Inexpensive Microsensor Fabrication Process
sensors
Inexpensive Microsensor Fabrication Process (LEW-TOPS-78)
Sensors can be easily fabricated using nanostructures
Overview
Innovators at NASA's Glenn Research Center have developed a simple method of fabricating novel microsensors in large quantities using nanostructures as templates. Existing nanostructures, such as carbon nanotubes or biological structures, have excellent potential for use in sensor systems but lack certain advantages, including the ability to operate at high temperatures. Glenn's novel technique enables the advantageous properties of nanostructures to be combined with more durable materials, such as metal or metal oxides. In this way, the sensor gets the best of both worlds - the nanostructure offers a larger surface area for sensing, and the metal oxide provides durability and high-temperature capability. By fabricating chemical sensors with nanostructured materials at their core, Glenn has made it possible to develop compact, uniquely tailored sensor systems with significantly improved capabilities. These advanced microsensors can be used in a wide variety of critical applications, including fire detection, gas detection, environmental monitoring, and health monitoring.
The Technology
Because chemical sensors are used in many aspects of space missions, NASA researchers are continually developing ever smaller and more robust sensors that can be manufactured inexpensively and in high quantities; e.g., in batches. Glenn has developed a way to inexpensively fabricate microsensors using a sacrificial template approach. A nanostructure, such as a carbon nanotube, serves as a template, which can then be coated with a high-temperature oxide material. The carbon nanotube can be burned off, or sacrificed, leaving only the metal oxide. The resulting structure provides the unique morphology and properties of the carbon nanotube, which are advantageous for sensing, along with the material durability and high-temperature sensing capabilities of the metal oxide. This technique increases the surface area available for sensing because both the interior and exterior of the resulting microsensor can be used for gas detection, significantly increasing performance.
The fabrication of these microsensors includes three major steps: (1) synthesis of the porous metal or metal oxide nanostructures using a sacrificial template, (2) deposition of the electrodes onto alumina substrates, and (3) alignment of the nanostructures between the electrodes. The invention has been demonstrated for methane detection at room temperature (using tin oxide, with carbon nanotubes as the sacrificial template). The microsensor offers low power consumption (no heating required), compact size, extremely low cost, and simple batch-fabrication.
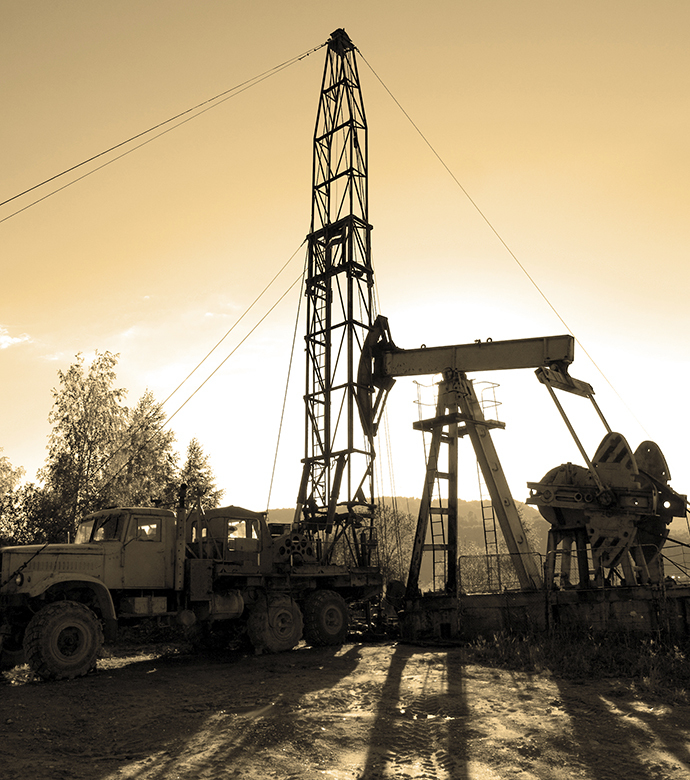
Benefits
- High-performance: Enables the simple fabrication of robust, highly reliable sensors that can be selectively tailored for specific uses
- Proven: Successfully demonstrated as a low-power, compact methane gas sensor (using tin oxide nanorods and carbon nanotubes as templates)
- Affordable: Permits batch fabrication, lowering costs
- Compact: Can be installed in a wide range of locations
Applications
- Environmental monitoring (fire detection, gas detection)
- System monitoring (leak detection)
- Health monitoring
- Oil and gas
- Remote sensing
- Fabrication
- Security
- Nanomaterials
- Composites
Similar Results

Polymer Nanofiber-Based Reversible Nano-Switch/Sensor Schottky Diode Device
Glenn's innovative nanoSSSD device includes a doped semiconducting substrate, an insulating layer deposited on the substrate, an electrode formed on the insulating layer, and at least one polymer nanofiber deposited on the electrode. The deposited nanofiber provides an electrical connection between the electrode and the substrate, serving as the electro-active element in the device. The nanofiber is generally composed of a customized polymer (e.g., polyaniline) that is extremely sensitive to the adsorption and desorption of a single gas molecule. As gas molecules are adsorbed and desorbed, the resistivity of the customized polymer also changes, providing its sensing capacity. When the nanoSSSD device senses a selected gaseous species, the switching portion of the device automatically actuates, sending a signal to the control component. This control component activates the output (warning) device. In addition to its ability to detect harmful gases (including ammonia, hydrogen, hydrocarbons, nitrogen oxides, carbon monoxide, and carbon dioxide), Glenn's device can also feature conducting polymers that are sensitive to UV radiation. Glenn's nanoSSSD technology has great commercial potential, particularly in situations where frequent replacement of the switch/sensor is impractical.

