Search
sensors

Compact, Temperature-Tuned OFDR Laser
Because OFDR-based fiber interrogation systems rely upon interferometry between sensors with respect to a unique reference length, the excitation source (laser) must lase at a single longitudinal mode (SLM). If the excitation source contains multiple modes, the resulting beat frequency becomes a super-position of the multiple frequencies caused by the modes; as a result, the sensor cannot be accurately defined in the Fourier domain. For OFDR systems with high sensing ranges, a continuous wavelength tunable laser must be used to accommodate the resonant wavelength shift of the fiber sensors due to environmental changes. External cavity lasers (ECLs) have been used due to their narrow linewidth and ability to lase at a SLM with no mode-hopping between steps. However, the mechanical complexity associated with tuning, susceptibility to vibration and shock, and high price point leave much to be desired.
To overcome the limitations of OFDR-based FOSS systems resulting from non-ideal excitation sources, NASA has developed a narrow linewidth solid-state laser based on the Distributed Feedback (DFB) laser. NASAs laser is continuously tuned by manipulating the laser cavitys temperature via a thermal-electric cooler feedback system. This continuous wavelength tuning generates a clean clock signal within an auxiliary interferometer, while the laser simultaneously interrogates multiple FBGs to produce a clean sensing interferometer. A Fourier domain spectrograph is used to show the unique frequency (i.e., location) of each FBG.
While NASAs excitation source provides several performance advantages over conventional lasers used in OFDR, it is also highly compact and one eighth the cost of the ECLs traditionally used as excitation sources in OFDR-based systems. The laser has no moving parts, which also substantially improves system reliability.
