Polyimide Wire Insulation Repair System
materials and coatings
Polyimide Wire Insulation Repair System (KSC-TOPS-35)
Permanent, flexible, and less intrusive wire repair systems
Overview
NASA Kennedy Space Center seeks partners interested in the commercial application of its Polyimide Wire Insulation Repair System. This technology is a kit, consisting of thin film polyimide patches that are applied to damaged areas of wire insulation with a heating device that adheres the polyimide repair film into place. The technology has been prototyped and successfully tested by NASA and the Naval Air Systems Command (NAVAIR). Wire repairs made with this system are permanent, flexible, and much less intrusive than repairs made using current techniques and materials. The technology is well suited for all applications of polyimide and other high-performance polymer-jacketed wire constructions.
The Technology
A major limitation of current aerospace wire insulation is that it tends to crack and fray as it ages and is easily damaged. Generally, it is more cost-effective to repair wire insulation than to replace a section of the wire (or bundle) itself. Current repair methods include a tape wrap repair and a heat shrink repair. These methods have a number of drawbacks: susceptibility to vibration, fluid intrusion, and other mechanical stresses. The repair patch/material can loosen or separate, exposing the bare metal conductor or opening the polyimide insulation to more damage at the interface.
The technology developed by KSC is a flexible polyimide film patch (either wrap or sleeve) that is heated with a custom heating tool to melt, flow, and cure the film. The new technology results in hermetically sealed, permanent repairs that are much more flexible and less intrusive than repairs made using current practices. The repair remains flexible after application, has no limit in length or bend radius, and retains the high-temperature exposure of the original polyimide insulation. Extensive testing by NASA and NAVAIR has demonstrated that these repairs comply with industry standards for tensile strength, electrical resistivity, voltage breakdown, solvent resistance, and flammability. This system is adaptable and may also be used on larger-gauge wiring, as well as flat-ribbon wire harnesses and twisted shielded wires.
