Search
electrical and electronics
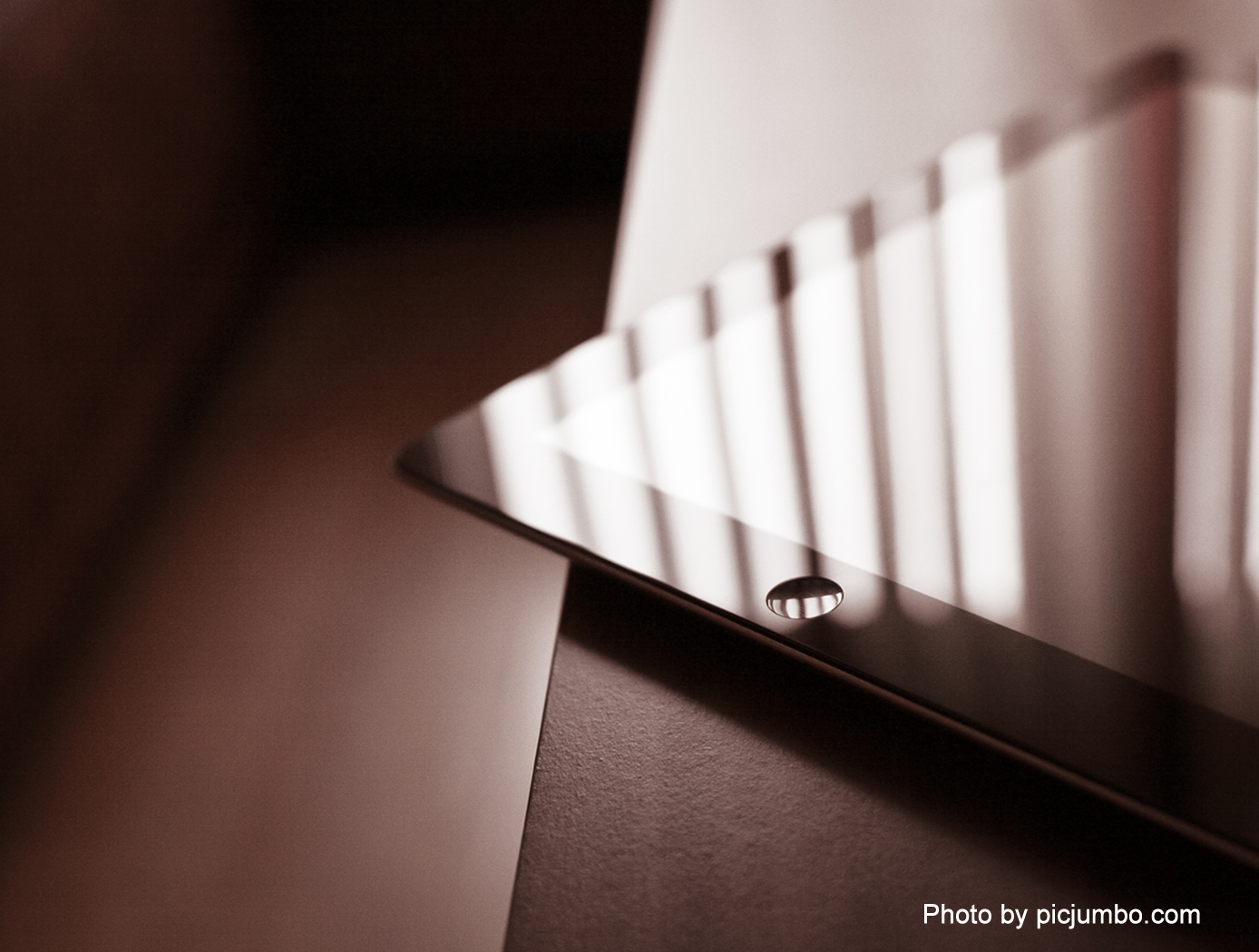
Double Sided Si(Ge)/Sapphire/III-Nitride Hybrid Structures
III-nitride devices are commonly made on sapphire substrates today for various commercial electronic and optoelectronic applications. Thus, this innovation relates directly to the combination of devices on opposite sides of the sapphire substrate. One possible device combination is to have LEDs one side and solar cells on the other, such as for displays.
