Oil-Free Lubricants
Materials and Coatings
Oil-Free Lubricants (LEW-TOPS-121)
Revolutionary solid lubricants enable extreme applications
Overview
NASA's Glenn Research Center has developed high-temperature solid lubricant materials to reduce friction and wear in mechanical components, especially in extreme temperatures. The lubricant performs in temperatures from cryogenic levels to greater than 900°C. It has been formulated to provide higher density, smoother surface finish, and better dimensional stability than prior solid lubricant coatings. It can be applied either through plasma spraying as a coating, known as PS400, or as a solid composite material via powder metallurgy, known as PM400. Because of its ability to maintain thermal and chemical stability in higher temperatures, PS/PM400 enables efficiency increases of up to 40% in rotating machinery applications. Furthermore, PS/PM400 has proven durable in over 20,000 hours of turbine engine operation. PS/PM400 offers a substantial upgrade in wear resistance and efficiency for a vast range of aerospace and aeronautics applications. Its unique combination of good mechanical properties, long-term environmental durability, exceptional friction and wear-reducing characteristics, higher density, smoother finish, and better dimension stability establishes it in a class by itself among solid self-lubricating materials.
The Technology
In applying PS400 using the plasma spray-coating process, a 0.010 inch layer is deposited onto a metal surface. This composite coating often includes a metallic-based binder, a metal-bonded hardener, a high-temperature lubricant, and/or a low- temperature lubricant. PS400's improved metallic-based binder alloy greatly increases the structural strength and durability of the composite with respect to the operating temperature and the bearing load, and provides superior dimensional stability. PS400's metal-bonded oxide hardening agent provides additional hardness, wear resistance, and thermal stability, while also exhibiting a low coefficient of friction when used in sliding contacts. It is also significantly less expensive in terms of both acquisition and grinding processes.
