Additive Manufacturing Model-based Process Metrics (AM-PM)
Information Technology and Software
Additive Manufacturing Model-based Process Metrics (AM-PM) (LAR-TOPS-368)
Computational tool to model and evaluate additively manufactured parts
Overview
Additive manufacturing enables unrivaled design freedom and flexible fabrication of components from a wide range of materials including metals, composites, polymers, and ceramics. The near net shape parts are made by processes like sequential melting or layer-by-layer material deposition with a complex set of processing variables. The sequential nature of the process means that every step can impact the next and thus, tools to evaluate that risk before and during manufacturing are necessary.
Inventors at the NASA Langley Research Center have developed a novel method to model and ingest point-wise process data to evaluate an additive manufacturing build and its file for issues by highlighting potential anomalies or other areas where the build may have issues with fusion of the material. The technique was originally developed for use in tandem with powder bed fusion additive manufacturing for aerospace parts and is capable of being used on consumer grade computers.
The Technology
Modeling additive manufacturing processes can be difficult due to the scale difference between the active processing point (e.g., a sub-millimeter melt pool) and the part itself. Typically, the tools used to model these processes are either too computationally intensive (due to high physical fidelity or inefficient computations) or are focused solely on either the microscale (e.g., microstructure) or macroscale (e.g., cracks). These pitfalls make the tools unsuitable for fast and efficient evaluations of additive manufacturing build files and parts.
Failures in parts made by laser powder bed fusion (L-PBF) often come when there is a lack of fusion or overheating of the metal powder that causes areas of high porosity. AM-PM uses a point field-based method to model L-PBF process conditions from either the build instructions (pre-build) or in situ measurements (during the build). The AM-PM modeling technique has been tested in several builds including a Ti-6Al-4V test article that was divided into 16 parts, each with different build conditions. With AM-PM, calculations are performed faster than similar methods and the technique can be generalized to other additive manufacturing processes.
The AM-PM method is at technology readiness level (TRL) 6 (system/subsystem model or prototype demonstration in a relevant environment) and is available for patent licensing.
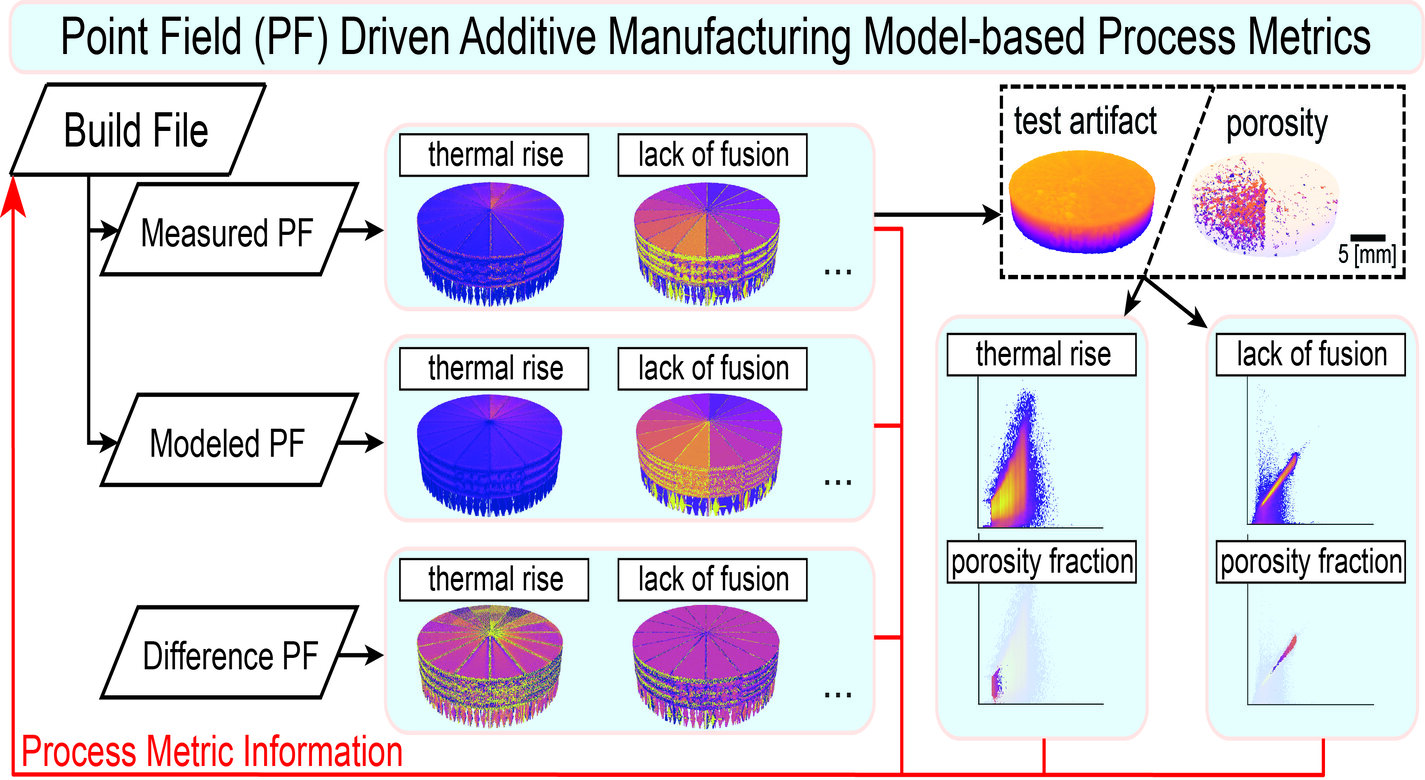
Benefits
- Computationally efficient: Calculations are performed with track-wise precision though a build in minutes, at least 10x faster than other in-use modeling approaches.
