Search
mechanical and fluid systems
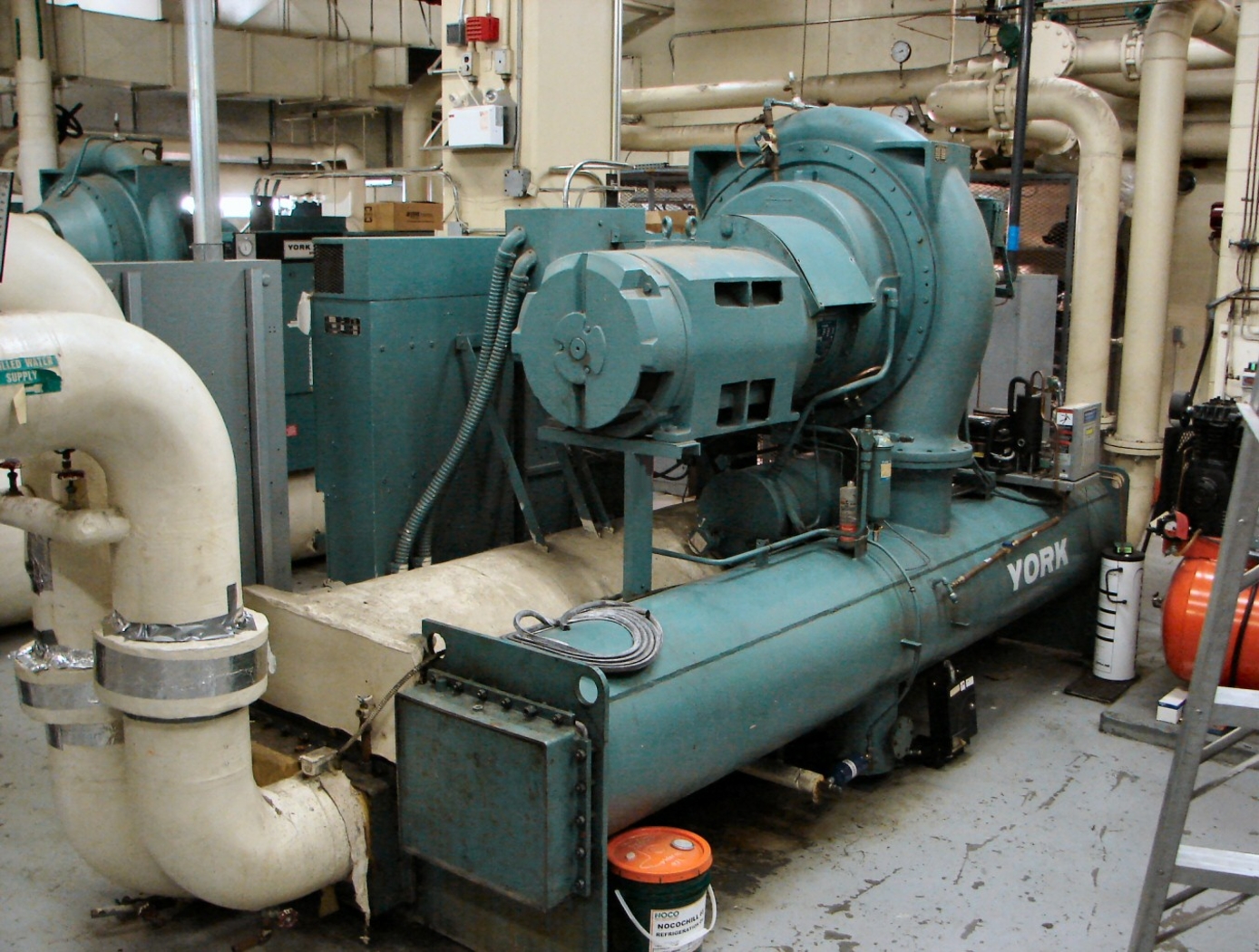
Variable-Aperture Reciprocating Reed (VARR) Valve
The VARR valve has been designed to provide a variable-size aperture that proportionately changes in relation to gas flow demand. When the pressure delta between two chambers is low, the effective aperture cross-sectional area is small, while at high delta pressure the effective aperture cross-sectional area is large. This variable aperture prevents overly restricted gas flow. As shown in the drawing below, gas flow through the VARR valve is not one way. Gas flow can traverse through the device in a back-and-forth reversing flow manner or be used in a single flow direction manner. The contour shapes and spacing can be set to create a linear delta pressure vs. flow rate or other pressure functions not enabled by current standard orifices. Also, the device can be tuned to operate as a flow meter over an extremely large flow range as compared to fixed-orifice meters. As a meter, the device is capable of matching or exceeding the turbine meter ratio of 150:1 without possessing the many mechanical failure modes associated with turbine bearings, blades, and friction, etc.
