Miniature Bioreactor System for Cell Culture
health medicine and biotechnology
Miniature Bioreactor System for Cell Culture (MSC-TOPS-73)
Automated bench-top cell culturing and sampling system for varied length terms
Overview
Scientists at the NASA Johnson Space Center and the University of Houston have developed a miniature bioreactor system for varied term cell culturing and sampling. The miniature bioreactor allows for continuous and simultaneous short, moderate, or long-term cell culturing of several types of cells and tissues. The invention can be used to study cell cultures and their response to stressors such as pharmaceuticals, hypoxia, pathogens, and more. The bioreactor is ideally suited for periodic cell harvesting and medium processing for secreted cellular components. The miniature bioreactor system has an existing prototype and an initial proof of concept has been completed. The miniature bioreactor system is available for licensing.
This NASA Technology is available for your company to license and develop into a commercial product. NASA does not manufacture products for commercial sale.
The Technology
The miniature bioreactor system was developed to provide the capabilities for NASA to perform cell studies in space and then provide results back to investigators on Earth with minimal tools and cost. The miniature bioreactor system has the potential to also be used on Earth as a laboratory bench-top cell culturing system without the need for expensive equipment and reagents.
The system can be operated under computer control to reduce the operator handling and to reduce result variations. The system includes a bioreactor, a fluid-handling subsystem, a chamber wherein the bioreactor is maintained in a controlled atmosphere and temperature, and control subsystems. The system can be used to culture both anchorage dependent and suspension cells (prokaryotic or eukaryotic cell types). Cells can be cultured for extended periods of time in this system, and samples of cells can be extracted and analyzed at specified intervals. The miniature bioreactor system for cell culturing has applications in pharmaceutical drug screening and cell culture studies.
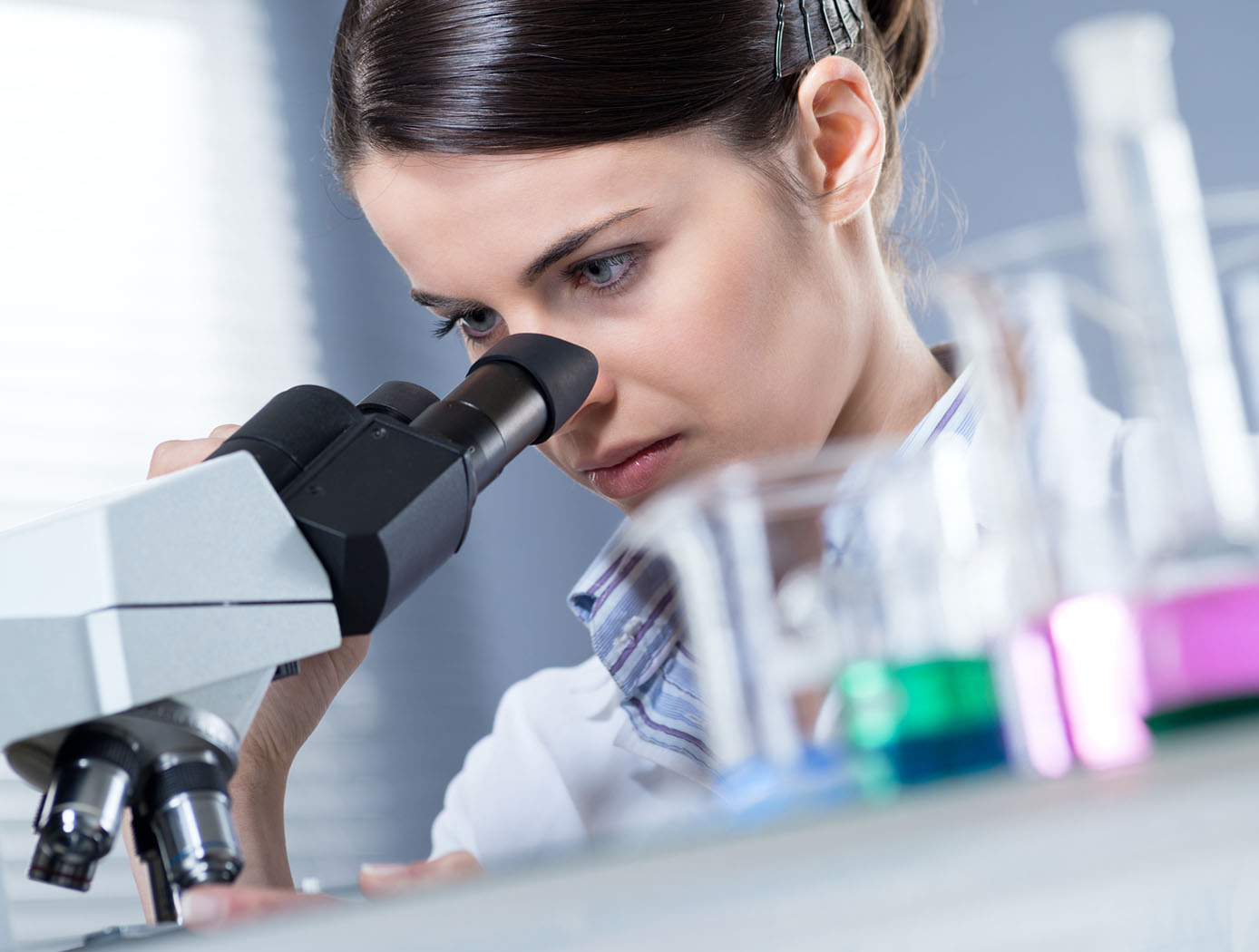

