High-Strength Superelastic Compounds
Materials and Coatings
High-Strength Superelastic Compounds (LEW-TOPS-144)
Shock-resistant material eliminates corrosion and polishes to a smooth surface finish
Overview
NASA's Glenn Research Center has developed a new method for producing a shock- and corrosion-proof superelastic intermetallic materials including NiTiNOL 60 (60NiTi) for use in ball bearings and other mechanical components. These superelastic materials can withstand tremendous loads and stresses without permanent deformation or denting. At the same time, the nickel-titanium alloy is immune to corrosion and rust, unlike mechanical components made from iron or steel. In addition, the material does not chemically degrade or break down lubricants, a common problem with existing bearing materials. These materials are best suited for oil lubricated rolling and sliding contact applications requiring superior and intrinsic corrosion resistance, electrical conductivity, and non-magnetic properties.
The Technology
60NiTi, which contains 60% nickel and 40% titanium, is a superelastic intermetallic material for use in bearings, gears, and other mechanical systems. When properly processed, 60NiTi is hard, lightweight, electrically conductive, highly corrosion resistant, readily machined prior to final heat treatment, non-galling, and non-magnetic.
60NiTi was previously considered difficult to machine, partly because of issues with residual stresses and quench cracking. Modern ceramic processing methods, co-developed by NASA Glenn, now enable 60NiTi bearings to be easily manufactured. In addition, a method is available for pre-stressing the materials to increase their durability.
Bearing-grade 60NiTi is manufactured via a patented, high-temperature powder metallurgy (PM) process. Pre-alloyed 60NiTi powder is hot isostatic pressed (HIPed) into various shapes and sizes depending upon the desired end product. To make 60NiTi balls, the powder is HIPed into rough, spherical ball blanks that are then ground, polished, and lapped. Because the PM process yields ball blanks that have isotropic mechanical properties, high-quality (Grade 5) ball bearings can be readily produced. The finished 60NiTi balls are bright and shiny in appearance and resemble conventional polished steel balls. The manufacture of 60NiTi balls is a fully commercialized process, and many standard ball sizes are available. The material can also be shaped into other metallic components, such as gears, sliding bearings, actuators, and drives.
