Search
materials and coatings
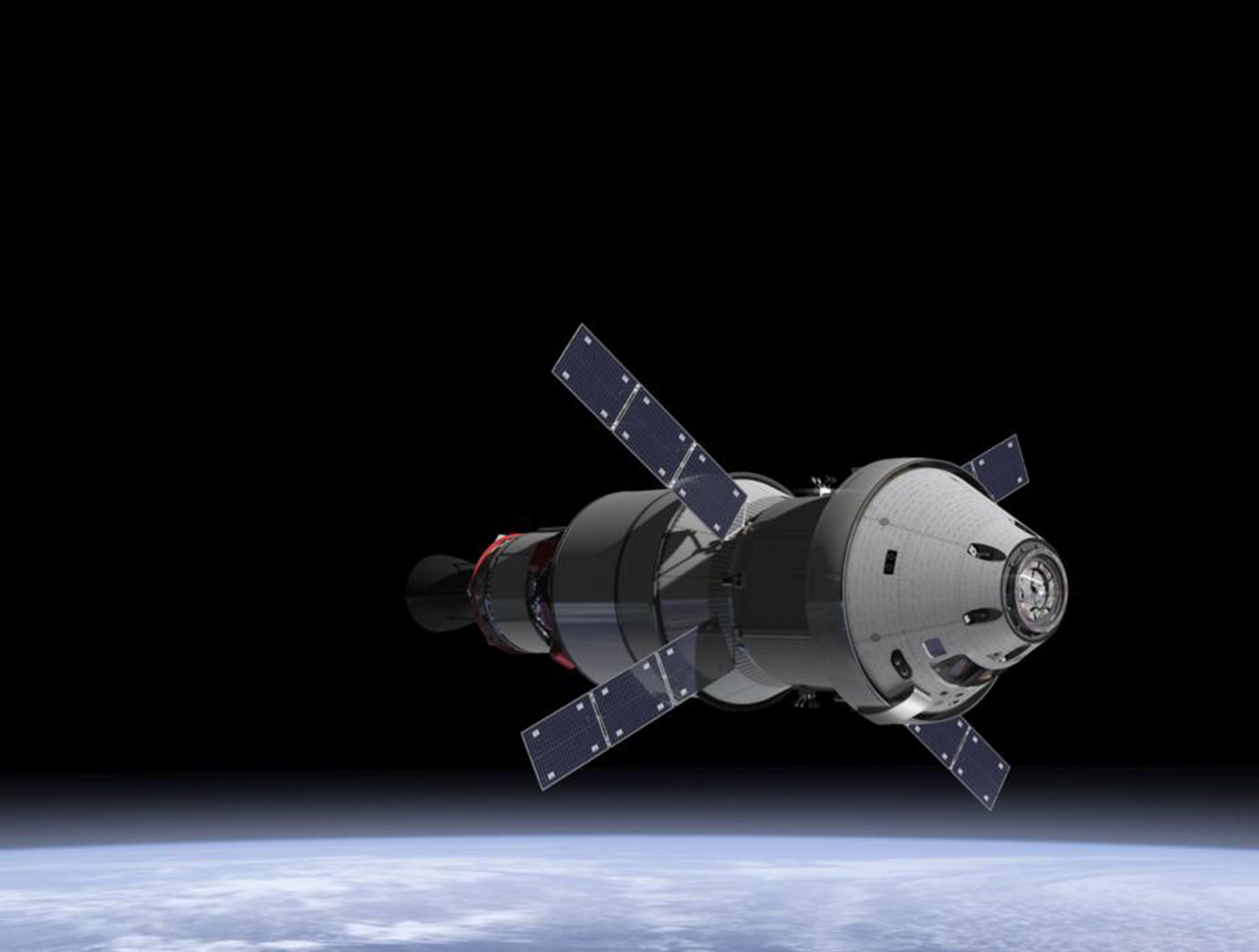
Advanced Protective Coatings for Graphite-Based Nuclear Propulsion Fuel Elements
To protect the graphite (Gr)-based substrates in a nuclear systems fuel elements from hot hydrogen attacks, earlier researchers developed a method to deposit (via chemical vapor deposition) a protective niobium carbide (NbC) or zirconium carbide (ZrC) coating in the inner cooling channels of the fuel elements through which the hydrogen propellant flows. Unfortunately, the significant difference in the coefficients of thermal expansion (CTE) between the Gr-based substrate and the ZrC coating leads to debonding at intermediate temperatures, thereby exposing the substrate to hot hydrogen attack despite the NbC or ZrC coating. Innovators at Glenn have proposed a solution to this problem by introducing additional layers of compliant metallic coatings to accommodate the differences in CTE between the ZrC and the Gr-substrate,thereby potentially increasing life and durability. In this configuration,the innermost layer is composed of molybdenum carbide (Mo<sub>2</sub>C), and additional outer layers are