Search
Information Technology and Software
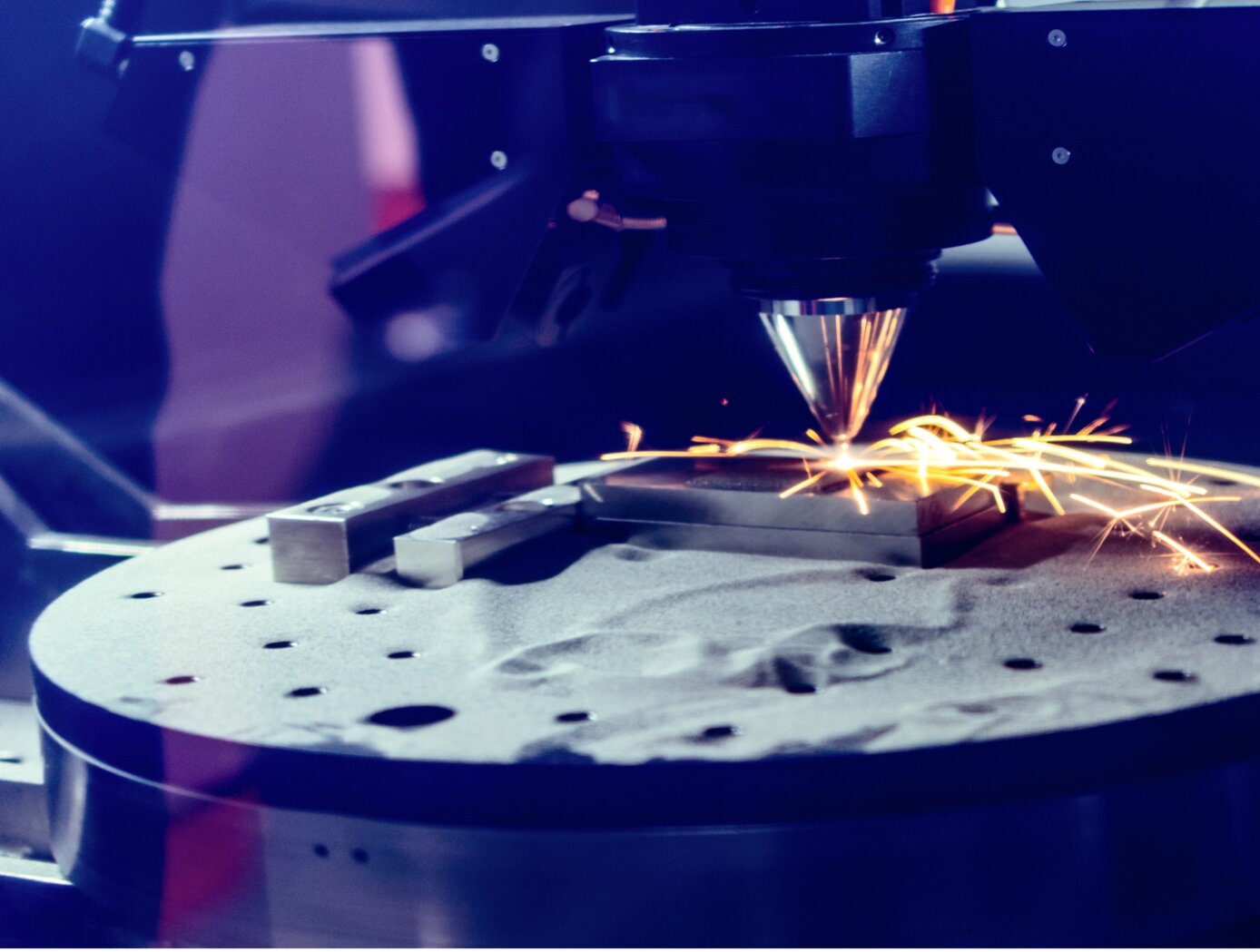
Additive Manufacturing Model-based Process Metrics (AM-PM)
Modeling additive manufacturing processes can be difficult due to the scale difference between the active processing point (e.g., a sub-millimeter melt pool) and the part itself. Typically, the tools used to model these processes are either too computationally intensive (due to high physical fidelity or inefficient computations) or are focused solely on either the microscale (e.g., microstructure) or macroscale (e.g., cracks). These pitfalls make the tools unsuitable for fast and efficient evaluations of additive manufacturing build files and parts.
Failures in parts made by laser powder bed fusion (L-PBF) often come when there is a lack of fusion or overheating of the metal powder that causes areas of high porosity. AM-PM uses a point field-based method to model L-PBF process conditions from either the build instructions (pre-build) or in situ measurements (during the build). The AM-PM modeling technique has been tested in several builds including a Ti-6Al-4V test article that was divided into 16 parts, each with different build conditions. With AM-PM, calculations are performed faster than similar methods and the technique can be generalized to other additive manufacturing processes.
