Lunar Landing Pads
manufacturing
Lunar Landing Pads (KSC-TOPS-89)
Durable takeoff and landing pads for the Moon and beyond
Overview
Lunar landing and launch pads represent critical infrastructure for enabling a sustained presence on the Moon or other planetary bodies. Such a Moon presence would require repeated lunar landings and takeoffs, preferably near an outpost or habitat. In the absence of takeoff and landing pads, such vehicles could project lunar regolith at high velocities, sandblasting the surrounding infrastructure and causing damage.
Conventional paver technology does not have the capability to withstand the loads experienced by landing pads during vehicle landing or take off. Use of existing technology may result in pavers being displaced by the plume of the vehicle, or exhaust from the vehicle entering spaces between paver seams and eroding the regolith underneath the landing pad. To address this issue, engineers at NASA's Kennedy Space Center and Sidus Space developed a novel interlocking paver system enabling the robotic construction of high stability vertical takeoff and landing pads.
The Technology
The jointly developed interlocking paver design consists of a molded solid material with tapered interlocking features that interface with features of an opposite gender in three orthogonal directions. This establishes a toleranced connection between the pavers that locks down six degrees of freedom.
More specifically, the system consists of two types of pavers: polygon and spacer pavers. Both are symmetrical about the longitudinal and transverse axes and are designed to interlock securely with one another in a checkerboard pattern. The polygon paver features an octagonal top level and a rectangular bottom level with protrusions and recessed notches. The spacer paver has an elongated center portion with isosceles trapezoid extensions on the top level and a rectangular bottom level with protrusions and notches. The interlocking design locks down six degrees of freedom, providing enhanced stability and preventing the flow of exhaust gases between the seams to mitigate erosion of the underlying regolith.
