Double-Fed Induction Linear Alternator
power generation and storage
Double-Fed Induction Linear Alternator (LEW-TOPS-114)
Ironless Stirling alternator operates efficiently at extremely high temperatures
Overview
Innovators at NASA's Glenn Research Center have developed a lightweight, double-fed induction linear alternator capable of highly efficient extreme-environment performance. While traditional linear alternators cannot withstand temperatures of 250°C, this innovation has the ability to operate at 950°C with increased performance and efficiency. The innovation replaces the traditional permanent magnet with a copper electromagnetic Halbach circular array (essentially a 3D printed copper coil). Its simple design also eliminates iron, slip rings, and - because it is fabricated as a single piece - adhesives. As a result, it is easy to maintain, does not require iron flux containment and experiences minimal electromagnetic interference. When used with the double action extremely light thermo-acoustic (DELTA) converter, the engine/alternator system is one-tenth the weight of a traditional system. This economical alternator enables unprecedented performance for high-temperature environments such as aircraft power systems, micro combined heat and power (CHP), and downhole drilling.
The Technology
This technology was developed to address the limitations of traditional, single-fed linear alternators, which require permanent magnets, adhesive bonding organics, and heavy iron laminations for flux control. They experience eddy-current losses and require electromagnetic interference protection. Furthermore, they have a limited operational temperature range (only up to 250°C), which typically declines to below 200°C as the adhesive bonding organics outgas and degrade over time. Consequently, they are limited to approximately 93% efficiency at ambient temperatures.
Glenn's novel linear alternator addresses all of the limitations of its predecessors and engenders a number of desirable new qualities - notably the ability to reduce eddy-current losses by 25% and operate at 99% efficiency at temperatures up to 950°C. It features a concentric, additively manufactured monolithic copper plunger and stator. The stator is a stationary single copper Halbach array, whereas the plunger is a moving electromagnetic copper Halbach array. A direct current is delivered through the conductive piston flexure support, which also provides reactive power for resonance. It creates a fixed magnetic field similar to that of a permanent magnet, but the magnetic field is channeled inward by the Halbach mover, doubling its strength. By utilizing standard double-fed induction control methods, the reactive power can be transferred and adjusted between both coils. This maximizes system efficiency and minimizes weight. This innovative technology will enable a new class of vastly superior linear alternators with the ability to operate at extreme temperatures with increased performance and efficiency. This is an early-stage technology requiring additional development. Glenn welcomes co-development opportunities.
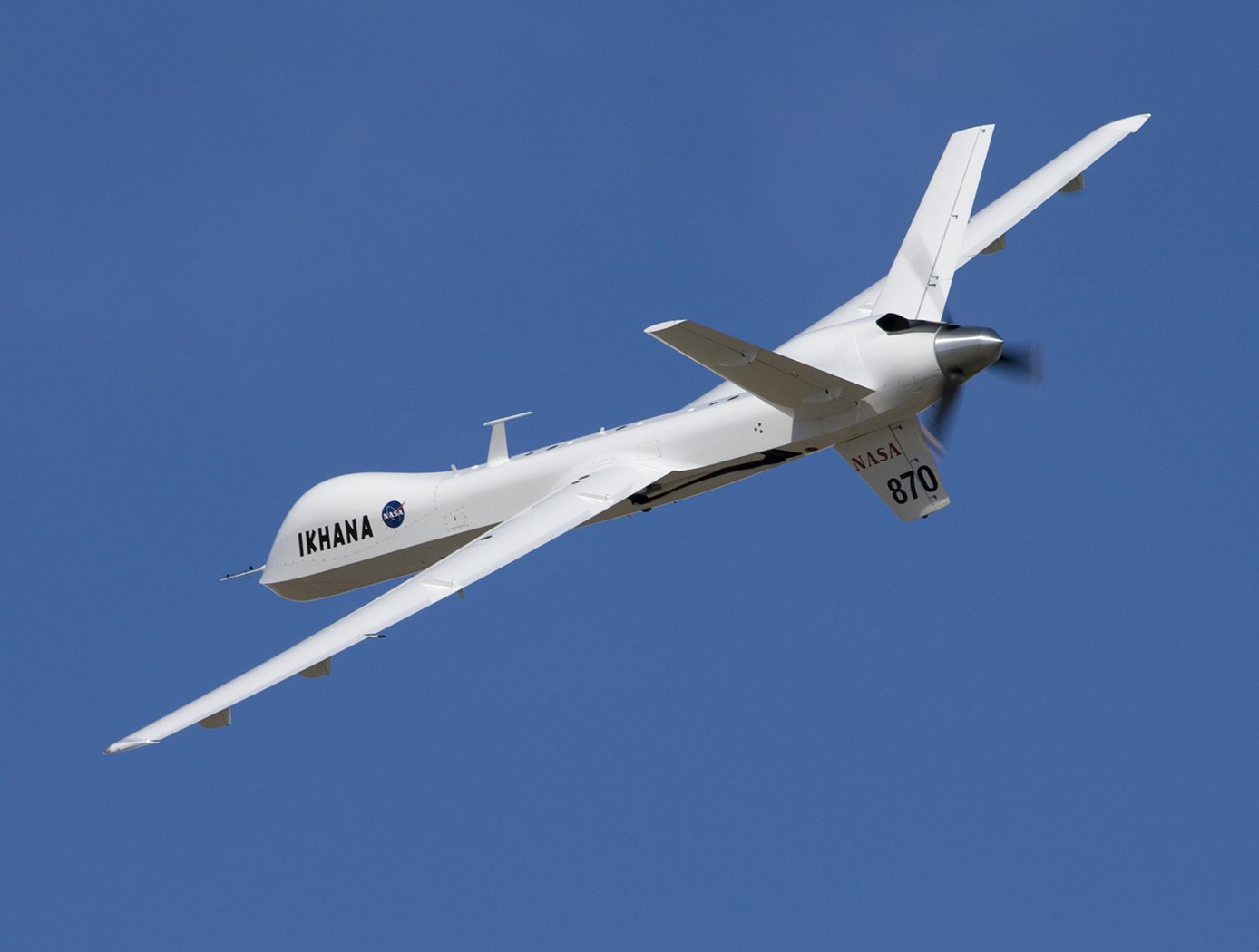