The AM-PM method is at technology readiness level (TRL) 6 (system/subsystem model or prototype demonstration in a relevant environment) and is available for patent licensing.
mechanical and fluid systems
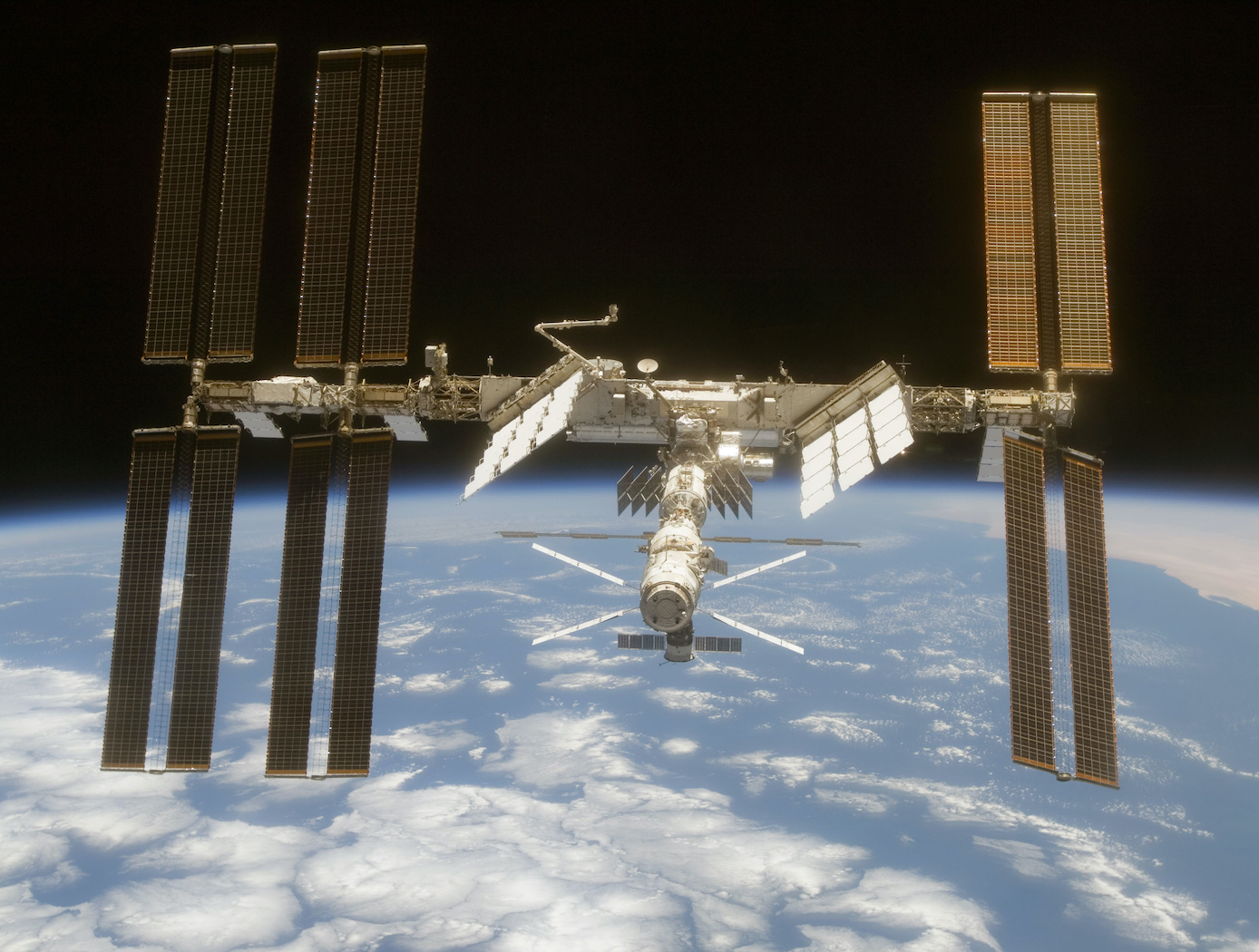
Liquid Sorbent Carbon Dioxide Removal System
NASA's Liquid Sorbent Carbon Dioxide Removal System was designed as an alternative to the current CO2 removal technology used on the International Space Station (ISS), which uses solid zeolite media that is prone to dusting, has a low absorption capacity, and requires high regeneration temperatures and frequent maintenance. Motivated by CO2 removal systems on submarines, NASA innovators began investigating the use of liquid sorbents. Liquid sorbents have a capacity four times greater than solid zeolites, require low regeneration temperature, and need fewer unreliable moving mechanical parts than solid based systems. While submarine CO2 scrubbers spray an adsorbing chemical directly into the air stream and allow the liquid to settle, NASA's new system uses a capillary driven 3D printed microchannel direct air/liquid contactor in a closed loop system. The Liquid Sorbent Carbon Dioxide Removal System is robust and reliable, while being low in weight, volume, and power requirements. The system is capable of reaching equilibrium when the liquid sorbent surface is being regenerated at a rate equal to the rate of absorption into the liquid.
