Automated Fabric Circuit and Antenna Fabrication
Manufacturing
Automated Fabric Circuit and Antenna Fabrication (MSC-TOPS-92)
Improves performance of e-textiles through automation
Overview
Innovators at NASA Johnson Space Center have developed a cost-effective method to create fabric-based circuits and antennas by combining conventional embroidery with automated milling. The technology allows for higher surface conductivity, improved impedance control, expanded design and application potential, and greater choice of materials for optimized performance. Previous efforts to automate fabric circuit and antenna fabrication have faltered on either the complexity of the manufacturing hardware and associated costs, or design and application limitations of the resulting e-textiles. This fabrication method offers benefits in cost and labor savings and provides opportunities for the development of design patterns with higher geometric complexity and performance improvements.
The Technology
Modern production of e-textiles utilizes an embroidery technique called “e-broidery” that directly stitches circuit patterns with conductive thread onto textiles. This automated manufacturing process combines steps of e-broidery and milling to expand the application of e-textiles to high-current and high-speed uses. Manufacturing begins with two layouts of the desired conductive pattern. After assembling the layers of conductive and nonconductive materials, e-broidery is performed with the second layout and nonconductive thread to secure the layers together and designate the pattern for the conductive material. The secured assembly is transferred to an automated milling or laser cutting machine, which cuts the desired conductive pattern and releases the unneeded portions of the conductive material. The resulting e-textiles are tightly woven together, providing higher surface conductivity and impedance control. Initial comparison tests assessing the performance of fabric-based spiral antennas developed with this method, compared to conventional antennas, indicated no loss in performance across multiple metrics, including voltage standing wave ratio (VSWR), radiation pattern, and axial ratio performance.
The Method and Apparatus for Fabric Circuits and Antennas is a technology readiness level (TRL) 6 (system/subsystem prototype demonstration in a relevant environment). The innovation is now available for your company to license. Please note that NASA does not manufacture products itself for commercial sale.

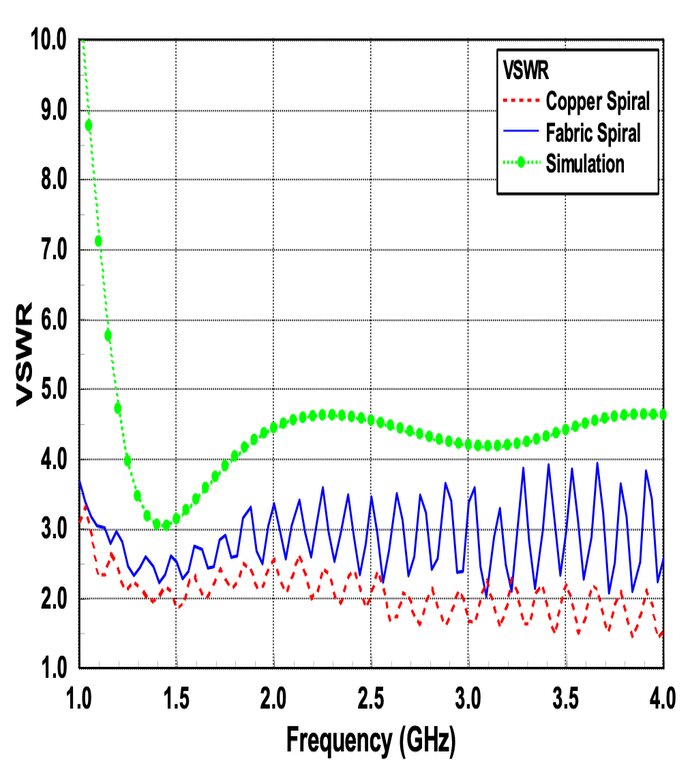
Benefits
- Mirrors methods used for fabrication of conventional rigid PCBs and printed antennas
- Permits use of materials that enable traces characterized by high surface conductivity
- Allows control of line characteristic impedance for applications over a wide range of the electromagnetic spectrum
- Actualizes complex single and multi-layered circuits with high degrees of geometric complexity
- Setup costs comparable to wet-etch process commonly used for flexible and conventional rigid PCBs
Applications
- Aerospace: lightweight fabric antennas for fabric skin aircraft and unmanned autonomous vehicles (UAVs); advanced sensors/antennas for spacesuits
- Military: digital battlefield apparel can be embedded with stealth and flexible electronics and antennas
- Textiles/wearables: wireless or cellular networking, RFID, sensors, GPS
Similar Results

Method for discrete assembly of Cuboctahedron Lattice Materials
The novel technology is a method for the design, manufacture, and assembly of modular lattice structure based mechanical metamaterials composed of cuboctahedron unit cells. The main parameters for determining the behavior of an architected lattice material are 1. Lattice geometry: base unit cell topology defines joint connectivity and informs general lattice behavior (e.g. bending or stretch dominated), which can then be used for performance prediction relative to constituent material and density. Cell size (edge length) and edge thickness (cross section) can be used to calculate relative density; 2. Base constituent material: solid properties (mechanical, thermal, electrical, etc.) are used to calculate effective properties of resulting lattice, as well as to inform manufacturing processes.
The invention relates particularly to a cuboctahedral lattice geometry, which can be decomposed into face connected cuboctahedrons. The material used is determined by the manufacturing process, such as injection molding. This offers a range of high-performance options such as glass fiber and carbon fiber reinforced polymer (GFRP, CFRP) composites. The size of the lattice can vary based on the application. Molded individual faces (bottom left figure) are then assembled into the cuboctahedron voxel building block (bottom right figure). This assembly can be achieved with a number of methods, including permanent methods such as welding or gluing, or reversible methods such as bolting or riveting.