mechanical and fluid systems
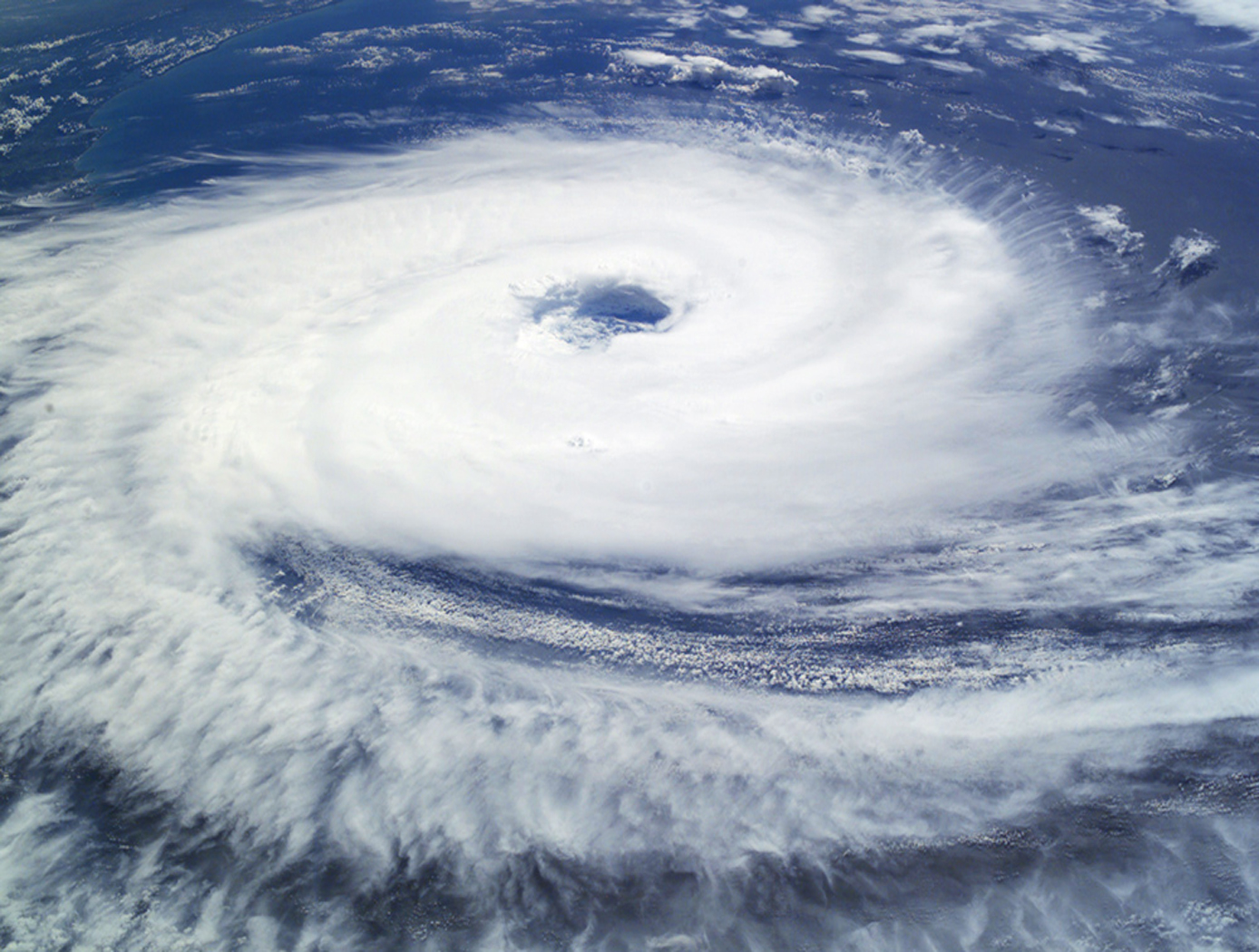
Micro scale electro hydrodynamic (EHD) modular cartridge pump
NASA GSFCs EHD pump uses electric fields to move a dielectric fluid coolant in a thermal loop to dissipate heat generated by electrical components with a low power system. The pump has only a few key components and no moving parts, increasing the simplicity and robustness of the system. In addition, the lightweight pump consumes very little power during operation and is modular in nature. The pump design takes a modular approach to the pumping sections by means of an electrically insulating cartridge casing that houses the high voltage and ground electrodes along with spacers that act as both an insulator and flow channel for the dielectric fluid. The external electrical connections are accomplished by means of commercially available pin and jack assemblies that are configurable for a variety of application interfaces. It can be sized to work with small electric components or lab-on-a-chip devices and multiple pumps can be placed in line for pumping greater distances or used as a feeder system for smaller downstream pumps. All this is done as a one-piece construction consolidating an assembly of 21 components over previous iterations.
Electrical and Electronics

Passive PCB-Mounted Thermal Switch
NASA’s Passive PCB-Mounted Thermal Switch uses a heat pipe that extends from the electronics enclosure wall to the center of the electronics board. The switch includes a wax actuator that extends when warm. The extending piston on the actuator pushes the heat pipe against the anvil of the mechanism, which then provides a low-resistance heat path to the wall of the enclosure. When the wax actuator drops below a certain temperature, the piston retracts. A spring then pushes the heat pipe away from the anvil, breaking thermal contact and conserving heat. A series of insulating materials is used to reduce unwanted heat transfer through the springs. The mechanism is mounted to the board with a thermal interface material and screws to provide high contact pressure and thermal conductivity between the board and the mechanism. Additional heat straps are used to carry heat directly from particularly hot components.
