Axial Magnetic Flux Airflow Integrated Compressor-Generator-Motor Turbojet
propulsion
Axial Magnetic Flux Airflow Integrated Compressor-Generator-Motor Turbojet (DRC-TOPS-39)
Lowering weight and volume of turbo-machinery for aircraft applications
Overview
Innovators at NASA's Armstrong Flight Research Center have developed a compressor-generator-motor turbojet design that integrates the generator into the aerodynamic blade structures of the compression section of turbo-machinery. This lowers both weight and volume compared with conventional turbine generator arrangements in which the turbojet or turbofan drives a separate shaft-driven generator. All manner of other conventional designs suffer from system inefficiencies. Conventional side-mounted generators require the weight of a 90-degree gearbox, while a rear-mounted generator suffers from cooling problems. Armstrong's design offers improvements over these configurations with a flight-weight electromagnetic turbo-generator that is suitable for application to distributed turboelectric systems on aircraft and aids in cooling the system. The unique technology may enable new aircraft configurations and future Turboelectric Distributed Propulsion (TeDP) aircraft designs.
The Technology
The innovation uses the rotating blades of the compressor section to act as structural support for the generator. Since the compressor is the coolest part of the engine, it will reduce the potential for interference with magnetics and associated curie points of the permanent magnets. The placement of the generator in the cooler part of the engine flowpath (fan or compressor) will also improve the electrical insulation system's degradation and serve to improve overall system lifetime.
The configuration proposed by Armstrong's design would be an axial magnetic flux permanent magnet generator or motor. The electrical/mechanical interface could serve to deliver power to the shaft of the turbojet/fan or extract power from the shaft.
This axial electromagnetic flux design is more efficient for the combined function of aero-thermal heat transfer and generation of electricity. This is due to the relative amount of available cooling surface area, which has an advantage over radial designs given the total system volumetric aspect ratio of the generator/compressor section. When the system is viewed as a thermodynamic cycle, it is more efficient because it is essentially a regenerative cycle, with the heat of generation being fed back into the cycle instead of being released into the ambient surroundings
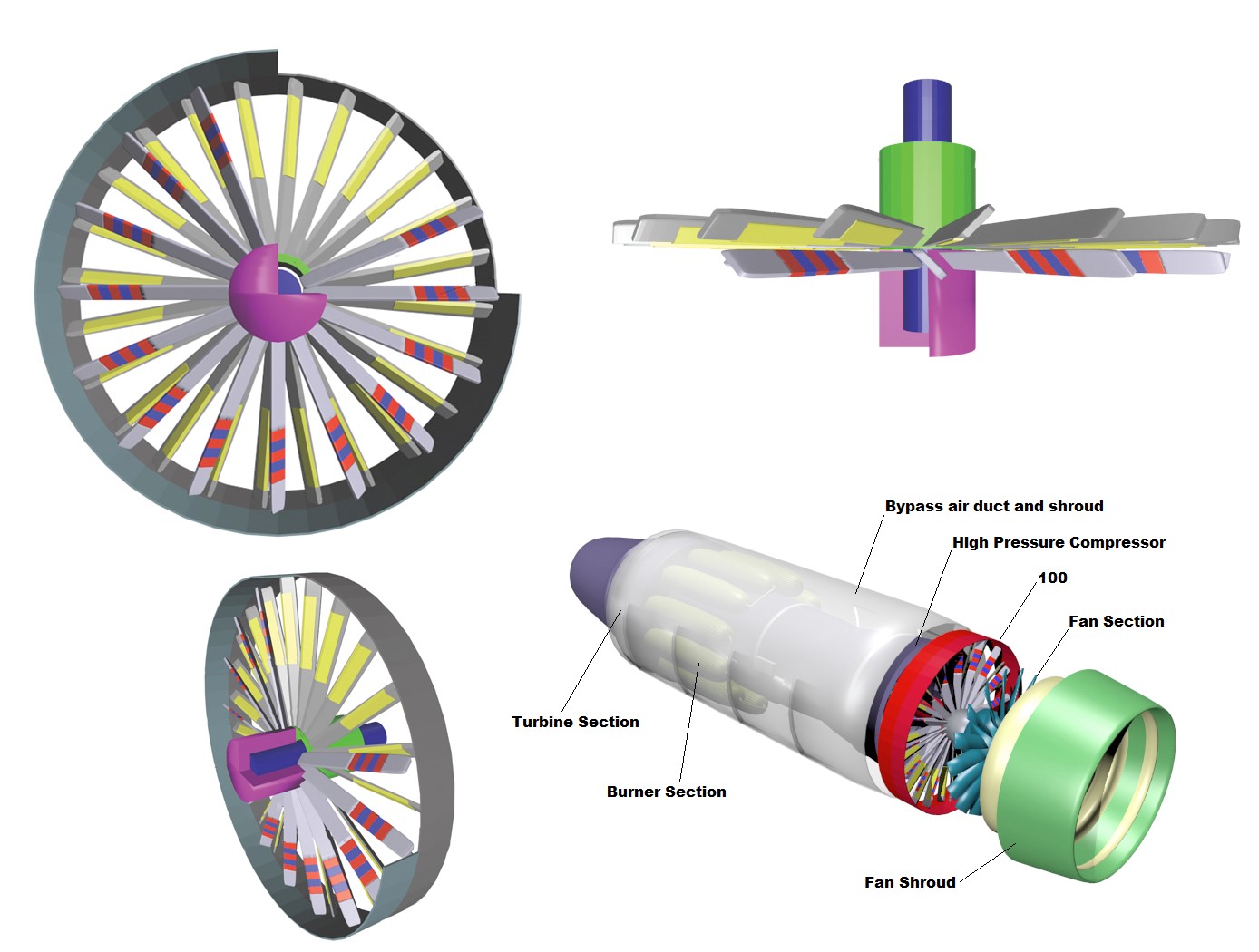
Benefits
- Streamlined: Integrates the generator into the blade structure of turbo-machinery, thereby simplifying the overall system design
- Lower weight: Lowers the weight and volume of the overall system, bypassing the need for a heavy 90-degree gearbox in conventional side-mounted generators
- Cooler: Eliminates the intrinsic cooling problems of rear-mounted generators by enabling the blades of the compressor to cool the electromagnetic machinery
Applications
- Turboelectric Distributed Propulsion (TeDP) aircraft designs
- N+3 vehicle concepts
- Large-class cargo transports
- Commercial and private aircraft
Similar Results