Environment

TerraROVER
The TerraROVER’s core functionality is centered around its electric propulsion system, enabling it to traverse various outdoor environments. Its drive system consists of electric motors and gearboxes that provide controlled speed and maneuverability. The remote-control interface allows users to adjust speed and direction, making it an effective platform for training and testing mobility systems. For advanced applications, the TerraROVER can be adapted for pre-programmed or autonomous navigation, expanding its use in robotics and automation research.
A key design feature of the TerraROVER is its adaptability for sensor integration. It includes mounting provisions for miniaturized sensors capable of capturing environmental data such as temperature, GPS location, and visual imagery. The platform supports both onboard data logging and real-time transmission, making it suitable for field studies, distributed sensing applications, and educational experiments. Fabrication is streamlined through the use of 3D-printed components, allowing for cost-effective production and easy assembly in classroom or research settings. Currently at Technology Readiness Level (TRL) 7, the system has been successfully demonstrated in an operational environment and is available for patent licensing.
materials and coatings
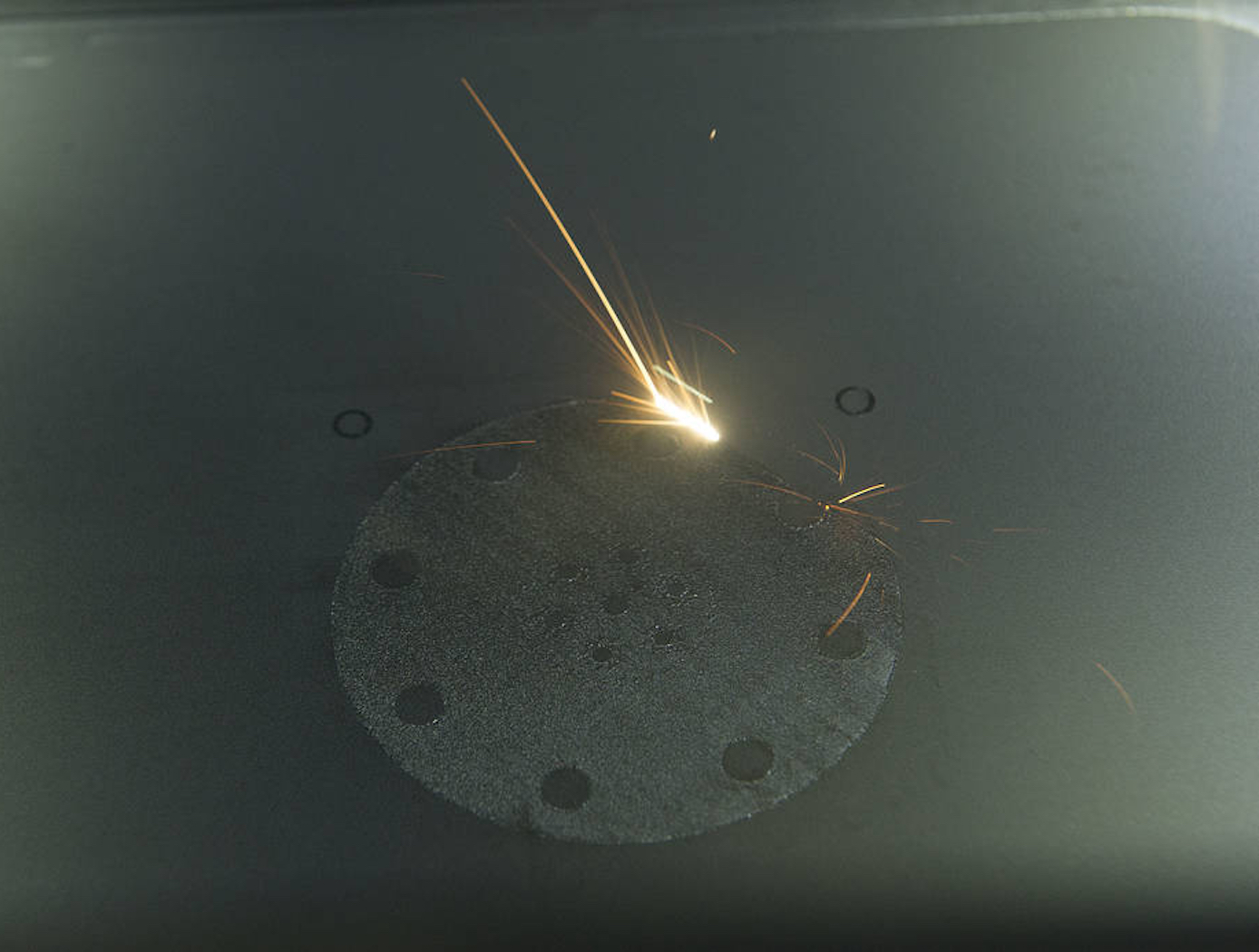
3D-Printed Composites for High Temperature Uses
NASA's technology is the first successful 3D-printing of high temperature carbon fiber filled thermoset polyimide composites. Selective Laser Sintering (SLS) of carbon-filled RTM370 is followed by post-curing to achieve higher temperature capability, resulting in a composite part with a glass transition temperature of 370 °C.