A key advantage of this NASA invention is that it does not require any energy input for operations (i.e., it is completely passive). In spaceflight applications, this enables significant mass savings as heaters can represent up to 50% of electronics systems’ power consumption. Given that typical battery chemistries stop functioning at approximately 0C, additional power is required to keep the batteries themselves warm. Thus, reducing heater power requirements by 50% could reduce overall energy storage requirements by approximately 70% – leaving more capacity for sensors, fuel, or other priorities.
NASA’s switch is particularly useful for spaceflight applications where electronics are exposed to long bouts of extreme heat and cold, such as on the Moon (where the day-night cycle lasts 14 days with nighttime lows near -173C and daytime highs near 127C), or in deep space. Lunar landers and lunar infrastructure developers might be ideal end-users of the invention. Other applications where electronics experience extreme temperatures may benefit from this NASA innovation.
mechanical and fluid systems
Feedthrough for Severe Environments and Temperatures
Space and ground launch support related hardware often operate under extreme pressure, temperature, and corrosive conditions. When dealing with this type of equipment, it is frequently necessary to run wiring, tubes, or fibers through a barrier separating one process from another with one or both operating in extreme environments. Feedthroughs used to route the wiring, tubes, or fibers through these barriers must meet stringent sealing and leak tightness requirements.
This affordable NASA feedthrough meets or exceeds all sealing and leak requirements utilizing easy-to-assemble commercial-off-the-shelf hardware with no special tooling. The feedthrough is a fully reconfigurable design; however, it can also be produced as a permanent device. Thermal cycling and helium mass spectrometer leak testing under extreme conditions of full cryogenic temperatures and high vacuum have proven the sealing capability of this feedthrough with or without potting (epoxy fill) on the ends. Packing material disks used in the construction of the device can be replaced as needed for rebuilding a given feedthrough for another job or a different set of feeds if potting is not used for the original feedthrough build. (Potting on one or both sides of the sleeve provides double or triple leak sealing protection). Variable Compression Ratio (VCR) connectors were adapted for the pressure seal on the feedthrough; however, any commercial connector can be similarly adapted. The design can easily be scaled up to larger (2" diameter) and even very large (12" or more) sizes.
power generation and storage
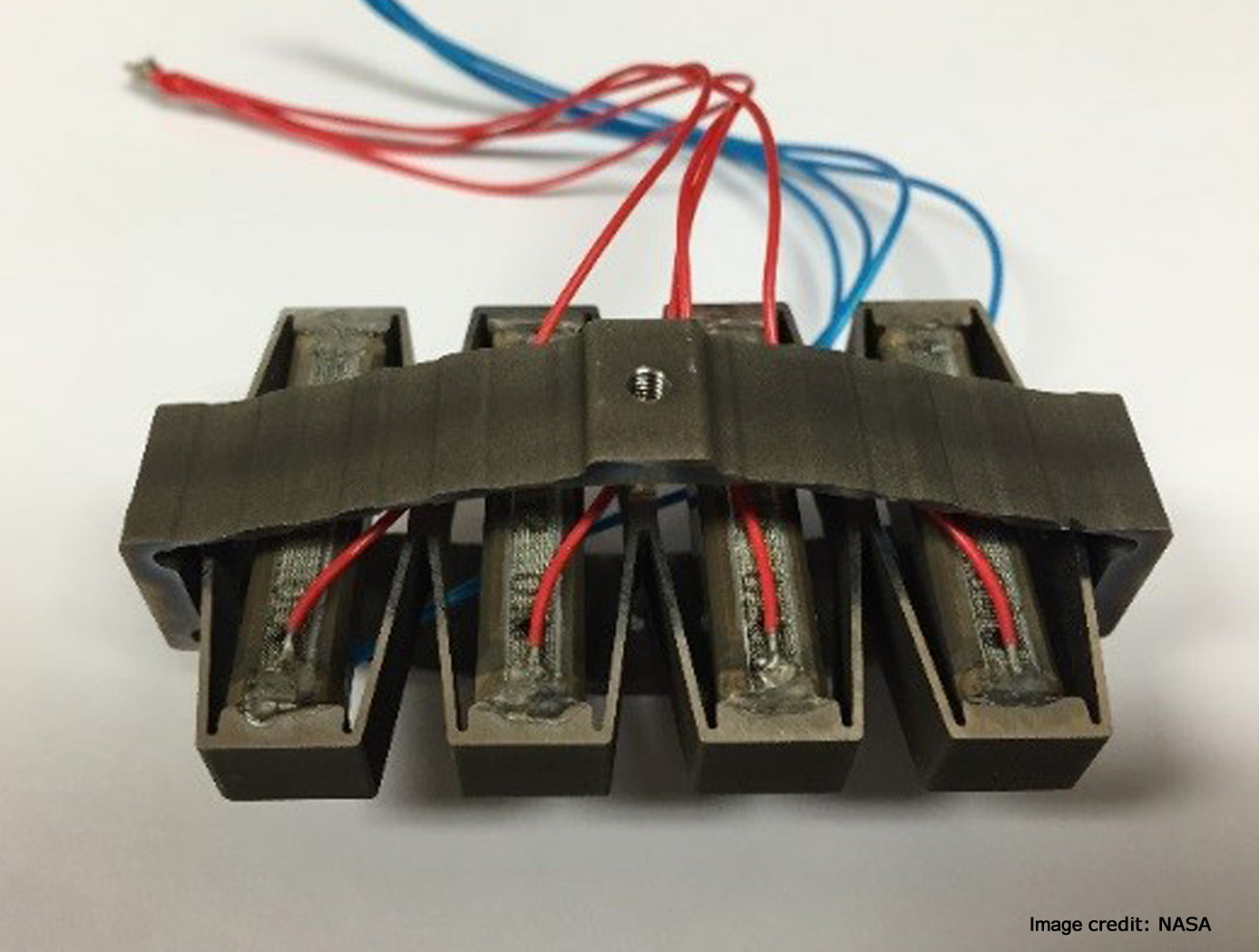
Relaxor Piezoelectric Single Crystal Multilayer Stacks for Energy Harvesting Transducers (RPSEHT)