made of molybdenum (Mo) and niobium (Nb) layers. The MoC acts as a diffusion barrier to minimize the diffusion of carbon into the refractory metal layers and the diffusion of Mo or Nb into the Gr-based substrate. The Mo layer is deposited on top of the Mo<sub>2</sub>C layer. A Nb layer is deposited on the Mo layer with the ZrC forming the outside layer of the coating. A thin Mo layer on the ZrC helps to seal the cracks on the ZrC and acts a diffusion barrier to hydrogen diffusion into the coating.The Mo and Nb layers are compliant so that differences in the thermal expansion of ZrC and other layers can be accommodated without significant debonding or cracking. They also act as additional diffusion barriers to hydrogen diffusion towards the Gr-substrate. Overall, Glenn's pioneering use of layered coatings for these components will potentially increase the durability and performance of nuclear propulsion rockets.
sensors
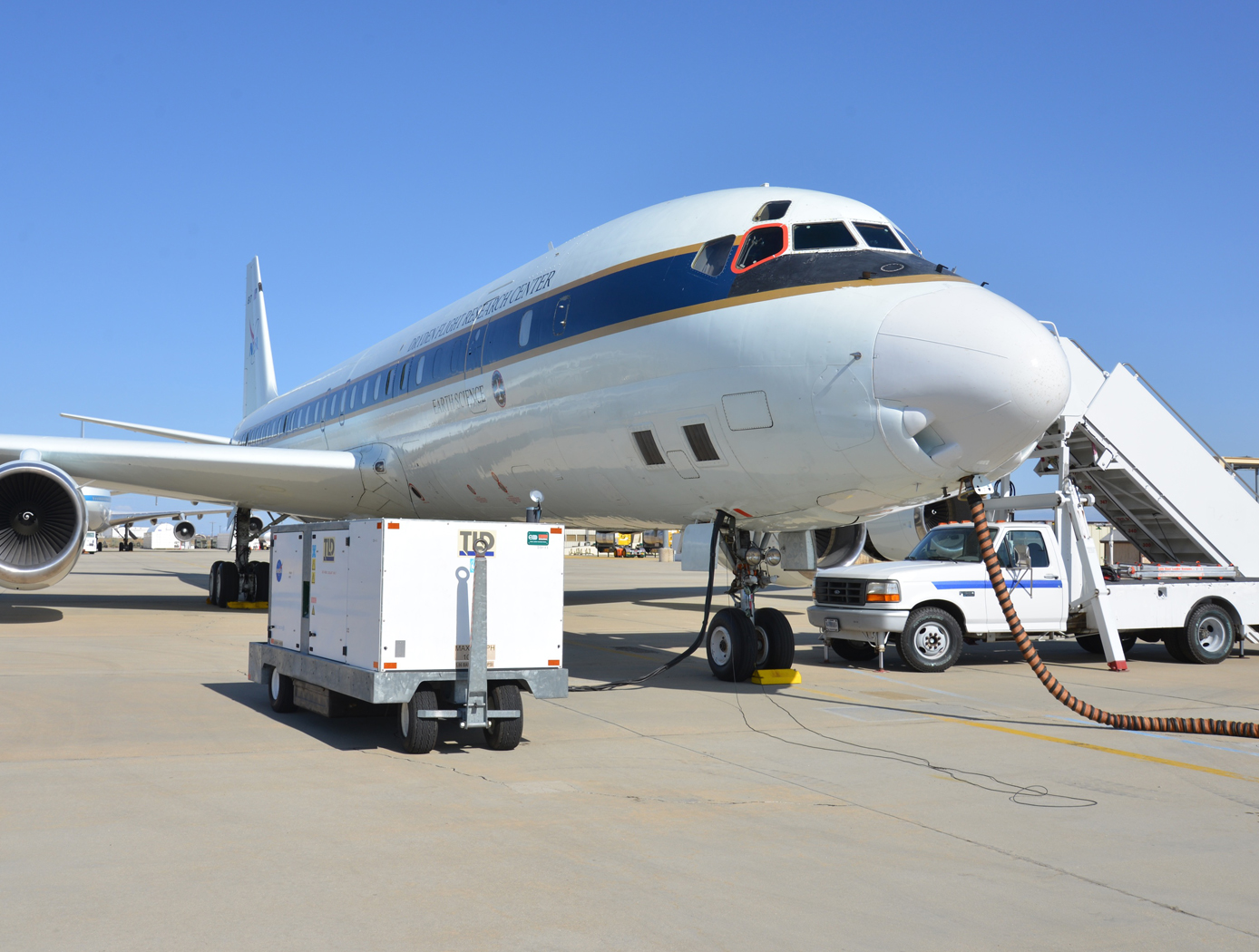
Highly Accurate Level Sensor
The FAA and Aircraft Industry recognize the need to reduce fuel tank explosion risk
by eliminating ignition sources and changing fuel tank design and maintenance.
