Search
Aerospace
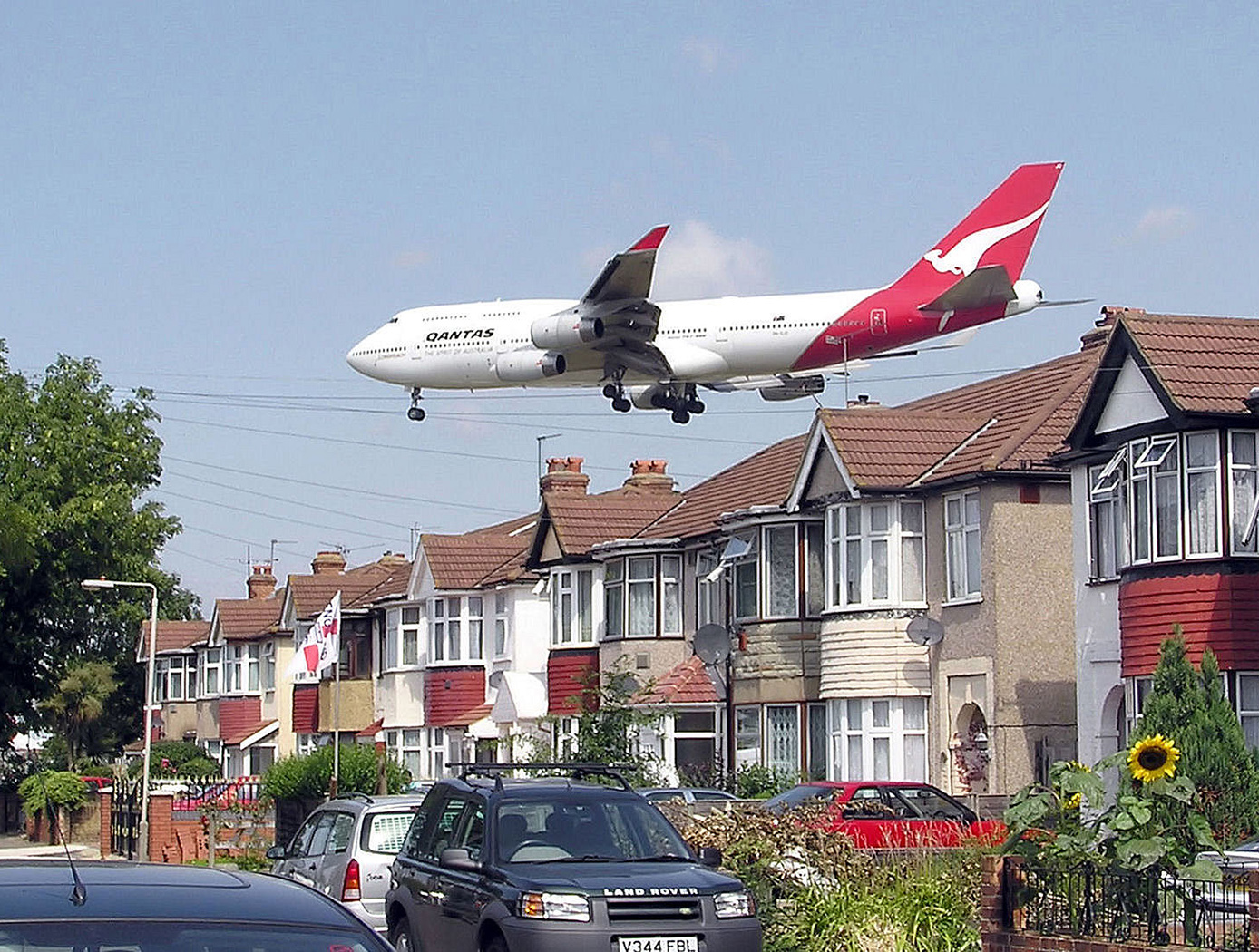
Compact, Lightweight, CMC-Based Acoustic Liner
NASA researchers are extending an existing oxide/oxide CMC sandwich structure concept that provides mono-tonal noise reduction. That oxide/oxide CMC has a density of about 2.8 g/cc versus the 8.4 g/cc density of a metallic liner made of IN625, thus offering the potential for component weight reduction. The composites have good high-temperature strength and oxidation resistance, allowing them to perform as core liners at temperatures up to 1000°C (1832°F). NASA's innovation uses cells of different lengths or effective lengths within a compact CMC-based liner to achieve broadband noise reduction. NASA has been able to optimize the performance of the proposed acoustic liner by using improved design tools that help reduce noise over a specified frequency range. One such improvement stems from the enhanced understanding of variable-depth liners, including the benefits of alternate channel shapes/designs (curved, bent, etc.). These new designs have opened the door for CMC-based acoustic liners to offer core engine noise reduction in a lighter, more compact package. As a first step toward demonstrating advanced concepts, an oxide/oxide CMC acoustic testing article with different channel lengths was tested. Bulk absorbers could also be used, either in conjunction with or in place of the liners internal chambers, to reduce noise further if desired.