SLS typically uses thermoplastic polymeric powders and the resultant parts have a useful temperature range of 150-185 °C, while often being weaker compared to traditionally processed materials. Recently, higher temperature thermoplastics have been manufactured into 3D parts by high temperature SLS that requires a melting temperature of 380 °C, but the usable temperature range for these parts is still under 200 °C.
NASA's thermoset polyimide composites are melt-processable between 150-240 °C, allowing the use of regular SLS machines. The resultant parts are subsequently post-cured using multi-step cycles that slowly heat the material to slightly below its glass transition temperature, while avoiding dimensional change during the process. This invention will greatly benefit aerospace companies in the production of parts with complex geometry for engine components requiring over 300 °C applications, while having a wealth of other potential applications including, but not limited to, printing legacy parts for military aircraft and producing components for high performance electric cars.
manufacturing
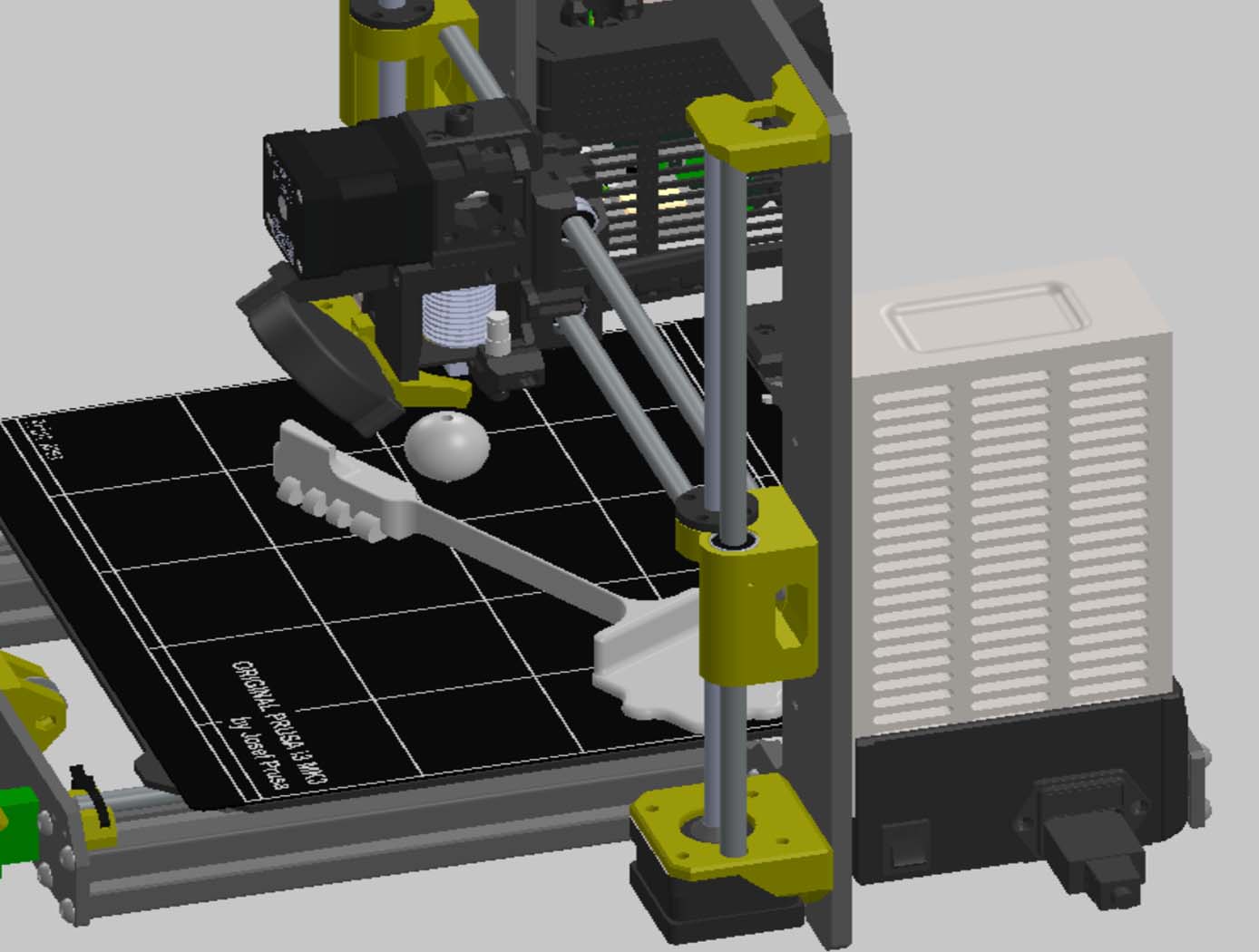
Fully Automated High-Throughput Additive Manufacturing
The technology is a method to increase automation of Additive Manufacturing (AM) through augmentation of the Fused Filament Fabrication (FFF) process. It can significantly increase the speed of 3D printing by automating the removal of printed components from the build platform without the need for additional hardware, which increases printing throughput. The method can also be leveraged to perform automated object testing and characterization. The method includes embedding into the manufacturing instructions methods to fabricate directly onto the build platform an actuator tool, such as a linear spring. The deposition head can be leveraged