Debris-Tolerant Valve
Mechanical and Fluid Systems
Debris-Tolerant Valve (MFS-TOPS-100)
For Use in Environments with Substantial Dust or other Contaminants
Overview
Innovators at NASA's Marshall Space Flight Center (MSFC) have developed a Debris-Tolerant Valve designed for use in machines/environments with a large quantity of airborne dust or other contaminants. The invention was created for an atmospheric revitalization system on the International Space Station. On the ISS, the use of dried pelletized media in the system caused a problem with the collection of contaminants in the existing selector valve, requiring persistent valve maintenance and replacement. NASA's Debris-Tolerant Valve was offered as a solution and is currently being developed for use in future NASA missions. The new valve implements a novel design that has been extensively tested and offers substantial benefits including extended lifetime of internal valve parts, ease of maintenance, and low-cost manufacturability. Applications for the Debris-Tolerant Valve include use in aerospace or industrial processes.
The Technology
NASA's Debris-Tolerant Valve is designed for use in machines/environments with a large quantity of airborne dust or other contaminants. Valves subjected to airborne contaminants tend to have limited lifetime due to damaged seals, bearings, and other internal components. The Debris-Tolerant Valve design addresses this problem with four core improvements over existing commercial valves that are typically used in dusty or debris-laden processes: (1) a new cylinder design that substantially decreases dust collection within the valve; (2) a rotational valve design that minimizes grinding and packing experienced by the standard ball valve; (3) the use of elastomeric seals rather than the Teflon-based seals used in existing valves which are prone to scratching and subsequent leakage; and (4) a bleed port for fluid intake that allows pressure to build slowly in the valve and eliminates the stirring of dust commonly caused by rapid inflow of air in existing valves.
The operational lifetime of NASA's Debris-Tolerant Valve exceeds the lifetime of a standard commercial valve and the existing selector valve used on the ISS by 12X and 6X, respectively. NASA's valve design has fewer parts than existing valves and could be disassembled without tools, enabling easier servicing and maintenance. The Debris-Tolerant Valve is only about one-seventh (1/7) the cost of the existing ISS selector valve.
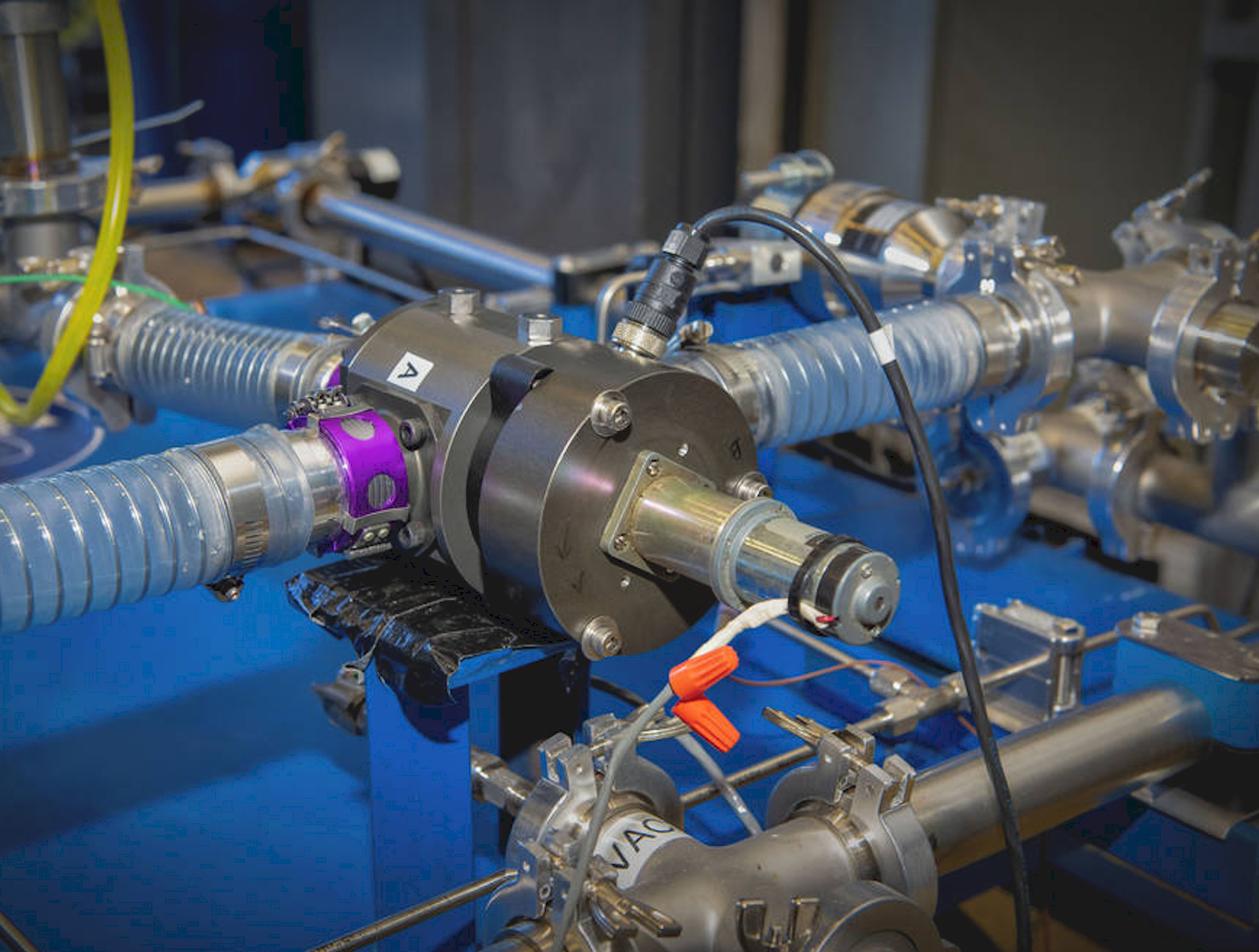