Originally developed to demonstrate a low-cost interrogator for liquid level sensing in oil tanks, NASAs compact, temperature-tuned OFDR laser can be applied wherever OFDR-based fiber optic sensing is desirable. Additional applications may include temperature distribution sensing, strain sensing, pressure sensing, and more.
NASA AFRC has strong subject matter expertise in fiber optic sensing systems, and has developed several patented technologies that are available for commercial licensing. For more information about the full portfolio of FOSS technologies, visit:
https://technology-afrc.ndc.nasa.gov/featurestory/fiber-optic-sensing
manufacturing
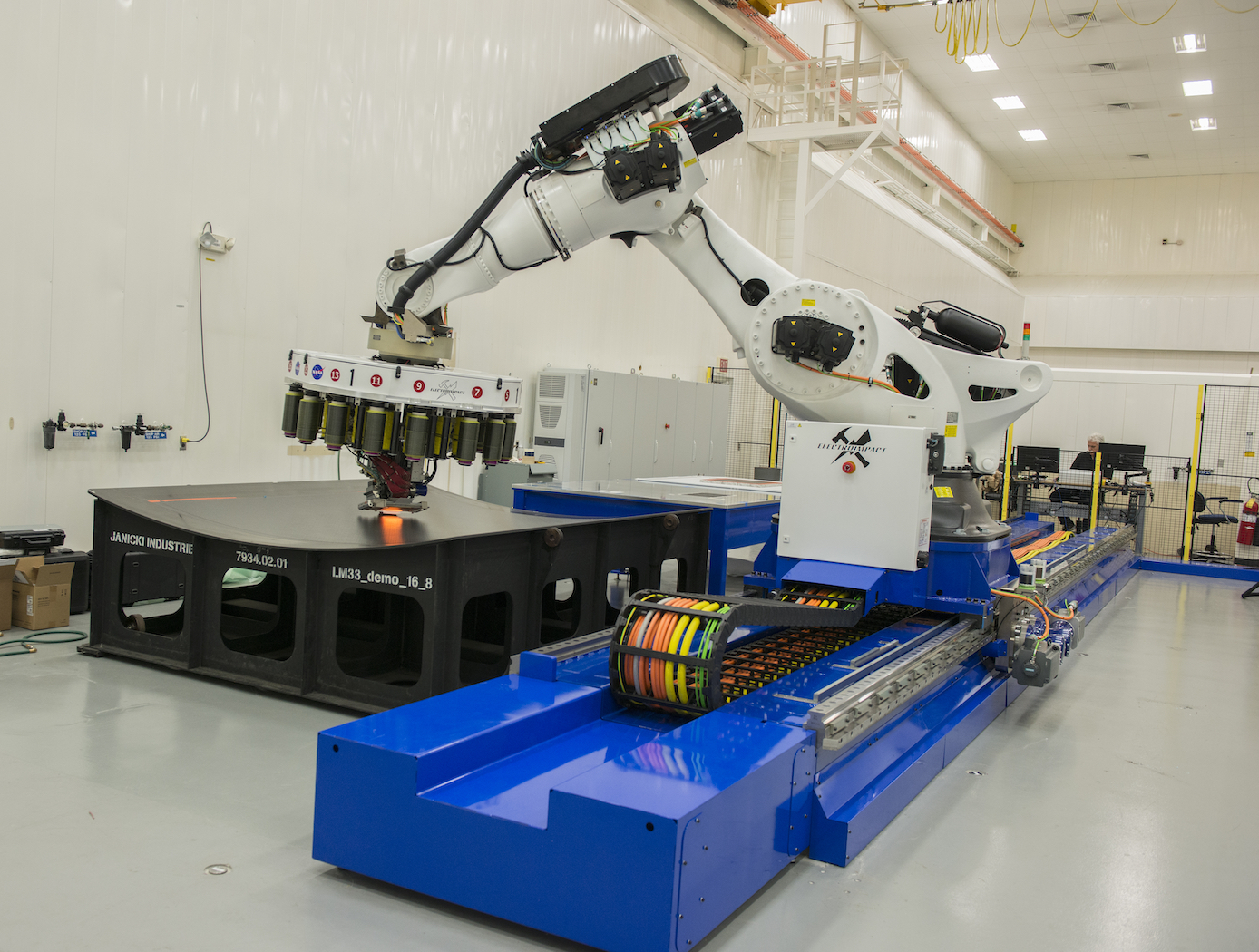
Calibration System for Automated Fiber Placement
NASA's new calibration system is a proprietary method to quickly design and make predictable and repeatable gap-and-overlap defects when employing AFP. The system creates defects within the course of layup with known sizes, geometries, and locations. Using this defect-creation technique, one can now accurately quantify the ability to detect defects on inspection systems, perform accurate risk assessments, and calibrate in-situ inspection equipment to specific materials. The equipment that makes the defects can be efficiently and inexpensively 3D printed. This technique is currently being used to successfully calibrate NASA's in situ inspection system for their AFP equipment.
AFP is experiencing increasing adoption in aerospace, automotive, and other industries that leverage large-scale advanced composite components. NASA's new AFP calibration system could be very useful to companies that develop and manufacture AFP machines or AFP machine inspection equipment to improve the quality of their products in a provable manner. Furthermore, users of AFP machines may find value in the tool for creating their own calibration standards.