as a robotic manipulator of the actuator tool to bend, cock, and release the linear spring to strike the target manufactured object and move it off the build platform of the machine they were manufactured on. The ability for an object to 'fly off of the machine that made it' essentially enables automated clearing of the processed build volume. The technology can also be used for testing the AM machine or the feedstock material by successively fabricating prototypes of the manufactured object, and taking measurements from sensors as the actuator strikes the prototype. This provides automated testing for quality control, machine calibration, material origins, and counterfeit detection.
Robotics Automation and Control
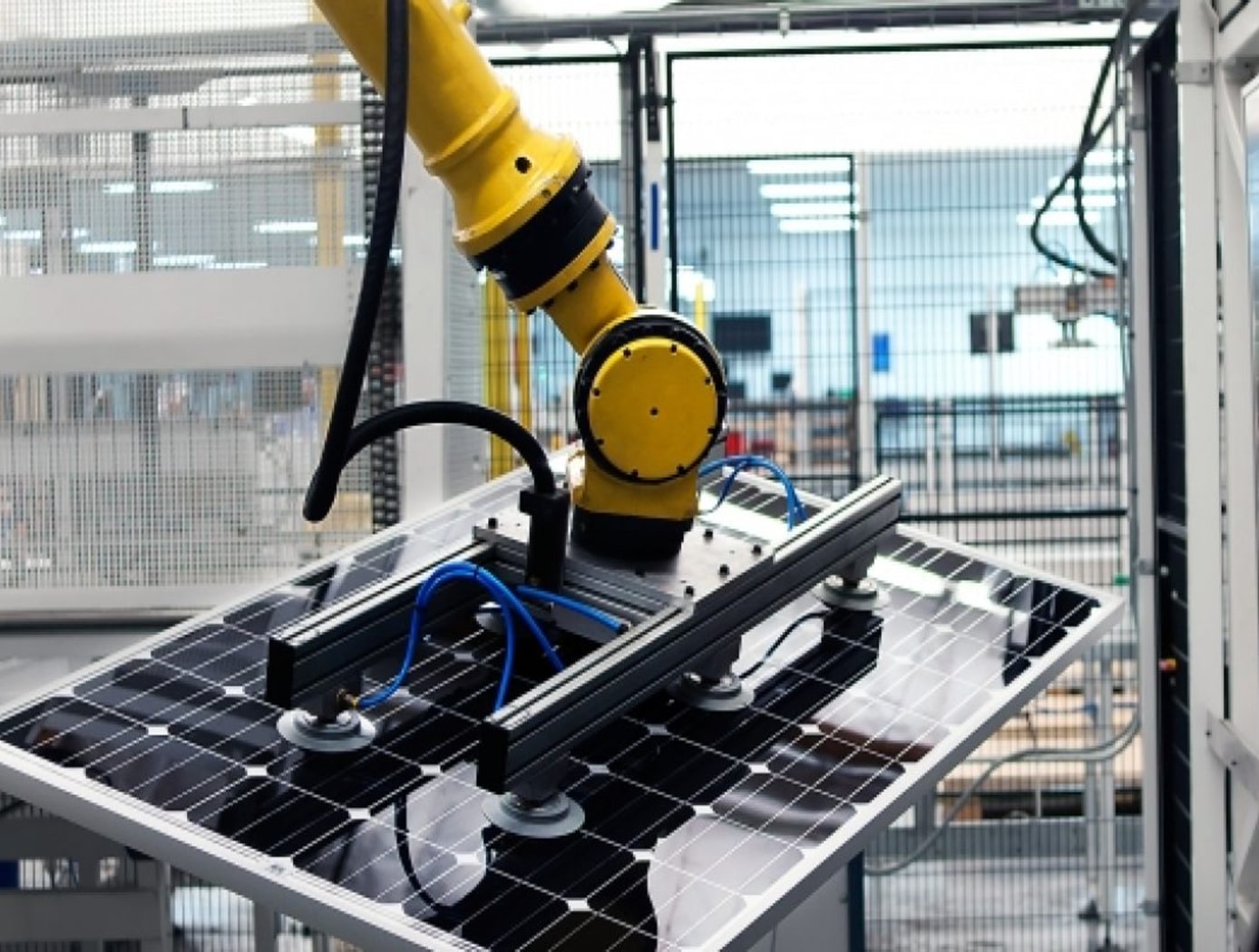
Robotic Assembly of Photovoltaic Arrays
NASA researchers have developed the PAPA technology to increase the efficiency of the thin-film solar array assembly process, significantly decreasing assembly time and labor costs associated with manufacturing large scale solar arrays. Traditional solar cell assembly is a labor intensive, multi-step, time-consuming process. This manual assembly will not be possible in a space environment. To enable solar array assembly in space, PAPA leverages robotic automation to distill the traditional assembly method into four fully automated steps: applying adhesive to block substrate, placing the solar cells using a vacuum tool attached to a universal robotic arm, printing the interconnects and buses to connect the cells, and applying a protective cover.
The PAPA technology is compatible with a variety of thin-film solar cells, including 3D printed cells (essential for future in-space manufacturing of arrays) and terrestrial manufacturing methods. As solar cell technologies mature, PAPA will be able to incorporate advancements into the paneling