A New Twist Makes Rotating Machinery More Efficient and Quieter
Derived from a design approach for a new wing known as PRANDTL-D, this technology achieves similar improvements for propellers and other rotating machinery.
How It Works
To achieve the innovation's alternate spanload, Armstrong designers applied a non-linear twist to the propeller blade. The twist moves the load inward and dissipates the tip vortex over a wider area, minimizing its effect on drag. It also results in a decrease in load at the tip and reduced torque at the tip. These changes combine to achieve a dramatic reduction in power consumption without compromising the blade's other parameters. Specifically, the blade's diameter and rpm remain unchanged.
What Makes It Better
Unlike the conventional minimum induced loss (elliptical) spanload, which consumes large amounts of power at the tip of the blade, the new design unloads the tip and reduces torque, achieving significant improvements in efficiency. First-order analysis shows a more than 15 percent improvement in power consumption while producing the same thrust. The design also produces significantly less noise than conventional blade designs.

High-Voltage Power System for Hybrid Electric Aircraft Propulsion
Glenn's novel system supports the NASA Aeronautics Research Mission Directorate (ARMD) strategic plan to leverage advancements in technologies over the next 25 years and beyond, leading to new aircraft configurations with enhanced performance, improved energy efficiency, and reduced CO2 emissions. The electric system is a multi-megawatt micro-grid that converts mechanical energy to electric via generators, and electric energy to mechanical via motor-driven fans. This innovation would use the variation in aircraft throttle settings to produce a high-voltage (20 kilovolts), variable-frequency 9-phase AC distribution system. Using doubly fed electric machines (generator, propulsor, and flywheel) allows for field excitation that can cause variable-frequency or variable speed operation around the commanded throttle setting. The flywheel enables an energy storage system that recovers and reuses energy, while the flywheel slews with the throttle control using the electromagnetic torque produced by the doubly fed electric machine. This design permits both sub-synchronous and super-synchronous operation using limited field excitation power provided through power converters. Finally, the reduced switchgear mass facilitated through the use of a high-frequency AC system, setting-less protection zones, and simplified switches for fault clearance provides enhanced operational capability. This system can be controlled so that fault energy is minimized, preventing collateral damage to aircraft structures even with high voltage distribution. Glenn's innovative system adds performance, efficiency, reliability, and cost savings to cutting-edge hybrid electric technology.
This is an early-stage technology requiring additional development, and Glenn welcomes co-development opportunities.

