Smart Coating for Corrosion Detection and Protection
Materials and Coatings
Smart Coating for Corrosion Detection and Protection (KSC-TOPS-1)
A smart and environmentally friendly coating system
Overview
NASA Kennedy Space Center seeks partners interested in the commercial application of a smart, environmentally friendly coating system for early detection and inhibition of corrosion and self-healing of mechanical damage without external intervention. This coating will have the inherent ability to detect the onset of corrosion in the coated substrate and respond autonomously to control it. The high salt content of KSCs natural marine environment in combination with the sunlight, heat, and humidity of the subtropical Florida climate makes KSC the country's most corrosive area according to the American Society of Metals. These highly corrosive conditions are exacerbated at KSCs launch pads by extreme heat and acidic exhaust from the solid rocket motors of the space vehicles.
The Technology
The smart coating is based on the controlled release of corrosion inhibitors and indicators from specially formulated microcapsules and particles pioneered by NASA (patent allowed). The coating detects corrosion in its early stages, inhibits it, and/or repairs the coating. The onset of corrosion triggers the release of compounds that indicate and inhibit corrosion. Mechanical damage to the coating triggers the release of film-forming compounds to repair the damage. In practice, the corrosion-responsive microcapsules detect the chemical changes that occur when corrosion begins and respond by releasing their contents. A corrosion indicator will identify the affected region with a color change, and healing agents and corrosion inhibitors help mitigate the corrosion.