This technology can be utilized to wirelessly sense the level of fuel in aircrafts, thus
mitigating risk of inadvertent electrical failures and sparks. NO wires enter the fuel
tank and the radio frequency transponder typically requires 10 milliwatts of power or
less.
The technology can be used for dielectric tanks, by simply applying the sensors to the
tank surface (as pictured). Through certain techniques the technology can be applied
on metal tanks with no wires entering the tank from the outside.
Currently, there are more than 20,910 jet aircraft in service. This presents a large
market opportunity for retrofitting this technology onto existing airplane fuel tanks
Rapidly evolving aviation services are expected to spur worldwide requirement for
36,770 new jet aircraft by 2033. This presents a growing market for new installations.
Power Generation and Storage
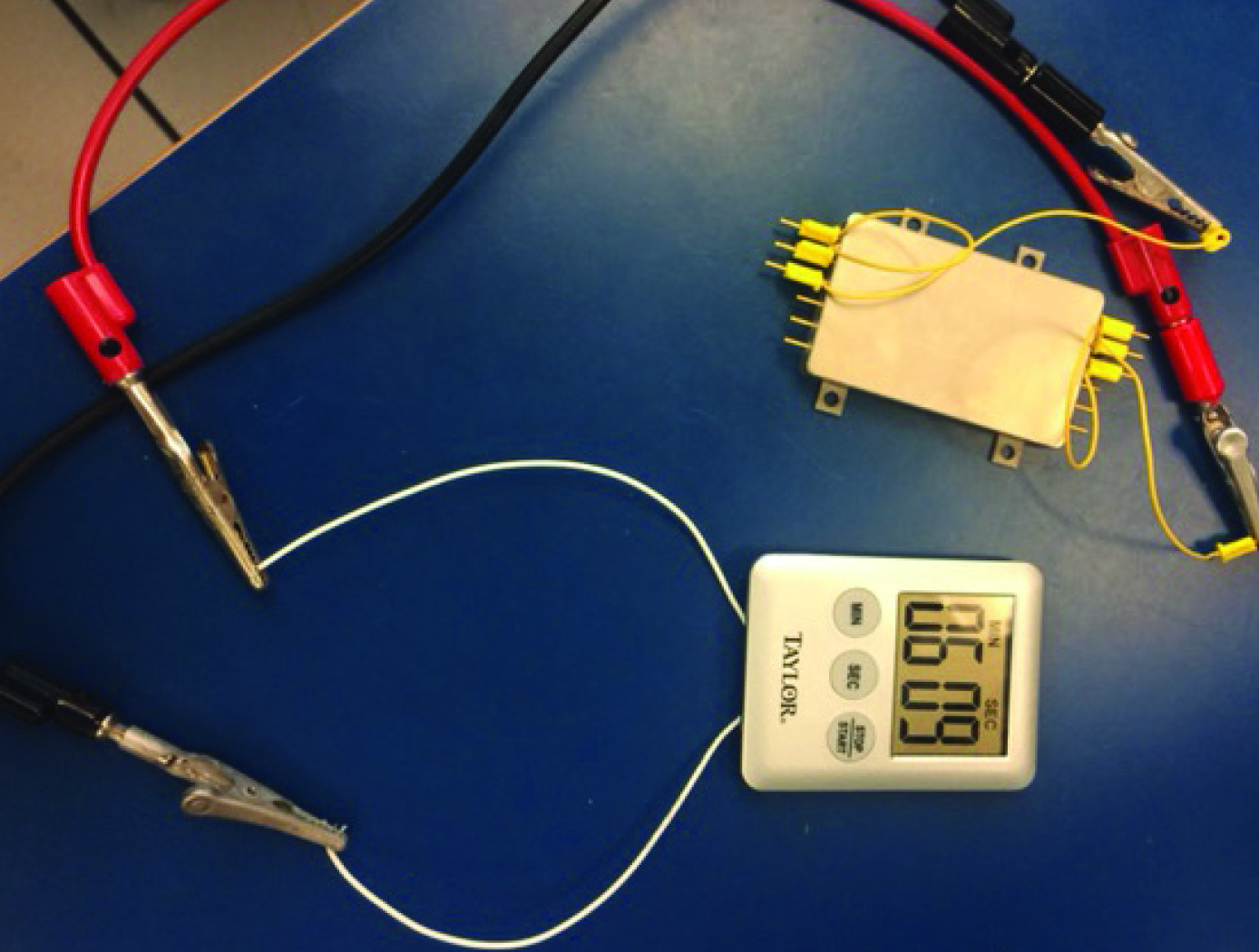
Novel, Solid-State Hybrid Ultracapacitor Battery
The subject technology is an extension of closely related, solid-state ultracapacitor innovations by the same team of inventors. The primary distinction for this specific technology is the addition of co-dopants to affect the dielectric behavior of the barium titanatebased perovskite materials. These co-dopants include lanthanum and other rare earths as well as hydroxyl ions. The materials are processed at the nano scale, and are subjected to carefully designed thermal treatments as well.
The presence of the hydroxyl ions has been shown to provide several orders of magnitude increase in the capacitance of the dielectric material. Additionally, these high capacitance values are obtained at relatively low voltages found in current consumer and industrial electronics.
