NASA’s Integral Tuned Mass Absorber for Turbine Blades Webinar
NASAs Marshall Space Flight Center has developed a novel turbine blade design and manufacturing approach that provides a significant reduction in turbine blade resonant vibration. In particular this innovation addresses the unique resonance vibration challenges of conventionally machined turbine bladed-discs, or blisks. The design approach includes an internal blade tuned mass absorber structure that can be placed at optimal location where deflection is greatest. Additive manufacturing is used to make this unique structure. Prototypes have demonstrated a 50% reduction in resonant vibration. Importantly, the innovation also enables improved predictive modelling of the resonant behavior of new blisk designs because the tuned-mass absorber acts as a linear system. In contrast, modelling of conventional blade dampers is extremely complex and therefore requires an expensive iterative test program dedicated to validation of the damper design.
To learn more about this technology, please click here.
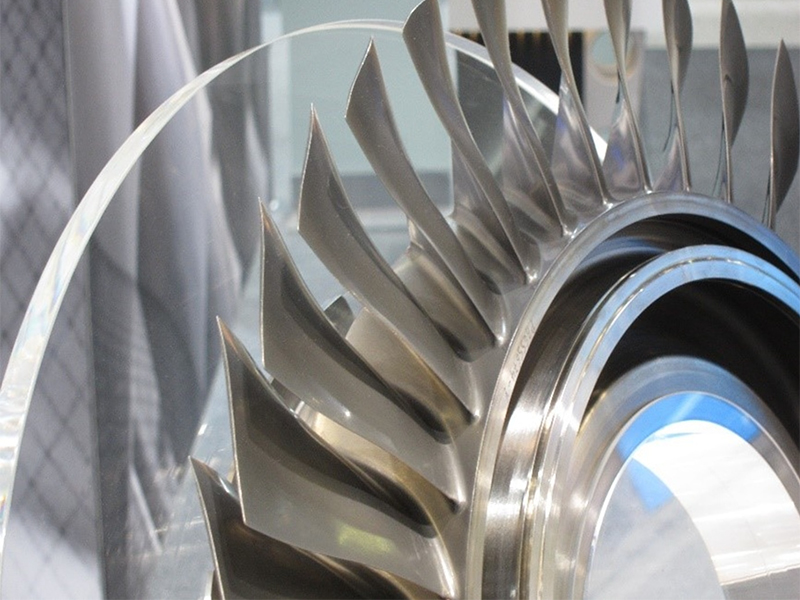
Andy Brown is an Aerospace Engineer in the NASA-MSFC/Propulsion Structures & Dynamic Analysis Branch. He joined MSFC in 1986, and has worked mainly on rocket engine dynamics and loads research, development, and production.He has authored or co-authored 11 journal papers and 32 conference papers and reports covering topics ranging from probabilistic design and loads combination methods to techniques for calculating turbine blade forced response in the presence of asymmetric flow. Andy received a BS in Mechanical Engineering from Duke University and a Masters and Ph.D. in ME from Georgia Tech, and is an Associate Fellow of the American Institute of Astronautics and Aeronautics. He is currently writing a book to be published by Springer entitled “Structural Dynamics of Liquid Rocket Engines” along with developing the turbine blade technology to be discussed today.