power generation and storage
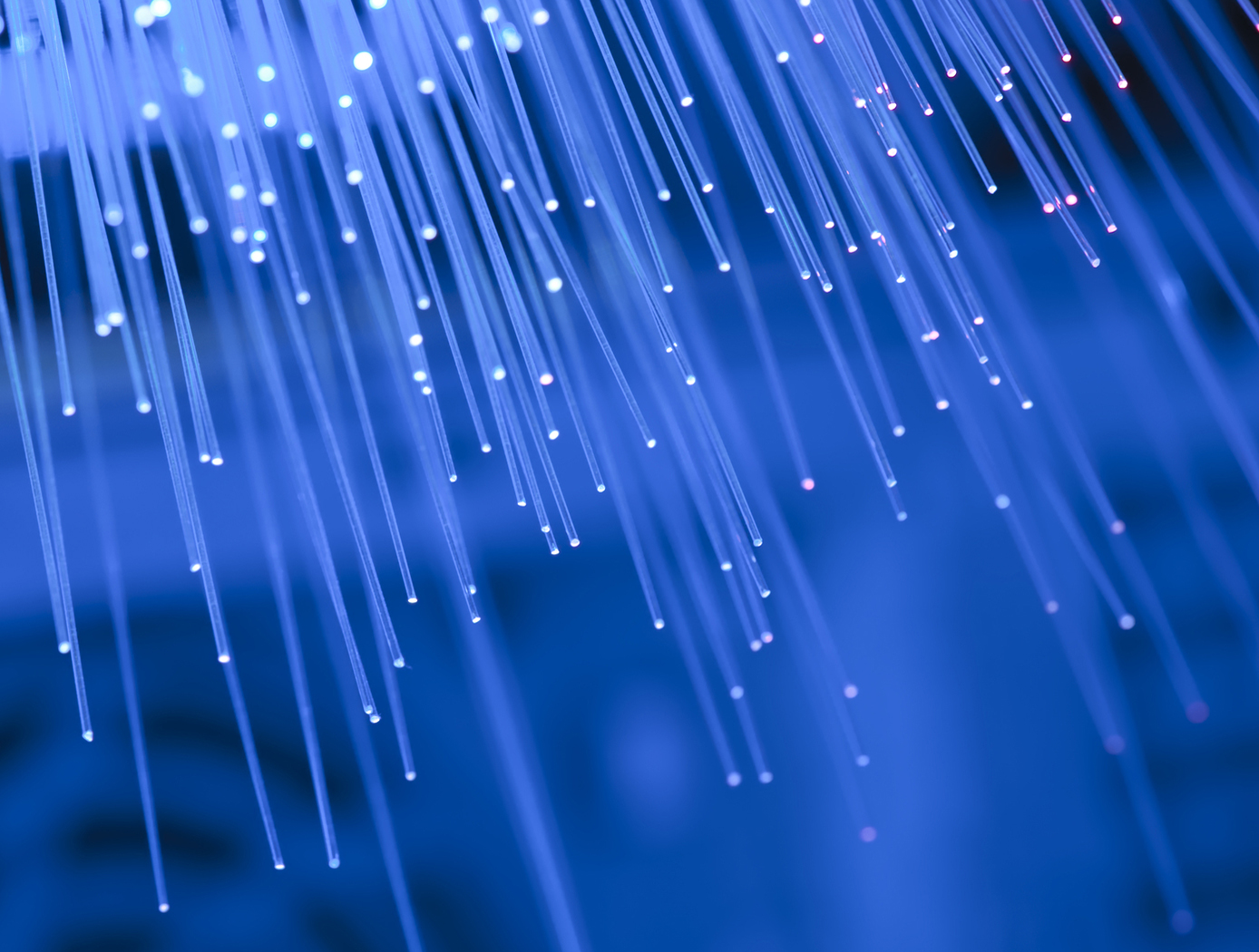
Optimum Solar Conversion Cell Configurations
A solar cell manufactured from this new optical fiber has photovoltaic (PV) material integrated into the fiber to enable electricity generation from unused light, including non-visible portions of the spectrum and visible light not transmitted to a lighting application. These new solar cells are based around cylindrical optical fibers, providing two distinct advantages over the flat panels that lead to increased efficiency. The core fiber, used to transmit light, can be adjusted to increase or decrease the amount of available light that is transmitted to the lighting application at any point in real time. This invention can be applied wherever optical concentrators are used to collect and redirect incident light. Wavelengths as large as 780 nanometers (nm) can be used to drive the conversion process. This technology has very low operating costs and environmental impacts (in particular, no greenhouse gas emissions). The fiber uses low-cost polymer materials. It is lightweight and flexible, and can be manufactured using low-cost solution processing techniques. Such multifunctional materials have great potential for the future of solar and photovoltaic devices. They will enable new devices that are small and lightweight that can be used without connection to existing electrical grids.