The capacitors tested to date are simple, single-layer devices. Ultimately, a range of manufacturing methods are possible for making commercial devices. Features of the technology enable manufacturing via traditional thick-film processing methods widely used in the capacitor industry, or via advanced printing methods for state-of-the-art printed electronics.
Future efforts will be made to advance the manufacturing and packaging processes to increase device energy density, including multilayer devices and packages
sensors
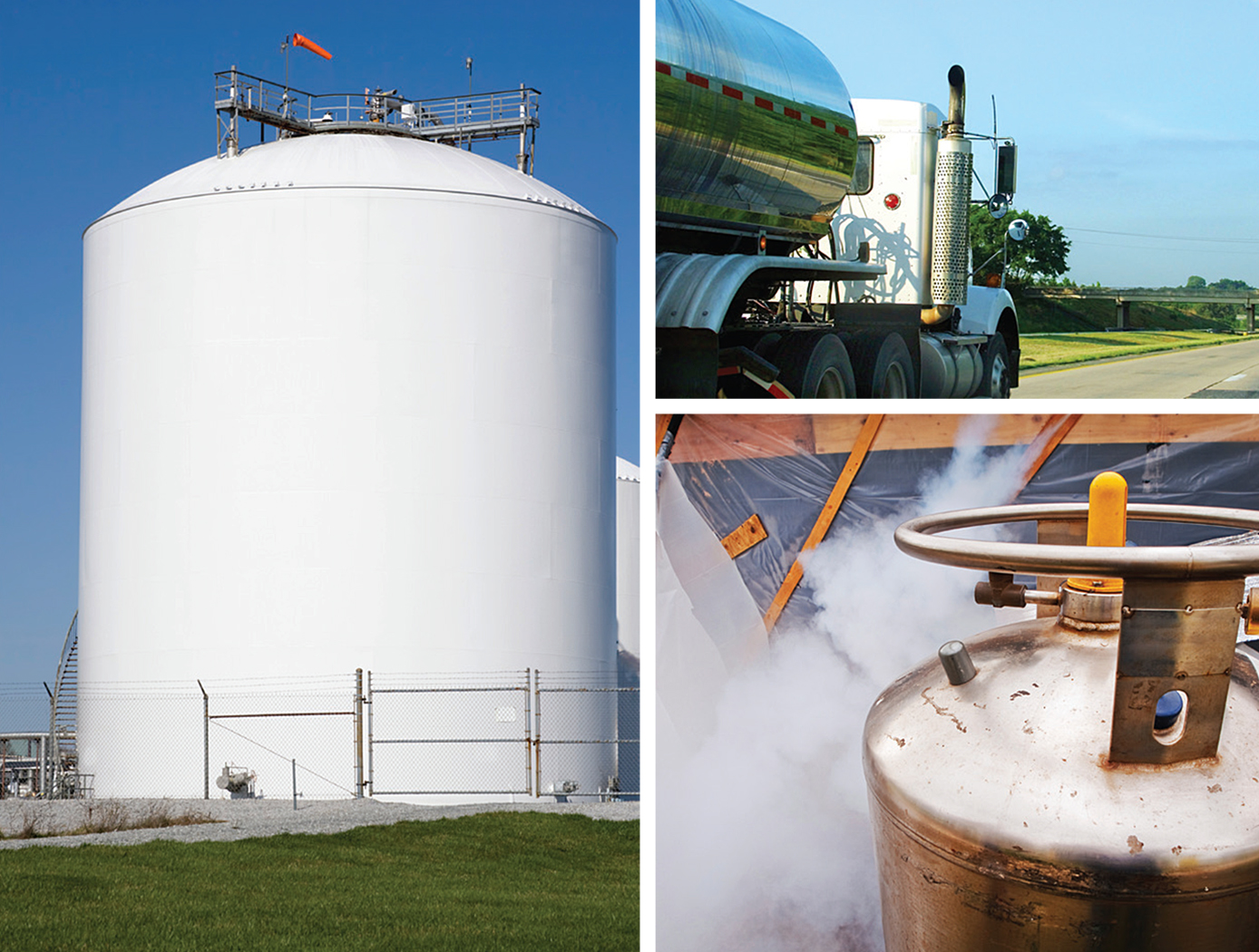
Streamlined Liquid Level Sensing Using Fiber Optics
Armstrong has developed a robust fiber optic–based sensing technology that offers extraordinary accuracy in liquid level measurements. The sensing system uses fiber optic Bragg sensors located along a single fiber optic cable. These sensors actively discern between the liquid and gas states along a continuous fiber and can accurately pinpoint the liquid level.
<strong><i>How It Works</strong></i>
The technology uses a resistive heater wire bundled with the optical fiber. The heater is pulsed to induce a local temperature change along the fiber, and the fiber Bragg grating data is used to monitor the subsequent cooling of the fiber. The length of fiber in the liquid cools more rapidly than the portion of the fiber in the gas above the liquid. The measurement system accurately establishes the location of this transition to within 1/4-inch.
<strong><i>Why It Is Better</strong></i>