- Multiple use-cases: AM-PM can be employed before, during, and after an additive manufacturing process to ensure build correctness.
- Possible time and cost saving: Evaluating build instructions for potential issues before manufacturing can reduce risk, cost, time to market for additively manufactured parts.
- Accessible: The AM-PM modeling technique can be run on a consumer-grade computer, and runs off of the build file or process points as recorded-only material property inputs.
- At a relevant size scale: The method models additive manufacturing processes on the mesoscale (between part-scale and cubic microns).
Applications
- Additive manufacturing: build correctness modeling before, during, and after manufacturing for any additive manufacturing process.
- Additive manufacturing: rapid development of build strategies customized to each part geometry and sub-geometries.
Technology Details
Information Technology and Software
LAR-TOPS-368
LAR-20083-1
LAR-20083-1-CIP
The Additive Manufacturing Moment Measure - A Parallel Computation Technique for Determining Build Variance in the Laser Powder Bed Fusion Process. May 10, 2022. Materials Research Society (MRS) 2022 Spring Meeting. Conference presentation.
The Additive Manufacturing Moment Measure (AM3) Approach to Predictions of Solid Cooling Rate and Time Above Melt. August 17, 2022. Additive Manufacturing Benchmarks (AM-Bench) 2022. Conference presentation.
Hocker, Samuel J. A., Brodan M. Richter, Joseph N. Zalameda, Peter W. Spaeth, Andrew R. Kitahara, and Edward H. Glaessgen. “Additive Manufacturing Model-Based Process Metrics: Reduced Order Modeling of the Laser Powder Bed Fusion Process.” Conference presentation presented at the 2022 Materials Science & Technology Conference, Pittsburg, PA, October 12, 2022. https://www.matscitech.org/MST22.
Hocker, Samuel J.A., Brodan Richter, Peter W. Spaeth, Andrew R. Kitahara, Joseph N. Zalameda, and Edward H. Glaessgen. “A Point Field Driven Approach to Process Metrics Based on Laser Powder Bed Fusion Additive Manufacturing Models and In-Situ Process Monitoring.” Journal of Materials Research (2023).
The Additive Manufacturing Moment Measure (AM3) Approach to Predictions of Solid Cooling Rate and Time Above Melt. August 17, 2022. Additive Manufacturing Benchmarks (AM-Bench) 2022. Conference presentation.
Hocker, Samuel J. A., Brodan M. Richter, Joseph N. Zalameda, Peter W. Spaeth, Andrew R. Kitahara, and Edward H. Glaessgen. “Additive Manufacturing Model-Based Process Metrics: Reduced Order Modeling of the Laser Powder Bed Fusion Process.” Conference presentation presented at the 2022 Materials Science & Technology Conference, Pittsburg, PA, October 12, 2022. https://www.matscitech.org/MST22.
Hocker, Samuel J.A., Brodan Richter, Peter W. Spaeth, Andrew R. Kitahara, Joseph N. Zalameda, and Edward H. Glaessgen. “A Point Field Driven Approach to Process Metrics Based on Laser Powder Bed Fusion Additive Manufacturing Models and In-Situ Process Monitoring.” Journal of Materials Research (2023).