Materials and Coatings

Carbon Fiber-Carbon Nanotube Yarn Hybrid Reinforcement
NASA's new material is a toughened triaxial braid made from ductile carbon nanotube (CNT) yarn hybridized with carbon fiber, which is ultimately used as reinforcement material to make toughened polymer matrix composites. The CNT yarn component of the reinforcement is solely responsible for adding toughness, while the processes used to optimize the fiber braiding parameters and tensile properties of the carbon fiber-CNT yarn hybrid tow material determine the overall improvement in tensile strength for resin impregnated fiber tows. Bundles of continuous carbon nanotube yarns are combined with a similar format of carbon fiber, yielding an easily scalable process.
Advantages of the material include reduced cost by eliminating use of toughening agents, increased ability to conform to highly complex geometries, greater environmental stability compared to aramid fiber reinforcements such as Kevlar, and possibly decreased density. Many hybrid reinforcements exhibit interfacial compatibility issues, which could lead to premature failure via crack propagation at the polymer matrix interface. In contrast, chemical similarities between the CNT yarn and carbon fiber constituents impart NASA's hybrid reinforcement material with excellent interfacial compatibility.
Potential applications include aerospace components, composite pressure vessels, wind turbine blades, automotive components, prosthetics, sporting equipment, construction reinforcement material, and other use-cases where strength-to-weight ratio is of utmost importance.
materials and coatings
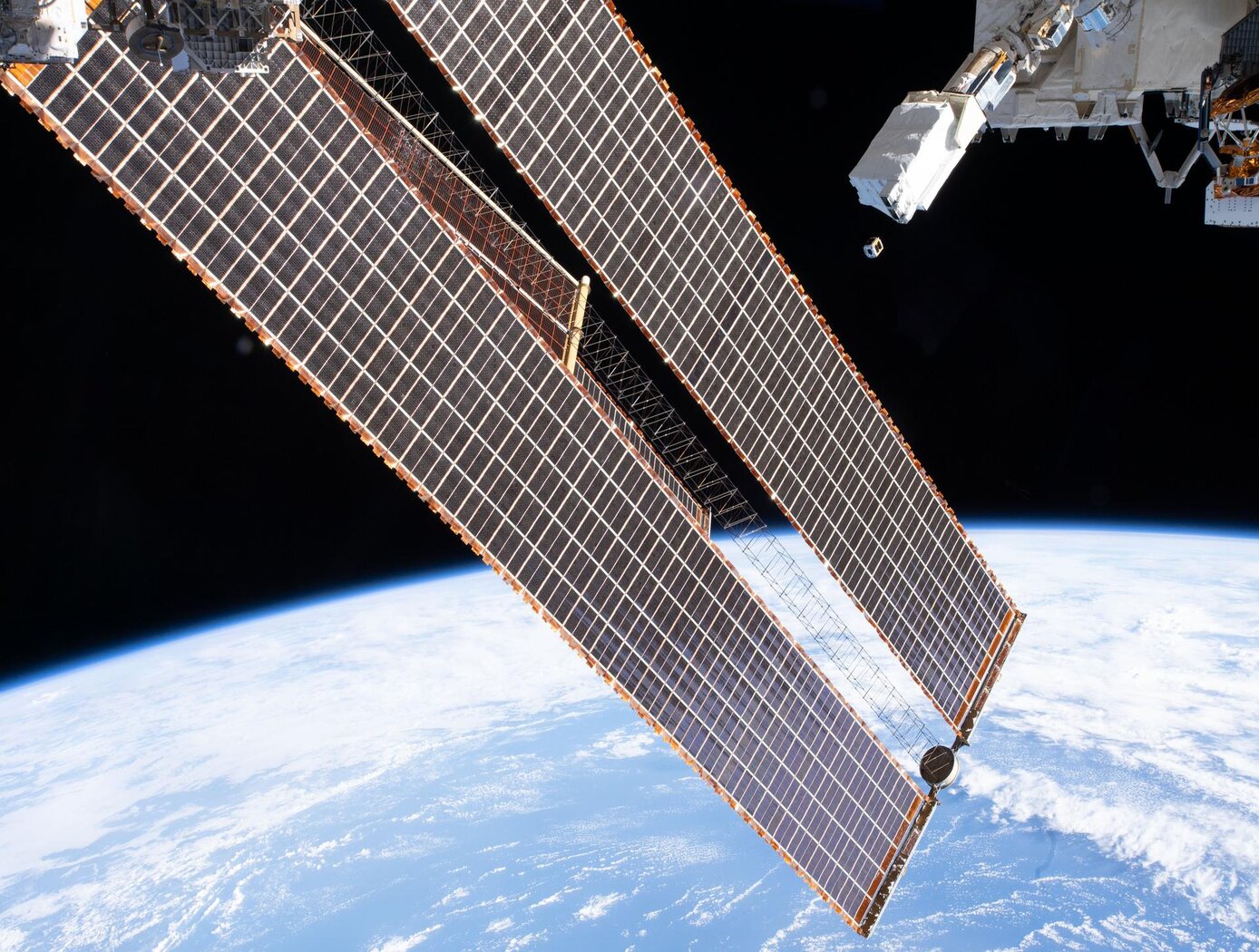
Origami-based Deployable Fiber Reinforced Composites
Deployable space structures often rely upon telescoping or folding structures that either must be manually deployed or deployed by attached motors. These structures are often made from heavier (relative to carbon fiber composites) metals to provide enough strength to support a load. As such, there is a need for in-space structures that are lightweight, can be packaged compactly, and can be deployed easily.
The composite material developed here does not require high temperature baking to cure the polymer, rather relying on UV light to solidify the polymer component. The composite is then included into origami-based structures that can fold and deploy using the polymer shape memory effect. The composite is first trained to assume the deployed structural shape when heated; it is then folded like origami and frozen into the packaged shape for storage and launch. Combining the composite material with the origami-inspired design leads to high strength structures (can hold at least 600 kg on Earth). To date, a ~5-inch prototype structural bar has been produced using the UV-curable composite and further development is on-going at NASA Langley.