Armstrong's liquid level sensing technology was originally developed to measure cryogenic liquid levels in rockets, and it represents a significant advancement in the state of the art in this application. Conventional methods for measuring cryogenic liquid levels rely on cryogenic diodes strategically placed along a rod or rack. The diodes are mounted in pre-selected, relatively widely spaced positions along the length of a rod; this configuration provides limited, imprecise data. Furthermore, each diode on the rod has two wires associated with it, which means a single system may require a large number of wires, making installation, connectivity, and instrumentation cumbersome.
Armstrong's novel technology provides liquid measurements with much greater precision, achieving measurements at 1/4-inch intervals. Furthermore, the streamlined system uses just two wires, which greatly simplifies installation and instrumentation. Due to its extraordinary accuracy and ease of use, Armstrong's measurement system offers important advantages for a wide range of applications beyond cryogenic liquids.
<strong><i>In Addition</strong></i>
Researchers have developed a new manufacturing process that improves the ability of fiber optic sensing systems to measure temperature and liquid levels when operating in humid environments. The process involves eliminating moisture from the optical fiber coating, then completing the sensor assembly within humidity-controlled conditions. The resulting sensor hardware provides precise and accurate measurements even when operating in a humid environment.
<b><i>For more information about the full portfolio of FOSS technologies, see DRC-TOPS-37 or visit <a href=https://technology-afrc.ndc.nasa.gov/featurestory/fiber-optic-sensing>https://technology-afrc.ndc.nasa.gov/featurestory/fiber-optic-sensing</a></b></i>