Tags:
|
Similar Results

Fully Automated High-Throughput Additive Manufacturing
The technology is a method to increase automation of Additive Manufacturing (AM) through augmentation of the Fused Filament Fabrication (FFF) process. It can significantly increase the speed of 3D printing by automating the removal of printed components from the build platform without the need for additional hardware, which increases printing throughput. The method can also be leveraged to perform automated object testing and characterization. The method includes embedding into the manufacturing instructions methods to fabricate directly onto the build platform an actuator tool, such as a linear spring. The deposition head can be leveraged as a robotic manipulator of the actuator tool to bend, cock, and release the linear spring to strike the target manufactured object and move it off the build platform of the machine they were manufactured on. The ability for an object to 'fly off of the machine that made it' essentially enables automated clearing of the processed build volume. The technology can also be used for testing the AM machine or the feedstock material by successively fabricating prototypes of the manufactured object, and taking measurements from sensors as the actuator strikes the prototype. This provides automated testing for quality control, machine calibration, material origins, and counterfeit detection.
.jpg)
Interim, In Situ Additive Manufacturing Inspection
The in situ inspection technology for additive manufacturing combines different types of cameras strategically placed around the part to monitor its properties during construction. The IR cameras collect accurate temperature data to validate thermal math models, while the visual cameras obtain highly detailed data at the exact location of the laser to build accurate, as-built geometric models. Furthermore, certain adopted techniques (e.g., single to grouped pixels comparison to avoid bad/biased pixels) reduce false positive readings.
NASA has developed and tested prototypes in both laser-sintered plastic and metal processes. The technology detected errors due to stray powder sparking and material layer lifts. Furthermore, the technology has the potential to detect anomalies in the property profile that are caused by errors due to stress, power density issues, incomplete melting, voids, incomplete fill, and layer lift-up. Three-dimensional models of the printed parts were reconstructed using only the collected data, which demonstrates the success and potential of the technology to provide a deeper understanding of the laser-metal interactions. By monitoring the print, layer by layer, in real-time, users can pause the process and make corrections to the build as needed, reducing material, energy, and time wasted in nonconforming parts.

Recyclable Feedstocks for Additive Manufacturing
NASA's new technique for generating recyclable feedstocks for on-demand additive manufacturing employs the high-yield reversibility of the Diels-Alder reaction between maleimide and furan functionalities, utilizing the exceedingly favorable interaction between specific chemical functionalities, often termed "click reactions" due to their rapid rate and high efficiency. Integration of these moieties within a polymer coating on epoxy microparticle enables reversible assembly into macroscopic, free-standing articles. This click chemistry can be activated and reversed through the application of heat. Monomer species can be used to incorporate these functionalities into polyimide materials, which provide excellent mechanical, thermal, and electrical properties for space applications. Copoly (carbonate urethane) has been shown to be a viable coating material in the generation of polymer-coated epoxy microparticle systems and is amenable to being processed through a variety of approaches (e.g., filaments and slurries for 3D printing, compression molding, etc.). The polymeric materials are grown from the surfaces of in-house fabricated epoxy microparticles. The thermal and mechanical properties of the microparticles can be readily tuned by changes in composition.
There are a number of potential applications for this NASA technology ranging from use of these materials for recyclable/repurpose-able articles (structural, decorative, etc.) to simple children's toys. More demanding uses such as for replacement parts in complex industrial systems are also possible. For long term space missions, it is envisioned that these feedstocks would be integrated into secondary spacecraft structures such that no additional concerns would be introduced due to in-space chemical reactions and no additional mass would be required.

In-situ Characterization and Inspection of Additive Manufacturing Deposits using Transient Infrared Thermography
Additive manufacturing or 3-D printing is a rapidly growing field where solid, objects can be produced layer by layer. This technology will have a significant impact in many areas including industrial manufacturing, medical, architecture, aerospace, and automotive. The advantages of additive manufacturing are reduction in material costs due to near net shape part builds, minimal machining required, computer assisted builds for rapid prototyping, and mass production capability. Traditional thermal nondestructive evaluation (NDE) techniques typically use a stationary heat source such as flash or quartz lamp heating to induce a temperature rise. The defects such as cracks, delamination damage, or voids block the heat flow and therefore cause a change in the transient heat flow response. There are drawbacks to these methods.

A One-piece Liquid Rocket Thrust Chamber Assembly
The one-piece multi-metallic composite overwrap thrust chamber assembly is centrally composed of an additively manufactured integral-channeled copper combustion chamber. The central chamber is being manufactured using a GRCop42 or GRCop84 copper-alloy additive manufacturing technology previously developed by NASA. A bimetallic joint (interface) is then built onto the nozzle end of the chamber using bimetallic additive manufacturing techniques. The result is a strong bond between the chamber and the interface with proper diffusion at the nozzle end of the copper-alloy. The bimetallic interface serves as the foundation of a freeform regen nozzle. A blown powder-based directed energy deposition process (DED) is used to build the regen nozzle with integral channels for coolant flow. The coolant circuits are closed with an integral manifold added using a radial cladding operation. To complete the TCA, the entire assembly including the combustion chamber and regen nozzle is wrapped with a composite overwrap capable of sustaining the required pressure and temperature loads.