Depending on the desired environment, high- and low-temperature lubricants may be added to the composite coating. The preferred high-temperature lubricant is a metal fluoride and the optional optional low-temperature lubricant is composed of metals, such as silver or copper, that are soft enough to provide lubrication at low temperature while maintaining oxidation resistance with a sufficiently high melting point. These qualities permit the materials to be used over a broad temperature range. Once the spray coating has been applied, the metal surface is ground and polished to produce a smooth, self-lubricating surface before use. Unlike some coatings that must be diamond-ground, PS400 is readily ground with a substantially less expensive abrasive, such as silicon carbide. This grinding process generally yields a coating thickness of 200 to 400 micrometers.
In instances when a coating is not convenient or possible, powder metallurgy techniques using PM400 can be used to make freestanding self-lubricating components such as bushings and wear plates.
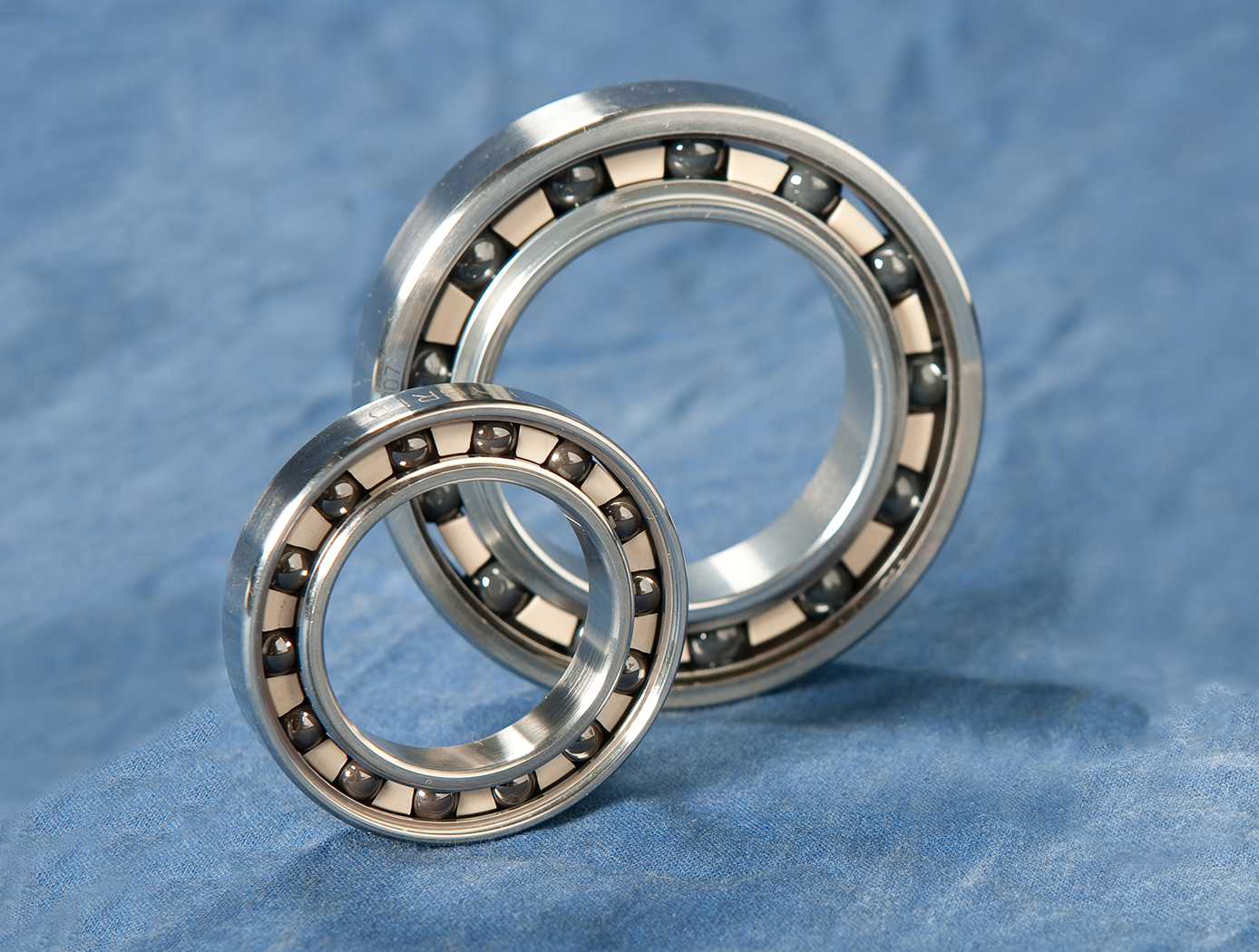
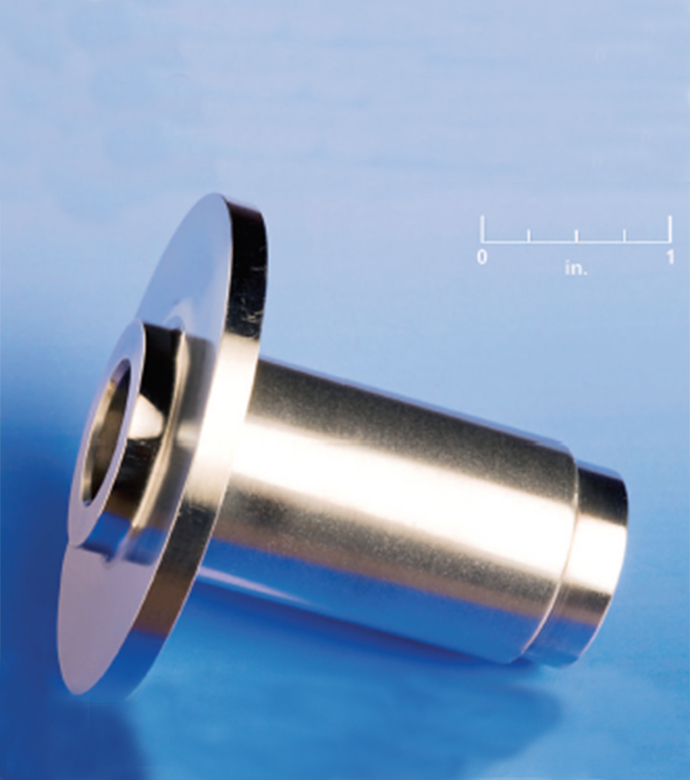
Benefits
- Increased strength and durability: Use of a hardening agent improves the material's wear resistance without sacrificing flexibility in fabrication or lubricating ability
- Better oxidative and dimensional stability: The metallic binder eliminates the oxidative effects that often lead to dimensional swelling in other solid lubricants
- Improved surface finish: A denser coating results in a smoother finish and improved performance
- Reduced expense and complexity in fabrication: PS/PM400 does not require extra processes and uses less expensive silicon-carbide grinding
- Easily procured: Available in the marketplace from licensed vendors
Applications
- Power generation
- Turbomachinery
- Valves
- Large engines
- Bushings, bearings, and races in extreme environments
- Turbines
- High-speed rotating equipment
Similar Results