instrumentation

Data Transfer for Multiple Sensor Networks
High-temperature sensors have been used in silicon carbide electronic oscillator circuits. The frequency of the oscillator changes as a function of changes in the sensor's parameters, such as pressure. This change is analogous to changes in the pitch of a person's voice. The output of this oscillator, and many others may be superimposed onto a single medium. This medium may be the power lines supplying current to the sensors, a third wire dedicated to data transmission, the airwaves through radio transmission, or an optical or other medium. However, with nothing to distinguish the identities of each source, this system is useless. Using frequency dividers and linear feedback shift registers, comprised of flip flops and combinatorial logic gates connected to each oscillator, unique bit stream codes may be generated. These unique codes are used to amplitude modulate the output of the sensor (both amplitude shift keying and on-off keying are applicable). By using a dividend of the oscillator frequency to generate the code, a constant a priori number of oscillator cycles will define each bit. At the receiver, a detected frequency will have associated with it a stored code pattern. Thus, a detected frequency will have a unique modulation pattern or "voice," disassociating it from noise and from other transmitting sensors. These codes may be pseudorandom binary sequences (PRBS), ASCII characters, gold codes, etc. The detected code length and frequency are measured, offering intelligent data transfer.
This is an early-stage technology requiring additional development. Glenn welcomes co-development opportunities.
Materials and Coatings

Silicon Carbide (SiC) Fiber-Reinforced SiC Matrix Composites
Aimed at structural applications up to 2700°F, NASA's patented technologies start with two types of high-strength SiC fibers that significantly enhance the thermo-structural performance of the commercially available boron-doped and sintered small-diameter “Sylramic” SiC fiber. These enhancement processes can be done on single fibers, multi-fiber tows, or component-shaped architectural preforms without any loss in fiber strength. The processes not only enhance every fiber in the preforms and relieve their weaving stresses, but also allow the preforms to be made into more shapes. Environmental resistance is also enhanced during processing by the production of a protective in-situ grown boron-nitride (iBN) coating on the fibers. Thus the two types of converted fibers are called “Sylramic-iBN” and “Super Sylramic-iBN”.
For high CMC toughness, two separate chemical vapor infiltration (CVI) steps are used, one to apply a boron nitride coating on the fibers of the preform and the other to form the SiC-based matrix. The preforms are then heat treated not only to densify and shrink the CVI BN coating away from the SiC matrix (outside debonding), but also to increase its creep resistance, temperature capability, and thermal conductivity.
One crucial advantage in this suite of technologies lies in its unprecedented customizability. The SiC/SiC CMC can be tailored to specific conditions by down-selecting the optimum fiber, fiber coating, fiber architecture, and matrix materials and processes. In any formulation, though, the NASA-processed SiC fibers display high tensile strength and the best creep-rupture resistance of any commercial SiC fiber, with strength retention to over 2700°F.