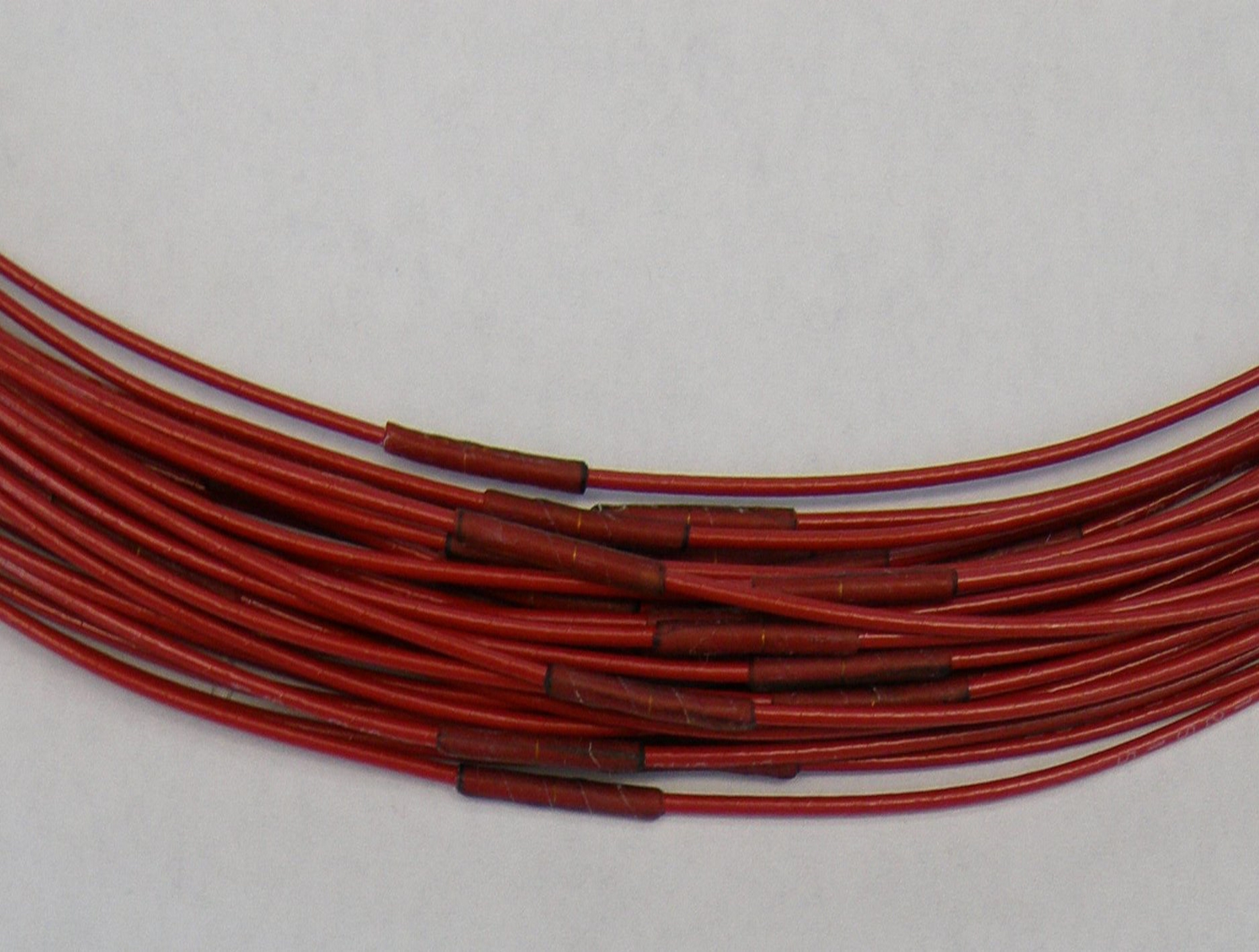
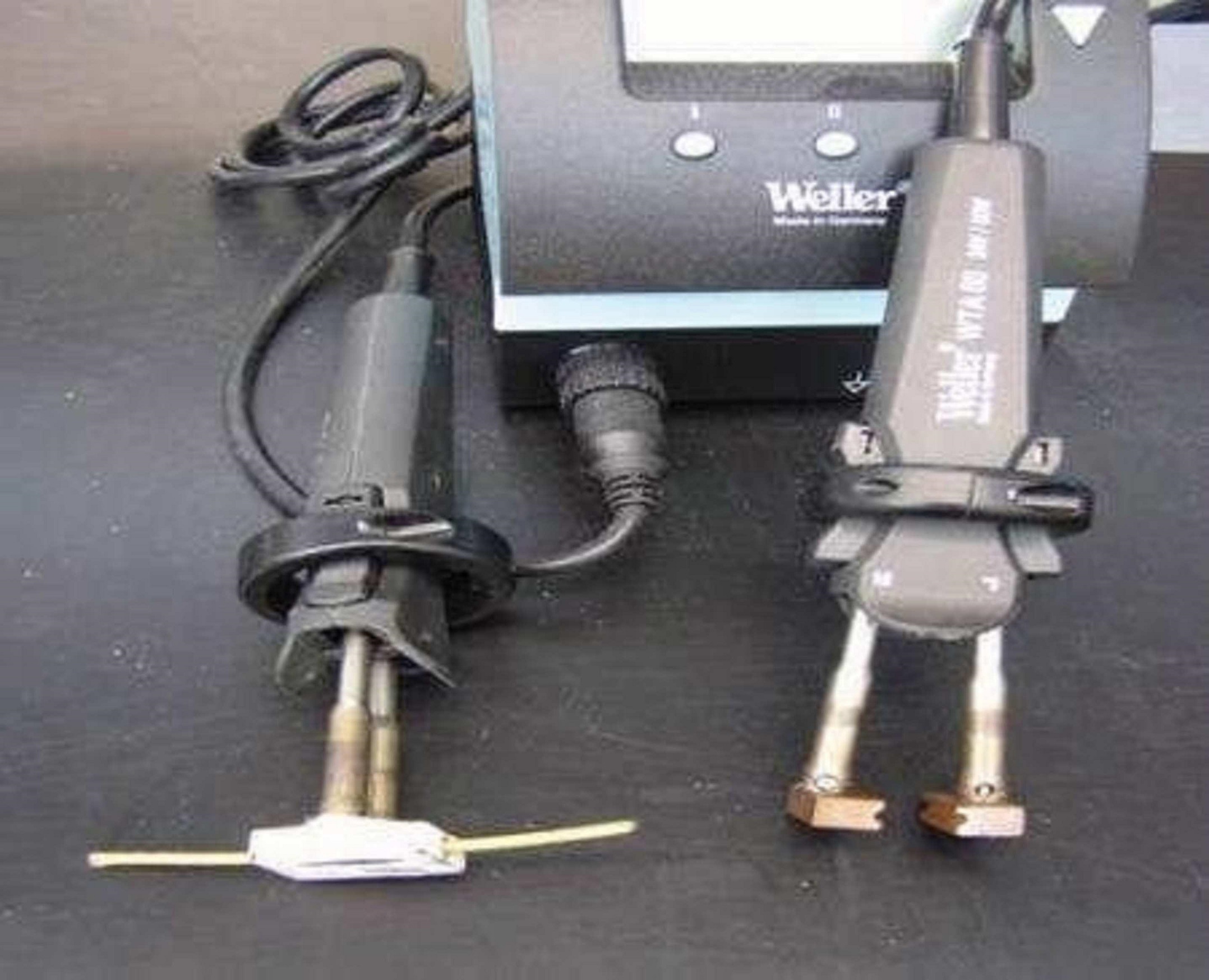
Benefits
- High performance Repairs comply with industry standards for tensile strength, electrical resistivity, voltage breakdown, solvent resistance, and flammability
- Flexibility Repairs are more flexible and less bulky than repairs using existing techniques
- Airtight - Technology provides a hermetic repair
- Durability Repairs are permanent
- Adhesion Unique adhesive properties provide superior bonding to damaged surface
- Adaptability Materials and techniques can be used on larger-gauge wiring and flat-ribbon wire harnesses
Applications
- Aerospace Wiring
- Automotive Wiring
- Marine Wiring
- Industrial Wiring
Similar Results

Self-Healing Wire Insulation
Insulation is necessary on electrical wires in order to protect electrical systems from shorting. In high voltage systems such shorting can lead to sparking and fires. Many lives have been lost due to electrical wire insulation failure. Many man hours are also expended in the repair and inspection of electrical wiring in order to attempt to prevent wire failure. Wire insulation with a built in "self-healing" capability would greatly improve the safety of systems containing electrical wiring. Such insulation would require far less inspection and repair time over the lifetime of the system.
Polyimides such as Kapton are an integral part of high performance electrical wire insulation. Traditional polyimides are very inert to solvents and do not melt. A new set of polyimides, developed for use as films for the manual repair of high performance electrical wire insulation, have a low melting point and can be dissolved in special solvents. These properties can be taken advantage of in self-healing polyimide films. Microcapsules containing a solvent soluble polyimide are prepared using industry standard inter-facial or in situ polymerization techniques. These capsules are then incorporated into a low melt polyimide film for use as either a primary electrical wire insulation or as one of several layers of a composite wire insulation. The low melt polyimide film substrate in which the