process. NASA researchers have begun to employ PAPA solar array fabrication and estimate savings of $300-$400/watt. For extraterrestrial assembly of solar panels the size of a football field or larger, PAPA could result in savings of approximately $500 million; a substantial cost savings driven by standardization and efficiency in the solar array assembly process. By demonstrating increases in assembly efficiency, time and cost savings, and passing multiple environmental exposure tests, the PAPA lab protype has completed the final phases of technology development and is ready for scale-up and commercialization.
manufacturing
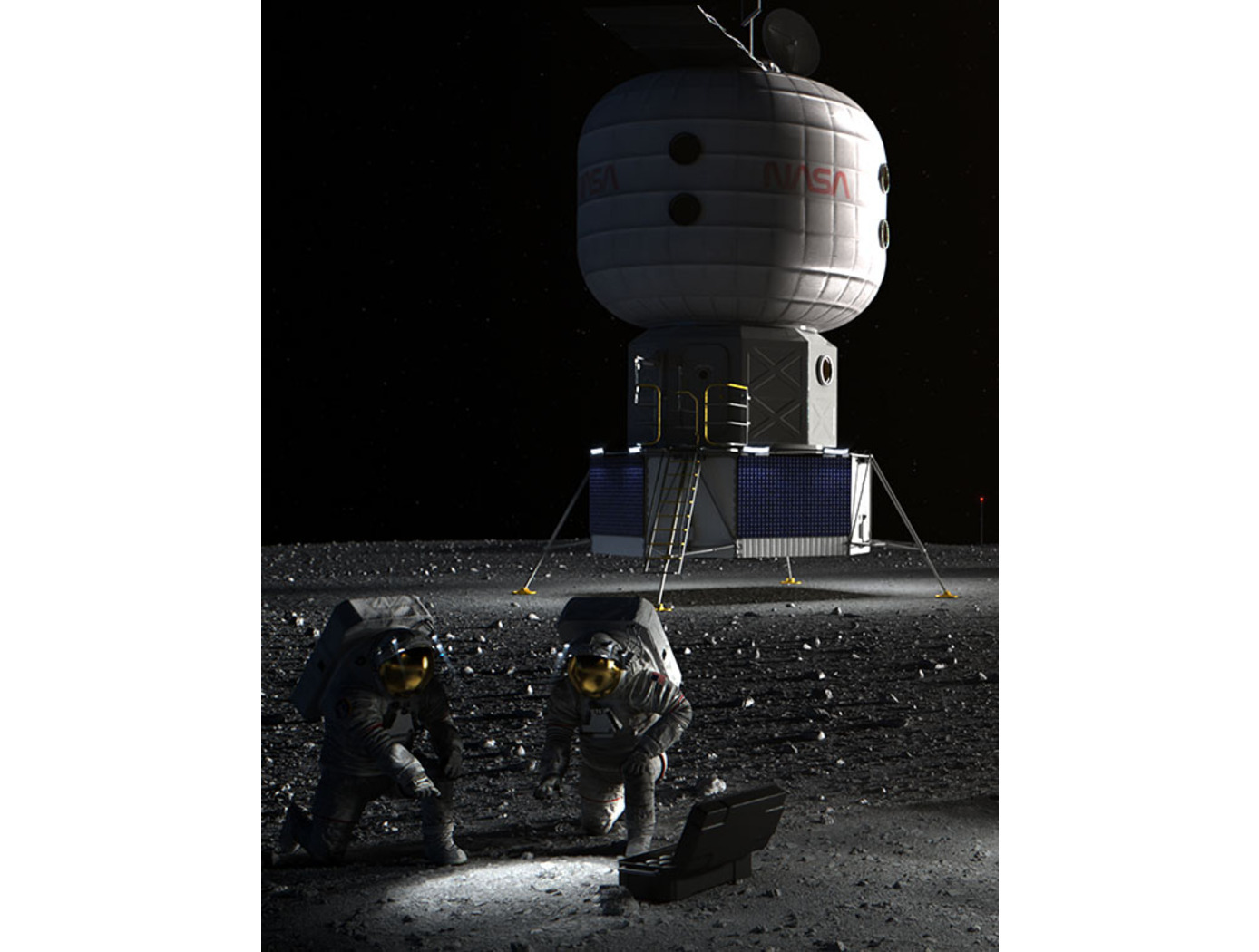
Regolith-Polymer 3D Printing
The invention consists of a 3D print head apparatus that heats and extrudes a regolith-polymer (or other) mixture as part of an additive manufacturing process. The technology includes a securing mechanism, hopper, nozzle, barrel, and heating system. The securing mechanism attaches to a wrist joint of a robotic arm. The hopper, connected to the securing mechanism, has a cavity and a lower aperture. The barrel is an elongated, hollow member with its first end connected to the hopper's lower aperture and its second end connected to the nozzle's upper aperture. The heating system is positioned along the barrel and comprises a heater, thermocouple, insulator, and heating controller. The heating controller activates the heater based on input signals received from the thermocouple.
The print head apparatus also includes a feed screw, drive shaft, and motor. The feed screw is positioned within the elongated hollow member of the barrel, and the drive shaft transmits torque to the feed screw. The motor provides torque to the drive shaft.
