Search
Electrical and Electronics

Self-Cleaning Seals
This NASA innovation applies the concepts of electrodynamic dust shielding (EDS) to develop seals (e.g., O-rings) with active self-cleaning capabilities. NASA’s self-cleaning seals are manufactured in the following manner: A seal with a conductive surface (or otherwise fabricated to be conductive) is generated and an electrical connection, lead or electrode is attached. Next, a dielectric material is coated or placed over the conductive surface of the seal. (NOTE: Using conductive elastomer materials eliminates the need for a conductive cover layer) A high voltage (nominally >1kV) power supply is connected to the conductive layer on the seal and grounded to the metallic groove or gland that houses the seal.
Given the design, dust accumulates on the outer dielectric layer (a high-voltage insulator) of the seal. To clean the seal, a time varying alternating voltage is applied from the power supply, through the high voltage lead and onto the conductive layer of the seal. When this voltage is applied, the resulting electric field produces Coulomb and dielectrophoretic forces that cause the dust to be repelled from the sealing surface. In practice, NASA’s self-cleaning seals could be operated in continuous cleaning mode (actively repelling dust at all times, preventing it from ever contacting the seal surface) or in a periodic cleaning cycle mode (removing dust from the seal surface at regular intervals).
NASA’s self-cleaning seals have been prototyped and demonstrated to be highly effective at dust removal. The invention could serve as the basis of an active, self-cleaning seal product line marketed for in-space and/or terrestrial applications. Additionally, companies developing space assets destined for operation on dusty planetary surfaces (e.g., the Moon) may be interested in leveraging the technology to protect seals from dust/regolith accumulation, ensuring continuous low leakage operations.
Materials and Coatings

