Gimbal for Steering Propelled CubeSats
robotics automation and control
Gimbal for Steering Propelled CubeSats (MFS-TOPS-74)
Compact, Mount-ready Package to Facilitate Attitude Control
Overview
NASA is preparing for the next generation of CubeSats that are propelled and will make directional maneuvers. The new gimbal mount provides a seat for the motor and controls the position of the thrusters that propel the CubeSat as it moves about and/or changes orbits. This small-footprint device controls the rotation (360 degrees) and tilt (+/- 12 degrees) of a directional system to a very high accuracy (0.02 degrees). It alleviates the need for more traditional directional control hardware, including magnetorquers and magnetometers. The gimbal controls larger masses for its size than other positioning systems. It has a low parts count (six) and can support up to 0.5 kg mass. NASA built a prototype and conducted several tests to prove its control and precision capabilities, and its ability to withstand vibration testing. Now NASA seeks companies to commercialize the gimbal.
The Technology
The small thruster mount, roughly the size of a doughnut, controls the rotation and tilt of a directional system to a high degree of accuracy (0.02 degrees). NASA developed the rotary tilting gimbal (RTG) for thruster directional control of CubeSats. This RTG is designed to provide precision control in both the tilting and rotary degree of freedom by using accurate positioning, encoded piezoelectric motors, and a close tolerance machined structure. The RTG functions via rotary motion of the integrated assembly by a grounded piezoelectric support motor, and tilts via a rotary motor that rides on the primary structure. This alleviates the need for more traditional, directional control hardware, including magnetorquers and magnetometers. The subject technology has a resulting rotational degree of freedom of 360 degrees and a tilting degree of freedom of +/- 12 degrees. The rotary motor is connected to the tilt plate by a two-piece crank assembly. The gimbal weight, including the motors, is about 420 grams; without motors, it is about 100 grams. The operating temperature range is 0-50C. Sinusoidal testing was performed before and after the random vibration tests to determine if any structural changes occurred as a result of the tests. The gimbal met the qualification requirements and did not present any significant structural changes from flight-level testing.
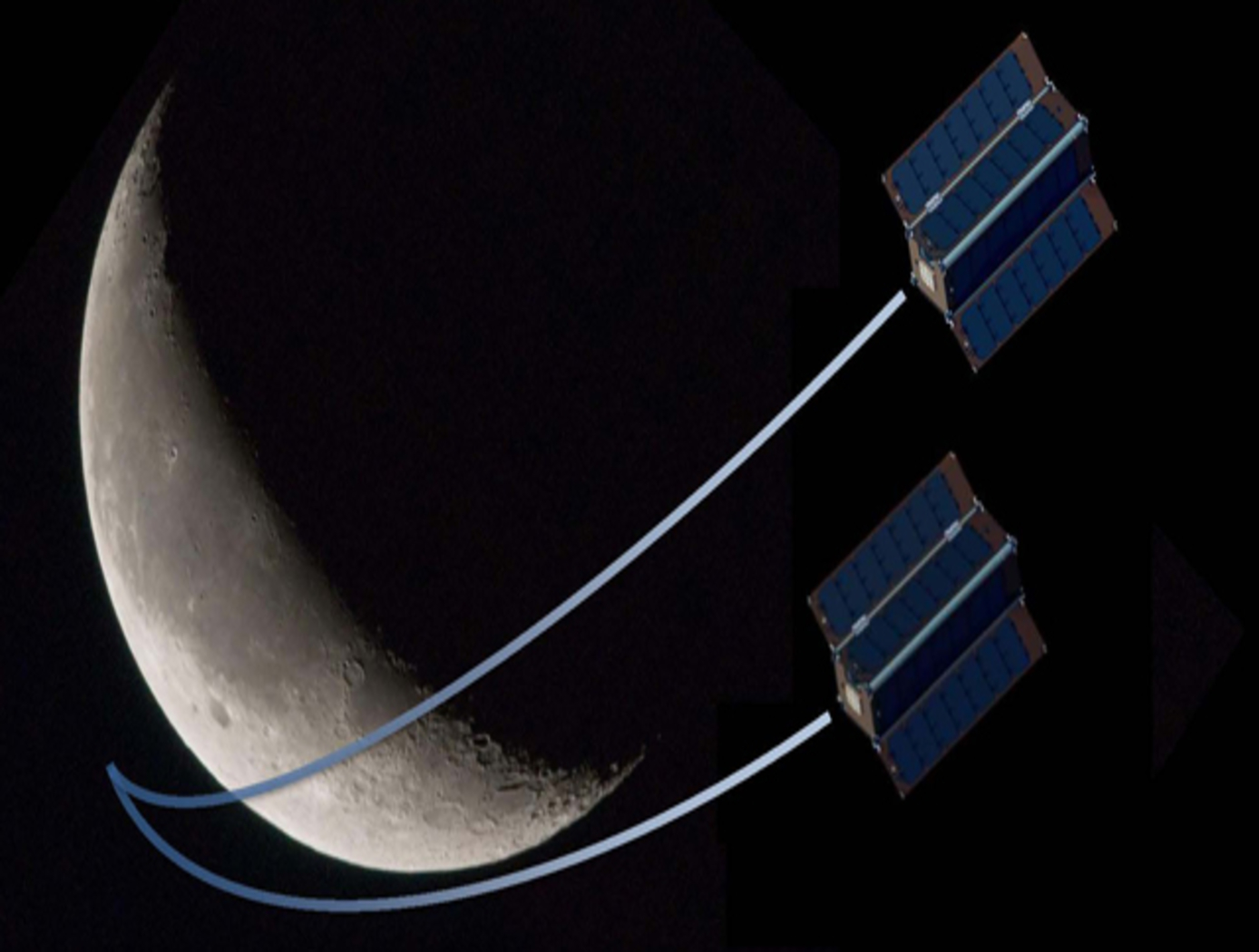
.jpg)
Benefits
- Low parts count: the gimbal alone comprises six parts; with motors and frangibolts, the parts count is nine
- High precision: controls position to 0.02°
- Reduced mass, volume, and power requirements compared to magnetorquers and magnetometers
Applications
- Aerospace: attitude control of electric propulsion thrusters for spacecraft, including CubeSats
- Optics: precise imager/camera positioning
- Manufacturing: laser control
Similar Results

