Silicon Carbide Fiber Tows
materials and coatings
Silicon Carbide Fiber Tows (LEW-TOPS-131)
Rapid processing method produces stronger materials, even heals lower-quality fibers
Overview
Innovators at NASA's Glenn Research Center have developed a rapid processing method that produces stronger, tailored silicon carbide (SiC) tows and even heals damaged or otherwise low-quality fibers. Never before could poor-quality SiC fibers be healed and improved by this magnitude. This simple microwave process enables SiC tows and parts made from SiC fibers to be integrated in previously impossible applications while significantly saving costs. Glenn's novel technique uses a microwave sintering furnace to reduce power requirements, processing temperatures (by as much as 1000°C), processing times, and costs. Thus, it is easier to produce quality, high-strength SiC tows, as well as to increase the effective yield of usable SiC material. This breakthrough process stands ready to significantly increase the implementation of lightweight, high-performance SiC/SiC ceramic matrix composite (CMC) materials and SiC fibers in aeronautics, automotive, power generation, and countless other industries that operate in extreme environments.
The Technology
SiC fiber tows and preform materials are commonly used as reinforcements in CMCs, to make parts for use in harsh, high-temperature environments such as aircraft engines. These materials are desirable for numerous high-temperature applications because of their very low weight and outstanding thermo-chemical inertness. However, the multiple-step process using electric furnaces to produce these materials have numerous drawbacks: they are very expensive ($10,000 to $25,000 per spool); they involve high temperatures (greater than 2000°C); they require high power (more than 700 watts); and they produce much wasted material. Glenn innovators have discovered an efficient way to improve the quality and strength of SiC fiber tows using a unique microwave-furnace design that induces molecular heating. Glenn's innovation relies on microwave sintering to convert a polymer to ceramic fibers/tows/yarns, or to manipulate commercially available SiC fibers to increase strength and improve other qualities. Not only can higher quality tows be produced, but also - for the first time - old, damaged, or otherwise unusable fibers can be improved and recycled, thereby saving significant costs by increasing yield. Even entire engine components can be placed in the furnace and restored. The desired results can be achieved in minutes rather than the usual hours or even days. Glenn's low-temperature microwave process provides greater control with less power, while also eliminating plasma generation and minimizing arcing events. Because this method also facilitates the shaping of the SiC fiber after initial processing, fabricating preforms with 2D or 3D architectures becomes simpler. Glenn's creative processing method makes producing SiC tows and preforms much less expensive, opening them up for increased use in a broad range of applications.
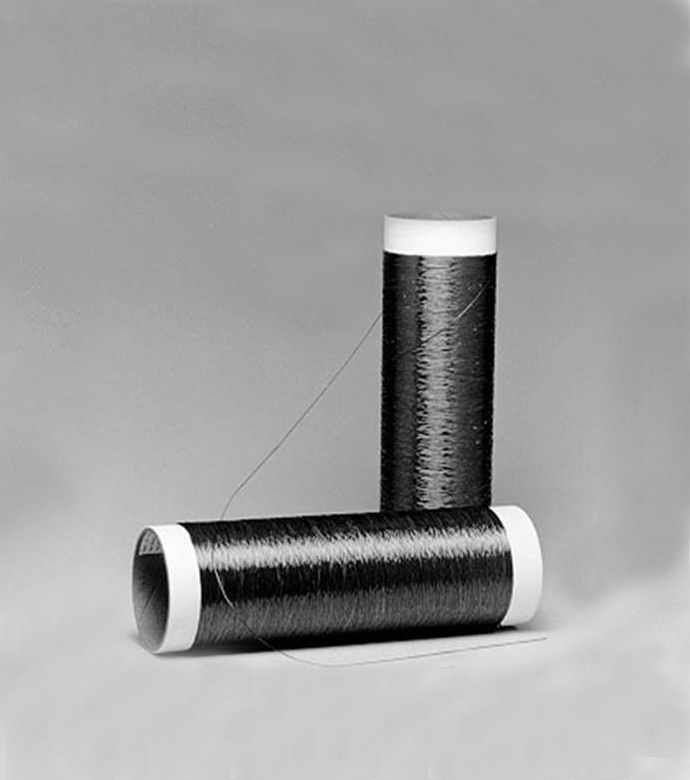
Benefits
- Cost-saving: Produces quality fibers consistently and heals low-quality fibers, thereby reducing costs
- Low-power: Decreases extended power usage from 700 watts to 70 watts or less
- Fast: Reduces processing time from more than 24 hours to 15 minutes
- Reduced temperature: Decreases processing temperature by as much as 60%
- Increased flexibility: Simplifies processing of hybrid tows and 2D and 3D architectures
Applications
- Aerospace (e.g., engines, thermal protection systems, and turbopumps)
- Propulsion (e.g., reusable rocket and thruster nozzles)
- Power (e.g., gas turbine engines, nuclear reactor fuel cladding, radiation blankets)
- Chemical manufacturing (e.g., heat exchangers, reformers, reactors, filters)
- Industrial machinery (e.g., preheaters, recuperators, and radiant tubes)
- Furnaces
- Turbines
Technology Details
materials and coatings
LEW-TOPS-131
LEW-19691-1
Similar Results