mechanical and fluid systems
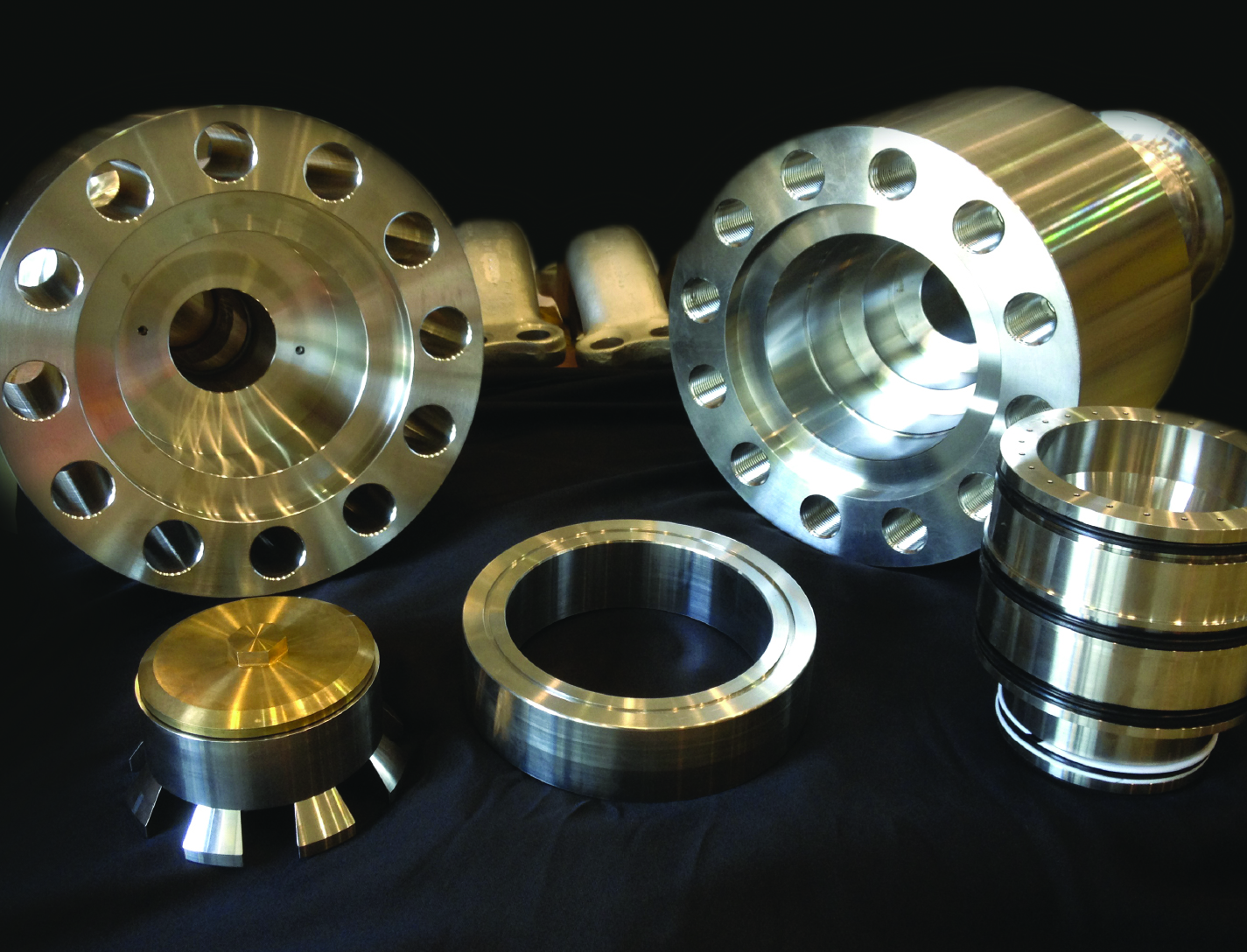
Floating Piston Valve
Instead of looking to improve current valve designs, a new type of valve was conceived that not only addresses recurring failures but could operate at very high pressures and flow rates, while maintaining high reliability and longevity. The valve design is applicable for pressures ranging from 15-15,000+ psi, and incorporates a floating piston design, used for controlling a flow of a pressurized working fluid.
The balanced, floating piston valve design has a wide range of potential applications in all sizes and pressure ranges. The extremely simple design and few parts makes the design inherently reliable, simple to manufacture, and easy to maintain. The valve concept works with soft or hard metal seats, and the closing force is easily adjustable so that any closing force desired can be created. The fact that no adjustment is required in the design, ensures valve performance throughout valve life and operation.
This valve has many unique features and design advantages over conventional valve concepts:
- The largest advantage is the elimination of the valve stem and any conventional actuator, reduces physical size and cost.
- It is constructed with only 5 parts.
- It eliminates the need for many seals, which reduces failure, downtime and maintenance while increasing reliability and seat life.