Benefits
- Compact: eliminates the need for permanent magnets, reducing size and weight
- Reliable: reduces electromagnetic interference emissions and eliminates the need for maintenance due to its simple design
- Efficient: achieves 25% greater efficiency than conventional liner alternators
- High-temperature capable: operates at temperatures up to 950°Ca 280% increase over the state-of-the-art
- Affordable: uses simple 3D printing technologies, enabling low-cost manufacturing
Applications
- Power (CHP, solar, stirling or free-piston engines, cryocoolers, auxiliary power units)
- Unmanned vehicles
- Oil and gas
- Commercial space
- Turbines
Technology Details
power generation and storage
LEW-TOPS-114
LEW-19354-1
See also LEW-TOPS-106 "Double-Acting Extremely Light Thermo-Acoustic (DELTA) Convertor"
Similar Results

High-Voltage Power System for Hybrid Electric Aircraft Propulsion
Glenn's novel system supports the NASA Aeronautics Research Mission Directorate (ARMD) strategic plan to leverage advancements in technologies over the next 25 years and beyond, leading to new aircraft configurations with enhanced performance, improved energy efficiency, and reduced CO2 emissions. The electric system is a multi-megawatt micro-grid that converts mechanical energy to electric via generators, and electric energy to mechanical via motor-driven fans. This innovation would use the variation in aircraft throttle settings to produce a high-voltage (20 kilovolts), variable-frequency 9-phase AC distribution system. Using doubly fed electric machines (generator, propulsor, and flywheel) allows for field excitation that can cause variable-frequency or variable speed operation around the commanded throttle setting. The flywheel enables an energy storage system that recovers and reuses energy, while the flywheel slews with the throttle control using the electromagnetic torque produced by the doubly fed electric machine. This design permits both sub-synchronous and super-synchronous operation using limited field excitation power provided through power converters. Finally, the reduced switchgear mass facilitated through the use of a high-frequency AC system, setting-less protection zones, and simplified switches for fault clearance provides enhanced operational capability. This system can be controlled so that fault energy is minimized, preventing collateral damage to aircraft structures even with high voltage distribution. Glenn's innovative system adds performance, efficiency, reliability, and cost savings to cutting-edge hybrid electric technology.
This is an early-stage technology requiring additional development, and Glenn welcomes co-development opportunities.