High Performance, All-Metal X-Band Patch Antenna
The patch antenna consists of two radiating metal patch elements, a metal feed circuit, choke rings, several alignment spacers, a SMA connector, and a mounting lid giving the antenna a total diameter of 54 mm; small enough to fit in a coffee cup. The signal is carried between the lower patch and the circuit via a coaxial transmission structure, in which the probes are the inner conductor and the antenna structure is the outer conductor. The patch antenna is constructed entirely of metal, offering rugged physical durability while delivering superior performance. This advanced material not only enables the antenna to handle higher power loads (exceeding 10 watts) but also ensures exceptional stability under demanding conditions—outperforming standard patch antennas made with traditional dielectric materials. It is also not susceptible to the manufacturing variability incurred from using dielectrics. Ideally, this metallic design also allows for reentry and reuse across missions.
The patch antenna is designed with integrated choke rings to effectively mitigate multipath signal interference, delivering an impressive front-to-back ratio of over 35 dB. Its integrated polarizer circuit enhances signal clarity and boosts overall efficiency, ensuring reliable communication in challenging environments. With support for both right- and left-handed circular polarization, the antenna achieves a co-polarization peak gain of 9 dBi and an axial ratio of less than 3 dB within a wide 50-degree orientation range. These advanced features provide superior signal performance and consistent clarity across diverse applications.
Although designed for space and planetary exploration applications, the antenna may also be valuable for terrestrial use cases with rugged conditions. The X-band patch antenna is at technology readiness level (TRL) 5 (component and/or breadboard validation in relevant environment) and is available for patent licensing.

Multi-and Wide-Band Single-Feed Patch Antenna
NASA's patch antenna technology exhibits higher operational bandwidth (on the order of 20%) than typical patch antennas (less than 10%) and can operate across integer-multiple frequency bands (e.g. S/X, C/X, S/C). Testing of the antenna design has demonstrated > 6dB of gain on both S and X bands (boresight), with an axial ratio of < 6dB and voltage standing wave ratio (VSWR) < 3:1 throughout the entire near-Earth network (NEN) operating bands (22.4GHz and 88.4GHz) with hemispherical coverage. The patch size is on the order of 10 x 10 cm and with associated electronics, is about 1 cm in height.

Continuous Fiber Composite for Use in Gears
Designers are constantly seeking to improve the power-to-weight ratio of components in rotorcraft and other flight vehicles. One approach has involved using lightweight carbon fiber composite materials to replace gear web portions and other components that are typically made from steel. The problem with using fiber composite materials comes when more complex shapes are required. To create thickness variation and other accommodations for complex shapes, manufacturers can stack cut continuous fiber plies and/or form short, fiber-reinforced composite material to the desired shape. Unfortunately, these methods leave cut fiber ends within the structure, which often become initial sites for high cycle fatigue damage in high speed, high power density applications. Glenn's new method tackles this problem with one of three approaches. The first approach is applicable to gears that are planar in shape and have a single hub and a single rim. The hub and web sections of the gear are made as an integrated structure with decreased thickness from the hub inner diameter to the web outer diameter. The thickness variation is accomplished using multiple layers of continuous fiber composite material formed to specific shapes and separated by filler materials. The second approach is applicable to gears that have an extended gear body in the axial direction rather than a simple planar structure. In this approach, the gear body is made using multiple layers of continuous fiber composite material in the shape of a solid of revolution. The third approach is a power transfer assembly made by combining approaches one and two. With any of these three approaches, the material can be tailored to the structure by the properties of fibers used, the number of fiber layers used, and the location of the fibers relative to the neutral axis of the structure. Glenn's innovation opens the door for carbon fiber composite materials to be used for many applications for which they were previously unsuited.

Lightweight, Self-Deployable Helical Antenna
NASA's newly developed antenna is lightweight (at or below 2 grams), low volume (at or below 1.2 cm3), and low stowage thickness (approx. 0.7 mm), all while delivering high performance (at or above 10 dBi gain). The antenna includes a novel design-material combination in a helical coil conformation. The design allows the antenna to compress for stowage (e.g., satellite launch), then self-deploy at the desired time in orbit.
NASA's lightweight, self-deployable helical antenna can be integrated into a thin-film solar array (or other large deployable structures). Integrating antenna elements into deployable structures such as power generation arrays allows spacecraft designers to maximize the inherently limited resources (e.g., mass, volume, surface area) available in a small spacecraft. When used as a standalone (i.e., single antenna) setup, the the invention offers moderate advantages in terms of stowage thickness, volume, and mass. However, in applications that require antenna arrays, these advantages become multiplicative, resulting in the system offering the same or higher data rate performance while possessing a significantly reduced form factor.
Prototypes of NASA's self-deployable, helical antenna have been fabricated in S-band, X-band, and Ka-band, all of which exhibited high performance. The antenna may find application in SmallSat communications (in deep space and LEO), as well as cases where low mass and stowage volume are valued and high antenna gain is required.