Benefits
- Small and lightweight - miniature bioreactor system
- Automation - computer controlled operation option
- Diverse - suited for studying short, moderate and long term cell culture studies
Applications
- Pharmacokinetic and Pharmacodynamics studies
- Pharmaceutical Drug Screening
- Laboratory Cell Culturing
Similar Results

Micro-Organ Device Mimics Organ Structures for Lab Testing
The MOD platform technology represents a small, lightweight, and reproducible in vitro drug screening model that could inexpensively mimic different mammalian tissues for a multitude of applications. The technology is automated and imposes minimal demands for resources (power, analytes, and fluids). The MOD technology uses titanium isopropoxide to bond a microscale support to a substrate and uses biopatterning and 3D tissue bioprinting on a microfluidic microchip to eliminate variations in local seeding density while minimizing selection pressure. With the MOD, pharmaceutical companies can test more candidates and concentrate on those with more promise therefore, reducing R&D overall cost.
This innovation overcomes major disadvantages of conventional in vitro and in vivo experimentation for purposes of investigating effects of medicines, toxins, and possibly other foreign substances. For example, the MOD platform technology could host life-like miniature assemblies of human cells and the effects observed in tests performed could potentially be extrapolated more readily to humans than could effects observed in conventional in vivo cell cultures, making it possible to reduce or eliminate experimentation on animals.
The automated NASA developed technology with minimal footprint and power requirements, micro-volumes of fluids and waste, high throughput and parallel analyses on the same chip, could advance the research and development for new drugs and materials.

Surface Attached BioReactor (SABR) for Microbial Cell Cultivation
The Surface-Adhering BioReactor (SABR) is a novel microbial cell cultivation platform that mimics the way vascular plants use transpiration to deliver nutrients to their cells. In this biomimetic platform, microbial cells are cultivated as immobilized cells on a porous substrate where transpiration is used to passively deliver water and nutrients as well as harvest and concentrate secreted biomolecules by the microbial cells. The SABR transports nutrients to microorganisms without using a pump. Instead, evaporation and the cohesive property of water are exploited to pull the nutrient medium through the device, with a high degree of control, on an as needed basis. It eliminates the hydrodynamic shear stress on the cells and decreases the working volume of water needed for cultivation by a factor of 25 compared to planktonic bioreactors. Furthermore, the transpiration mechanism allows for the concentration of secreted products in areas of relatively fast evaporation, thus providing a passive means of secreted product harvesting. By matching the time scales of nutrient medium delivery and product harvesting with the time scales of growth and product formation, minimal energy is wasted in bioreactor operation. Transpiration enables a passive cooling system for the cells where either externally imposed or internally generated heat due to cellular activity is mitigated, thus preventing overheating that can lead to decreased productivity or even cell death. This technology enables significant reductions in energy input for cultivating microorganisms.

