Floating Piston Valve
mechanical and fluid systems
Floating Piston Valve (SSC-TOPS-2)
A Novel Approach to Low Maintenance Actuator-less Valves
Overview
The valve developed consists of a solid piston floating in a medium to control the flow stream. The piston is designed to be axially and radially balanced within the flow stream whether the valve is in the open or closed position. The only force imparted onto the piston is that which the operator chooses to input on to it. The advantages to this design are (1) the elimination of a conventional actuator, which is replaced by one or two simple solenoid valves; (2) elimination of valve actuator adjustments; (3) consistent seating force regardless of the pressure drop across the valve; (4) elimination of the valve stem and stem seals; and (5) elimination of most flow induced thrust forces. Additionally, the valve consists of only five parts with a few simple seals incorporated into a well protected design. The simple design allows for use in nominal or extremely high pressures and for the use of soft or hard metal seats; this valve design reduces downtime and maintenance costs, while increasing valve reliability and seat life.
The Technology
Instead of looking to improve current valve designs, a new type of valve was conceived that not only addresses recurring failures but could operate at very high pressures and flow rates, while maintaining high reliability and longevity. The valve design is applicable for pressures ranging from 15-15,000+ psi, and incorporates a floating piston design, used for controlling a flow of a pressurized working fluid.
The balanced, floating piston valve design has a wide range of potential applications in all sizes and pressure ranges. The extremely simple design and few parts makes the design inherently reliable, simple to manufacture, and easy to maintain. The valve concept works with soft or hard metal seats, and the closing force is easily adjustable so that any closing force desired can be created. The fact that no adjustment is required in the design, ensures valve performance throughout valve life and operation.
This valve has many unique features and design advantages over conventional valve concepts:
- The largest advantage is the elimination of the valve stem and any conventional actuator, reduces physical size and cost.
- It is constructed with only 5 parts.
- It eliminates the need for many seals, which reduces failure, downtime and maintenance while increasing reliability and seat life.
- The flow path is always axially and radially symmetric, eliminating almost all of the flow induced thrust loads - even during transition from closed to open.
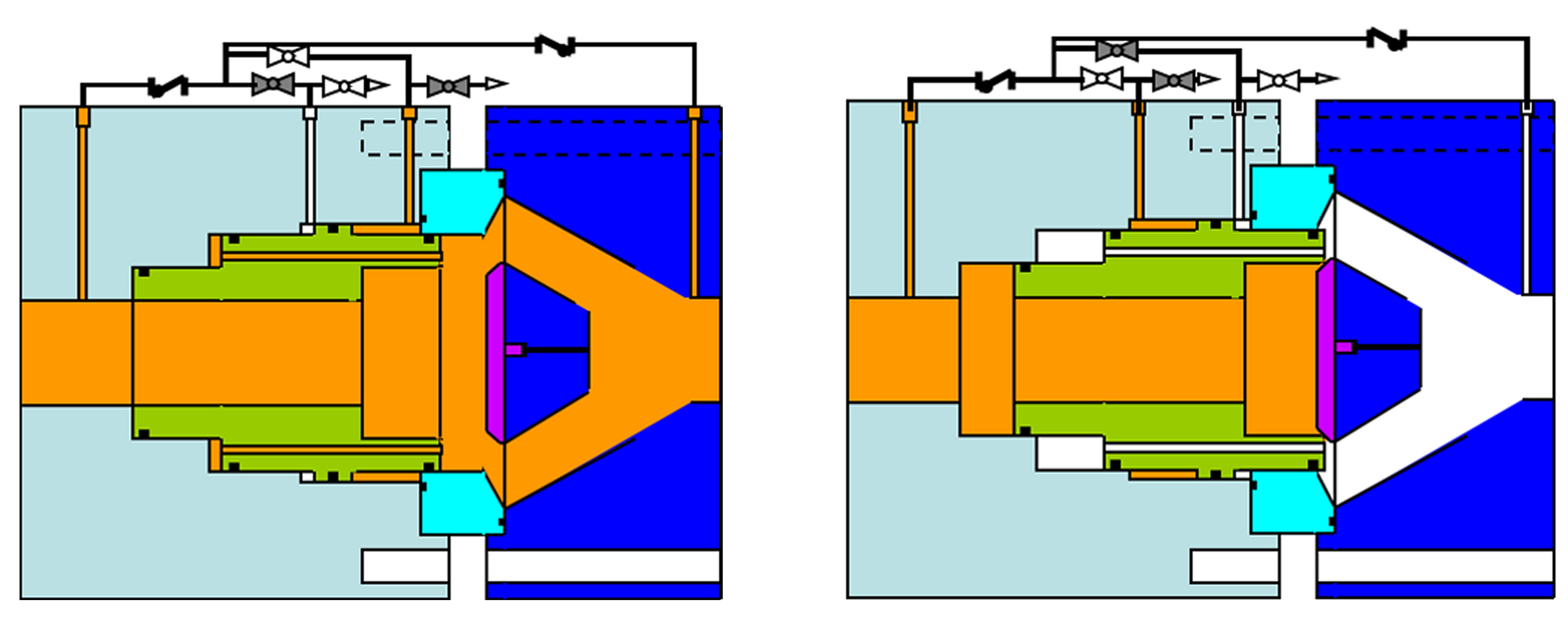
Benefits
- Reduced maintenance due to single design with fewer parts and seals
- Reduced size
- Reduced cost
- No fugitive emissions
- Hermetically sealed and leak-free
- Withstand high pressure
Applications
- Power plants
- Petrochemical plants
- Chemical industry
- Refineries
- Pressurized storage tanks
- Cryogenic fluid systems
- Pharmaceutical manufacturing industry
- Severe duty, extremely high pressure or temperature
- Fast actuation applications
Technology Details
mechanical and fluid systems
SSC-TOPS-2
SSC-00264
Farner, Bruce. "Conical Floating Piston Valve." TechConnect World Innovation Conference & Expo, June 16, 2015, Washington, DC.
Tags:
|
Similar Results