materials and coatings
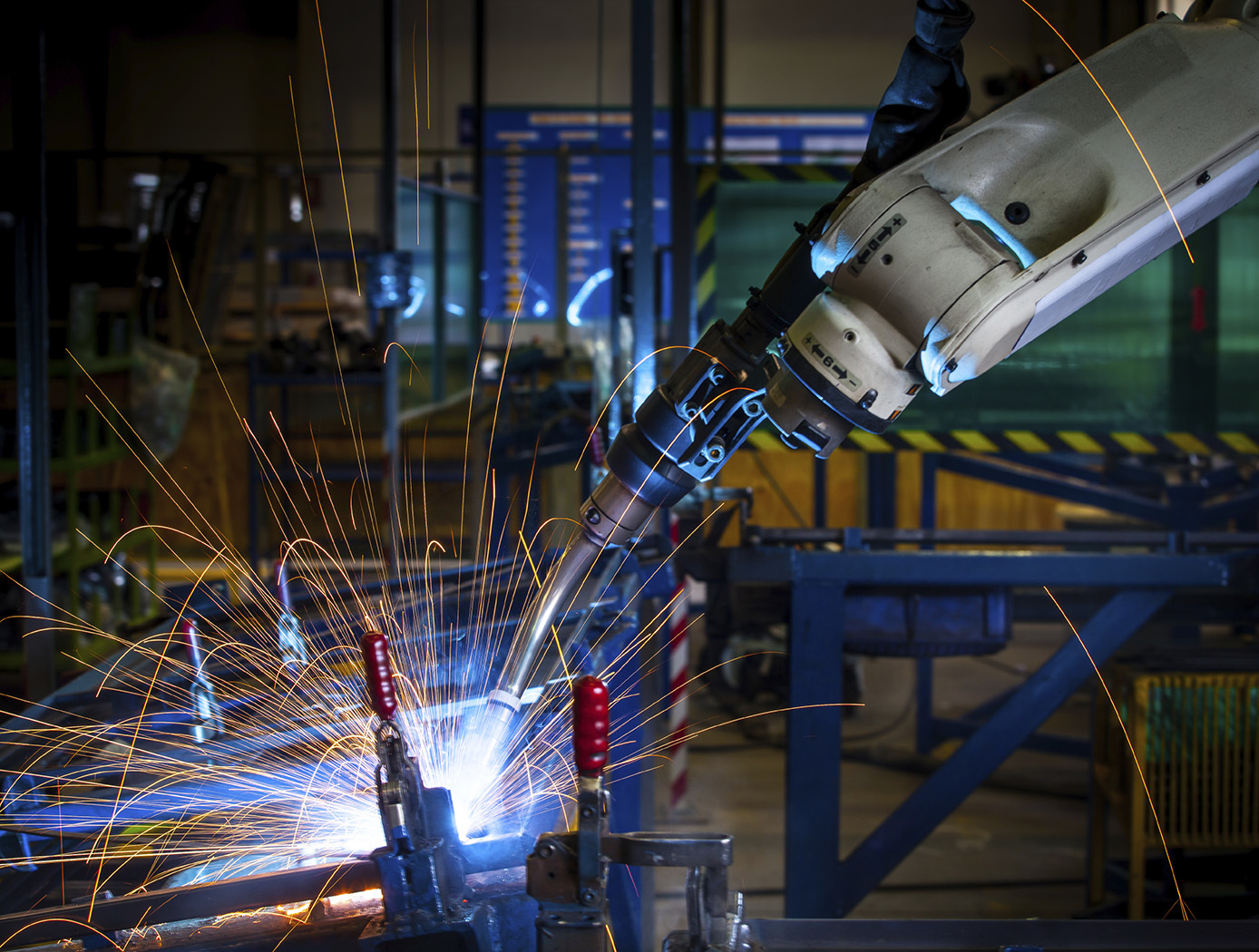
How to Train Shape Memory Alloys
Glenn researchers have optimized how shape memory alloys (SMAs) are trained by reconceptualizing the entire stabilization process. Whereas prior techniques stabilize SMAs during thermal cycling, under conditions of fixed stress (known as the isobaric response), what Glenn's innovators have done instead is to use mechanical cycling under conditions of fixed temperature (the isothermal response) to achieve stabilization rapidly and efficiently. This novel method uses the isobaric response to establish the stabilization point under conditions identical to those that will be used during service. Once the stabilization point is known, a set of isothermal mechanical cycling experiments is then performed using different levels of applied stress. Each of these mechanical cycling experiments is left to run until the strain response has stabilized. When the stress levels required to achieve stabilization under isothermal conditions are known, they can be used to train the material in a fraction of the time that would be required to train the material using only thermal cycling. As the strain state has been achieved isothermally, the material can be switched back under isobaric conditions, and will remain stabilized during service. In short, Glenn's method of training can be completed in a matter of minutes rather than in days or even weeks, and so SMAs become much more practical to use in a wide range of applications.