The pavers could be constructed leveraging in-situ resource utilization (ISRU). Lunar regolith has been identified as a potential construction material. Additionally, the pavers could be installed via robotic assembly, reducing the need for human labor in harsh environments.
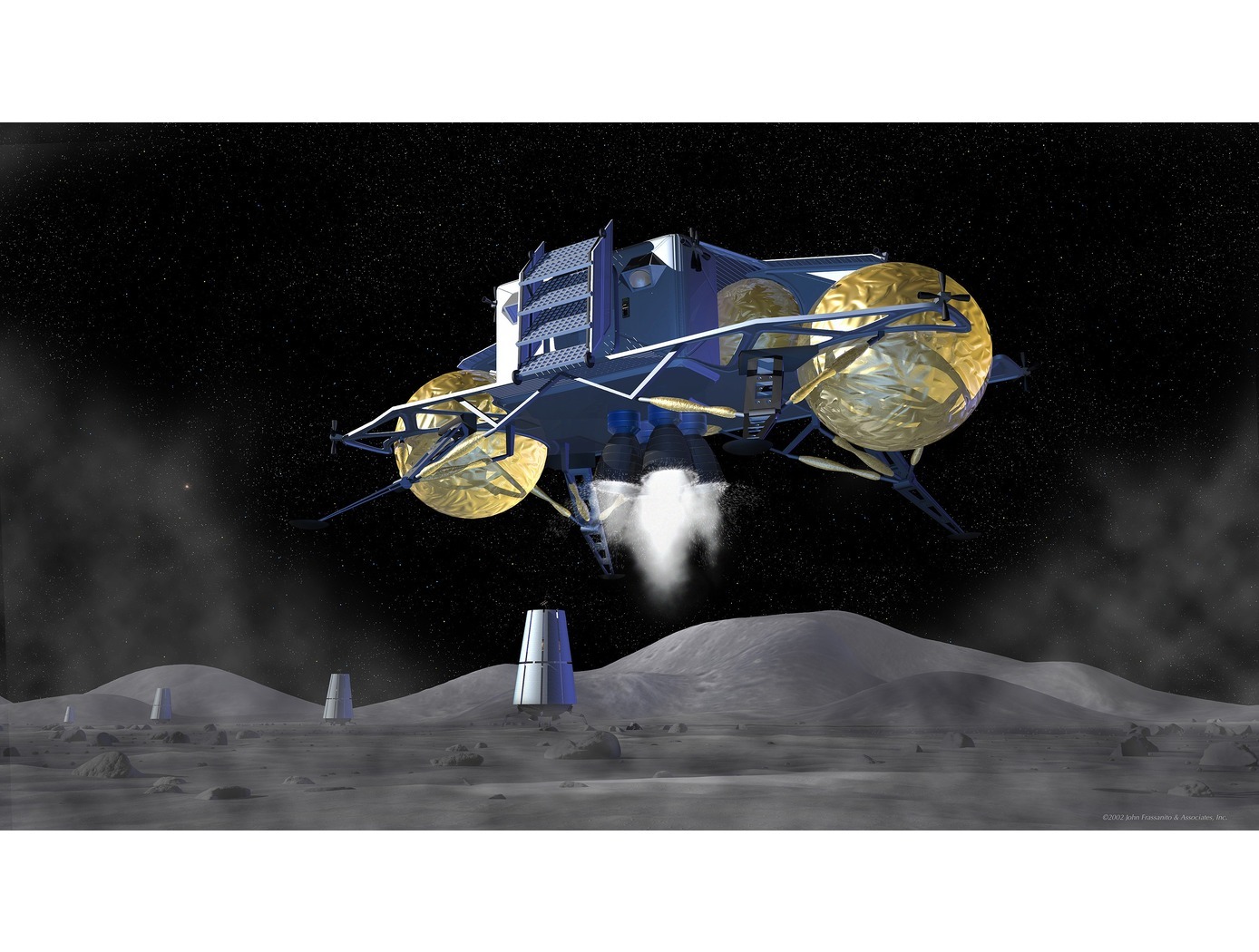
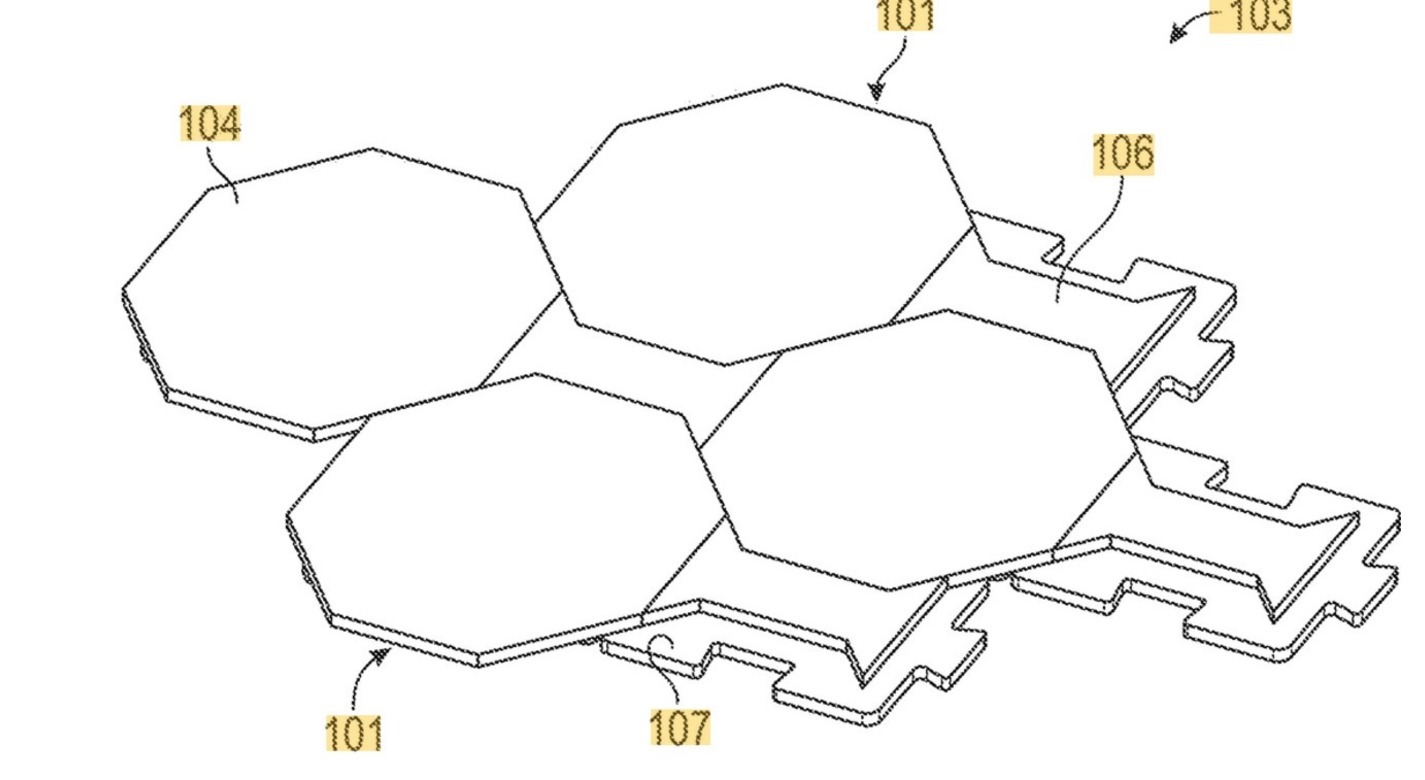
Benefits
- Enhanced stability & longevity: The interlocking design of the pavers provides a secure connection, reducing the risk of displacement during vehicle landings and takeoffs.
- Prevents regolith erosion: The interlocking pavers prevent exhaust gases from entering the spaces between paver seams, mitigating erosion and projection of underlying regolith onto surrounding infrastructure.
- In-situ resource utilization: The ability to construct the pavers from in situ materials, such as lunar regolith, reduces the need for transporting materials from Earth to extraterrestrial surfaces.
- Scalability: The interlocking paver system can be easily expanded or reconfigured to accommodate different landing pad sizes or layouts.
- Autonomous installation: The pavers can be installed by an autonomous paver-laying machine, reducing the need for human intervention in harsh environments.
Applications
- Extraterrestrial landing/takeoff pads: Construction of stable landing pads for spacecraft on surfaces like the Moon, Mars, or other planetary bodies.
- Consumer & commercial applications: The pavers could be used to provide easy installation for consumer and commercial applications (e.g., driveways, walkways, streets, patios, etc.) by requiring less site prep work, as well as potentially last longer than current paver technologies.
- Military landing/takeoff pads: Special military situations may benefit from this design in atypical environments.
Tags:
|
Similar Results

eVTOL UAS with Lunar Lander Trajectory
This NASA-developed eVTOL UAS is a purpose-built, electric, reusable aircraft with rotor/propeller thrust only, designed to fly trajectories with high similarity to those flown by lunar landers. The vehicle has the unique capability to transition into wing borne flight to simulate the cross-range, horizontal approaches of lunar landers. During transition to wing borne flight, the initial transition favors a traditional airplane configuration with