Portable Slide Staining System for Microscopy
To stain a specimen slide, one or more liquid reagents are injected via the dispenser into the slide staining device via a syringe port. The volume of a given reagent is determined by adjustable settings on the dispenser, so that when connected to the staining device, initiates a thin film over the slide. The dispensing device uses only a fraction of the reagents typically used in non-sealed environments. Medical grade polyvinyl alcohol sponges have been incorporated into the dispenser to provide additional fluid containment and retention during the staining procedure. Furthermore, the dispenser can recall excess reagent, minimizing reagent use until refill.
The slide staining device is composed of an upper and lower section held together and aligned by use of Nd magnets. With the device open, a specimen slide is positioned upon a silicone gasket that sits within a recess in the lower section. When the device is closed, the silicone gasket in the upper section applies a seal to the slide forming a cavity that allows the slide to be exposed to reagents injected from the connected dispenser creating a stain through the use of capillary forces. Although originally designed for use in microgravity, the slide staining system also works in gravity environments.
Numerous applications may exist for this technology, particularly in hematology and cellular biology. Other applications could be considered for academic research, veterinary field use, military, disaster stricken and remote environments or where fine control of fluid delivery, removal, and management is desired.
The slide staining system is at technology readiness level (TRL) 8 (actual system completed and "flight qualified" through test and demonstration), and are now available to license. Please note that NASA does not manufacture products itself for commercial sale.

Portable Microscope
The handheld digital microscope features a 3D-printed chassis to house its hardware, firmware, and rechargeable Li-ion battery with built-in power management. It incorporates an internal stainless-steel cage system to enclose and provide mechanical rigidity for the optics and imaging sensor. To reduce the microscope’s size, yet retain high spatial resolution, engineers devised an optical light path that uniquely folds back on itself using high reflectivity mirrors, thus significantly reducing internal volume.
Imaging control and acquisition is performed using a secure web-based graphical user interface accessible via any wireless enabled device. The microscope serves as its own wireless access point thus obviating the need for a pre-existing network. This web interface enables multiple simultaneous connections and facilitates data sharing with clinicians, scientists, or other personnel as needed. Acquired images can be stored locally on the microscope server or on a removable SD card. Data can be securely downloaded to other devices using a range of industry standard protocols.
Although the handheld digital microscope was originally developed for in-flight medical diagnosis in microgravity applications, prototypes were thoroughly ground-tested in a variety of environments to verify the accurate resolve of microbial samples for identification and compo-sitional analysis for terrestrial field use. Owing to its portability, other applications demanding rapid results may include research, education, veterinarian, military, contagion disaster response, telemedicine, and point-of-care medicine.

3D Construction of Biologically Derived Materials
Once genes for a desired material type, delivery mode, control method and affinity have been chosen, assembling the genetic components and creating the cell lines can be done with well-established synthetic biology techniques. A 3D microdeposition system is used to make a 3D array of these cells in a precise, microstructure pattern and shape.
The engineered cells are suspended in a printable 'ink'. The 3D microdeposition system deposits minute droplets of the cells onto a substrates surface in a designed print pattern. Additional printer passes thicken the material. The cell array is fed nutrients and reagents to activate the engineered genes within the cells to create and deposit the desired molecules. These molecules form the designed new material. If desired, the cells may be removed by flushing. The end product is thus a 3D composite microstructure comprising the novel material.
This innovation provides a fast, controlled production of natural, synthetic, and novel biomaterials with minimum resource overhead and reduced pre- and post-processing requirements.