Search
propulsion
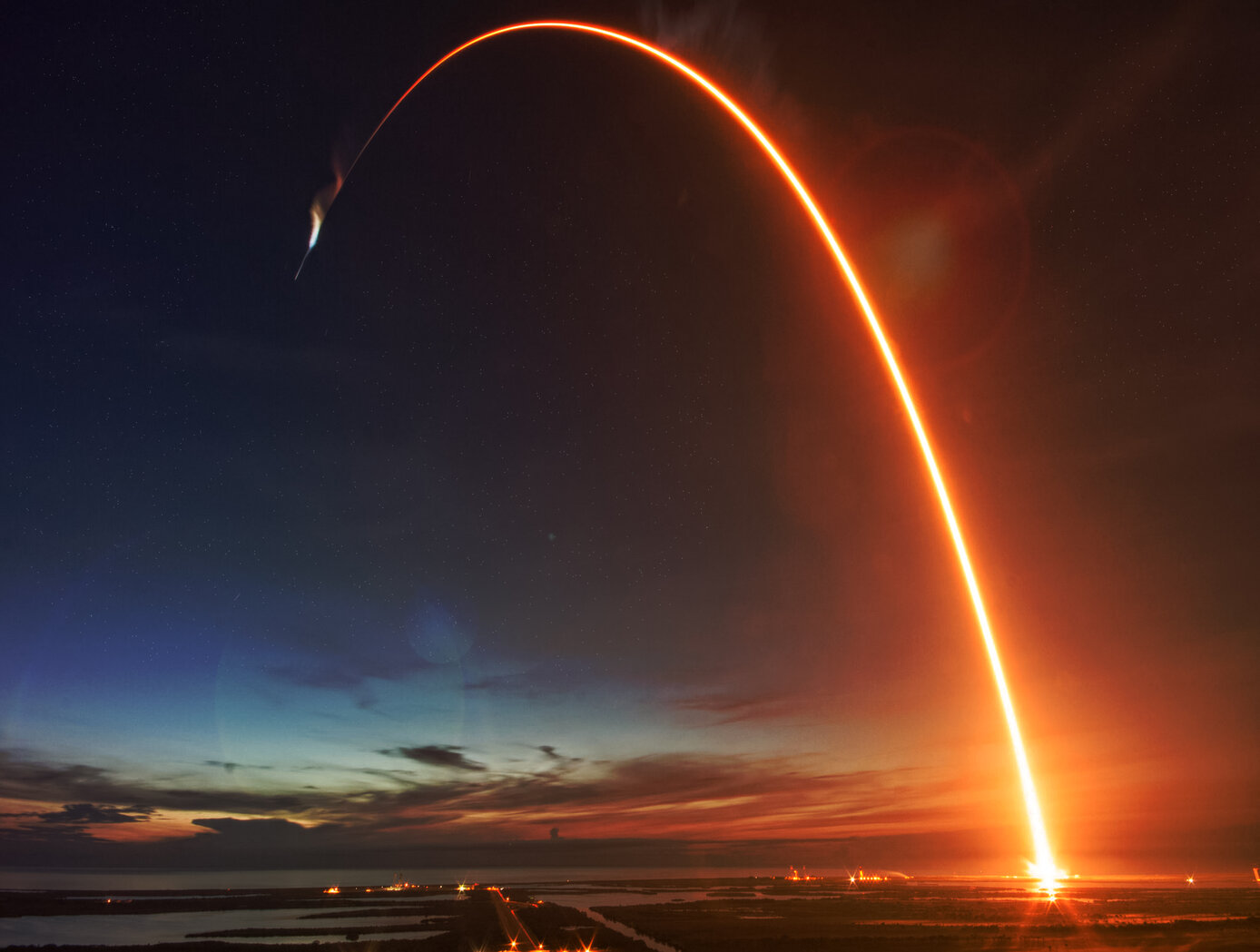
Fast-Acting, Deep-Throttling Hybrid Motor
Hybrid chemical motors offer an alternative to traditional liquid or solid motors for spacecraft, missiles, rockets, or other vehicles. The key advantage of a hybrid motor is the capability to throttle the motor via active control, which cannot be done in solid propellant motors. However, rapid throttling presents significant challenges to implement in practice.