microcapsules are incorporated has good solubility with the solvent used to dissolve the polyimide which makes up the fluid inside the microcapsule. Such a capsule filled insulation, when cut or otherwise damaged, will result in the release of the capsule contents into the cut or damage area. The solvent then dissolves a small amount of the surrounding polyimide insulation but will also begin the process of evaporation. The combination of these two processes allows for excellent intermingling of the healant and the surrounding substrate, resulting in a repair with superior bonding and physical properties.

In Situ Wire Damage Detection and Rerouting System
The tester was designed to monitor electrical faults in either online or offline modes of operation. In the online mode, wires are monitored without disturbing their normal operation. A cable can be monitored several times per second in the offline mode, and once per second in the online mode. The online cable fault locator not only detects the occurrence of a fault, but also determines the type of fault (short/open/intermittent) and the location of the fault. This enables the detection of intermittent faults that can be repaired before they become serious problems. Since intermittent faults occur mainly during operations, a built-in memory device stores all relevant fault data. This data can be displayed in real time or retrieved later so maintenance and repairs can be completed without spending countless hours attempting to pinpoint the source of the problem.
Hardware and algorithms have also been developed to safely, efficiently, and autonomously transfer electrical power and data connectivity from an identified damaged/defective wire in a cable to an alternate wire path. This portion of the system consists of master and slave units that provide the diagnostic and rerouting capabilities. A test pulse generated by the master unit is sent down an active wire being monitored by the slave unit. When the slave unit detects the test pulse, it routes the pulse back to the master unit through a communication wire. When the master unit determines that a test pulse is not being returned, it designates that wire as faulty and reroutes the circuit to a spare wire.

