High-Efficiency Solar Cell
power generation and storage
High-Efficiency Solar Cell (LEW-TOPS-50)
Selenium Interlayer for multi-junction photovoltaic cell for both space and terrestrial applications
Overview
Innovators at NASA's Glenn Research Center have developed a high-efficiency multi-junction solar cell that uses a thin interlayer of selenium as the bonding material between wafers. Selenium is a unique semiconductor in that its transparent to light at photon energies below the band gap (infrared), enabling light to pass from the multi-junction top cell to the silicon-based bottom cell. The innovation allows a multi-junction solar cell to be developed without the constraint of lattice matching, and with a low-cost, robust silicon wafer as the supporting bottom substrate and bottom cell. This approach enables a cell that is simultaneously lower in cost, more rugged, and more efficient than existing space-based photovoltaic cells. This high-efficiency solar technology takes advantage of inexpensive silicon wafers and provides a more robust design for next-generation solar cells in space. For terrestrial applications, it can provide unprecedented efficiencies for auxiliary power units in vehicles, solar roof tiles, power plants, and smart grid systems.
The Technology
This NASA Glenn innovation is a novel multi-junction photovoltaic cell constructed using selenium as a bonding material sandwiched between a thin film multi-junction wafer and a silicon substrate wafer, enabling higher efficiencies. A multi-junction photovoltaic cell differs from a single junction cell in that it has multiple sub-cells (p-n junctions) and can convert more of the sun's energy into electricity as the light passes through each layer. To further improve the efficiencies, this cell has three junctions, where the top wafer is made from high solar energy absorbing materials that form a two-junction cell made from the III-V semiconductor family, and the bottom substrate remains