Here, NASA has combined a deep-throttling hybrid motor previously developed by Utah State University with a fast-acting digital valve design to produce a fast-acting, deep-throttling hybrid. Testing performed to-date using a prototype of the hybrid motor and digital valve design has shown the new hybrid motor to be capable of full-scale throttling twice as fast (1 second throttling compared to 2 seconds) as previous control valve designs. With optimization, there is potential full-range throttling may be further reduced to 0.5 second, a 4x improvement over previous control valve designs for hybrid motors. Additionally, smaller mid-range thrust changes have currently been measured in the <0.5 second range.
With the throttling capability enabled by the implemented digital valves, it also becomes feasible to achieve thrust ratios of >40:1 for relatively small motors (<1000 N), opening up the opportunity to replace both the main propulsion system (MPS) and reaction control system (RCS) with a single, more efficient motor capable of meeting the needs of both on a spacecraft.
The hybrid motor is at technology readiness level (TRL) 4 (component and/or breadboard validation in laboratory environment) and is available for patent licensing.
Robotics Automation and Control
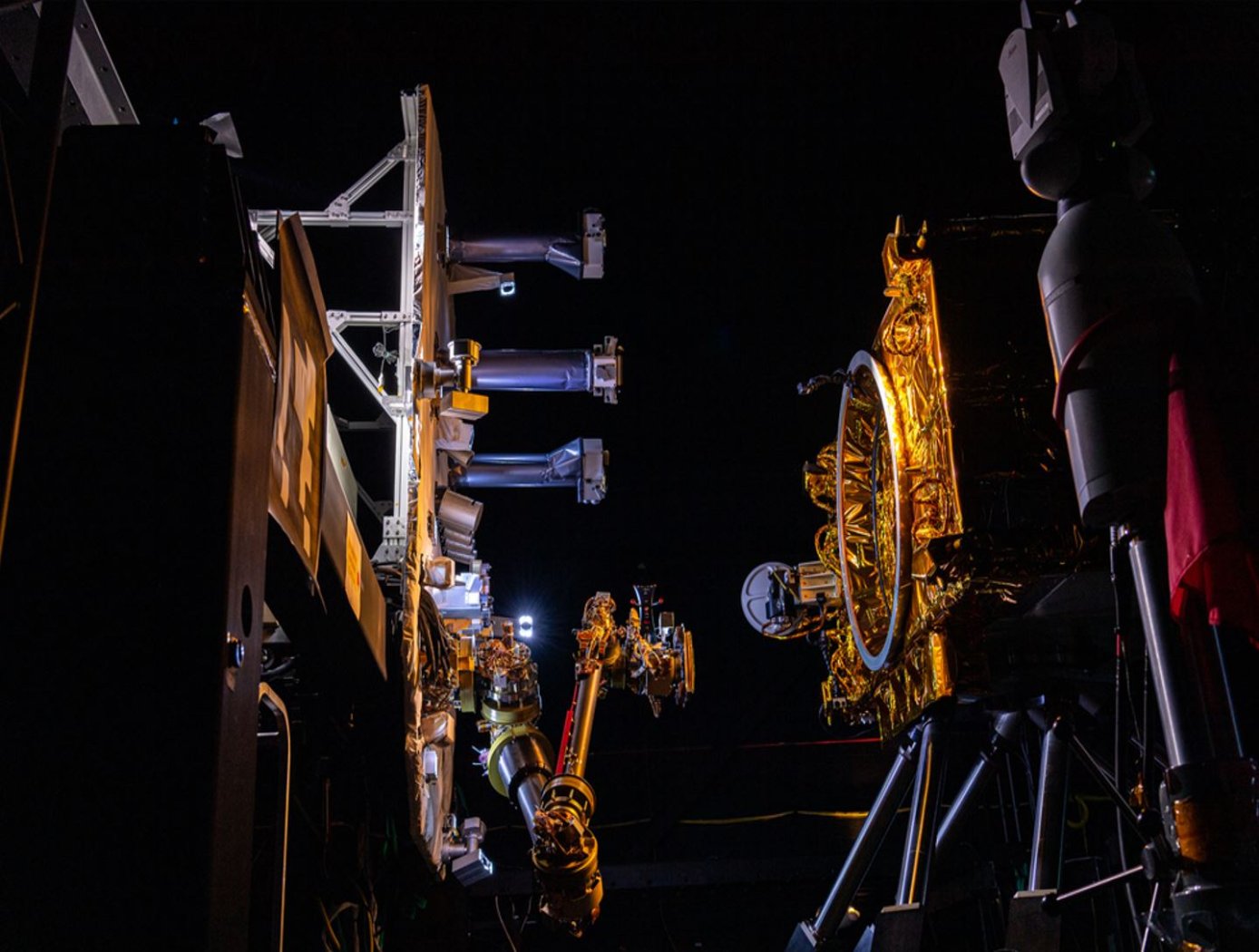
New motors for next-generation in-space servicing
Satellites and other spacecraft require maintenance and service after being deployed in orbit, requiring a wide variety of tools that perform multiple maintenance tasks (grip, cut, refuel, etc.). Current drive systems for the tool interfaces on the robotic arms that perform these service tasks are not as robust nor packaged properly for use in the ATDS. The ATDS is one part of a larger in-space servicing system (example shown in the figure below) that must be versatile and perform multiple jobs.
