Search
sensors

Wearable RFID Sensor Tags Yield Extended Operational Times
This technology exploits the inherently passive nature of RFID to approximate the services provided by traditional active Internet of Things (IOT) protocols like ZigBee and Bluetooth. A novel store-and-forward overlay on COTS RFID protocols allows an RFID active tags to transit through an ecosystem of RFID interrogators, exploiting contact opportunities as they arise and quietly transfers sensor readings at nearly no power cost to the RFID active tag. Specific intelligence built into both the interrogator and the tag leverages the RFID tag user memory (UM) as a stand-in IOT interface. The tag operates by sampling data into timestamped packets and loads them into tag memory. When an interrogator in the ecosystem realizes that a tag is in view and that there is unrecovered data on the tag, it takes custody of the sensor data packet and offloads the data into a database. A smart scheduler reads from the population of interrogators and schedules data transfers for specific tags when an interrogator can seed the custody transfer process for the data packets. NASA has produced working prototypes of wearables, worn by the crew aboard the International Space Station, that reports humidity, temperature and CO2 readings. In one estimate, the battery life is on pace to last an estimated nine years.
The Low-Power RFID to Collect and Store Data From Many Moving Wearable Sensors is a technology readiness level (TRL) 6 (system/subsystem prototype demonstration in a relevant environment). The innovation is now available for your company to license and develop into a commercial product. Please note that NASA does not manufacture products itself for commercial sale.
Manufacturing

Automated Fabric Circuit and Antenna Fabrication
Modern production of e-textiles utilizes an embroidery technique called “e-broidery” that directly stitches circuit patterns with conductive thread onto textiles. This automated manufacturing process combines steps of e-broidery and milling to expand the application of e-textiles to high-current and high-speed uses. Manufacturing begins with two layouts of the desired conductive pattern. After assembling the layers of conductive and nonconductive materials, e-broidery is performed with the second layout and nonconductive thread to secure the layers together and designate the pattern for the conductive material. The secured assembly is transferred to an automated milling or laser cutting machine, which cuts the desired conductive pattern and releases the unneeded portions of the conductive material. The resulting e-textiles are tightly woven together, providing higher surface conductivity and impedance control. Initial comparison tests assessing the performance of fabric-based spiral antennas developed with this method, compared to conventional antennas, indicated no loss in performance across multiple metrics, including voltage standing wave ratio (VSWR), radiation pattern, and axial ratio performance.
The Method and Apparatus for Fabric Circuits and Antennas is a technology readiness level (TRL) 6 (system/subsystem prototype demonstration in a relevant environment). The innovation is now available for your company to license. Please note that NASA does not manufacture products itself for commercial sale.
sensors