as a simple silicon wafer. The selenium interlayer is applied between the top and bottom wafers, then pressure annealed at 221°C (the melting temperature of selenium), then cooled. The selenium interlayer acts as a connective layer between the top cell that absorbs the short-wavelength light and the bottom silicon-based cell that absorbs the longer wavelengths. The three-junction solar cell manufactured using selenium as the transparent interlayer has a higher efficiency, converting more than twice the energy into electricity than traditional cells. To obtain even higher efficiencies of over 40%, both the top and bottom layers can be multi-junction solar cells with the selenium layer sandwiched in between. The resultant high performance multi-junction photovoltaic cell with the selenium interlayer provides more power per unit area while utilizing a low-cost silicon-based substrate. This unprecedented combination of increased efficiency and cost savings has considerable commercial potential.
This is an early-stage technology requiring additional development. Glenn welcomes co-development opportunities.
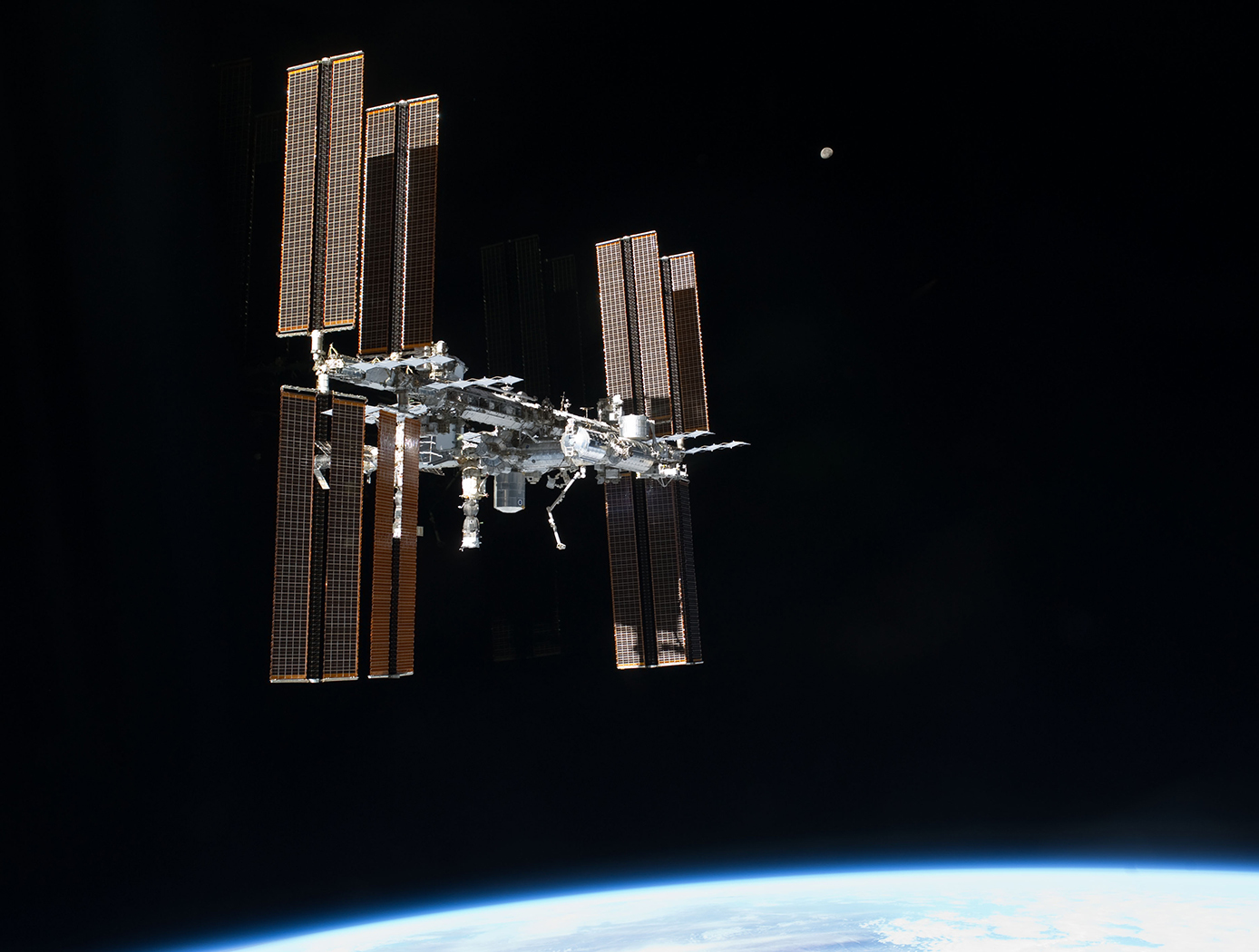
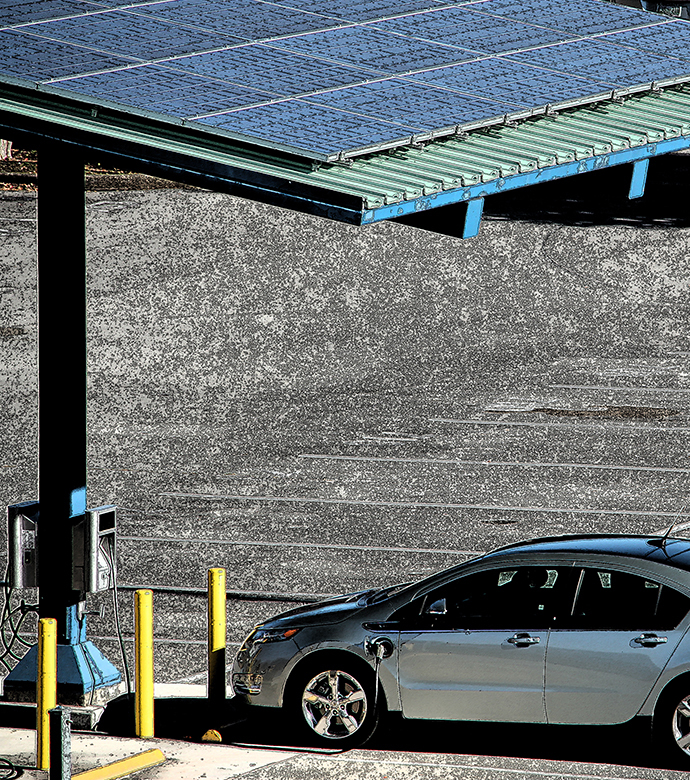
Benefits
- High efficiency: Expected conversion efficiencies of 30% to over 40%
- Low-cost materials: Substrate material is a low-cost silicon wafer as compared to materials used for space-based photovoltaic cells
- Easy to manufacture: Photovoltaic cells can be manufactured on a large scale
- Low environmental impact: Zero greenhouse gasses are emitted
- Robust: The cell features a rugged design for space applications
Applications
- Space-based and military power systems
- Unmanned aerial vehicles
- Satellites
- Solar aircraft
- Auxiliary power units for vehicles
- Electric vehicle charging stations
- PV distributed generation for smart grid systems
- Building-integrated photovoltaics
- Utility-scale PV power plants
- Communications systems
Tags:
|
Similar Results