Silicon Carbide (SiC) Fiber-Reinforced SiC Matrix Composites
Aimed at structural applications up to 2700°F, NASA's patented technologies start with two types of high-strength SiC fibers that significantly enhance the thermo-structural performance of the commercially available boron-doped and sintered small-diameter “Sylramic” SiC fiber. These enhancement processes can be done on single fibers, multi-fiber tows, or component-shaped architectural preforms without any loss in fiber strength. The processes not only enhance every fiber in the preforms and relieve their weaving stresses, but also allow the preforms to be made into more shapes. Environmental resistance is also enhanced during processing by the production of a protective in-situ grown boron-nitride (iBN) coating on the fibers. Thus the two types of converted fibers are called “Sylramic-iBN” and “Super Sylramic-iBN”.
For high CMC toughness, two separate chemical vapor infiltration (CVI) steps are used, one to apply a boron nitride coating on the fibers of the preform and the other to form the SiC-based matrix. The preforms are then heat treated not only to densify and shrink the CVI BN coating away from the SiC matrix (outside debonding), but also to increase its creep resistance, temperature capability, and thermal conductivity.
One crucial advantage in this suite of technologies lies in its unprecedented customizability. The SiC/SiC CMC can be tailored to specific conditions by down-selecting the optimum fiber, fiber coating, fiber architecture, and matrix materials and processes. In any formulation, though, the NASA-processed SiC fibers display high tensile strength and the best creep-rupture resistance of any commercial SiC fiber, with strength retention to over 2700°F.

Integrated Circuit Chips
NASA Glenn's durable, extreme-temperature, integrated circuit chips begin with the replacement of conventional silicon IC transistors with n-channel SiC junction field effect transistors (JFET) and resistors that can reliably function above 500°C. JFETs with the necessary high-temperature stability and electrical gain are fabricated from commercial 4H-SiC wafers with epilayers using dry etching and a self-aligned n-type ion implantation. An innovative circuit approach creates digital logic gates from these normally-on n-channel JFETs and resistors. Using two levels of 500°C durable metal to interconnect numerous SiC gates, complex circuits enabling a variety of control, operation and sensing functions for intelligent systems in harsh environments can be implemented in physically small chips. The challenge of getting electrical signals to and from the chip in a harsh environment is overcome by the use of the iridium interfacial stack (IrIS) that acts simultaneously as a bond metal and diffusion barrier, and can be used on an ohmic contact to the SiC. Combined with Glenn-developed high-temperature durable ceramic chip packaging and harsh environment sensor technology, this revolutionary durable integrated circuit technology is game changing for harsh-environment applications of all types.