Energy management is one of the most challenging issues in the world today. Accordingly, various energy harvesting technologies have gained attention, including harvesting energy from ambient vibration sources using piezoelectric materials. However, conventional piezoelectric energy harvesting transducer (PEHT) structures have effective piezoelectric constants that are lower than about 10^4 pC/N, (resonant mode). These low piezoelectric constants lead to conventional PEHTs not being able to harvest electric power effectively. Further, for a specific vibration/motion source, it would be advantageous to maximize the mechanical energy captured from the vibration structure into the piezoelectric device and to convert a greater fraction of that mechanical energy into electrical energy more efficiently.
This invention is a system and method using multistage force amplification of piezoelectric energy harvesting transducers (MFAPEHTs) to increase the effective piezoelectric constant to >10^6 pC/N and to increase the mechanical energy input to the device. The invention utilizes 33 mode PZT to permit maximum coupling between the input mechanical energy with the piezoelectric material, and multilayer construction of single crystal PMN-PT material to significantly amplify the voltage/charge generation and storage from the applied mechanical force.
aerospace

Improved Ground Collision Avoidance System
This critical safety tool can be used for a wider variety of aircraft, including general aviation, helicopters, and unmanned aerial vehicles (UAVs) while also improving performance in the fighter aircraft currently using this type of system.
<strong>Demonstrations/Testing</strong>
This improved approach to ground collision avoidance has been demonstrated on both small UAVs and a Cirrus SR22 while running the technology on a mobile device. These tests were performed to the prove feasibility of the app-based implementation of this technology. The testing also characterized the flight dynamics of the avoidance maneuvers for each platform, evaluated collision avoidance protection, and analyzed nuisance potential (i.e., the tendency to issue false warnings when the pilot does not consider ground impact to be imminent).
<strong>Armstrong's Work Toward an Automated Collision Avoidance System</strong>
Controlled flight into terrain (CFIT) remains a leading cause of fatalities in aviation, resulting in roughly 100 deaths each year in the United States alone. Although warning systems have virtually eliminated CFIT for large commercial air carriers, the problem still remains for fighter aircraft, helicopters, and GAA.
Innovations developed at NASAs Armstrong Flight Research Center are laying the foundation for a collision avoidance system that would automatically take control of an aircraft that is in danger of crashing into the ground and fly it—and the people inside—to safety. The technology relies on a navigation system to position the aircraft over a digital terrain elevation data base, algorithms to determine the potential and imminence of a collision, and an autopilot to avoid the potential collision. The system is designed not only to provide nuisance-free warnings to the pilot but also to take over when a pilot is disoriented or unable to control the aircraft.