SHEAth-based Rollable LEnticular-Shaped and Low-Stiction (SHEARLESS) Composite Booms
The SHEARLESS composite boom has a rollable structure with a large moment of inertia per unit of stored height that does not suffer from shear-derived problems. The boom is fabricated from joining two independent tape-springs front-to-front with the use of a durable seamless polymer sleeve. This sleeve allows the two parts to slide past each other during the coiling/deployment process so as to minimize shear and its derived problems. The innovation enables a lightweight structure that can be stowed on a reel without appreciable shear stresses developing in its constitutive composite parts, allowing for unprecedentedly small coiling diameters for the total thickness of the structure. As demonstrated, through specific laminate design of the two inner composite parts, the SHEARLESS composite boom can also be fabricated with a special inherent feature, bi-stability, which enables designs with minimal mechanisms and aids in deployment controllability and reliability.

Automated Fabric Circuit and Antenna Fabrication
Modern production of e-textiles utilizes an embroidery technique called “e-broidery” that directly stitches circuit patterns with conductive thread onto textiles. This automated manufacturing process combines steps of e-broidery and milling to expand the application of e-textiles to high-current and high-speed uses. Manufacturing begins with two layouts of the desired conductive pattern. After assembling the layers of conductive and nonconductive materials, e-broidery is performed with the second layout and nonconductive thread to secure the layers together and designate the pattern for the conductive material. The secured assembly is transferred to an automated milling or laser cutting machine, which cuts the desired conductive pattern and releases the unneeded portions of the conductive material. The resulting e-textiles are tightly woven together, providing higher surface conductivity and impedance control. Initial comparison tests assessing the performance of fabric-based spiral antennas developed with this method, compared to conventional antennas, indicated no loss in performance across multiple metrics, including voltage standing wave ratio (VSWR), radiation pattern, and axial ratio performance.
The Method and Apparatus for Fabric Circuits and Antennas is a technology readiness level (TRL) 6 (system/subsystem prototype demonstration in a relevant environment). The innovation is now available for your company to license. Please note that NASA does not manufacture products itself for commercial sale.

Stirling Thermoacoustic Power Converter and Magnetostrictive Alternator
Glenn's thermoacoustic power converter reshapes the conventional Stirling engine from a toroidal shape into a straight colinear arrangement. Instead of relying on failure-prone mechanical inertance and compliance tubes, this design achieves acoustical resonance by using electronic components. In a typical Stirling engine, the acoustical wave travels around a toroid and reflects back, forming a standing wave. In Glenn's device, by contrast, the wave instead travels in a straight plane where a transducer receives the acoustical wave and electrical components modulate the signal. A second transducer on the diametrically opposed side reintroduces the acoustic wave with the correct phasing to achieve amplification and resonance. Glenn's design allows the transducers to operate at high frequency while presenting a mass rather than stiffness impedance.
Glenn's magnetostrictive alternator uses stacked magnetostrictive materials under a biased magnetic and stress-induced compression. The acoustic energy from the engine travels through an impedance-matching layer (which can be formed from aerogel materials) that is physically connected to the magnetostrictive mass. Compression bolts keep the structure under compressive strain, allowing for the micron-scale compression of the magnetostrictive material and eliminating the need for bearings. The alternating compression and expansion of the magnetostrictive material creates an alternating magnetic field that then induces an electric current in a coil wound around the stack. This alternator produces electrical power from the acoustic pressure wave and, when the resonant frequency is tuned to match the engine, can replace the linear alternator to great effect.

Fuel Cell Power Management
In general, individual fuel cells produce relatively small electrical potentials, so fuel cells are "stacked" or placed in series (anode to cathode) to increase the combined voltage and meet the application's requirements. The current is drawn off by connection points, which typically are at the extreme ends of the fuel cell stack. DC power converters reduce or boost the voltage produced at the ends of the stack into a voltage that can be used by attached device. However, these converters add cost, mass, volume, and potential failure points into the fuel cell system.
With NASA Glenn's groundbreaking technique, the fuel cell stack includes a plurality of connection points to the device instead of having a fixed number of individual fuel cells. By connecting additional cells in the same stack to the device the system power can be to be tailored to produce the required voltage for the connected device. Initially, this plurality includes a ground, a first connection point, and a second connection point. Additional connection points to the device can be added as needed, resulting in various powers that are available for use. Each connection point allows power to be drawn the combined voltages of the fuel cells located between the connection point and the ground. This configuration permits the voltage to be adjusted to the system power requirements of the device without the need to add DC power converters to the fuel cell system to add additional fuel cell systems to meet the power demand of the device. For larger fuel cell configurations in particular, NASA's innovative technique results in a far less costly, more efficient means of power generation.