Packaging for SiC Sensors and Electronics
Prior approaches to bonding a SiC sensor and a SiC cover member relied on either electrostatic bonding or direct bonding using glass frits. The problem with the former is that its relatively weak bond strength may lead to debonding during thermal cycling, while the latter requires the creation of apertures that can allow sealant to leak. Glenn's innovation uses NASA's microelectromechanical system direct chip attach (MEMS-DCA) technology that can be bulk-manufactured to reduce sensor costs. The MEMS-DCA process allows a direct connection to be made between chip and pins, thereby eliminating wire bonding. Sensors and electronics are attached in a single-stage process to a multifunctional package, which, unlike previous systems, can be directly inserted into the housing. Additional thick pins within the electrical outlet allow the package to be connected to external circuitry. Furthermore, because the top and bottom substrates' thermomechanical properties are similar to that of the sensors, the problem of mismatch in the coefficient of thermal expansion is significantly reduced, minimizing thermal cycling and component fatigue. By protecting sensors and electronics in temperatures up to 600°C, approximately twice what has previously been achievable, Glenn's innovation enables SiC components to realize one of their most exciting possibilities - direct placement within high-temperature environments.

Metallization for SiC Semiconductors
To avoid catastrophic failure, traditional electrical ohmic contacts must be placed at some distance from the optimal position (especially for sensors) in high-temperature environments. In addition, conventional metallization techniques incur significant production costs because they require multiple process steps of successive depositions, photolithography, and etchings to deposit the desired ohmic contact material. Glenn's novel production method both produces ohmic contacts that can withstand higher temperatures than ever before (up to 600°C), and permits universal and simultaneous ohmic contacts on n- and p-type surfaces. This makes fabrication much less time-consuming and expensive while also increasing yield. This innovative approach uses a single alloy conductor to form simultaneous ohmic contacts to n- and p-type 4H-SiC semiconductor. The single alloy conductor also forms an effective diffusion barrier against gold and oxygen at temperatures as high as 800°C. Glenn's extraordinary method enables a faster and less costly means of producing SiC-based sensors and other devices that provide quicker response times and more accurate readings for numerous applications, from jet engines to down-hole drilling, and from automotive engines to space exploration.

Thermal Management for Aircraft Propulsion Systems
Aircraft thermal management systems typically comprise over half the mass associated with full electric power propulsion systems, with significant negative impact on fuel efficiency. In addition, the traditional method of using jet fuel to cool aircraft generators does not provide enough cooling for use in flight-weight cryogenic systems. Lastly, the much higher bus voltages required for flight-weight systems (4.5 kV vs. 270 V) introduce additional spark-ignition hazards associated with alternative cryogenic cooling fuels, including liquid methane or liquid hydrogen. The Glenn flight-weight thermal management system addresses all of these problems by using the considerable waste heat energy from turbogenerators to create a pressure wave thermoacoustically. This wave can then be delivered quietly and efficiently via routed ductwork to hollow pulse-tube coolers located near any component in the aircraft that requires cooling. The tubes can be fabricated in any length and can be curved to fit any space. This technology also allows waste heat energy to be used in at least four ways: 1) the waste heat energy can drive a thermoacoustics-based ambient or cryogenic heat pump; 2) it can be channeled directly into a thermoacoustic engine that generates power; 3) it can convectively preheat the fuel/ or air supplied to the aircraft engine; 4) it can drive a pulse-tube generator providing power. The delivered thermoacoustic power can provide cabin cooling as well as ambient/cryogenic cooling of converter, cables, and motors. In addition, this power can be converted to local electric power through the use of a transducer (such as a linear alternator) or piezoelectrics. Further, the efficient thermal management system enables the size, mass, and resultant cost of the radiating fins to be reduced. Glenn's system offers an efficient method of cooling next-generation flight-weight electric aircraft with significant benefits for fuel efficiency and safety.