The payoff from implementing the system, designed to operate with minimal modifications on a variety of aircraft, including military jets, UAVs, and GAA, could be billions of dollars and hundreds of lives and aircraft saved. Furthermore, the technology has the potential to be applied beyond aviation and could be adapted for use in any vehicle that has to avoid a collision threat, including aerospace satellites, automobiles, scientific research vehicles, and marine charting systems.
communications
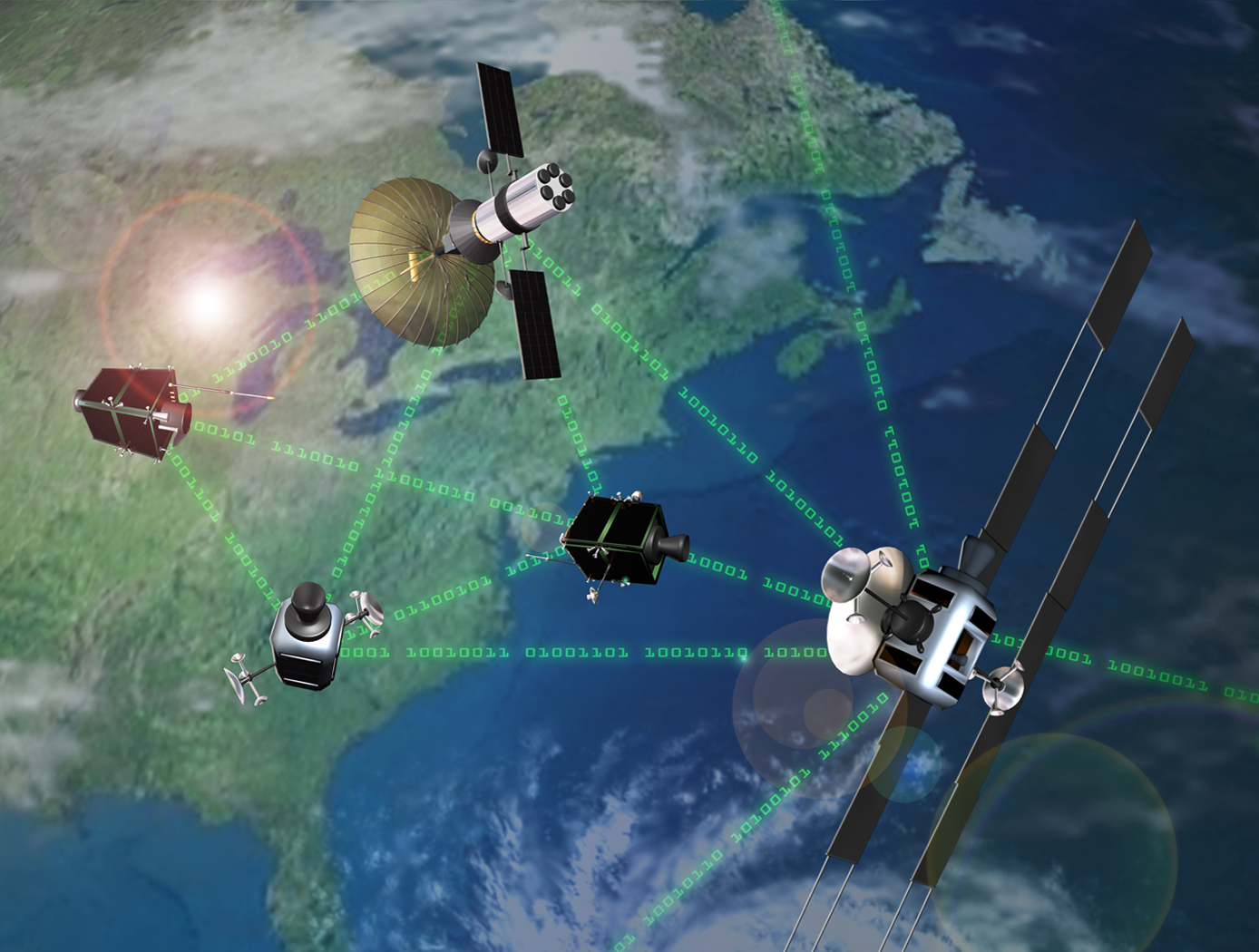
Heterogeneous Spacecraft Networks
Heterogeneous Spacecraft Networks address an emerging need, namely, the ability of satellites and other space-based assets to freely communicate with each other. While it appears that there has been no significant effort to date to address the application, emergence of such a solution is inevitable, given the rapidly-growing deployments of small satellites. These assets need to be able to communicate with each other and with global participants. Extending established global wireless network platforms like Wi-Fi and ZigBee to space-based assets will allow different satellite clusters to assist each other. For example, one cluster could provide images of the earths surface when another cluster is with out visibility at the needed time and location. More importantly, use of such common platforms will enable collaboration among individuals, institutions, and countries, each with limited assets of its own. Thus, allowing the incorporation of space-based assets into commercial wireless networks, and extending commercial communications into low Earth orbit satellites, access to satellite data will become ubiquitous.Similarly, some global networks will also benefit from the ability of a variety of nodes of different types to communicate with each other. One instance is in the emerging Internet of Things (IoT), where an enormous number of smart objects work together to provide customized solutions.