The deployable origami composite structures are at technology readiness level (TRL) 4 (component and/or breadboard validation in laboratory environment) and are available for patent licensing.
materials and coatings

Conductive Carbon Fiber Polymer Composite
The new composite developed by NASA incorporates PGS and CNTs to enhance its thermal conductivity while preserving the mechanical properties of the underlying carbon fiber polymer composite. NASA has also improved the composite manufacturing process to ensure better thermal conductivity not only on the surface, but also through the thickness of the material. This was achieved by adding perforations that enable the additives to spread through the composite.
The process for developing this innovative, highly thermally conductive hybrid carbon fiber polymer composite involves several steps. Firstly, a CNT-doped polymer resin is prepared to improve the matrix's thermal conductivity, which is then infused into a carbon fiber fabric. Secondly, PGS is treated to enhance its mechanical interface with the composite. Thirdly, perforation is done on the pyrolytic graphite sheet to improve the thermal conductivity through the thickness of the material by allowing CNT-doped resin to flow and better interlaminar mechanical strength. Finally, the layup of PGS and CNT-CF polymer is optimized.
Initial testing of the composite has shown significant increases in thermal conductivity compared to typical carbon fiber composites, with a more than tenfold increase. The composite also has higher thermal conductivity than aluminum alloys, with more than twice the thermal conductivity of the Aluminum 6061 typically used in the aerospace industry. For this new material, NASA has completed a proof-of-concept demonstration and work continues to use the material in a heat exchanger system and further characterize the properties including longevity and radiation impact analysis.
communications

Optical De-Multiplexing Method for QKD Encryption
Classical laser communication gimbals are coupled to 105um multimodal receiving fibers for the high-power transmission of data, fine pointing, and tracking. These fibers cannot be used in free space optical communication applications using Quantum Key Distribution (QKD) since polarization state information encoded by QKD photons is not retained. To accommodate low energy QKD photons and high energy data streams necessary for encryption of optical links, the inventor adopted a space-and-wave (SAW) division de-multiplexing approach.