Benefits
- Extended lifetime in dusty environments
- Easier to make and maintain
- Low-cost manufacturability
Applications
- Aerospace components
- Industrial processes
- Systems with desiccants, dryers, catalysts, dry pelletized media, or other dusty/powdery substances
- Swing dryer towers
- Slurry diverters
- Feed mill systems
- Portland cement equipment
Technology Details
Mechanical and Fluid Systems
MFS-TOPS-100
MFS-33708-1
"Marshall Advances Carbon Dioxide Filtration for Deep Space Exploration," October 24, 2018
Tags:
|
|
Related Links:
|
Similar Results

Magnetically Damped Check Valve
NASA's Magnetically Damped Check Valve invention is a damping technology for eliminating chatter in passive valves. Because valve failure in space missions can cause catastrophic failure, NASA sought to create a more reliable check valve damper. The new damper includes the attachment of a magnet to the poppet in a check valve to provide stabilizing forces that optimize flow and pressure conditions. Test results have proven that the Magnetically Damped Check Valve offers substantial benefits.
The Magnetically Damped Check Valve works over a wide range of flow dynamics and eliminated chatter under all flow conditions tested, allowing valves to operate under various flow rates and pressures without a risk of degradation or total destruction from chatter. This technology could provide a more simple and cost-effective solution for valve manufacturers and system designers than solutions currently available in the market.
Applications for the new valve include use in aerospace or industrial processes. NASA's damping technology was originally designed for check valves, but could also benefit pressure regulators, relief valves, shuttle valves, bellows sealed valves or other passive valves.

Wastewater Treatment and Remediation
NASA's system was developed for smaller-scale, space-based applications. However, the technology is scalable for larger industrial and municipal water treatment applications. Implementation of the Ammonia Recovery System could significantly reduce nitrogen content from water treatment processes, meaningfully improving the quality of water. This system offers a novel way to reduce nitrogen water pollutants, while allowing for the nitrogen to be collected and reused- reducing environmental and public health risks and providing an environmentally friendly fertilizer option. NASAs environmental solutions work to sustain life on earth through space based technology
The adaptable nature of this system gives it potentially broad applications in a wide variety of industries; it is particularly ideal for on-site remediation of wastewater in places like condo complexes, hotels and water parks. Current methods of ammonia recovery could not meet NASAs mission requirements, so a new process was devised to optimize for high ammonia selectivity, simplicity, low volume , low power usage and zero contaminants in the effluent. To do this, NASA designed a novel regenerable struvite-formation system for the capture of ammonia. This system has three primary functions:
1) Removal of ammonia from wastewater using a media that is highly selective for ammonia
2) Capture of the ammonia for later use (e.g., as a fertilizer)
3) Regeneration of the capture media for reuse in the system