An agitator is secured to the drive shaft, facilitating the consistent movement and mixing of the regolith-polymer mixture in the hopper. The nozzle includes a tube with an open end and an occluded end, allowing the mixture to be extruded through the lower aperture.
The jointly developed 3D print head technology enables efficient, large-scale additive construction using in-situ resources, such as regolith or other materials. The innovation reduces the need for transporting materials from Earth and allows for sustainable habitat development on the Moon or Mars. Given its adaptability to different crushed rock-polymer materials, the invention may also serve as an alternative to conventional Portland concrete construction on Earth.
manufacturing
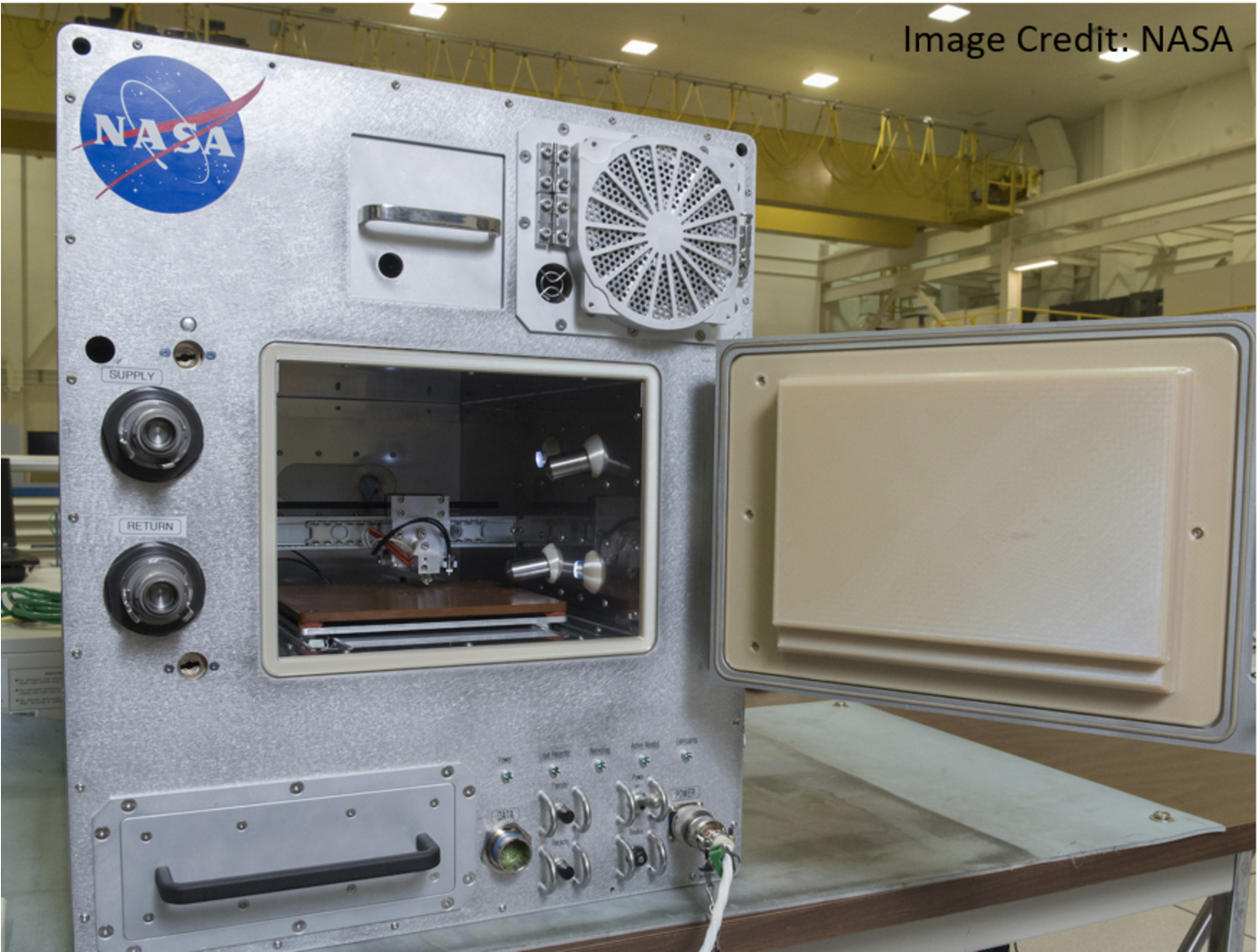
Recyclable Feedstocks for Additive Manufacturing
NASA's new technique for generating recyclable feedstocks for on-demand additive manufacturing employs the high-yield reversibility of the Diels-Alder reaction between maleimide and furan functionalities, utilizing the exceedingly favorable interaction between specific chemical functionalities, often termed "click reactions" due to their rapid rate and high efficiency. Integration of these moieties within a polymer coating on epoxy microparticle enables reversible assembly into macroscopic, free-standing articles. This click chemistry can be activated and reversed through the application of heat. Monomer species can be used to incorporate these functionalities into polyimide materials, which provide excellent mechanical, thermal, and electrical properties for space applications. Copoly (carbonate urethane) has been shown to be a viable coating material in the generation of polymer-coated epoxy microparticle systems and is amenable to being processed through a variety of approaches (e.g., filaments and slurries for 3D printing, compression molding, etc.). The polymeric materials are grown from the surfaces of in-house fabricated epoxy microparticles. The thermal and mechanical properties of the microparticles can be readily tuned by changes in composition.
