Search
Instrumentation

Dual-Polarized, Wideband, Lightweight P-band Antenna Element and Array
The P-band antenna array is built from rows and columns of antenna elements for the purpose of allowing beam steering up to the maximum desirable angle without incurring grating lobes in the radiation patterns. For flexible mission planning, a large array can be built from several of the small, panel-like elements. The elements are deployable from a folded or stacked stowed configuration during launch, arranged side by side during operation. Each antenna element is itself a fully functional small antenna array. The number of panels can be chosen as dictated by the mission objectives and budget.
Three geometries were designed and tested. Geometry 1 features non-planar metal structures with minimal dielectric support, where the back cavity is closed. Geometry 2 features non-planar metal structures with minimal composite sheet dielectric support, but with an open cavity. Both geometries avoid large flat sheets, which are vulnerable to bending, thereby increasing the mechanical stiffness of the structure while using only thin sheet metal and maintaining an exceptionally low mass-to-size ratio. Geometry 3 features planar metal structures, with sandwich composite dielectric support and an open cavity. While it does not benefit from the mechanical stiffness utilized in non-planar designs, the planar sandwich structure increase robustness and reduces the cost of fabrication. All element geometries have wideband capabilities and are dual polarized.
Although designed for space and planetary exploration, the P-band antenna is also valuable for various terrestrial use cases. The P-band antenna array is at technology readiness level (TRL) 5 (component and/or breadboard validation in relevant environment) and is available for patent licensing.
Robotics Automation and Control
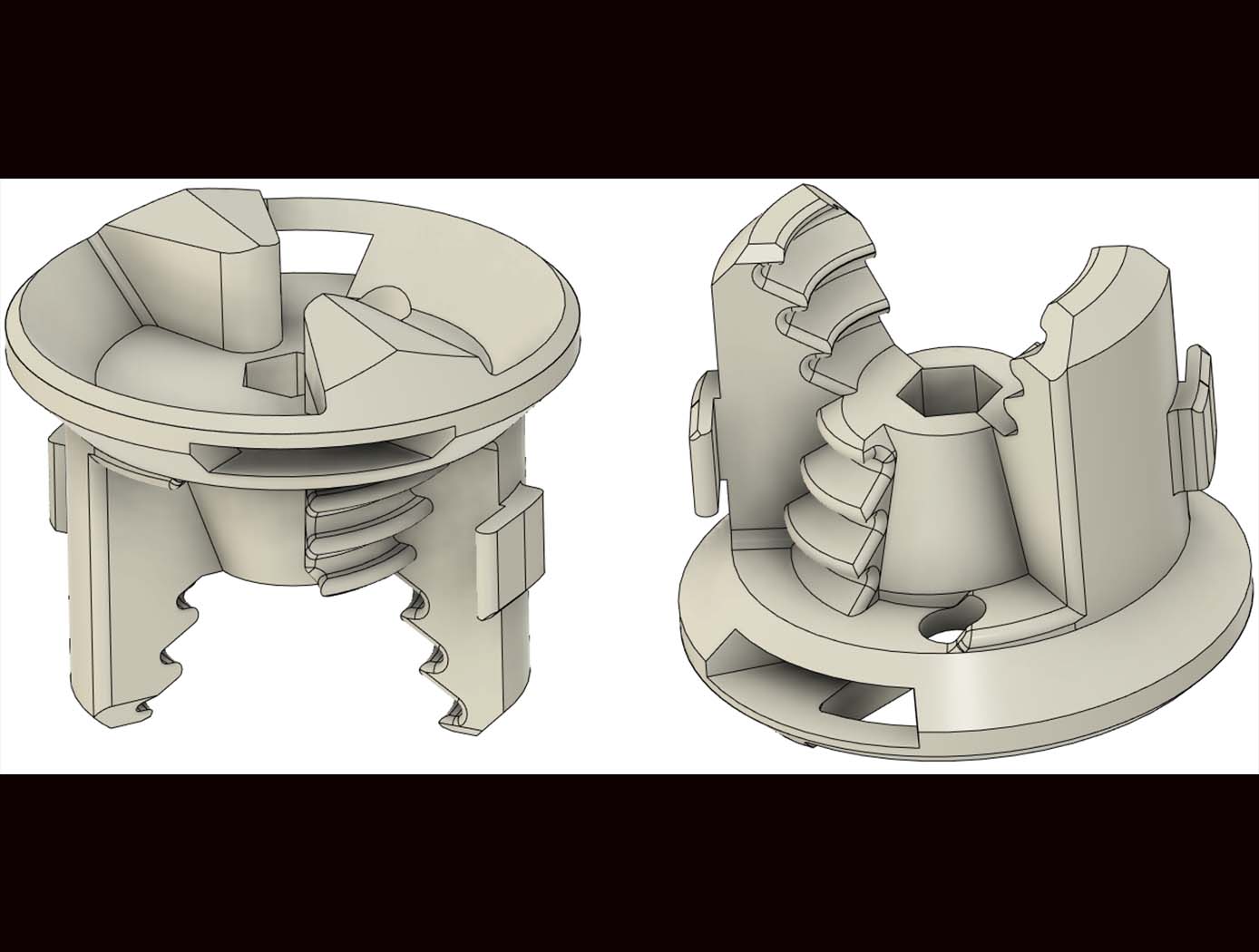
Reversible Androgynous Mechanical Fastener