Aerospace
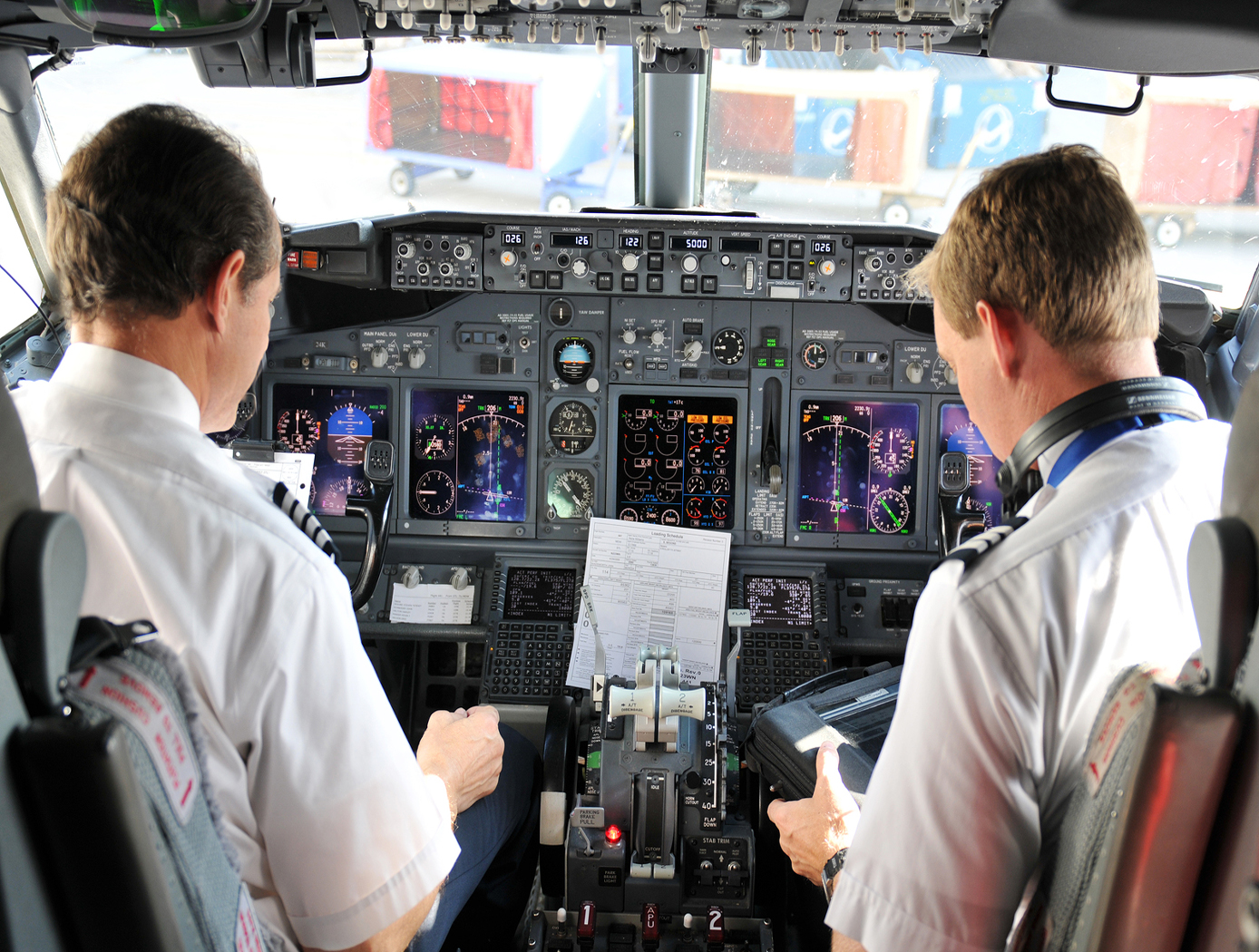
Foot Pedal Controller
The Foot Pedal Controller enables an operator of a spacecraft, aircraft, or watercraft, or a simulation of one in a video game, to control all translational and rotational movement using two foot pedals. This novel technology allows control across all six degrees of freedom, unlike any technology on the market. The components of the technology are a support structure, a left foot pedal, a right foot pedal, and supporting electronics. The Foot Pedal Controller is intuitive, easy to learn, and has ergonomic features that accommodate and stabilize the operator's feet. A working prototype is available to demonstrate key technology features to potential licensees.