Self-Healing Low-Melt Polyimides
There are multiple space-related systems that can benefit from high performance, thin film, self-healing/sealing systems. Space vehicles and related ground support equipment can contain miles of wire, much of which is buried inside structures making it very difficult to access for inspection and repair. Space-based inflatable structures, solar panels, and astronauts performing extra-vehicular activities are subject to being struck by micrometeoroids and orbital debris. Self-healing or sealing layers on inflatables, solar panels and spacesuits would increase the safety and survivability of astronauts as well as the survivability and functionality of inflatables and solar panels. Self-healing insulation on wiring would greatly improve the reliability and safety of systems containing such wiring and reduce inspection and repair time over the lifetime of those systems. This technology combines the use of a self-sealing low melt, high performance polyimide film that exhibits the ability, when cut, for separated edges to slowly flow back together and seal itself, with the options of a laminate system and the inclusion of healant microcapsules that, when broken, release healant which can then additionally assist in the healing process. Combinations of the healing approaches can be enabling to the healing process proceeding at a much greater rate and dual mode healing approach can also allow for healing of a larger area.

Layered Composite Insulation for Extreme Conditions (LCX)
The approach in developing the LCX system was to provide a combination of advantages in thermal performance, structural capability, and operations. The system is particularly suited for the complex piping, tanks, and apparatus subjected to the ambient environment common in the aerospace industry. The low-cost approach also lends the same technology to industrial applications such as building construction and chilled-water piping. The system can increase reliability and reduce life cycle costs by mitigating moisture intrusion and preventing the resulting corrosion that plagues subambient-temperature insulation systems operating in the ambient (humidity and rain) environment. Accumulated internal water is allowed to drain and release naturally over the systems normal thermal cycles. The thermal insulation system has a long life expectancy because all layer materials are hydrophobic or otherwise waterproof. LCX systems do not need to be perfectly sealed to handle rain, moisture accumulation, or condensation.
Mechanically, the LCX system not only withstands impact, vibration, and the stresses of thermal expansion and contraction, but can help support pipes and other structures, all while maintaining its thermal insulation effectiveness. Conventional insulation systems are notoriously difficult to manage around pipe supports because of the cracking and damage that can occur. Used alone or inside another structure or panel, the LCX layering approach can be tailored to provide additional acoustic or vibration damping as a dual function with the thermal insulating benefits. Because LCX systems do not require complete sealing from the weather, it costs less to install. The materials are generally removable, reusable, and recyclable, a feature not possible with other insulation systems. This feature allows removable insulation covers for valves, flanges, and other components (invaluable benefits for servicing or inspection) to be part of original designs.
Thermal performance of the LCX system has been shown to equal or exceed that of the best polyurethane foam systems, which can degrade significantly during the first two years of operation. With its inherent springiness, the system allows for simpler installation and, more importantly, better thermal insulation because of its consistency and full contact with the cold surface. Improved contact with the cold surface and better closure of gaps and seams are the keys to superior thermal performance in real systems. Eliminating the requirement for glues, sealants, mastics, expansion joints, and vapor barriers provides dramatic savings in material and labor costs of the installed system.

Advanced Materials for Electronics Insulation
Many researchers have attempted to use polymer-ceramic composites to improve the thermal and dielectric performance of polymer insulation for high voltage, high temperature electronics. However, using composite materials has been challenging due to manufacturing issues like incomplete mixing, inhomogeneous properties, and void formation. Here, NASA has developed a method of preparing and extruding polymer-ceramic composites that results in high-quality, flexible composite ribbons.
To achieve this, pellets of a thermoplastic (e.g., polyphenylsulfone or PPSU) are coated with an additive then mixed with particles of a ceramic (e.g., boron nitride or BN) as shown in the image below. After mixing the coated polymer with the ceramic particles, the blended material was processed into ribbons or films by twin-screw extrusion. The resulting ribbons are highly flexible, well-mixed, and void free, enabled by the coated additive and by using a particle mixture of micronized BN and nanoparticles of hexagonal BN (hBN).
The polymer-ceramic composite showed tunable dielectric and thermal properties depending on the exact processing method and composite makeup. Compared to the base polymer material, the composite ribbons showed comparable or improved dielectric properties and enhanced thermal conductivity, allowing the composite to be used as electrical insulation in high-power, high-temperature conditions.
The related patent is now available to license. Please note that NASA does not manufacturer products itself for commercial sale.