Variable-Aperture Reciprocating Reed (VARR) Valve
The VARR valve has been designed to provide a variable-size aperture that proportionately changes in relation to gas flow demand. When the pressure delta between two chambers is low, the effective aperture cross-sectional area is small, while at high delta pressure the effective aperture cross-sectional area is large. This variable aperture prevents overly restricted gas flow. As shown in the drawing below, gas flow through the VARR valve is not one way. Gas flow can traverse through the device in a back-and-forth reversing flow manner or be used in a single flow direction manner. The contour shapes and spacing can be set to create a linear delta pressure vs. flow rate or other pressure functions not enabled by current standard orifices. Also, the device can be tuned to operate as a flow meter over an extremely large flow range as compared to fixed-orifice meters. As a meter, the device is capable of matching or exceeding the turbine meter ratio of 150:1 without possessing the many mechanical failure modes associated with turbine bearings, blades, and friction, etc.

Magnetically Damped Check Valve
NASA's Magnetically Damped Check Valve invention is a damping technology for eliminating chatter in passive valves. Because valve failure in space missions can cause catastrophic failure, NASA sought to create a more reliable check valve damper. The new damper includes the attachment of a magnet to the poppet in a check valve to provide stabilizing forces that optimize flow and pressure conditions. Test results have proven that the Magnetically Damped Check Valve offers substantial benefits.
The Magnetically Damped Check Valve works over a wide range of flow dynamics and eliminated chatter under all flow conditions tested, allowing valves to operate under various flow rates and pressures without a risk of degradation or total destruction from chatter. This technology could provide a more simple and cost-effective solution for valve manufacturers and system designers than solutions currently available in the market.
Applications for the new valve include use in aerospace or industrial processes. NASA's damping technology was originally designed for check valves, but could also benefit pressure regulators, relief valves, shuttle valves, bellows sealed valves or other passive valves.

Pilot Assisted Check Valve for Low Pressure Applications
Check valves are traditionally designed as a simple poppet/spring system where the spring is designed to equal the force created from the sealing area of the valve seat multiplied by the cracking pressure. Since the valve seat diameter in these types of valves are relatively small, less than 0.5 inches diameter, a low cracking pressure required for back pressure relief devices results in a low spring preload. When sealing in the reverse direction, the typical 20 psid storage pressure of the cryogenic fluid is not enough pressure force to provide adequate sealing stress. To better control the cracking pressure and sealing force, a bellows mechanism was added to a poppet check valve (see Figure 2). The bellows serves as a reference pressure gauge; once the targeted pressure differential is reached, the bellows compresses and snaps the valve open. Prior to reaching the desired crack pressure differential, the bellows diaphragm is fully expanded, providing sufficient seal forces to prevent valve flow (including reverse flow) and undesired internal leakage. Room temperature testing of cracking pressure, full flow pressure, and flow capacity all showed improvements. The overall results of the test proved to be 10-20 times greater than conventional check valves with no internal leakage at three different pressure differentials.

Cryogenic Hydraulically Actuated Isolation Valve
NASA's cryogenic isolation valve technology uses solenoid valves powered by direct current (DC) electrical energy to control and redirect the energy stored in the upstream line pressure. Powering the solenoid valves only requires a DC power source capable of supplying 22 watts that can be distributed and controlled in an on/off manner. By achieving actuation using only upstream line pressure and a 22-watt DC power source, many additional support systems that are required for electromechanical and pneumatic actuation are eliminated. This reduction of parts results in several benefits, including reduced footprint, weight, and potential cost of the valve in addition to lower energy consumption.
NASA fabricated several operational prototype valves using this technology for a rocket company. The table below shows the results of tests performed on these valves under cryogenic conditions. Please contact the NASA MSFC Technology Transfer Office for additional information.

Micro scale electro hydrodynamic (EHD) modular cartridge pump
NASA GSFCs EHD pump uses electric fields to move a dielectric fluid coolant in a thermal loop to dissipate heat generated by electrical components with a low power system. The pump has only a few key components and no moving parts, increasing the simplicity and robustness of the system. In addition, the lightweight pump consumes very little power during operation and is modular in nature. The pump design takes a modular approach to the pumping sections by means of an electrically insulating cartridge casing that houses the high voltage and ground electrodes along with spacers that act as both an insulator and flow channel for the dielectric fluid. The external electrical connections are accomplished by means of commercially available pin and jack assemblies that are configurable for a variety of application interfaces. It can be sized to work with small electric components or lab-on-a-chip devices and multiple pumps can be placed in line for pumping greater distances or used as a feeder system for smaller downstream pumps. All this is done as a one-piece construction consolidating an assembly of 21 components over previous iterations.