materials and coatings
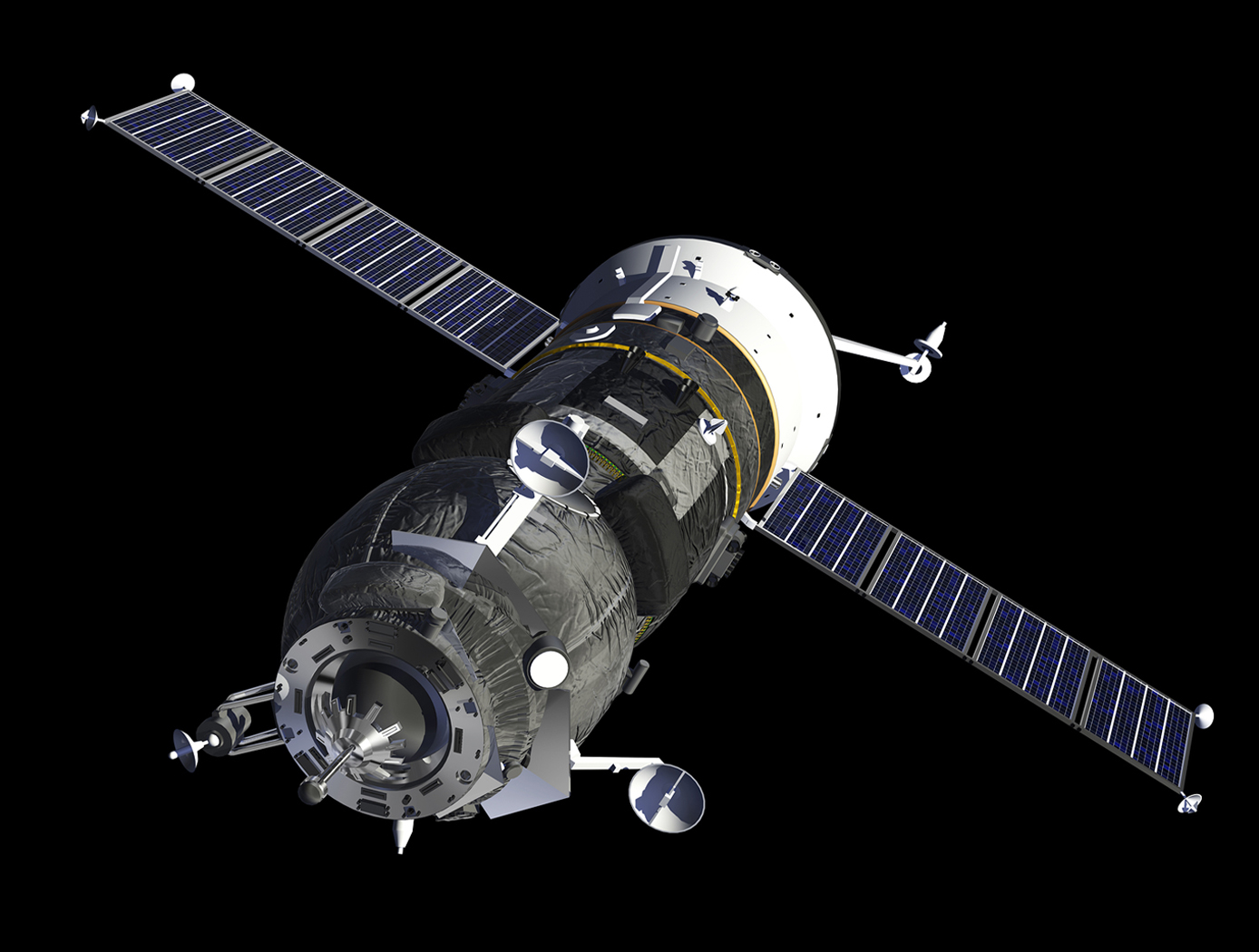
Thermal protection supplement for reducing interface thermal mismatch
The invention includes an exposed surface cap with a specially formulated coating, an insulator base adjacent to the cap with another specially formulated coating, and one or more pins that extend from the cap through the insulator base to tie the cap and base together through ceramic bonding and mechanical attachment. The cap and insulator base have corresponding depressions and projections that mate and allow for differences in thermal expansion of the cap and base. The cap includes a high-temperature, low density, carbonaceous, fibrous material whose surface is optionally treated with a High Efficiency Tantalum-based Ceramic Composite (HETC) formulation, the fibrous material being drawn from the group consisting of silicon carbide foam and similar porous, high temperature materials. The insulator base and pin(s) contain similar material. The mechanical design is arranged so that thermal expansion differences in the component materials (e.g., cap and insulator base) are easily tolerated. It is applicable to both sharp and blunt leading edge vehicles. This extends the possible application of fibrous insulation to the wing leading edge and/or nose cap on a hypersonic vehicle. The lightweight system