- The flow path is always axially and radially symmetric, eliminating almost all of the flow induced thrust loads - even during transition from closed to open.
mechanical and fluid systems
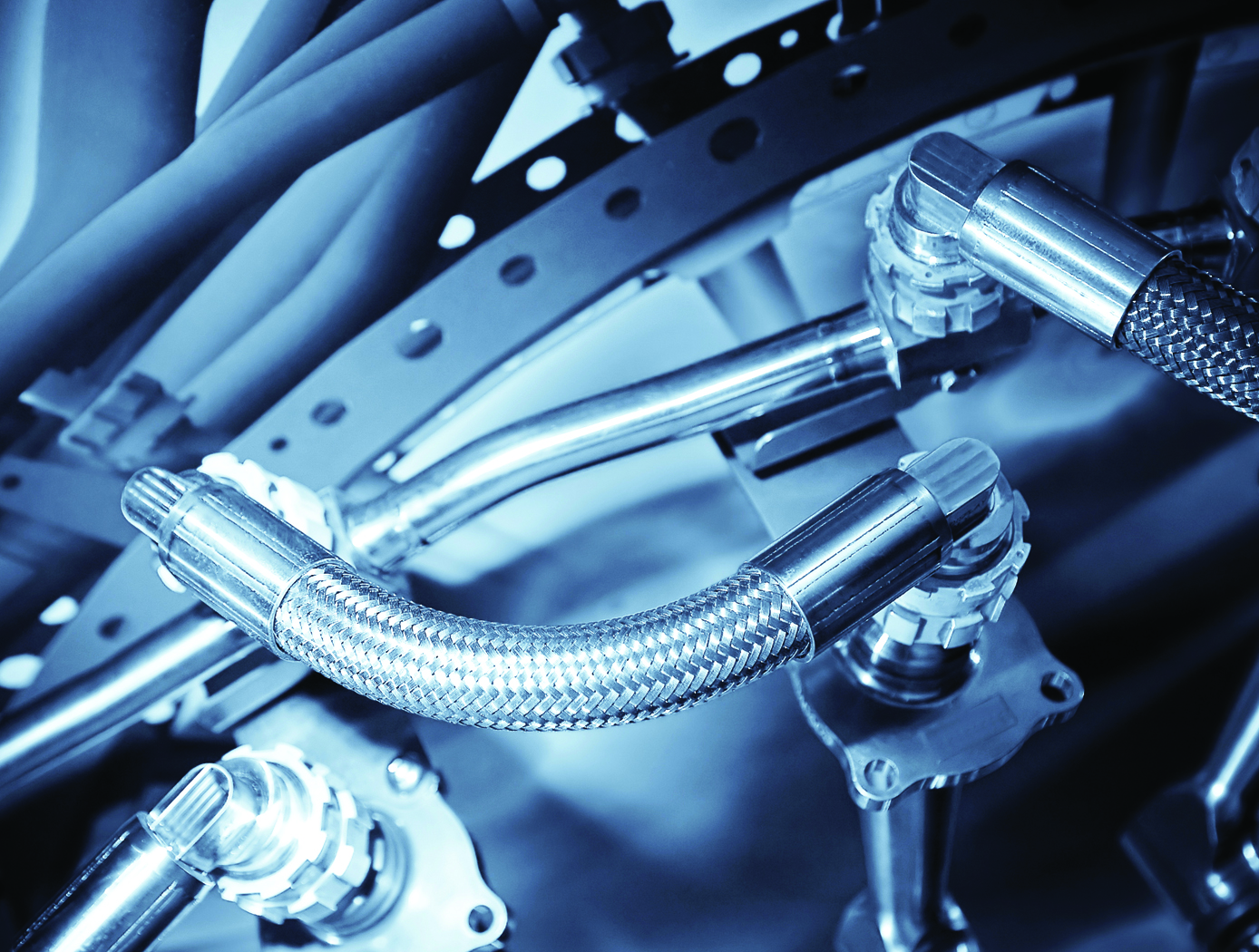
Low-Cost, Long-Lasting Valve Seal
NASA's technique simplifies the seat installation process by requiring less installation equipment, eliminating the need for unnecessary apparatus such as fasteners and retainers. Multiple seals can be installed simultaneously, saving both time and money.
NASA has tested the long-term performance of a solenoid actuated valve with a seat that was fitted using the new installation technique. The valve was fabricated and tested to determine high-cycle and internal leakage performance for an inductive pulsed plasma thruster (IPPT) application for in-space propulsion. The valve demonstrated the capability to throttle the gas flow rate while maintaining low leakage rates of less than
10<sup>-3</sup> standard cubic centimeters per second (sccss) of helium (He) at the beginning of the valves lifetime. The IPPT solenoid actuated valve test successfully reached 1 million cycles with desirable leakage performance, which is beyond traditional solenoid valve applications requirements. Future design iterations can further enhance the valve's life span and performance.
The seat seal installation method is most applicable to small valve instruments that have a small orifice of 0.5 inches or less.