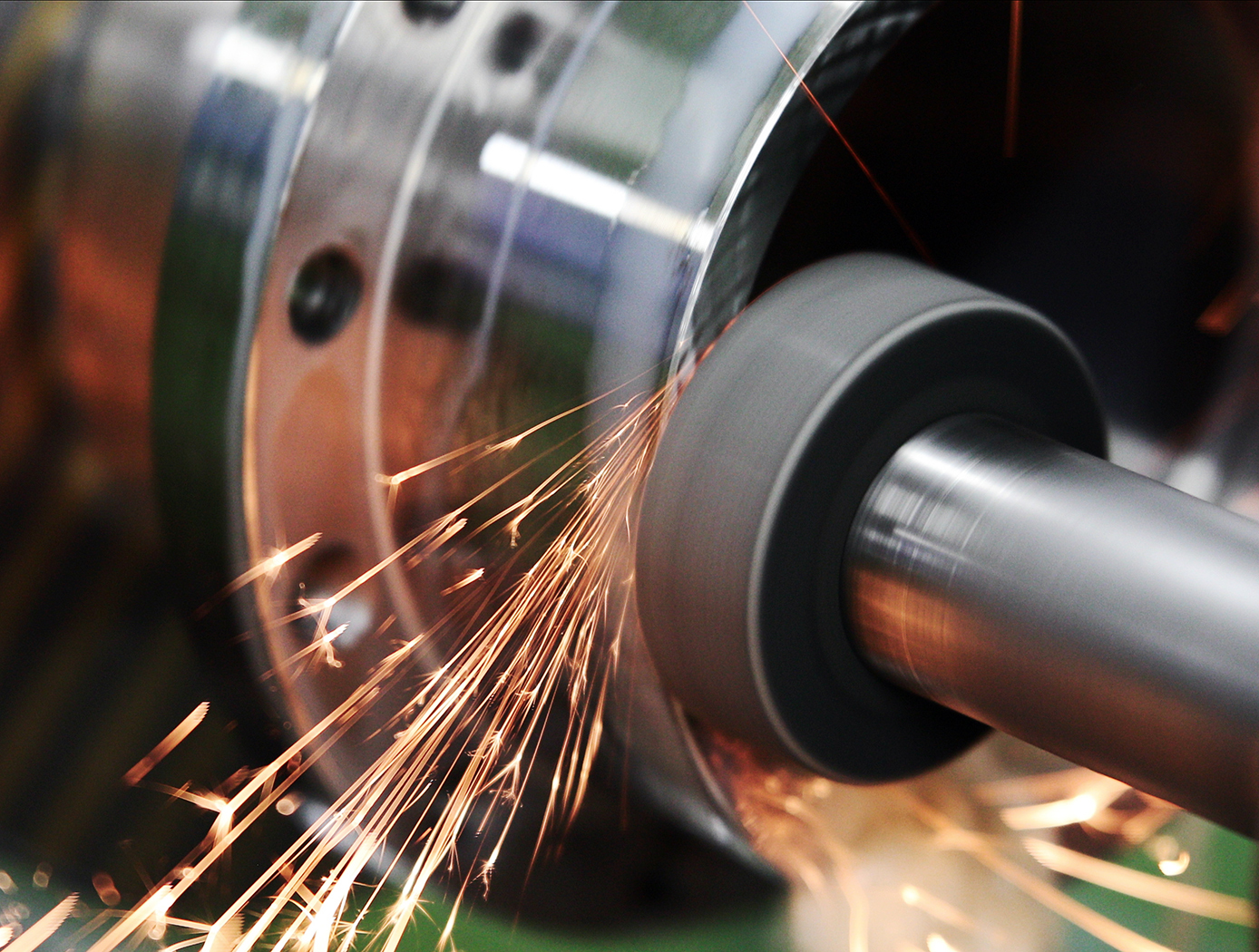
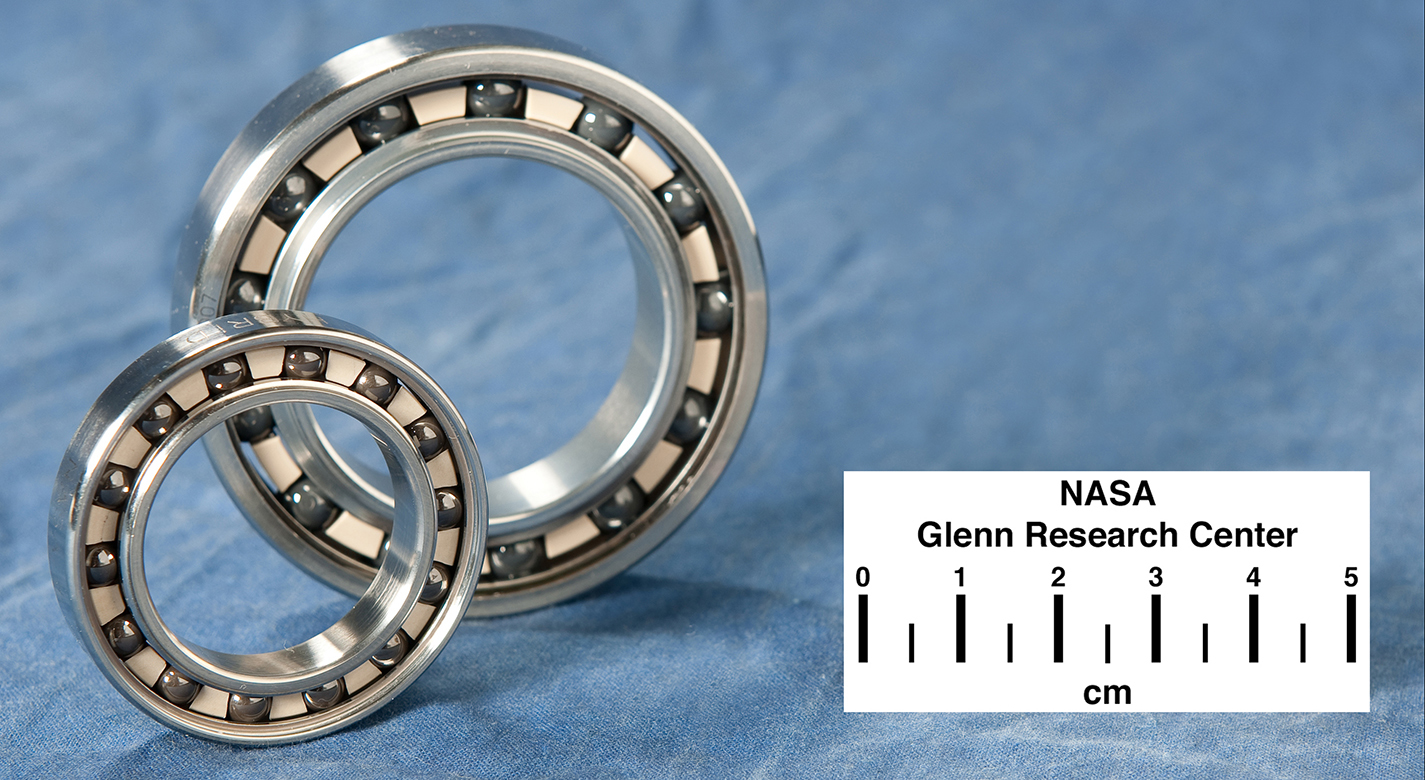
Benefits
- Corrosion-proof - Intrinsically immune to rust
- Shock-proof - Highly resistant to excessive and unexpected loads
- Durable - Can be pre-stressed to further resist wear
- Lightweight - Weighs 15% less than steel
- Tribochemically benign - Compatible with existing liquid lubricants
- Ease of manufacture - Can be manufactured to very high levels of precision with regard to final dimensions and surface finish
Applications
- Aerospace
- Mechanical systems
- Vehicles
- Marine
- Military
- Agricultural equipment
- Industrial machinery
- Valves
- Turbines
- Transportation
Technology Details
Materials and Coatings
LEW-TOPS-144
LEW-18785-1
LEW-18604-1
LEW-19029-1
LEW-18476-1
LEW-18476-2
LEW-18476-3
Similar Results

NiTi Alloy Ball Bearings
For the very first time, NASA Glenn has successfully produced large quantities of high-grade ball bearings that are less than 0.25" in diameter thanks to the development of a new alloy made of 57.6% Ni, 39.2% Ti and 3.2% Hf. Smaller, shockproof balls improve load capability in conventional steel races, aircraft control surface joints, actuator gearboxes, and more. The production of standard NiTi alloy ball bearings that are smaller than 0.375" in diameter has proven challenging for multiple reasons, the primary being that small parts made from NiTi alloys cool excessively before they can be quenched (an important step in attaining high hardness). NiTi-Hf alloy, on the other hand, does not require such high-rate quenching to achieve high hardness. Consequently, the production of small, extremely durable NiTi ball bearings is now a reality.
The powder metallurgy process by which these high-quality NiTi-Hf ball bearings are manufactured combines many new techniques with several existing ones. First, a high-purity NiTi-Hf powder is created through an atomization process and transformed into long, cylindrical rods through hot isostatic pressing. The rods are then cut into cylinders