comprises a treated carbonaceous cap composed of Refractory Oxidation-resistant Ceramic Carbon Insulation (ROCCI), which provides dimensional stability to the outer mold line, while the fibrous base material provides maximum thermal insulation for the vehicle structure. The composite has graded surface treatments applied by impregnation to both the cap and base. These treatments enable it to survive in an aero-convectively heated environment of high-speed planetary entry. The exact cap and base materials are chosen in combination with modified surface treatments and a specially formulated surface coating, taking into account the duration of exposure and expected surface temperatures for the particular application.
mechanical and fluid systems
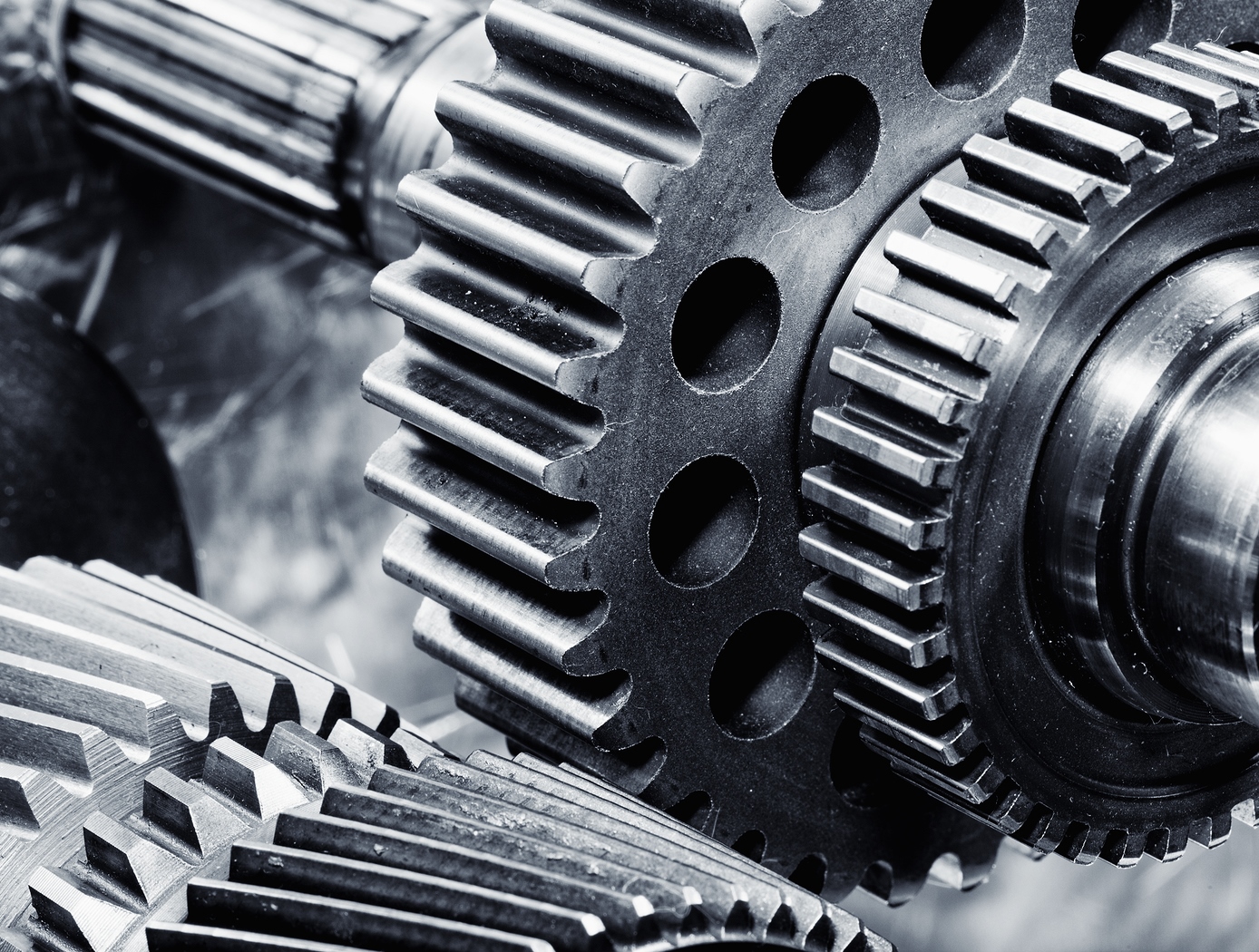
Gear Bearings
These patented gear bearings provide superior speed reduction in a small package. They form rolling friction systems that function both as gears and bearings and are compatible with most gear types, including spur, helical, elliptical, and bevel gears. These self-synchronized components can be in the form of planets, sun, rings, racks, and segments thereof. The design reduces micro chatter and eliminates rotational wobble to create smooth and precise control. It offers tighter mesh, more even gear loading, and reduced friction and wear.
Gear bearings eliminate separate bearings, inner races, and carriers, as well as intermediate members between gears and bearings. Load paths go directly from one gear bearing component to another and then to ground. By incorporating helical gear teeth forms (including herringbone), gear bearings provide outstanding thrust bearing performance. They also provide unprecedented high- and low-speed reduction through the incorporation of phase tuning. Phase tuning allows differentiation in the number of teeth that must be engaged govbetween input and output rings in a planetary gearset, enabling successful reduction ratios of 2:1 to 2,000:1. They provide smooth and accurate control with rifle-true anti-backlash. This produces a planetary transmission with zero backlash. The gear bearing technology is based on two key concepts: the roller gear bearing and the phase-shifted gear bearing. All designs are capable of efficiently carrying large thrust loads.
Existing gear systems have drawbacks including weak structures, large size, and poor reliability, as well as high cost for some types (e.g., harmon-ic drives). Gear bearings solve these problems with simpler construction, fewer parts, and superior strength.
By selecting the appropriate manufacturing method and materials, gear bearings can be tailored to benefit any application, from toys to aircraft.