The microcapsules can be tailored for incorporation into different coating systems. This multifunctional coating system will reduce maintenance cost and improve safety by preventing catastrophic corrosion failures. The coating can reduce infrastructure life cycle costs by extending the life of corrosion-susceptible structures and components, reduce inspection times of structures, and reduce the level of repair for corrosion-affected areas.
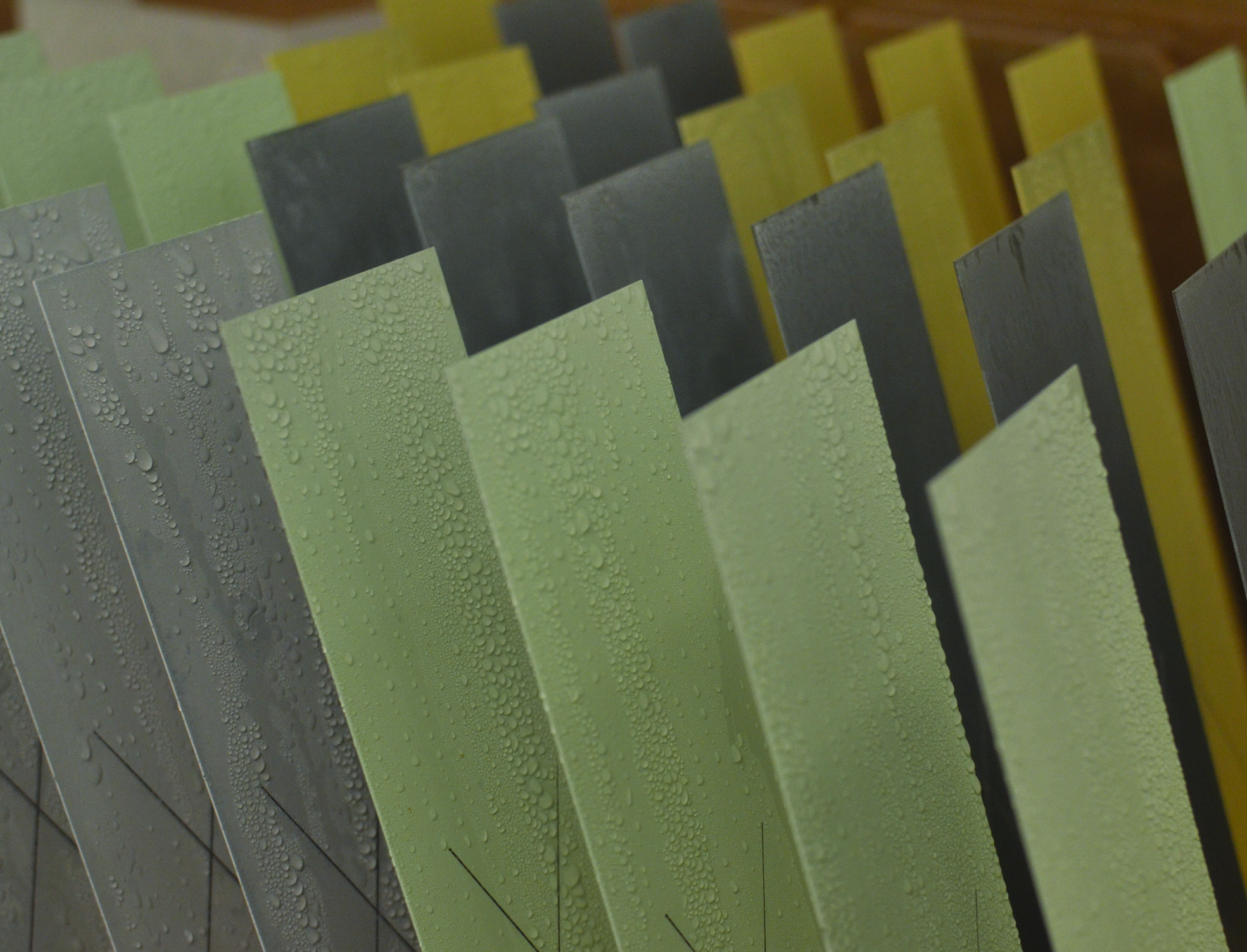
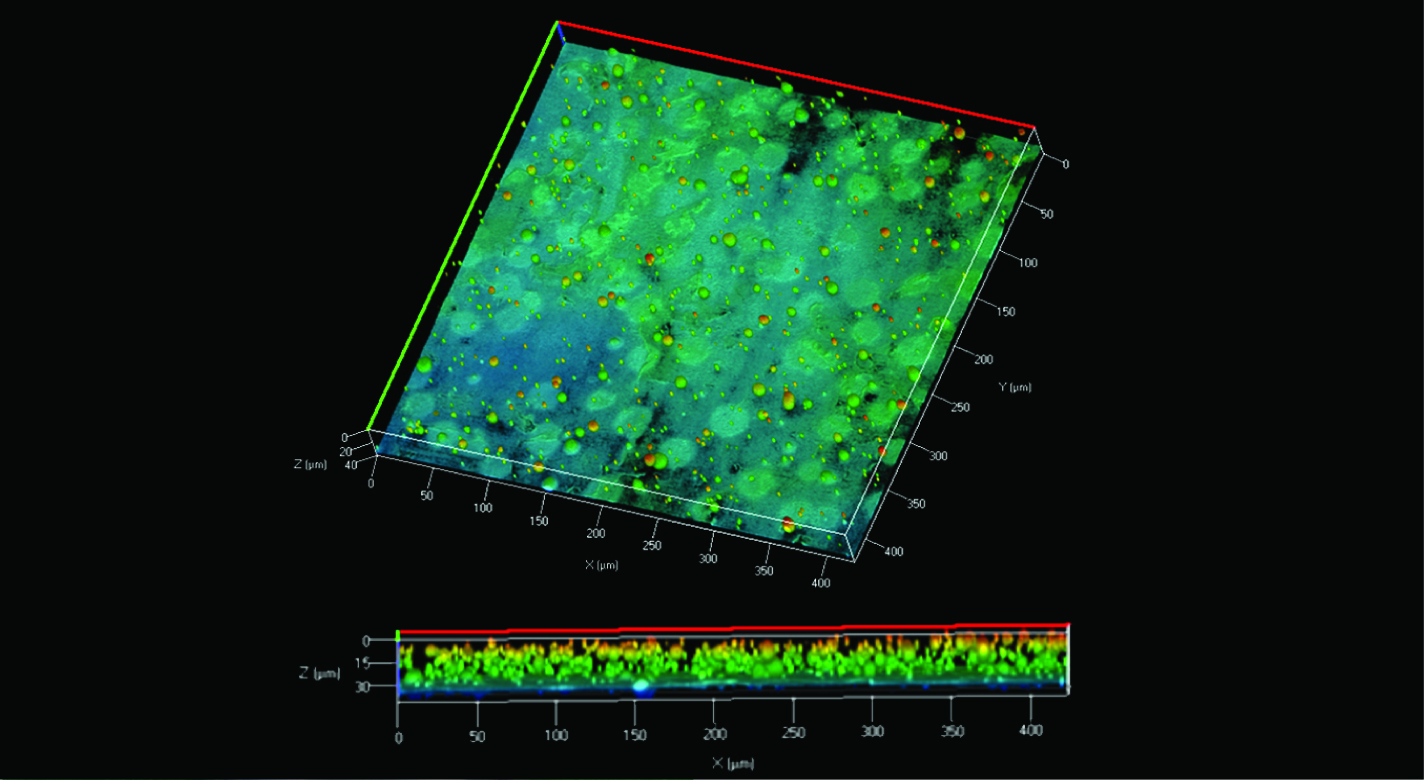
Benefits
- Autonomous corrosion detection and protection
- Early corrosion detection and hidden corrosion indication
- Self-healing of mechanical damage
- On-demand delivery of corrosion inhibitors
Applications
- The technology is a corrosion detection and prevention coating for:
- Bridges
- Automobiles
- Ships
- Pipes and other infrastructure
- Machinery
- Airplanes
Tags:
|
|
Related Links:
|
Similar Results
Multidimensional Damage Detection System
The Damage Detection System consists of layered composite material made up of two-dimensional thin film damage detection layers separated by thicker, nondetection layers, coupled with a detection system. The damage detection layers within the composite material are thin films with a conductive grid or striped pattern. The conductive pattern can be applied on a variety of substrates using several different application methods. The number of detection layers in the composite material can be tailored depending on the level of damage detection detail needed for a particular application. When damage occurs to any detection layer, a change in the electrical properties of that layer is detected and reported. Multiple damages can be detected simultaneously, providing real-time detail on the depth and location of the damage.