and machined into spheres somewhat larger than the desired finished ball size. Finally, the spheres are hardened through heat treatment and polished until the desired finished size diameter and surface finish (typically 1 micro-inch root mean square roughness) is achieved. The result is a non-corrosive, very hard, highly elastic yet remarkably strong ball bearing with unbridled potential.

High-Temperature Ni-Based Superalloy Composition
NASA's new Ni-based superalloy uses a powder metallurgy (PM) composition that inhibits the deleterious gamma-prime to gamma-phase transformation along stacking faults during high temperature creep deformation. Ni-base superalloys have excellent high temperature properties, mostly due to the presence of coherent precipitates. At higher temperatures, these precipitates are defeated by the diffusional shear dislocations producing intrinsic and extrinsic faults. Recent studies have found that, during deformation of turbine disk alloys at high temperature, Co, Cr, and Mo segregate to these faults (removing Ni and Al) inside the strengthening precipitates of these alloys. This represents a local phase transformation from the strengthening precipitate to the weaker matrix phase. Therefore, this elemental segregation significantly weakens the ability of a precipitate to withstand further deformation, producing faster strain rates in the alloy at higher temperatures. This invention presents a solution to prevent this type of segregation along these two faults to improve the creep properties of turbine disks and similar Ni-based alloys. By alloying a specific amount of eta phase formers (Ti, Ta, Nb, and Hf), the phase transformation to can be eliminated along 2-layer extrinsic stacking faults (SESFs) in precipitates without precipitating bulk eta phase. Also, by adding a certain amount of D019 formers (Mo and W), the phase transformation to can be mitigated along 1-layer intrinsic stacking faults (SISFs) without producing bulk sigma phase. This alloy composition incorporates both strengthening methods for use in jet turbine disks, though the composition has applications in other high-stress and/or high-temperature environments as are found in power plants, space launch systems, and other critical structural applications.

