural components (or other parts) together. It may be particularly desirable for applications requiring frequent movement of hardware to an assembly site to replace joint connections.