The androgynous fastener is lightweight and facilitates assembly through simple actuation with large driver-positioning tolerance requirements. This fastener provides a high-strength, reversible mechanical connection and may be used in high strength-to-weight ratio structural systems, such as lattice structure systems. The androgynous fastener resists tensile and shear forces upon loading of the lattice structure system thereby ensuring that the struts of the lattice structure system govern the mechanical behavior of the system. The androgynous fastener eliminates building-block orientation requirements and allows assembly in all orthogonal build directions. This androgynous fastener may be captive in building-block structural elements thereby minimizing the logistical complexity of transporting additional fasteners. Integration of a plurality of the androgynous fasteners into a high performance, robotically managed, structural system reduces launch energy requirements, enables higher mission adaptivity and decreases system life-cycle costs. The androgynous fastener is beneficial in any application where robotic end effectors are used to join structural components (or other parts) together. It may be particularly desirable for applications requiring frequent movement of hardware to an assembly site to replace joint connections.
Robotics Automation and Control
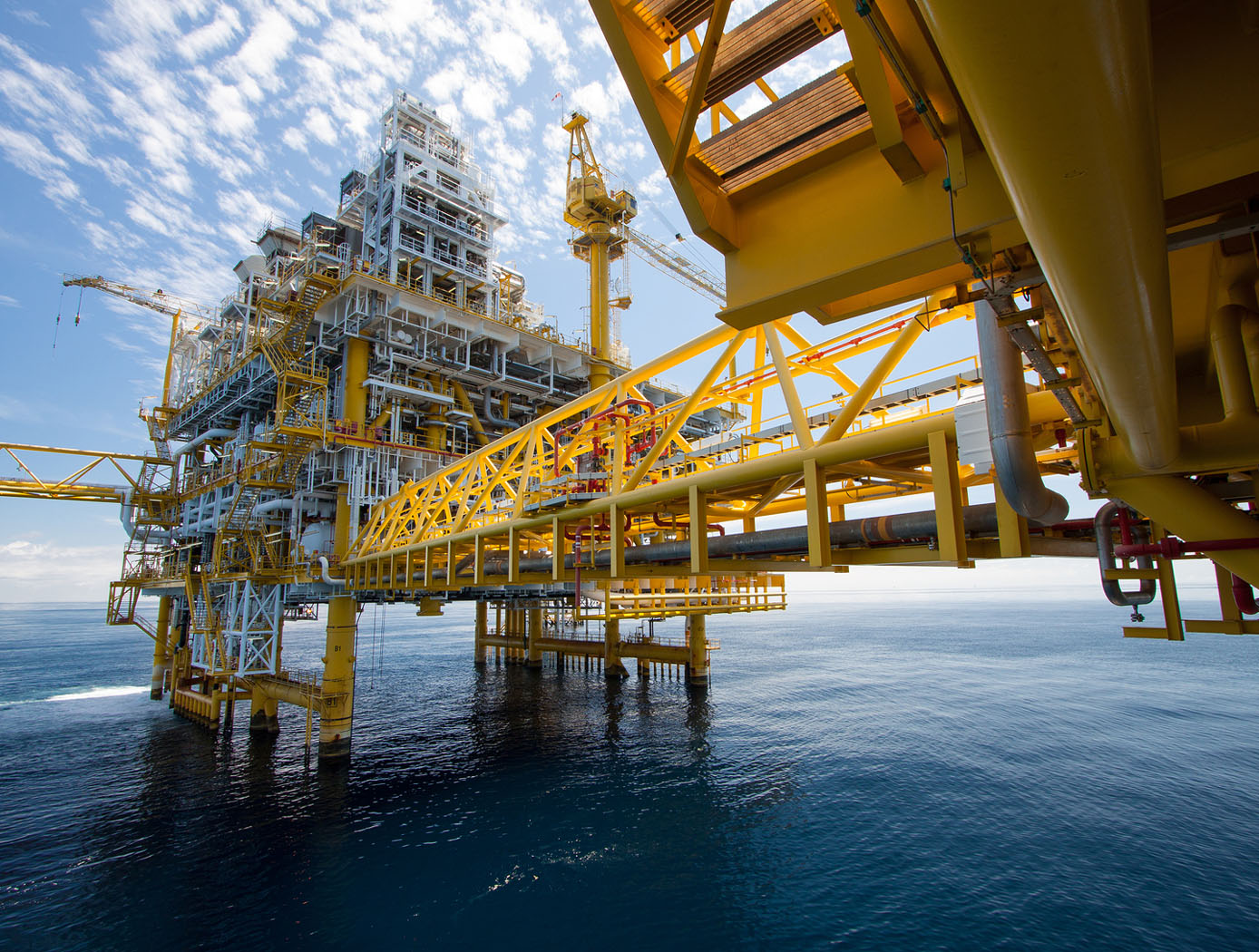
Robotic System for Infra-structure Reconnaissance
The robotic system is comprised of six main components: the orb that performs the reconnaissance, an orb injector housing that attaches to a piping network, a tether and reel subsystem that attaches to the back of the injector housing, a fluid injection subsystem that attaches toward the front of the injector housing, an external power and data subsystem, and associated control and monitoring software.
Usage of the system begins with an operator attaching the injector housing, with the orb stowed inside, to a flanged gate valve belonging to the piping network of concern. Requisite power, data, and fluid subsystems are attached, and the system is energized for usage. The orb is released via the tether and reel, and a controlled fluid force is imparted on the orb to help guide it along its mission. The tether supplies power and guidance to the orb, and relays real-time data back to the operator.