The SAW division method uses a double clad fiber with a 9um core and a 105um 1st cladding. This arrangement captures 1590nm wavelength QKD photons in the core channel and a 1555.75nm wavelength data channel in the 1st cladding. By defining wavelength separation between 30-40nm, a single focusing lens can be used to focus only one wavelength to a diffraction limited spot (see figures included). Using this method, a QKD channel is focused to a diffraction limited spot on the 9um core of the double clad fiber. The chosen wavelength separation generates a defocused diffraction pattern with a hollow center, and with remaining optical power in concentric rings outside of the 9um core, yet inside the 105um core. The QKD signal is directed into the 9um core, and the data channel is coupled into the 105um secondary core for traditional data demodulation.
Communications

Boosting Quantum Communication Efficiency
The technology consists of an array of quantum photon sources connected via a sophisticated switching network. This system is designed to produce single pairs of entangled photons at a high rate while actively suppressing the generation of multiple pairs. The key innovation lies in its ability to detect and eliminate instances where two or more entangled photon pairs are generated, effectively reducing noise in the quantum system.
The technology operates by providing a heralding pulse that notifies the external system of successful entangled photon generation. When multiple pairs are detected, they are prevented from entering the rest of the system, thereby maintaining the integrity of the quantum information.
By combining multiple single-photon sources through its switching network, the technology not only reduces noise but also increases the overall single photon pair generation rate. This dual approach of noise reduction and increased generation efficiency improves qubit transmission rates, potentially by a factor of 10 to 100 over current methods.
While still in the early stages of development, the source array represents a significant advancement in quantum communication systems. It addresses the critical need for high-fidelity entangled photon sources, which are essential for various quantum applications, including entangling sensor networks, quantum computer networks, and quantum key distribution for secure communications.