the propellers in the front and smaller surfaces in the rear, allowing the vehicle to reach high speeds. However, after achieving wing borne flight, the vehicle can transition to wing borne flight in the opposite (canard) direction. During this mode of operation, the vehicle is controllable, and the propellers can be powered or unpowered.
This NASA invention also has the capability to decelerate rapidly during the descent phase (also to simulate lunar lander trajectories). Such rapid deceleration will be required to reduce vehicle velocity in order to turn propellers back on without stalling the blades or catching the propeller vortex. The UAS also has the option of using variable pitch blades which can contribute to the overall controllability of the aircraft and reduce the likelihood of stalling the blades during the deceleration phase.
In addition to testing EDL sensors and precision landing payloads, NASA’s innovative eVTOL UAS could be used in applications where fast, precise, and stealthy delivery of payloads to specific ground locations is required, including military applications. This concept of operations could entail deploying the UAS from a larger aircraft.

Multifunctional Ablative Thermal Protection System
The initial compression pad design for Orion was complex and limited to Earth orbit return missions, such as the 2014 Exploration Flight Test-1 (EFT-1). The 2-D carbon phenolic material used for EFT-1 has relatively low interlaminar strength and requires a metallic sheer insert to handle structural loads. There are few options for materials that can meet the load demands of lunar return missions due to performance or part-size limitations. The 3DMAT material is a woven fiber preform fully densified with cyanate ester resin. It produces a large composite with significant structural capabilities and the ability to withstand high aerothermal heating environments on its outer surface while keeping the inner surface cool and protected from the aerothermal heating. The robustness of the 3DMAT material is derived from high fiber volume (>56%), 3-D-orthoganol architecture, and low porosity (0.5%). Orion has adopted 3DMAT for all future MPCV missions, including EM-1 schedule to launch in 2018.