The orb’s interior features a modular plug-and-play architecture which may comprise COTS instrumentation for reconnaissance or investiga-tion, LIDAR, and inertial measuring and motion sensors. This instru-mentation could be used in combination with other sub-systems such as lighting, and core and sample retrieving mechanisms. These com-ponents are supported by other onboard devices such as a CPU, power source and controller, and data transmission encoders and multiplexers.
The Robotic System for Infrastructure Reconnaissance is at TRL 8 (actual system completed and "flight qualified" through test and demonstration), and is now available for licensing. Please note that NASA does not manufacture products itself for commercial sale.
manufacturing

Modular Artificial-Gravity Orbital Refinery Spacecraft
Modular Artificial-Gravity Orbital Refinery Spacecraft is a solution for refining in-situ materials collected in space, such as from asteroids and Mars moons, as well as recycling spacecraft debris, while orbiting in micro-gravity conditions. The spacecraft is coupled with refining modules for refining and recycling different types of materials. It generates artificial gravity for operation in low-gravity environments. The spacecraft is comprised of rotating rings, each generating artificial gravity and angular momentum. When the rotating rings are combined on the spacecraft platform, however, they have a net near-zero angular momentum such that the spacecraft can change its attitude with minimal propellant or rotate at the rate of the object the spacecraft platform is attached to. The spacecraft platform can self-balance to accommodate different sized modules and modules with moving loads. The refined and recycled materials can be used to create products in-situ as well as products too large to launch from Earth, such as construction of orbiting space habitats, large spacecraft, solar-power stations, and observatories.