Split-Ring Torque Sensor
The SRTS enables measurement of position, velocity, and torque of a rotating system (e.g., actuator, motor, crankshaft, rotor, etc.) using two optical sensors and a single, custom-designed split-ring rather than the standard dual-ringed systems commonly used for similar applications. The split-ring is comprised of two structural arcs positioned in a concentric, coplanar relationship, wherein each arc is attached to a component capable of rotation (e.g., a lower leg and upper leg, where the SRTS acts as a knee). The two arcs contain indications or codes on their outer surfaces that are read by the optical sensors to determine the relative deflection of the structural arcs as they rotate.
The SRTS configuration discussed above is limited to 180-degree applications. The addition of a third structural arc and a third optical reader, however, would enable 360-degree functionality.
Tests have shown the SRTS has a high degree of tolerance to temperature differences and provides higher resolution measurements than competing technologies.
Electrical and Electronics
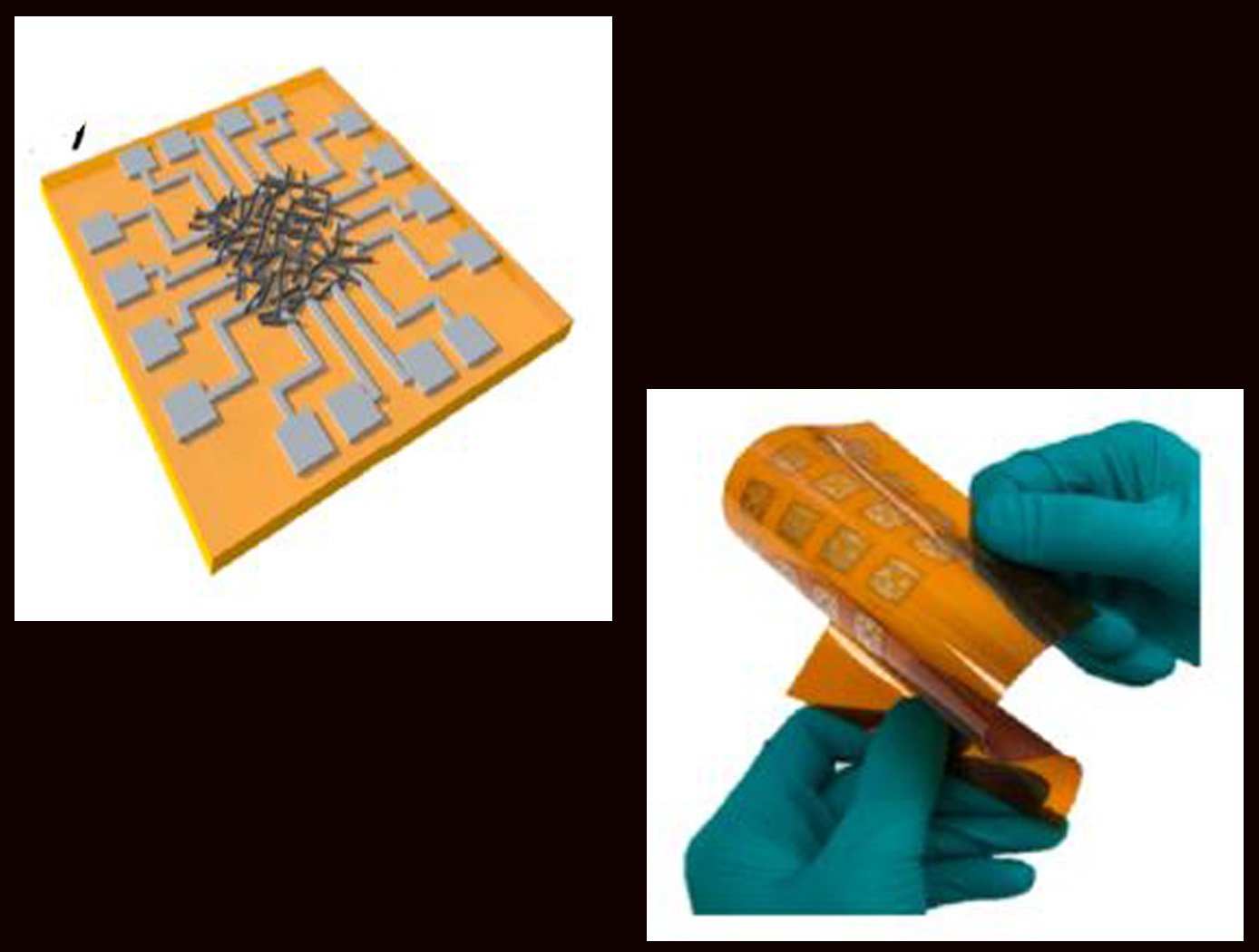
Highly secure all-printed Physically Unclonable Function (PUF) electronic device based on a nanomaterial network
The technology is an all-printed Physically Unclonable Function (PUF) electronic device based on a nanomaterial (such as single-walled carbon nanotube) network. The network may be a mixture of semiconducting and metallic nanotubes randomly tangled with each other through the printing process. The all-printed PUF electronic device comprises a nanomaterial ink that is inkjet deposited, dried, and randomly tangled on a substrate, creating a network. A plurality of electrode pairs is attached to the substrate around the substrate perimeter. Each nanotube in the network can be a conduction path between electrode pairs, with the resistance values varying among individual pairs and between networks due to inherent inter-device and intra-device variability. The unique resistance distribution pattern for each network may be visualized using a contour map based on the electrode information, providing a PUF key that is a 2D pattern of analog values. The PUF security keys remain stable and maintain robustness against security attacks. Although local resistance change may occur inside the network (e.g., due to environmental impact), such change has little effect on the overall pattern. In addition, when a network-wide resistance change occurs, all resistances are affected together, so that the unique pattern is maintained.
Robotics Automation and Control

Upper Body Robotic Exoskeleton
NASA's soft, portable, wearable robotic device is "plug and play" - it includes all necessary electronics, actuation, software, and sensors required to achieve augmented limb movement. The garment is designed such that the human-robot interface distributes load across the torso, maximizing user comfort. Donning and doffing is simple, as the device lowers over the head, straps to the torso via Velcro, and possesses adjustable custom arm cuffs. Actuators are housed in the back of the garment, which pull custom conduit-tendon-based systems attached to the limb at optimized locations, causing the joint of interest to move to the specified orientation. Force sensing is employed to enable optimal control of the limb, measuring user-applied force to maintain commanded joint orientations. Integrated electronics and software provide power distribution, safety monitoring, data transfer and data logging.
NASA's garment has multiple modes of operation. In active assist mode, shoulder abduction and flexion, and elbow flexion, may be commanded either simultaneously via coordinated control or individually while holding position/orientation of the other joints. In passive assist mode, the user can freely move the limb while the system provides minimal torque to the shoulder and elbow.
The upper body robotic exoskeleton is at a TRL 6 (system/subsystem prototype demonstration in a relevant environment) and it is now available for your company to license and develop into a commercial product. Please note that NASA does not manufacture products itself for commercial sale.