Search
power generation and storage
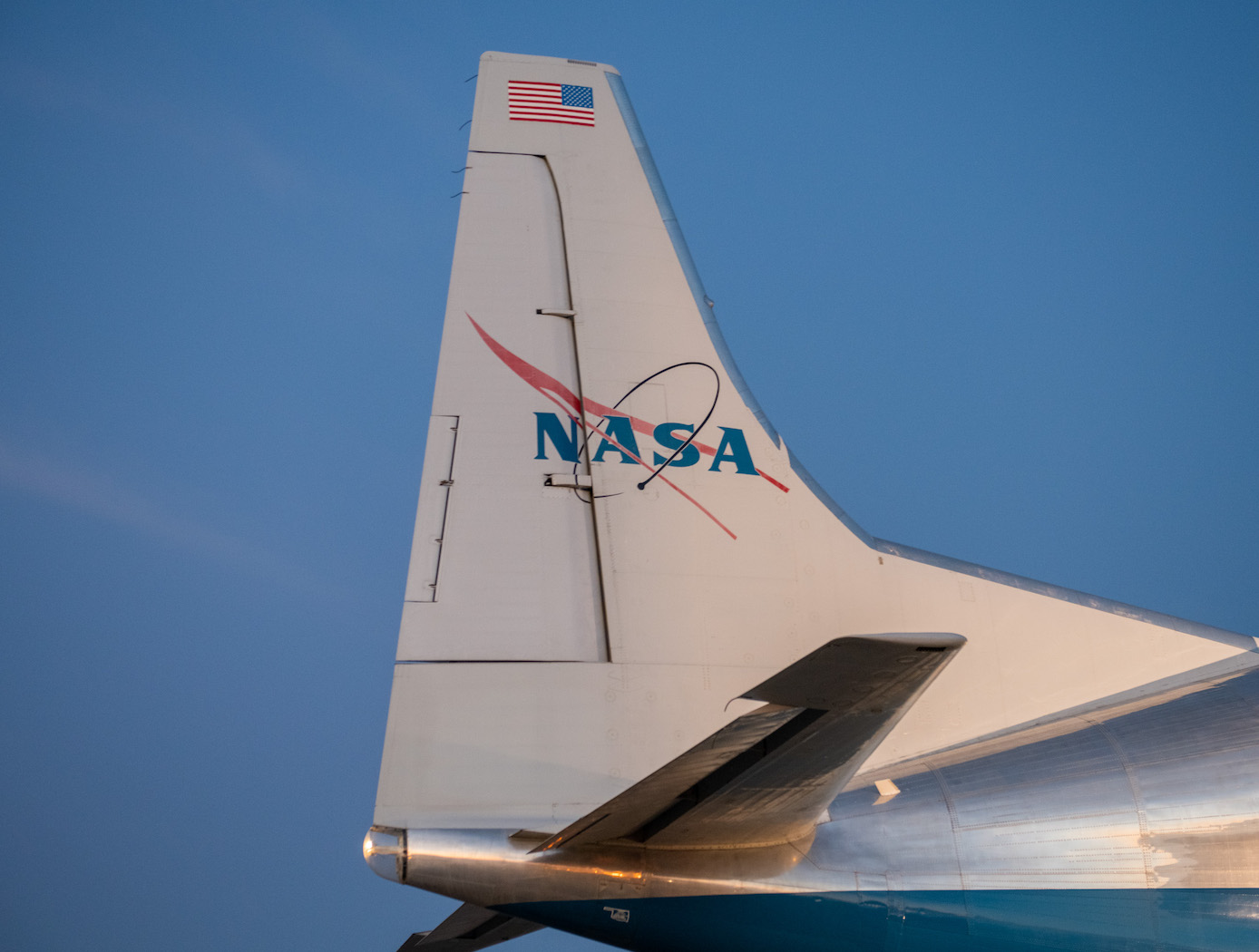
High Efficiency Megawatt Motor
The HEMM is a is a wound-field partially superconducting machine that implements a combination of rotor superconducting and stator normal conductor elements, along with an integrated acoustic cryocooler, to achieve some of the benefits of a superconducting motor without the need for an external cryogenic system. The combination of the described elements allows a motor to be built which essentially operates like any other motor when viewed as a black box, but substantially enhanced performance can be achieved. The incorporation of superconductors on the rotor to create a high-level magnetic field results in a specific power and efficiency that could not be achieved any other way. The HEMM can achieve over 98% efficiency in a lightweight electric machine with an operating power greater than 1.4 MW, a specific power greater than 16 kW/kg (ratio to electromagnetic mass), and a rated operating speed of 6800 RPM. The HEMM can be used as both a motor or a generator, offering a wide range of applications including propulsion systems for hybrid aircraft, electric trains, hybrid cars, and turboelectric ships, as well as generator systems for wind turbines, power plants, or motors for other industrial machinery.
Power Generation and Storage

Next Generation “Closed Strayton” Engine Design
The core “Strayton” generator technology consists of a gas turbine engine with short, axial pistons installed inside the hollow turbine shaft. These pistons form a Stirling engine that cycles via thermo-acoustic waves, transferring heat from the turbine blades to the compressor stage, which improves overall engine performance. Power to an alternator is, thus, delivered from both turbine shaft rotation and the oscillation of the internal pistons.
This synergistic relationship is markedly enhanced in a closed-cycle system, where the sealed turbine engine recirculates a working fluid heated via an external source, such as a hydrogen fuel cell and combustor. This system supports higher compression ratios, reduces the turbine diameter to less than 4”, and eliminates the need for large recuperators. Operational efficiency is projected to extend into the low temperature range (750° C), reducing the need for advanced materials and providing cleaner combustion for hydrogen-based applications. Pressurized, inert working fluids also replace mechanical bearings and gearboxes, enabling years of maintenance-free operation.
The fuel cell and Stirling cycle produce 10% of the total system energy, while the Brayton cycle produces 90%. Other external heat sources could include nuclear, solar, or biogas. Conservative estimates for the hydrogen fuel-cell configuration lifetime are in the 100,000 hour range.