Self-Cleaning Coatings for Space or Earth
The new transparent EDS technology is lighter, easier to manufacture, and operates at a lower voltage than current transparent EDS technologies. The coating combines an optimized electrode pattern with a vapor deposited protective coating of SiO2 on top of the electrodes, which replaces either polymer layers or manually adhered cover glass (see figure on the right). The new technology has been shown to achieve similar performances (i.e., over 90% dust clearing efficiency) to previous technologies while being operated at half the voltage.
The key improvement of the new EDS coating comes from an innovative method to successfully deposit a protective layer of SiO2 that is much thinner than typical cover glass. Using vapor deposition enables the new EDS to scale more successfully than other technologies that may require more manual manufacturing methods. The EDS here has been proven to reduce dust buildup well under vacuum and may be adapted for terrestrial uses where cleaning is done manually. The coatings could provide a significant improvement for dust removal of solar cells in regions (e.g., deserts) where dust buildup is inevitable, but water access is limited. The EDS may also be applicable for any transparent surface that must remain transparent in a harsh or dirty environment.
The related patent is now available to license. Please note that NASA does not manufacturer products itself for commercial sale.
Mechanical and Fluid Systems
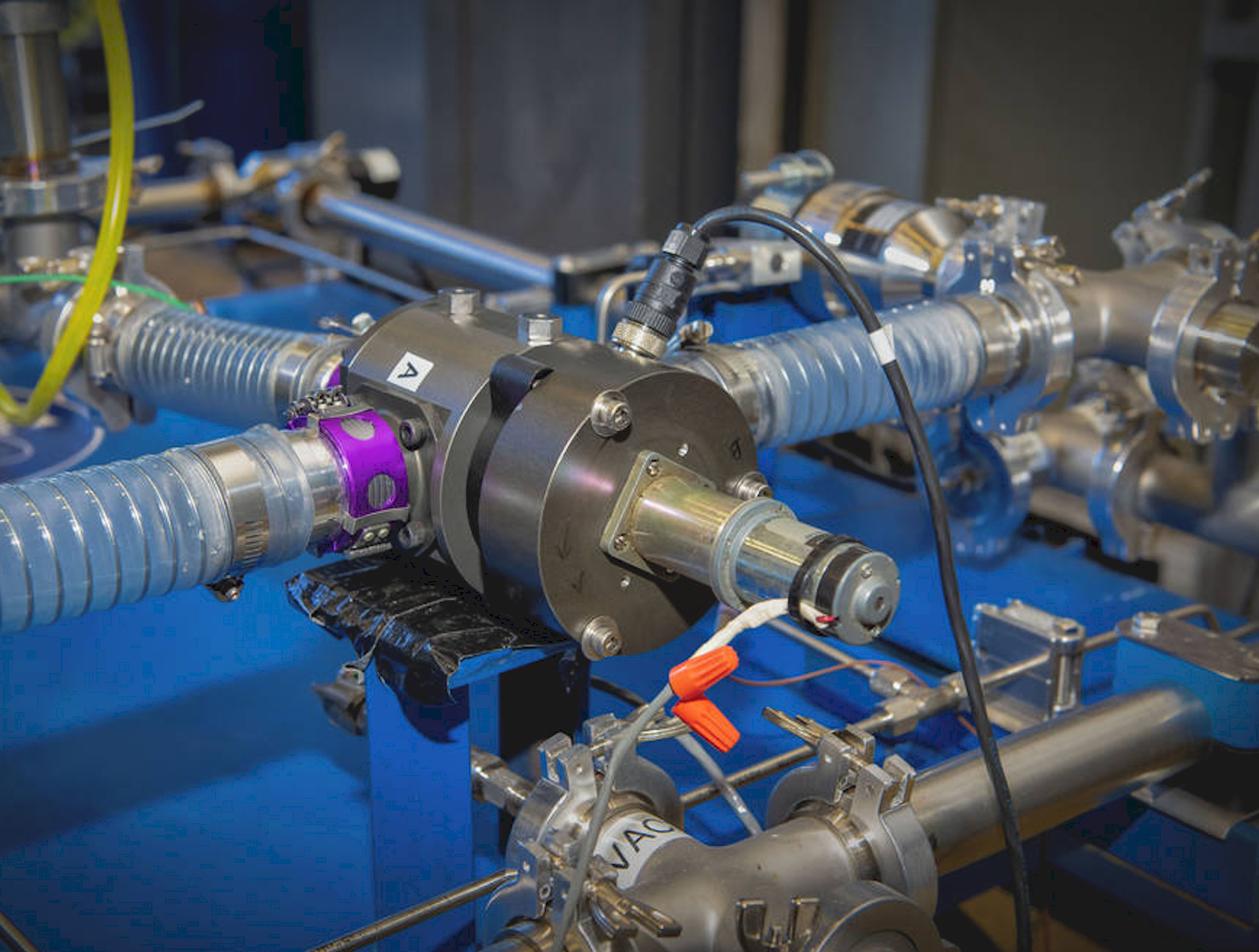
Debris-Tolerant Valve
NASA's Debris-Tolerant Valve is designed for use in machines/environments with a large quantity of airborne dust or other contaminants. Valves subjected to airborne contaminants tend to have limited lifetime due to damaged seals, bearings, and other internal components. The Debris-Tolerant Valve design addresses this problem with four core improvements over existing commercial valves that are typically used in dusty or debris-laden processes: (1) a new cylinder design that substantially decreases dust collection within the valve; (2) a rotational valve design that minimizes grinding and packing experienced by the standard ball valve; (3) the use of elastomeric seals rather than the Teflon-based seals used in existing valves which are prone to scratching and subsequent leakage; and (4) a bleed port for fluid intake that allows pressure to build slowly in the valve and eliminates the stirring of dust commonly caused by rapid inflow of air in existing valves.
The operational lifetime of NASA's Debris-Tolerant Valve exceeds the lifetime of a standard commercial valve and the existing selector valve used on the ISS by 12X and 6X, respectively. NASA's valve design has fewer parts than existing valves and could be disassembled without tools, enabling easier servicing and maintenance. The Debris-Tolerant Valve is only about one-seventh (1/7) the cost of the existing ISS selector valve.
Environment

Carbon Capture Filter
NASA’s Carbon Capture Filter was designed to trap solid carbon dust through a variety of mechanisms. These include inertial separation, flow recirculation, flow tortuosity, media filtration, and quenching of hot particles or of precursor particles from pyrolysis. The filter uses a custom-designed housing to produce a strong and large recirculating pattern to remove dust through inertial forces and confine it into a large collection cup, which is enshrouded in a cold trap (using a thermoelectric cooler) to thermally induce precipitation of the solid carbon. The flow then passes through a single stage baffle and tube filters before exiting through the outlet at the top of the housing.
During operations, gaseous carbon-containing streams enter the filter via an inlet tube at the top of the housing. The inlet tube extends down towards the bottom of the collection cup, where the high-speed stream meets a sudden perpendicular bottom wall, inducing a stagnation flow. Large particles inertially separate from the flow and impinge onto the bottom wall. The partial enclosure of the collection cup (aside from a small slit connecting it to the upper chamber) causes a recirculation bubble to form, increasing the residence time of the stream. The vortical motion of the recirculation bubble causes the large particles to spin outwards towards the walls of the collection cup. The collection cup is cooled to quench the carbon particles, causing them to precipitate out and collect on the walls of the cup. The extended residence time caused by the recirculating flow further quenches the stream. Only small particles that are entrained sufficiently by the flow make it through the slit between the collection cup and upper chamber. On the top wall of the upper chamber, an array of tubular filters collects the remaining particles before the gaseous stream exits the system.
NASA’s Carbon Capture Filter has been prototyped and undergone initial testing with simulant dust, yielding promising results. The invention is available for licensing to industry.