mechanical and fluid systems
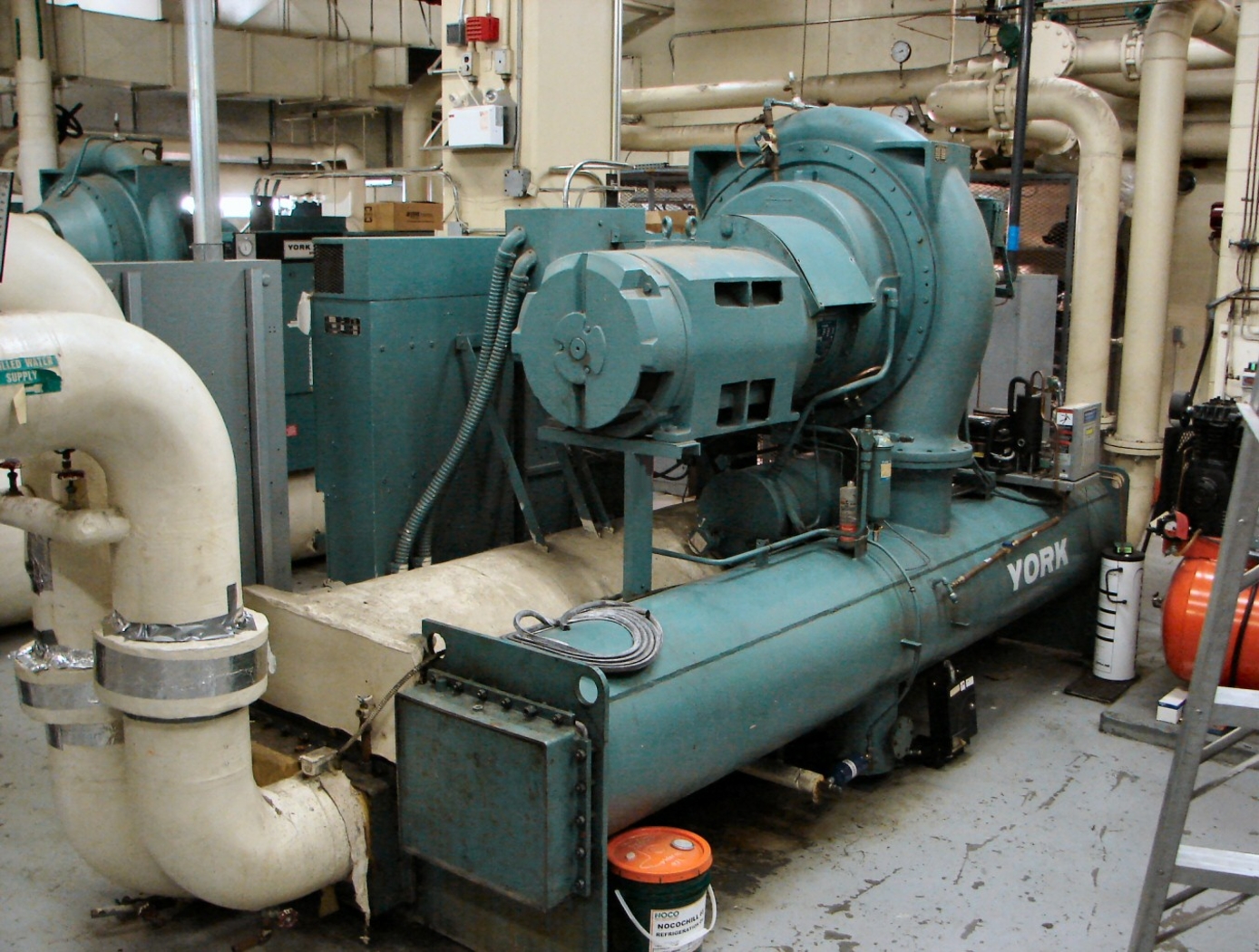
Variable-Aperture Reciprocating Reed (VARR) Valve
The VARR valve has been designed to provide a variable-size aperture that proportionately changes in relation to gas flow demand. When the pressure delta between two chambers is low, the effective aperture cross-sectional area is small, while at high delta pressure the effective aperture cross-sectional area is large. This variable aperture prevents overly restricted gas flow. As shown in the drawing below, gas flow through the VARR valve is not one way. Gas flow can traverse through the device in a back-and-forth reversing flow manner or be used in a single flow direction manner. The contour shapes and spacing can be set to create a linear delta pressure vs. flow rate or other pressure functions not enabled by current standard orifices. Also, the device can be tuned to operate as a flow meter over an extremely large flow range as compared to fixed-orifice meters. As a meter, the device is capable of matching or exceeding the turbine meter ratio of 150:1 without possessing the many mechanical failure modes associated with turbine bearings, blades, and friction, etc.