There are a number of potential applications for this NASA technology ranging from use of these materials for recyclable/repurpose-able articles (structural, decorative, etc.) to simple children's toys. More demanding uses such as for replacement parts in complex industrial systems are also possible. For long term space missions, it is envisioned that these feedstocks would be integrated into secondary spacecraft structures such that no additional concerns would be introduced due to in-space chemical reactions and no additional mass would be required.
propulsion

A One-piece Liquid Rocket Thrust Chamber Assembly
The one-piece multi-metallic composite overwrap thrust chamber assembly is centrally composed of an additively manufactured integral-channeled copper combustion chamber. The central chamber is being manufactured using a GRCop42 or GRCop84 copper-alloy additive manufacturing technology previously developed by NASA. A bimetallic joint (interface) is then built onto the nozzle end of the chamber using bimetallic additive manufacturing techniques. The result is a strong bond between the chamber and the interface with proper diffusion at the nozzle end of the copper-alloy. The bimetallic interface serves as the foundation of a freeform regen nozzle. A blown powder-based directed energy deposition process (DED) is used to build the regen nozzle with integral channels for coolant flow. The coolant circuits are closed with an integral manifold added using a radial cladding operation. To complete the TCA, the entire assembly including the combustion chamber and regen nozzle is wrapped with a composite overwrap capable of sustaining the required pressure and temperature loads.