Oil-Free Lubricants
In applying PS400 using the plasma spray-coating process, a 0.010 inch layer is deposited onto a metal surface. This composite coating often includes a metallic-based binder, a metal-bonded hardener, a high-temperature lubricant, and/or a low- temperature lubricant. PS400's improved metallic-based binder alloy greatly increases the structural strength and durability of the composite with respect to the operating temperature and the bearing load, and provides superior dimensional stability. PS400's metal-bonded oxide hardening agent provides additional hardness, wear resistance, and thermal stability, while also exhibiting a low coefficient of friction when used in sliding contacts. It is also significantly less expensive in terms of both acquisition and grinding processes.
Depending on the desired environment, high- and low-temperature lubricants may be added to the composite coating. The preferred high-temperature lubricant is a metal fluoride and the optional optional low-temperature lubricant is composed of metals, such as silver or copper, that are soft enough to provide lubrication at low temperature while maintaining oxidation resistance with a sufficiently high melting point. These qualities permit the materials to be used over a broad temperature range. Once the spray coating has been applied, the metal surface is ground and polished to produce a smooth, self-lubricating surface before use. Unlike some coatings that must be diamond-ground, PS400 is readily ground with a substantially less expensive abrasive, such as silicon carbide. This grinding process generally yields a coating thickness of 200 to 400 micrometers.
In instances when a coating is not convenient or possible, powder metallurgy techniques using PM400 can be used to make freestanding self-lubricating components such as bushings and wear plates.

Shape Memory Alloy with Adjustable, Wide-Ranging Actuation Temperatures
SMAs are important multifunctional materials for the development of adaptive engineering structures. They exhibit a high work output that is competitive with, or superior to, conventional hydraulic, pneumatic, or electromagnetic actuators. While highly promising, SMAs are not always a practical alternative to conventional actuators because of their limited phase transformation temperatures and dimensional instability. Thanks to Glenn's innovative new SMA, that's about to change.
Unlike traditional binary NiTi SMAs, Glenn's Ni-Ti-Hf-Zr SMA includes secondary, nanoscale precipitate phases that offer inherent dimensional stability to the material. Consequently, there is minimal to no need for training, resulting in much faster production times, lower processing costs, and a finished product with superior work outputs and better operational life. These Ni-rich alloys can be produced by Vacuum Induction Melting, Vacuum Arc Melting, Vacuum Arc Remelting, and Induction Skull Melting. Perhaps the most exciting characteristic of Glenn's SMA, however, is its ability to achieve a broad range of transformation temperatures suitable for high temperature (100 to 300°C), ambient, and sub-ambient temperature applications nearing -100°C. Furthermore, these temperatures can be tailored and fine-tuned though heat treatment to fit the needed parameters for the application of interest. In contrast, traditional NiTi SMAs exhibit fixed phase transformation at temperatures from slightly below room temperature to around 100°C. Glenn's Ni-Ti-Hf-Zr SMA opens the door to countless applications that can benefit from the unique properties of SMAs but require high durability and extreme temperature capability.

Superelastic Tire
This NASA Glenn innovation comprises a non-pneumatic, compliant tire utilizing shape memory alloys (mainly NiTi and its derivatives) as load bearing components. These shape memory alloys are capable of undergoing significant reversible strain (up to 10%), enabling the tire to withstand an order of magnitude more deformation than other non-pneumatic tires before undergoing permanent deformation. Commonly used elastic-plastic materials (e.g. spring steels, composites, etc.) can only be subjected to strains on the order of ~ 0.3-0.5% before yielding. Hence, the use of a NiTi shape memory alloy produces a superelastic tire that is virtually impervious to plastic deformation. In addition, the utilization of shape memory alloys provides enhanced control over the effective stiffness as a function of the deformation, providing increased design versatility. For instance, the Glenn Superelastic Tire can be made to soften with increased deflection, reducing the amount of energy transferred to the vehicle during high deformation events. In addition, the use of shape memory alloys in the form of radial stiffeners, as opposed to springs, provides even more load carrying potential and improved design flexibility. This type of compliant tire would allow for increased travel speeds in off-road applications.