Reverse Vortex Ring (RVR)
Vibration problems, which occur more frequently in high power to weight machines, often lead to costly down time, subsequent redesign, and, in some instances, catastrophic failure. A disproportionate number of vibration problems in rotating machinery can be attributed to highly pre-swirled fluid entering tight clearance locations such as seals and fluid bearings. The relationship between high fluid pre-swirl and undesirable vibration issues is clear. Machines with high levels of fluid pre-swirl are more susceptible to instabilities and vibration problems.
A top priority in rotor dynamic design, therefore, is to develop devices to minimize the level of fluid pre-swirl entering tight clearance locations. The RVR was designed to condition the flow prior to entering the seal (or axial flow fluid-film bearing) so that the flow through the annular clearance is at a minimum purely axial. While conventional swirl brakes have only been shown to reduce pre-swirl by up to 30%, the RVR can actually reverse the direction of the swirl, so that circumferential fluid velocity flows in a direction counter to shaft rotation. Thus, a classic detriment to rotating machinery has now become an asset to ameliorate vibration issues through the RVR.
The RVR is axially efficient, typically increasing the axial length of a smooth annular seal on the order of 10-12%.
The RVR has been extensively tested and is now in use at NASA.

New Wing Design Exponentially Increases Total Aircraft Efficiency
Adverse yaw, present in current aircraft design, is the adverse horizontal movement around a vertical axis of an aircraft; the yaw opposes the direction of a turn. As an aircraft turns, differential drag of the left and right wings while banking contributes to aircraft yaw. Proverse yaw—yawing in the same direction as a turn—would optimize aircraft performance. Initial results from flight experiments at Armstrong demonstrated that this wing design unequivocally established proverse yaw. This wing design further reduces drag due to lift at the same time.
How It Works
The Armstrong team (supported by a large contingent of NASA Aeronautics Academy interns) built upon the 1933 research of the German engineer Ludwig Prandtl to design and validate a scale model of a non-elliptical loaded wing that reduces drag and increases efficiency.
The key to the innovation is reducing the drag of the wing through use of an alternative bell-shaped spanload, as opposed to the conventional elliptical spanload. To achieve the bell spanload, designers used a sharply tapered wing, with 12 percent less wing area than the comparable elliptical spanload wing. The new wing has 22 percent more span and 11 percent less area, resulting in an immediate 12 percent drag reduction.
Furthermore, using twist to achieve the bell spanload produces induced thrust at the wing tips, and this forward thrust increases when lift is increased at the wingtips for roll control. The result is that the aircraft rolls and yaws in the same direction as a turn, eliminating the need for a vertical tail. When combined with a blended-wing body, this approach maximizes aerodynamic performance, minimizes weight, and optimizes flight control.
Why It Is Better
Conventional aircraft make use of elliptical loaded wings to minimize drag. However, achieving aircraft stability and control in conventional elliptical wings produces a strong adverse yaw component in roll control (i.e., the aircraft will yaw the opposite direction with application of roll control). Therefore, a vertical tail or some other method of direct yaw control is required, such as split elevons for use as drag rudders. The use of elliptical wings also results in a suboptimal amount of structure to carry the integrated wing bending moment.
Adopting the bell-shaped spanload change results in an immediate 12 percent drag reduction. In addition, optimization of the overall aircraft configuration is projected to achieve additional significant overall performance increases.

Next Generation “Closed Strayton” Engine Design
The core “Strayton” generator technology consists of a gas turbine engine with short, axial pistons installed inside the hollow turbine shaft. These pistons form a Stirling engine that cycles via thermo-acoustic waves, transferring heat from the turbine blades to the compressor stage, which improves overall engine performance. Power to an alternator is, thus, delivered from both turbine shaft rotation and the oscillation of the internal pistons.
This synergistic relationship is markedly enhanced in a closed-cycle system, where the sealed turbine engine recirculates a working fluid heated via an external source, such as a hydrogen fuel cell and combustor. This system supports higher compression ratios, reduces the turbine diameter to less than 4”, and eliminates the need for large recuperators. Operational efficiency is projected to extend into the low temperature range (750° C), reducing the need for advanced materials and providing cleaner combustion for hydrogen-based applications. Pressurized, inert working fluids also replace mechanical bearings and gearboxes, enabling years of maintenance-free operation.
The fuel cell and Stirling cycle produce 10% of the total system energy, while the Brayton cycle produces 90%. Other external heat sources could include nuclear, solar, or biogas. Conservative estimates for the hydrogen fuel-cell configuration lifetime are in the 100,000 hour range.