High Mobility Transport Layer Structures for Rhombohedral Si/Ge/SiGe Devices
Performance of solar cells and other electronic devices such as transistors can be improved greatly if carrier mobility is increased. Si and Ge have Type-II bandgap alignment in cubically strained and relaxed layers. Quantum well and super lattice with Si, Ge, and SiGe have been good noble structures to build high electron mobility layer and high hole mobility layers. However, the atomic lattice constant of Ge is bigger than that of Si and direct epitaxial growth generates large density of misfit dislocations which decrease carrier mobility and shorten device life time. So it required special buffer layers such as super lattice or gradient indexed layers to grow Ge on Si wafers or Si on Ge wafers. The growth of these buffer layers takes extra effort and time such as post-annealing process to remove dislocations by dislocation gliding inside buffer layer.
This invention is a fabrication method for high mobility layer structures of rhombohedrally aligned SiGe on a trigonal substrate. The invention utilizes C-plane (0001) Sapphire which has a triangle plane, and a Si (Ge) (C) (111) crystal or an alloy of group TV semiconductor (111) crystal grown on the Sapphire.

Robotic Assembly of Photovoltaic Arrays
NASA researchers have developed the PAPA technology to increase the efficiency of the thin-film solar array assembly process, significantly decreasing assembly time and labor costs associated with manufacturing large scale solar arrays. Traditional solar cell assembly is a labor intensive, multi-step, time-consuming process. This manual assembly will not be possible in a space environment. To enable solar array assembly in space, PAPA leverages robotic automation to distill the traditional assembly method into four fully automated steps: applying adhesive to block substrate, placing the solar cells using a vacuum tool attached to a universal robotic arm, printing the interconnects and buses to connect the cells, and applying a protective cover.
The PAPA technology is compatible with a variety of thin-film solar cells, including 3D printed cells (essential for future in-space manufacturing of arrays) and terrestrial manufacturing methods. As solar cell technologies mature, PAPA will be able to incorporate advancements into the paneling process. NASA researchers have begun to employ PAPA solar array fabrication and estimate savings of $300-$400/watt. For extraterrestrial assembly of solar panels the size of a football field or larger, PAPA could result in savings of approximately $500 million; a substantial cost savings driven by standardization and efficiency in the solar array assembly process. By demonstrating increases in assembly efficiency, time and cost savings, and passing multiple environmental exposure tests, the PAPA lab protype has completed the final phases of technology development and is ready for scale-up and commercialization.

Advanced Efficiency Flexible Solar Film
By varying the number, type, orientation and functionality of various solar panel materials, a diverse family of devices can be constructed that can be tailored for many operational concepts. Various solar panel designs can be constructed that include active, cooling, and solar absorbance layers with tailored characteristics.
This flexibility is achieved by arranging multiple solar absorbance layers that are coupled to polymer composite solar absorbance layers. The polymer composite can contain metal salts, oxides and/or carbon nanotubes as needed for various applications. The polymer can be chosen for flexibility or stiffness characteristics as needed by the designer.
Configurations can include cooling layers with zinc oxides, indium oxides, and/or carbon nanotubes coupled between active layers. The carbon nanotubes can be aligned in a particular direction of the second cooling layer to achieve a heat flow bias. The cooling layer may be grooved to match other functional layers to increase the surface area for heat transfer.

Single Crystal Semiconductor Silicon-Germanium (SiGe)
Single Crystal SiGe semiconductors are viable via numerous advances patented by NASA. This includes the addition of a 1-2mm ring groove in the magnetron magnets which increases sputtering energy at 500C vs 800C, enabling thicker, faster deposition with better surface finish and consistent quality without heat soaking. The lack of thermal gradient removes inconsistencies in the product. SiGe can also utilize the CMOS manufacturing technique for additional cost savings and waste reduction.
Further decreases to time investment for single crystal SiGe is made possible via reduced thermal load and soak temperatures, growing SiGe semiconductors on, conveniently, less expensive sapphire substrates. Crystal lattice matched growing methods to the sapphire substrate ensure defect-free SiGe production without interfacial dislocations.
A graded indexed SiGe layer can be added to wafers grown in this lattice matched method, permitting thicker semiconductor growth without abrupt changes in strain build-up, carrier potential barrier, index of refraction change and bandgap at the interface. These advances provide improved semiconductor performance and quality with fewer defects in fabrication. The crystal alignment enables X-Ray diffraction identification of any defect location and density.
It is also possible to also grow a Gallium Nitride or Indium Gallium Nitride layer on the opposite side of the Sapphire wafer, useful for solar capable LED display.
A type II band-gap alignment of SiGe would result in highly efficient solar cells – attaining 30% to 40% energy conversion efficiency.
In addition to SiGe, the patented technology also covers these methodologies on tin-based or carbon-based semiconductors.

Optimum Solar Conversion Cell Configurations
A solar cell manufactured from this new optical fiber has photovoltaic (PV) material integrated into the fiber to enable electricity generation from unused light, including non-visible portions of the spectrum and visible light not transmitted to a lighting application. These new solar cells are based around cylindrical optical fibers, providing two distinct advantages over the flat panels that lead to increased efficiency. The core fiber, used to transmit light, can be adjusted to increase or decrease the amount of available light that is transmitted to the lighting application at any point in real time. This invention can be applied wherever optical concentrators are used to collect and redirect incident light. Wavelengths as large as 780 nanometers (nm) can be used to drive the conversion process. This technology has very low operating costs and environmental impacts (in particular, no greenhouse gas emissions). The fiber uses low-cost polymer materials. It is lightweight and flexible, and can be manufactured using low-cost solution processing techniques. Such multifunctional materials have great potential for the future of solar and photovoltaic devices. They will enable new devices that are small and lightweight that can be used without connection to existing electrical grids.