Regolith-Polymer 3D Printing
The invention consists of a 3D print head apparatus that heats and extrudes a regolith-polymer (or other) mixture as part of an additive manufacturing process. The technology includes a securing mechanism, hopper, nozzle, barrel, and heating system. The securing mechanism attaches to a wrist joint of a robotic arm. The hopper, connected to the securing mechanism, has a cavity and a lower aperture. The barrel is an elongated, hollow member with its first end connected to the hopper's lower aperture and its second end connected to the nozzle's upper aperture. The heating system is positioned along the barrel and comprises a heater, thermocouple, insulator, and heating controller. The heating controller activates the heater based on input signals received from the thermocouple.
The print head apparatus also includes a feed screw, drive shaft, and motor. The feed screw is positioned within the elongated hollow member of the barrel, and the drive shaft transmits torque to the feed screw. The motor provides torque to the drive shaft.
An agitator is secured to the drive shaft, facilitating the consistent movement and mixing of the regolith-polymer mixture in the hopper. The nozzle includes a tube with an open end and an occluded end, allowing the mixture to be extruded through the lower aperture.
The jointly developed 3D print head technology enables efficient, large-scale additive construction using in-situ resources, such as regolith or other materials. The innovation reduces the need for transporting materials from Earth and allows for sustainable habitat development on the Moon or Mars. Given its adaptability to different crushed rock-polymer materials, the invention may also serve as an alternative to conventional Portland concrete construction on Earth.

3D Lidar for Improved Rover Traversal and Imagery
The SQRLi system is made up of three major components including the laser assembly, the mirror assembly, and the electronics and data processing equipment (electronics assembly) as shown in the figure below. The three main systems work together to send and receive the lidar signal then translate it into a 3D image for navigation and imaging purposes.
The rover sensing instrument makes use of a unique fiber optic laser assembly with high, adjustable output that increases the dynamic range (i.e., contrast) of the lidar system. The commercially available mirror setup used in the SQRLi is small, reliable, and has a wide aperture that improves the field-of-view of the lidar while maintaining a small instrument footprint. Lastly, the data processing is done by an in-house designed processor capable of translating the light signal into a high-resolution (sub-millimeter) 3D map. These components of the SQRLi enable successful hazard detection and navigation in visibility-impaired environments.
The SQRLi is applicable to planetary and lunar exploration by unmanned or crewed vehicles and may be adapted for in-space servicing, assembly, and manufacturing purposes. Beyond NASA missions, the new 3D lidar may be used for vehicular navigation in the automotive, defense, or commercial space sectors. The SQRLi is available for patent licensing.

Improved Lunar Regolith Simulant Ion Implantation
Researchers and other technology developers require regolith simulants that accurately emulate the properties of lunar, Martian, and asteroid soils to ensure that the processes, devices, tools, and sensors being developed will be usable in an active mission environment. To move toward higher fidelity regolith simulants, NASA has developed a system that takes typical regolith simulants and implants ions of relevant elements to better simulate the conditions of extraterrestrial soils.
The ion implantation device developed here is composed of three key elements as shown in the figure below: two hopper and rotary valve elements and the acceleration grid structure. To perform the ion implantation, the system is first placed within a vacuum chamber, pumped down, and gases of the elements of interest are pumped into the chamber. The system then first passes a mass of granulated lunar regolith simulant through two stages of hoppers and rotary valves to condition the material. Key to the system is a process for interstitial gas removal (a source of contamination) as shown in the figure on the right. After conditioning, the regolith simulant is passed between two parallel electrodes under a high voltage, accelerating ions of the process gas and implanting those ions within the regolith simulant at controllable depths.
The related patent is now available to license. Please note that NASA does not manufacturer products itself for commercial sale.