Conductive High-Toughness Oxides
Oxide coatings have been used in thermal and environmental barrier layers for coatings for hot section turbine applications, among other uses. With the PS-PVD method, Glenn researchers observed the formation of a minority phase of a metastable oxide (zirconium oxide) that is usually found only in a vapor state. They found that the high temperatures and fast deposition process of the PS-PVD system incorporated nonequilibrium phases in the coating and retained them at room temperature as well as at high temperature in the absence of oxygen. The material is vaporized and condensed on the surface via a rapid quenching, essentially "trapping" this phase in the deposited coating. The coating microstructure and composition can also be manipulated by changing the processing parameters, allowing the thickness of the coating to be tailored to a given application. Since this metastable phase is conductive, this coating can be used as (for example) an extremely sensitive (thermal or temperature) sensor. It also has very good durability and erosion resistance, making it useful as a protective and conductive coating for electronics and microelectronics. This is an early-stage technology requiring additional development, and Glenn welcomes co-development opportunities.

Cryogenic Selective Surfaces
These materials, which are composed of highly optically transmissive materials, are engineered to provide near-perfect reflection of the full solar spectrum in space. The materials are finely divided such that they scatter and reflect the incoming radiation from the UV down into the mid-IR and are also coated in some fashion with silver to extend the reflectance down into the far IR region of the solar spectrum. With this near-perfect reflectance of the complete solar spectrum, the scientists envision use of these materials for maintaining cryogenic temperatures for extended periods of time in space. The materials have also been developed into highly flexible, moisture resistant selective surface paint.The use and storage of cryogenics fluids is critical to many space operations, and while there are thermal control coatings in use today for spacecraft, none can provide this near-perfect reflection required for long-term maintenance of cryogenic temperatures.

High-Strength Superelastic Compounds
60NiTi, which contains 60% nickel and 40% titanium, is a superelastic intermetallic material for use in bearings, gears, and other mechanical systems. When properly processed, 60NiTi is hard, lightweight, electrically conductive, highly corrosion resistant, readily machined prior to final heat treatment, non-galling, and non-magnetic.
60NiTi was previously considered difficult to machine, partly because of issues with residual stresses and quench cracking. Modern ceramic processing methods, co-developed by NASA Glenn, now enable 60NiTi bearings to be easily manufactured. In addition, a method is available for pre-stressing the materials to increase their durability.
Bearing-grade 60NiTi is manufactured via a patented, high-temperature powder metallurgy (PM) process. Pre-alloyed 60NiTi powder is hot isostatic pressed (HIPed) into various shapes and sizes depending upon the desired end product. To make 60NiTi balls, the powder is HIPed into rough, spherical ball blanks that are then ground, polished, and lapped. Because the PM process yields ball blanks that have isotropic mechanical properties, high-quality (Grade 5) ball bearings can be readily produced. The finished 60NiTi balls are bright and shiny in appearance and resemble conventional polished steel balls. The manufacture of 60NiTi balls is a fully commercialized process, and many standard ball sizes are available. The material can also be shaped into other metallic components, such as gears, sliding bearings, actuators, and drives.

3D-Printed Composites for High Temperature Uses
NASA's technology is the first successful 3D-printing of high temperature carbon fiber filled thermoset polyimide composites. Selective Laser Sintering (SLS) of carbon-filled RTM370 is followed by post-curing to achieve higher temperature capability, resulting in a composite part with a glass transition temperature of 370 °C.
SLS typically uses thermoplastic polymeric powders and the resultant parts have a useful temperature range of 150-185 °C, while often being weaker compared to traditionally processed materials. Recently, higher temperature thermoplastics have been manufactured into 3D parts by high temperature SLS that requires a melting temperature of 380 °C, but the usable temperature range for these parts is still under 200 °C.
NASA's thermoset polyimide composites are melt-processable between 150-240 °C, allowing the use of regular SLS machines. The resultant parts are subsequently post-cured using multi-step cycles that slowly heat the material to slightly below its glass transition temperature, while avoiding dimensional change during the process. This invention will greatly benefit aerospace companies in the production of parts with complex geometry for engine components requiring over 300 °C applications, while having a wealth of other potential applications including, but not limited to, printing legacy parts for military aircraft and producing components for high performance electric cars.

Self-Healing Wire Insulation
Insulation is necessary on electrical wires in order to protect electrical systems from shorting. In high voltage systems such shorting can lead to sparking and fires. Many lives have been lost due to electrical wire insulation failure. Many man hours are also expended in the repair and inspection of electrical wiring in order to attempt to prevent wire failure. Wire insulation with a built in "self-healing" capability would greatly improve the safety of systems containing electrical wiring. Such insulation would require far less inspection and repair time over the lifetime of the system.
Polyimides such as Kapton are an integral part of high performance electrical wire insulation. Traditional polyimides are very inert to solvents and do not melt. A new set of polyimides, developed for use as films for the manual repair of high performance electrical wire insulation, have a low melting point and can be dissolved in special solvents. These properties can be taken advantage of in self-healing polyimide films. Microcapsules containing a solvent soluble polyimide are prepared using industry standard inter-facial or in situ polymerization techniques. These capsules are then incorporated into a low melt polyimide film for use as either a primary electrical wire insulation or as one of several layers of a composite wire insulation. The low melt polyimide film substrate in which the microcapsules are incorporated has good solubility with the solvent used to dissolve the polyimide which makes up the fluid inside the microcapsule. Such a capsule filled insulation, when cut or otherwise damaged, will result in the release of the capsule contents into the cut or damage area. The solvent then dissolves a small amount of the surrounding polyimide insulation but will also begin the process of evaporation. The combination of these two processes allows for excellent intermingling of the healant and the surrounding substrate, resulting in a repair with superior bonding and physical properties.