The Foot Pedal Controller technology could be used in designs for the flight deck of the future, video game controls, drone operations and flight simulators. This technology can be useful in any application where it is preferred or desirable to use the feet to control motion rather than using the hands. A potential market could be foot control of equipment by people with arm or hand disabilities. A unique aspect of the innovation is the consideration of natural foot mechanics in the design and placement of the sensors and actuators to reduce operator fatigue. The axes of rotation of the Controller align with the joints of the foot so the foot moves naturally to control the movement of the craft. NASA seeks collaborations with companies interested in licensing and partnering to further develop and commercialize the technology.
materials and coatings
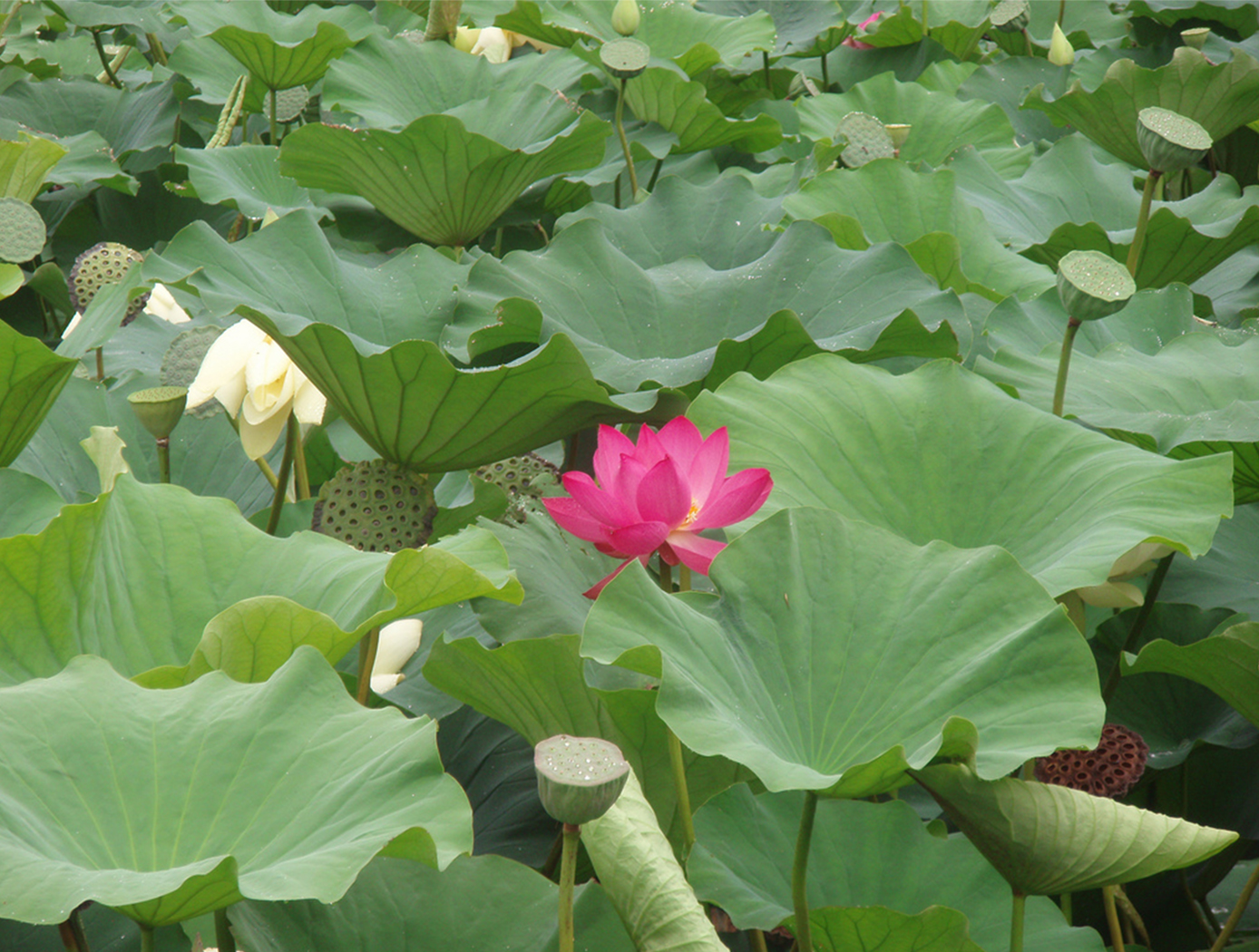
Lotus Coating
This durable, transparent, nano-textured coating can be applied via a wet chemistry process to variety of rigid and flexible surfaces by spin coating, brush application, or spray application, making it applicable for many purposes beyond space flight and aeronautical applications. The coatings unique nano-textured surface and overcoat reduces surface energy and contact surface area, giving the coating anti-contamination and self cleaning properties that minimize dust, liquid, and ice accumulation on its surface, similar to a leaf on the Lotus plant. The coating is low outgassing, stable in vacuum, and can survive harsh spaceflight environments. Depending on requirements, the Lotus Coating can be tailored to fit the specific needs of a project or customer. This customization makes the Lotus system far more adaptive, allowing for a more diverse range of applications.