The truly unique feature of the System is its flexibility. It can be designed to gather as much (or as little) information as needed for a particular application using wireless communication. Individual detection layers can be turned on or off as necessary, and algorithms can be modified to optimize performance. The damage detection system can be used to generate both diagnostic and prognostic information related to the health of layered composite structures, which will be essential if such systems are utilized to protect human life and/or critical equipment and material.

Alternative Transparent Coating Lotus Suitable for Optics with Vacuum Deposition Layer
In addition to previous LOTUS coating formulations, an additional optical formulation may be applied via vacuum deposition. This coating forms a top layer and may be applied in different thicknesses that serve to enhance its hydrophobic properties. The vacuum deposited material may comprise fluorinated ethylene propylene or a similar material. This coating is transparent and can be used on optical components or any other applications requiring a clear coating.

Activated Metal Treatment System (AMTS) for Paints
PCBs have been shown to cause cancer in animals and to have other adverse effects on immune, reproductive, nervous, and endocrine systems. Although the production of PCBs in the United States has been banned since the late 1970s, many surfaces are still coated with PCB-laden paints. The presence of PCBs in paints adds complexity and expense for disposal. Some treatment methods (e.g., use of solvents, physical removal via scraping) are capable of removing PCBs from surfaces, but these technologies create a new waste stream that must be treated. Other methods, like incineration, can destroy the PCBs but destroy the painted structure as well, preventing reuse.
To address limitations with traditional abatement methods for PCBs in paints, researchers at NASAs Kennedy Space Center (KSC) and the University of Central Florida have developed the Activated Metal Treatment System (AMTS) for Paints. This innovative technology consists of a solvent solution (e.g., ethanol, d-limonene) that contains an activated zero-valent metal.
AMTS is first applied to the painted surface either using spray-on techniques or wipe-on techniques. The solution then extracts the PCBs from the paint. The extracted PCBs react with the microscale activated metal and are degraded into benign by-products. This technology can be applied without removing the paint or dismantling the painted structure. In addition, the surface can be reused following treatment.
Feedthrough for Severe Environments and Temperatures
Space and ground launch support related hardware often operate under extreme pressure, temperature, and corrosive conditions. When dealing with this type of equipment, it is frequently necessary to run wiring, tubes, or fibers through a barrier separating one process from another with one or both operating in extreme environments. Feedthroughs used to route the wiring, tubes, or fibers through these barriers must meet stringent sealing and leak tightness requirements.
This affordable NASA feedthrough meets or exceeds all sealing and leak requirements utilizing easy-to-assemble commercial-off-the-shelf hardware with no special tooling. The feedthrough is a fully reconfigurable design; however, it can also be produced as a permanent device. Thermal cycling and helium mass spectrometer leak testing under extreme conditions of full cryogenic temperatures and high vacuum have proven the sealing capability of this feedthrough with or without potting (epoxy fill) on the ends. Packing material disks used in the construction of the device can be replaced as needed for rebuilding a given feedthrough for another job or a different set of feeds if potting is not used for the original feedthrough build. (Potting on one or both sides of the sleeve provides double or triple leak sealing protection). Variable Compression Ratio (VCR) connectors were adapted for the pressure seal on the feedthrough; however, any commercial connector can be similarly adapted. The design can easily be scaled up to larger (2" diameter) and even very large (12" or more) sizes.

Self-Healing Wire Insulation
Insulation is necessary on electrical wires in order to protect electrical systems from shorting. In high voltage systems such shorting can lead to sparking and fires. Many lives have been lost due to electrical wire insulation failure. Many man hours are also expended in the repair and inspection of electrical wiring in order to attempt to prevent wire failure. Wire insulation with a built in "self-healing" capability would greatly improve the safety of systems containing electrical wiring. Such insulation would require far less inspection and repair time over the lifetime of the system.
Polyimides such as Kapton are an integral part of high performance electrical wire insulation. Traditional polyimides are very inert to solvents and do not melt. A new set of polyimides, developed for use as films for the manual repair of high performance electrical wire insulation, have a low melting point and can be dissolved in special solvents. These properties can be taken advantage of in self-healing polyimide films. Microcapsules containing a solvent soluble polyimide are prepared using industry standard inter-facial or in situ polymerization techniques. These capsules are then incorporated into a low melt polyimide film for use as either a primary electrical wire insulation or as one of several layers of a composite wire insulation. The low melt polyimide film substrate in which the microcapsules are incorporated has good solubility with the solvent used to dissolve the polyimide which makes up the fluid inside the microcapsule. Such a capsule filled insulation, when cut or otherwise damaged, will result in the release of the capsule contents into the cut or damage area. The solvent then dissolves a small amount of the surrounding polyimide insulation but will also begin the process of evaporation. The combination of these two processes allows for excellent intermingling of the healant and the surrounding substrate, resulting in a repair with superior bonding and physical properties.