Here, innovators at the NASA Goddard Space Flight Center have developed new BLDC motors to provide the torque necessary to drive the wide variety of tools needed for in-space servicing. The four motors provide torque to the coupler drive, linear drive, inner rotary drive, and outer rotary drive of the ATDS. The new BLDC motors will enable the tools attached to the ATDS to be operated in multiple modes of operation.
Each of the four motors have been customized with different speed and torque capabilities to meet the different performance requirements of the various actuator drive trains while maintaining a common gearhead across all the motors. Further, the packaging surrounding the motors has been tailored to reduce the overall weight of the motors and reduce the motor footprint to meet the needs of the ATDS. The BLDC motors for the ATDS are available for patent licensing.
power generation and storage
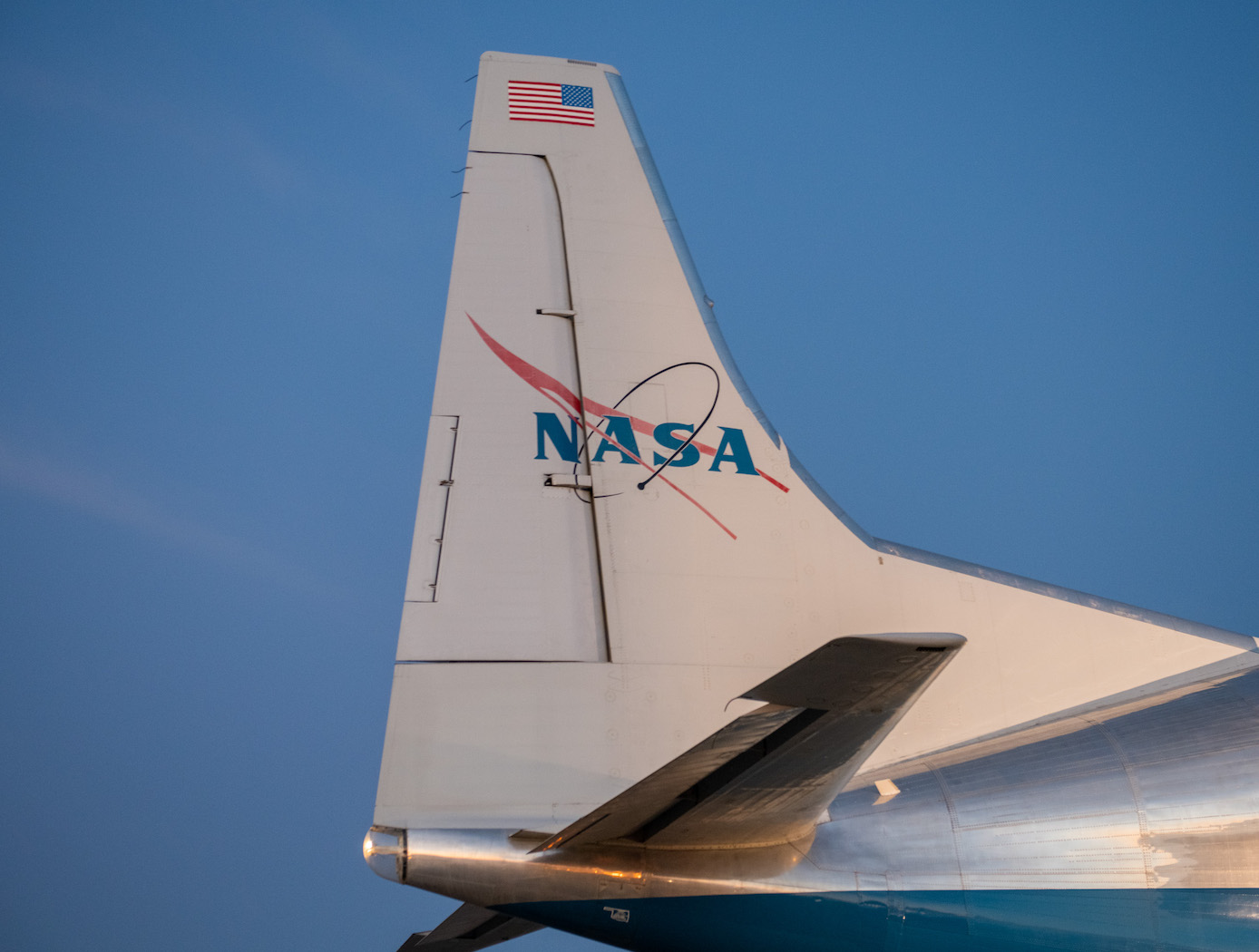
High Efficiency Megawatt Motor
The HEMM is a is a wound-field partially superconducting machine that implements a combination of rotor superconducting and stator normal conductor elements, along with an integrated acoustic cryocooler, to achieve some of the benefits of a superconducting motor without the need for an external cryogenic system. The combination of the described elements allows a motor to be built which essentially operates like any other motor when viewed as a black box, but substantially enhanced performance can be achieved. The incorporation of superconductors on the rotor to create a high-level magnetic field results in a specific power and efficiency that could not be achieved any other way. The HEMM can achieve over 98% efficiency in a lightweight electric machine with an operating power greater than 1.4 MW, a specific power greater than 16 kW/kg (ratio to electromagnetic mass), and a rated operating speed of 6800 RPM. The HEMM can be used as both a motor or a generator, offering a wide range of applications including propulsion systems for hybrid aircraft, electric trains, hybrid cars, and turboelectric ships, as well as generator systems for wind turbines, power plants, or motors for other industrial machinery.
Robotics Automation and Control

Upper Body Robotic Exoskeleton
NASA's soft, portable, wearable robotic device is "plug and play" - it includes all necessary electronics, actuation, software, and sensors required to achieve augmented limb movement. The garment is designed such that the human-robot interface distributes load across the torso, maximizing user comfort. Donning and doffing is simple, as the device lowers over the head, straps to the torso via Velcro, and possesses adjustable custom arm cuffs. Actuators are housed in the back of the garment, which pull custom conduit-tendon-based systems attached to the limb at optimized locations, causing the joint of interest to move to the specified orientation. Force sensing is employed to enable optimal control of the limb, measuring user-applied force to maintain commanded joint orientations. Integrated electronics and software provide power distribution, safety monitoring, data transfer and data logging.
NASA's garment has multiple modes of operation. In active assist mode, shoulder abduction and flexion, and elbow flexion, may be commanded either simultaneously via coordinated control or individually while holding position/orientation of the other joints. In passive assist mode, the user can freely move the limb while the system provides minimal torque to the shoulder and elbow.
The upper body robotic exoskeleton is at a TRL 6 (system/subsystem prototype demonstration in a relevant environment) and it is now available for your company to license and develop into a commercial product. Please note that NASA does not manufacture products itself for commercial sale.