manufacturing
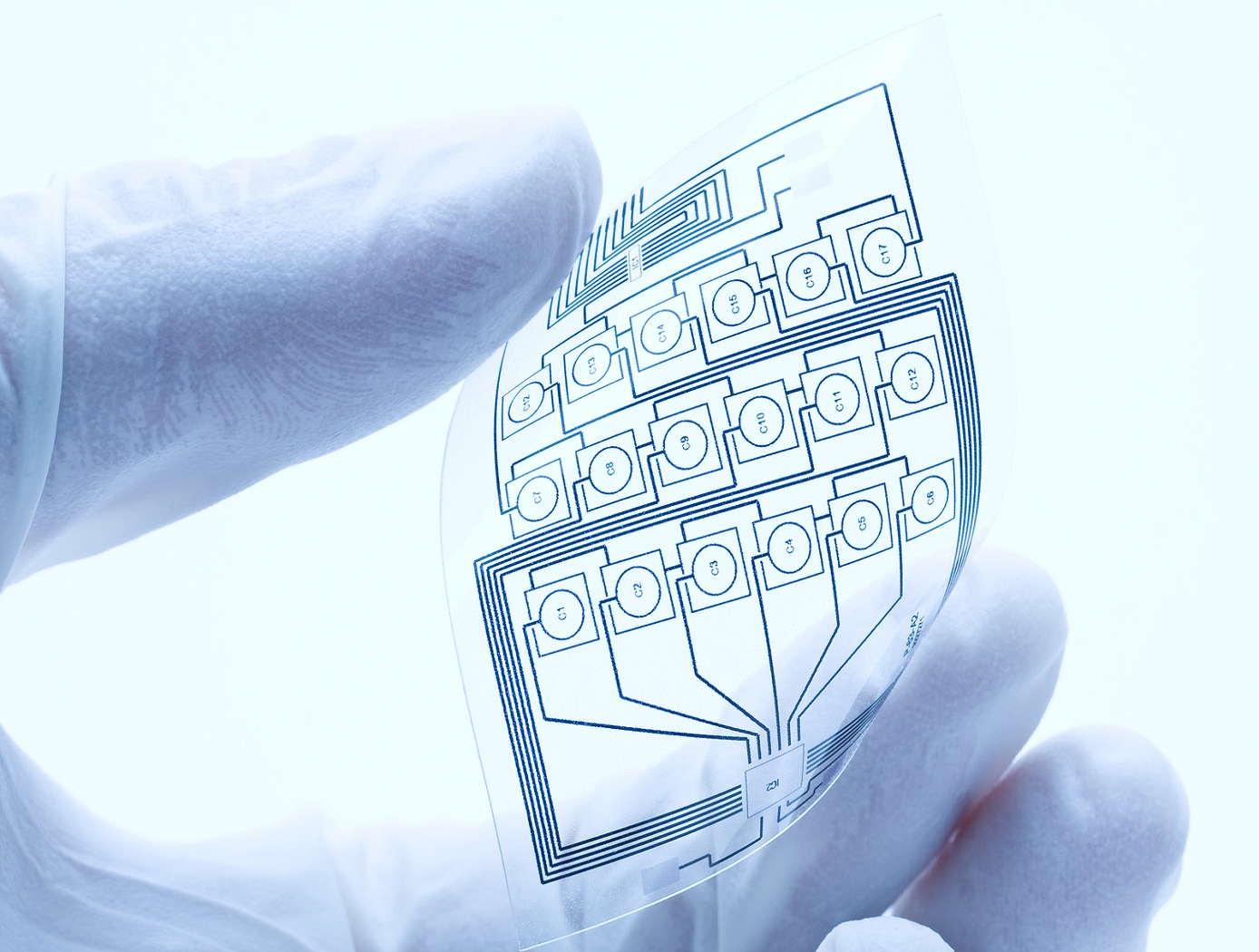
Fabricating printable electronics and biosensor chips
The plasma system consists of a glass tube with a diameter of 0.5 mm or larger, if desired. The electrodes are separated by 10 mm. Helium, argon or cold dry air can be used as a plasma gas source. An applied high voltage between the electrodes causes the gas to breakdown within the central core of the glass capillary generating atmospheric plasma. Nanostructures colloids/organic/inorganic precursors are placed in a glass container with an inlet and outlet for carrier gas and are seated on an ultrasonic nebuliser. The aerosol is then carried into the plasma stream by the carrier gas and is deposited.
The atmospheric plasma deposition system can be modified for depositing multiple materials, either simultaneously or sequentially, and for high-throughput processing by having multiple jets. Each capillary can either be connected to the container containing a single precursor material or to different containers containing different precursor materials to facilitate multiple depositions. The multi-jet plasma system can be automated and controlled individually to precisely control surface characteristics. This technique is independent of the chosen substrate, and has proven to work for many substrates, including paper, plastic, semiconductors and metals.