Carbon Dioxide Gas Sensors
Current bulk or thick film solid electrolyte CO2 sensors are expensive, difficult to batch fabricate, and large in size. In contrast, this new amperometric, solid-state, oxide-based electrolyte CO2 microsensor is affordable, easy to fabricate, and is so small that it could easily be integrated onto a substrate the size of a postage stamp.
The basic composition of the sensor is identical to a previously designed NASA Glenn technology in which a solid electrolyte of Na3Zr2Si2PO12 is deposited between interdigitated electrodes on an alumina substrate and is covered by Na2CO3/BaCO3. Unlike its predecessor, however, this innovation includes an additional layer of nanocrystalline SnO2 sol gel, an electron donor type (N-type) semiconductor, on top of the Na2CO3/BaCO3 . This new layer provides a greater number of electrons for reduction reaction at the working electrode to detect CO2. As a result, overall performance is enhanced, and this new state-of-the-art sensor has the ability to operate at temperatures as low as 375°C. This low temperature capability significantly decreases the amount of power required to operate the sensor, opening the door to a multitude of new applications that were previously unattainable.

Polymer Electrolyte-Based Ambient Temperature Oxygen Microsensor
Conventional ambient-temperature oxygen sensors are limited in various ways: optically based sensors can be expensive and challenging to manufacture; electrochemical cells with liquid electrolytes can have limited lifetimes and become leak sources; and both types of sensors are difficult to miniaturize. These problems are addressed with Glenn's novel ambient temperature oxygen microsensor, which is based on a Nafiontm polymer electrolyte, microfabricated using thin-film technologies. In the past, one drawback of Nafiontm film has been that it can lose conductivity when the moisture content in the film is too low, potentially affecting sensor operation. Glenn researchers devised a method to use certain salts to hold water molecules in the Nafiontm film structure at room temperature. The presence of these salts provides extra sites in the film to promote proton (H+) mobility, thus improving film conductivity and overall sensor performance, particularly in arid and high-temperature environments.
The innovative use of metal/metal oxide as the reference electrode enables miniaturization by eliminating the reference gas and sealing the reference electrode. The combination of interdigitized electrodes with the unique metal/metal oxide reference electrode permits sensor operation in either potentiometric or amperometric mode, as appropriate. In potentiometric mode, which measures voltage differences between working and reference electrodes in different gases, the voltage differences can be monitored with a voltmeter; however, the sensor itself does not need a power source. In room-temperature testing, the sensor achieved repeatable responses to 21 percent oxygen in nitrogen (using nitrogen as a baseline gas), and also detected oxygen from 7 to 21 percent, making Glenn's breakthrough technology usable for personal health monitoring as well as fire detection, fuel-leak detection, and environmental monitoring.

Gas Sensors Based on Coated and Doped Carbon Nanotubes
A typical sensor device includes a set of interdigitated microelectrodes fabricated by photolithography on silicon wafer or an electrically insulating substrate. In preparation for fabricating the SWCNT portion of such a sensor, a batch of treated (coated or doped) SWCNTs is dispersed in a solvent. The resulting suspension of SWCNTs is drop-deposited or injected onto the area containing the interdigitated electrodes. As the solvent evaporates, the SWCNTs form a mesh that connects the electrodes. The density of the SWCNTs in the mesh can be changed by varying the concentration of SWCNTs in the suspension and/or the amount of suspension dropped on the electrode area. To enable acquisition of measurements for comparison and to gain orthogonality in the sensor array, undoped SWCNTs can be similarly formed on another, identical set of interdigitated electrodes. Coating materials tested so far include chlorosulfonated polyethylene. Dopants that have been tested include Pd, Pt, Au, Cu and Rh nanoparticle clusters. To date, the sensor has been tested for NO2, NH3, CH4, Cl2, HCl, toluene, benzene, acetone, formaldehyde and nitrotoulene.

NanoWire Glass Switch for Radio Frequency
The nanoionic-based switches developed by NASA's Glenn Research Center exploit the properties of some amorphous materials that can incorporate relatively large amounts of metal and behave as solid electrolytes. As with liquid electrolytes found in lead-acid batteries, for example, solid electrolytes consist of mobile ions which undergo oxidation/reduction reactions at the anode and cathode of the system. The ionic conductivity of such a material can be of the same order of magnitude as the electronic conductivity of a semiconductor but without the drawbacks of an electromechanical device.
In the nanoionic switch, ions are formed at an anode and migrate into the solid electrolyte, while electrons are injected from a cathode, thereby causing the growth of metal nanowires through the electrolyte from the cathode to the corresponding anode when a positive DC bias is applied. Once a nanowire has grown sufficiently to form an electrically conductive path between the electrodes, the switch is closed and no electric power is needed to maintain the connection, unlike in a MEMS or semiconductor-based switch. Moreover, the process of making the connection can easily be reversed by applying a negative bias, causing the wires to ungrow and the switch to open. Thus, NASA's state-of-the-art device is a reversible electrochemical switch that can have geometric features as small as nanometers. The process time for making or breaking the connection is very brief -- about a nanosecond. In addition, this nanoionic material can be deposited in such a way to form multilayer control circuits, which has the potential to minimize circuit footprints, reduce overall circuit losses, and provide unprecedented ease of integration.