As quantum technologies continue to evolve, this source array technology positions itself as a crucial component in the development of large-scale, efficient quantum networks, offering a solution to one of the fundamental challenges in quantum information transmission.
materials and coatings
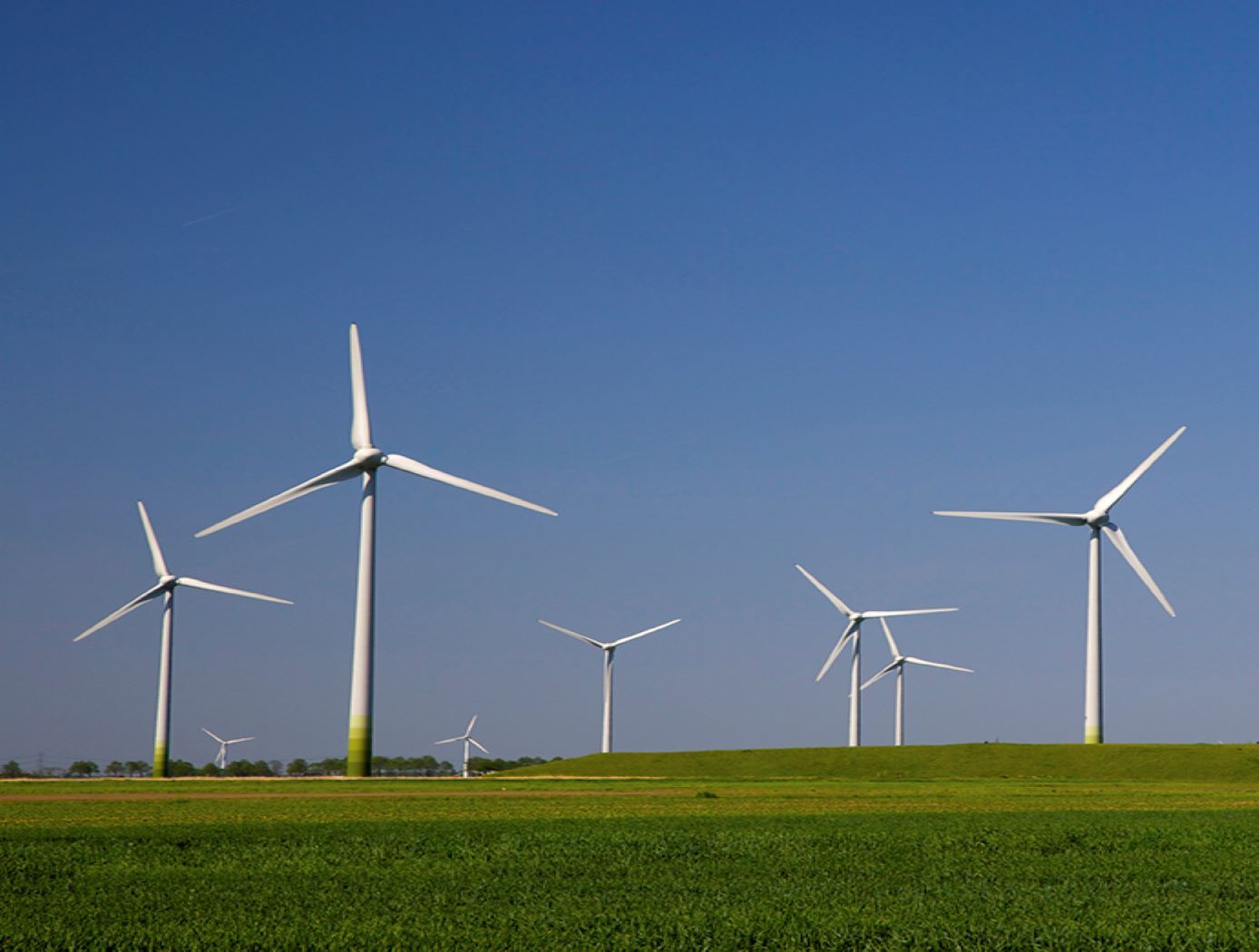
Vertically Aligned Carbon Nanotubes
Formation of the inventive polymer composite matrix begins by growing carbon nanotubes directly on a veil substrate. The carbon nanotubes are grown from both sides of a non woven carbon fiber mat. The carbon nanotubes can be single or multi walled and can be grown to predetermined lengths. The veiled substrate is positioned between carbon fiber/ polymer prepreg layers such that the carbon nanotubes protrude into the reinforcement layers. The polymer composite matrix formed following curing of the resin exhibits improved interlaminar strength, fracture toughness and impact resistance. Because of the thinness of the veil layer, electricity can pass from conductive carbon nanotubes on one side of the veil to conductive carbon nanotubes on the other side of the veil. Electricity can also pass between two veils intercalated into the same reinforcement layer when the length of the nanotubes is sufficiently long enough to provide overlap within the reinforcement layers.
Materials and Coatings

Flexible Lightweight Radiation Shielding
The thin, lightweight radiation shielding is comprised of a low Z/high Z/low Z layered structure wherein the low Z layer is composed of titanium and the high Z layer is composed of either tantalum or antimony. Modelling of radiation shielding performance from a Cobalt 57 source shows a 10 times reduction in gamma radiation when using tantalum and a 25 times reduction when using antimony as compared with a single layer of lead. In addition, the Z-shielding is 25% lighter than a single lead layer with the same thickness (0.35-0.36 mm). The direct textile spraying innovation outlined by this invention enables the ability to shape this shielding into garments via the sewing of metal coated fibers. The refractory metal shielding can be added onto a variety of commodity-based fabrics including glass fabrics.