Circumferential Scissor Spring Enhances Precision in Hand Controllers
The traditional scissor spring design for hand controllers has been improved upon with a circumferential spring controller mechanism that facilitates easy customization, enhanced durability, and optimum controller feedback. These advantages are partially facilitated by locating the spring to the outside of the mechanism which allows for easier spring replacement to adjust the deflection force or for maintenance.
The new mechanism is comprised of two rounded blades, or cams, that pivot forward and back under operation and meet to form a circle. An expansion spring is looped around the blade perimeter and resides in a channel, providing the restoring force that returns the control stick to a neutral position. Due to the use of a longer circumferential spring, the proportion of spring expansion is smaller for a given distance of deflection, so the forces associated with the deflection remain on a more linear portion of the force deflection curve.
The Circumferential Scissor Spring for Controllers is at technology readiness level (TRL) 8 (actual system completed and flight qualified through test and demonstration) and is available for patent licensing. Please note that NASA does not manufacture products itself for commercial sale.

Miniaturized Astrometric Alignment Sensor
The Miniaturized Astrometric Alignment Sensor advances satellite capabilities for astrophysical measurements, necessary for formation flying, relative navigation, and virtual telescope capabilities. The sensor is a single assembly consisting of a small, low powered camera assembly. The sensor detects stellar objects from which both stellar and object tracking are performed. The sensors components consist of a low power camera assembly, interchangeable lenses, camera power supply, and image processing software and algorithms. The system functions by searching and identifying objects in the camera's field of view and tracking the objects against a selected star pattern with a central body of interest in the sensor's field of view.
The Miniaturized Astrometric Alignment Sensor makes it possible to measure a spacecrafts altitude and orientation with respect to known stellar objects. The instrument takes an image of a patch of sky, identifies the stars in that field of view, and compares the field view with a stored star map. The data is processed with a dedicated processor attached to the instrument to spell out the attitude and orientation of a spacecraft.

Aerodynamically Actuated Thrust Vectoring Device
The thrust actuating device includes several innovations in the aerodynamically stable tilt actuation of propellers, propeller pylons, jets, wings, and fuselages, collectively called propulsors. The propulsors rotate between hover and forward flight mode for a tilt-wing or tilt-rotor aircraft. A vehicle designed using this technology can transition from a hovering flight condition to a wing born flight condition with no mechanical actuation and can do so without complex control systems. This results in a reduction in system weight and complexity and produces a robust and naturally stable hovering aircraft with efficient forward flight modes.

Lunar Surface Manipulation System
NASA Langley developed the LSMS because of the need for a versatile system capable of performing multiple functions on the lunar surface, such as unloading components from a lander, transporting components to an operational site and installing them, and supporting service and replacement during component life. Current devices used for in-space operations are designed to work on orbit (zero g) only and thus do not have sufficient strength to operate on planetary surfaces. Traditional cranes are specialized to the task of lifting and are not capable of manipulator-type positioning operations.
The innovations incorporated into the LSMS allow it to lower payloads to the ground over a significant portion of the workspace without use of a hoist, functioning like a robot manipulator, thus providing a rigid connection and very precise control of the payload. The LSMS uses a truss architecture with pure compression and tension members to achieve a lightweight design. The innovation of using multiple spreaders (like spokes in a wheel) allows the LSMS to maintain its high structural efficiency throughout its full range of motion. Rod portions of the tension members automatically lift off and re-engage the spreaders as the joint articulates, allowing a large range of motion while maintaining mechanical advantage. In addition, the LSMS uses a quick-change device at the tip end that enables automated acquisition of end effectors or special purpose tools to increase its versatility.

Low Cost Star Tracker Software
The current Star Tracker software package is comprised of a Lumenera LW230 monochrome machine-vision camera and a FUJINON HF35SA-1 35mm lens. The star tracker cameras are all connected to and powered by the PC/104 stack via USB 2.0 ports. The software code is written in C++ and is can easily be adapted to other camera and lensing platforms by setting new variables in the software for new focal conditions. In order to identify stars in images, the software contains a star database derived from the 118,218-star Hipparcos catalog [1]. The database contains a list of every star pair within the camera field of view and the angular distance between those pairs. It also contains the inertial position information for each individual star directly from the Hipparcos catalog. In order to keep the star database size small, only stars of magnitude 6.5 or brighter were included. The star tracking process begins when image data is retrieved by the software from the data buffers in the camera. The image is translated into a binary image via a threshold brightness value so that on (bright) pixels are represented by 1s and off (dark) pixels are represented by 0s. The binary image is then searched for blobs, which are just connected groups of on pixels. These blobs represent unidentified stars or other objects such as planets, deep sky objects, other satellites, or noise. The centroids of the blob locations are computed, and a unique pattern recognition algorithm is applied to identify which, if any, stars are represented. During this process, false stars are effectively removed and only repeatedly and uniquely identifiable stars are stored. After stars are identified, another algorithm is applied on their position information to determine the attitude of the satellite. The attitude is computed as a set of Euler angles: right ascension (RA), declination (Dec), and roll. The first two Euler angles are computed by using a linear system that is derived from vector algebra and the information of two identified stars in the image. The roll angle is computed using an iterative method that relies on the information of a single star and the first two Euler angles.
[1] ESA, 1997, The Hipparcos and Tycho Catalogues, ESA SP-1200