Filtering Molecules with Nanotube Technology
This water filtration innovation is an acoustically driven molecular sieve embedded with small-diameter carbon nanotubes. First, water enters the device and contacts the filter matrix, which can be made of polymer, ceramic, or metallic compounds. Carbon nanotubes within the matrix allow only water molecules to pass through, leaving behind any larger molecules and contaminants. The unique aspect of the technology is its use of acoustics to help drive water through the filter.
An oscillator circuit attached to the filter matrix propagates acoustic vibration, further causing water molecules to de-bond and move through the filter. This use of acoustics also eliminates dependence on gravity (and thus filter orientation) to move water through the device. When water exiting the system diminishes to a pre-determined set point, a cleaning cycle is triggered to clear the sediment from the inlet of the filter, reestablishing the standard system flow rate. Unlike other filtration systems, flushing of the filter system is not required. The combination of acoustics and small-diameter carbon nanotubes in this innovation make it an effective and efficient means of producing contaminant-free, clean water.

Microwave-Based Water Decontamination System
Bacterial contamination of water systems used in microgravity is a major issue for NASA because biofilms can clog or interfere with water system functions and bacterial ingestion can be harmful to astronaut health. To address this problem, NASA innovators developed a microwave based technology to purify contaminated water by eradicating and eliminating bacteria that grows in systems that generate potable water, in equipment utilizing cooling loops and heat exchangers, and removing bacterial contamination that is present on a variety of surfaces. This decontamination system is chemical free and requires minimal to no consumables.
Initial testing identified a specific microwave frequency band and exposure times for killing bacteria (Burkholderia cepacia) and biofilm. Test results show that exposing static water to microwave energy for 90 seconds can effectively kill waterborne bacteria and biofilm within a water filtration system. Additional testing, using a circulating water test bed, demonstrated that microwave energy at the selected frequency can effectively eradicate waterborne bacteria within 30 seconds. This technology could be further developed into a portable, lightweight system for use in remote locations as well as commercial space applications. The microwave decontamination system could also be added to existing water systems to extend the life of the system.

Modular System for Waste Treatment, Water Recycling, and Resource Recovery
Because resupply of commodities for long duration space missions would be prohibitively expensive and could take an extensive length of time to reach habitats in orbit around or on other planetary bodies, it is critical that astronauts have the ability to recycle and reuse local waste streams to provide resources such as clean water, fuel, and nutrients for growing plants. Scientists at Kennedy Space Center and the University of South Florida have developed a technology that addresses this critical mission need. The modular system design incorporates all wastewater streams and some food waste including urine water, hygiene water, humidity condensate, Sabatier water, fecal waste, laundry water, and organic food waste. These sources are fed simultaneously into the system, and a function-driven, sequential purification process occurs. The primary processes include carbon conversion, phase separation (solid/liquid/gas), disinfection, nutrient/salts management, and salts balancing to generate a clean water stream. The heart of the closed-loop bio-regenerative system is an anaerobic membrane bioreactor (AnMBR), which takes raw wastewater streams and utilizes an anaerobic microbial consortium to carry out the breakdown of the organic matter. An ultrafiltration membrane captures and destroys pathogenic bacteria and viruses. The AnMBR system generates a clean water stream containing fertilizer constituents which can be used to cultivate either microalgae (for food, pharma/nutraceuticals, fuel or bioplastics) in photobioreactors or crops in hydroponic systems. The system also generates methane and hydrogen gas which can be used for fuel (or conversion to bioplastics), and CO2 which can be used to support plant growth.