Coil-On-Plug Igniter for Reliable Engine Starts
Electrical and Electronics
Coil-On-Plug Igniter for Reliable Engine Starts (MSC-TOPS-105)
Compact igniter reduces thermal-vacuum corona discharge issues
Overview
Innovators at NASA Johnson Space Center have developed a coil-on-plug ignition system for integrated liquid oxygen (LOX)/liquid methane (LCH4) thermal-vacuum environment propulsion systems operating in a thermal vacuum environment. The innovation will help quell corona discharge issues and reduce overall mass. Corona discharge represents a local region surrounding a high-voltage conductor where air has undergone an electrical breakdown and become conductive due to ionization, allowing a charge to leak off the conductor and cause a possible malfunction.
NASA worked with commercial vendors to modify off-the-shelf automotive coil-on-plug spark plug systems for use with LOX/LCH4 igniters. The coil-on-plug configuration eliminates the bulky standalone coil-pack and conventional high-voltage spark plug cable by combining the coil and the spark plug into a single component. The test campaign successfully proved that coil-on-plug technology can enable integrated LOX/methane propulsion systems in future spacecraft.
The Technology
Spark-ignition devices have proven to be a high-reliability option for LOX/LCH4 ignition during development of the Integrated Cryogenic Propulsion Test Article (ICPTA) main and reaction control engines (RCEs); however, issues including spark plug durability (ceramic cracking) and corona discharge during simulated altitude testing have been observed, contributing to degraded spark output and no-light engine-start conditions. Innovators discovered that ignition system reliability could be improved and weight reduced by eliminating the traditional coil and spark plug wire. To achieve this result, engineers made the innovation by modifying an automotive coil-on-plug igniter to provide new high sparking energies at the point of combustion using low supply voltages. The coil was modified by vacuum-potting it into a threaded interface that mounts into existing spark plug ports on the ICPTA main engine and the RCEs. Engineers fabricated custom electrode tips that were thread-mounted into the potted coil body. Epoxy insulation was chosen with high dielectric strength to maintain insulation between the electrode and threaded adapter. Vacuum potting successfully prevented pressure or vacuum leakage into the coil body and maintained spark energy and location at the electrode tip. Successful hot-fire ignition was observed at sea-level, altitude, and thermal-vacuum for both ICPTA RCE and main engine igniters down to 10^-3 torr, which approaches the vacuum of cislunar space.
This technology is at technology readiness level (TRL) 7 (system prototype demonstration in an operational environment), and the related patent is now available to license. Please note that NASA does not manufacture products itself for commercial sale.
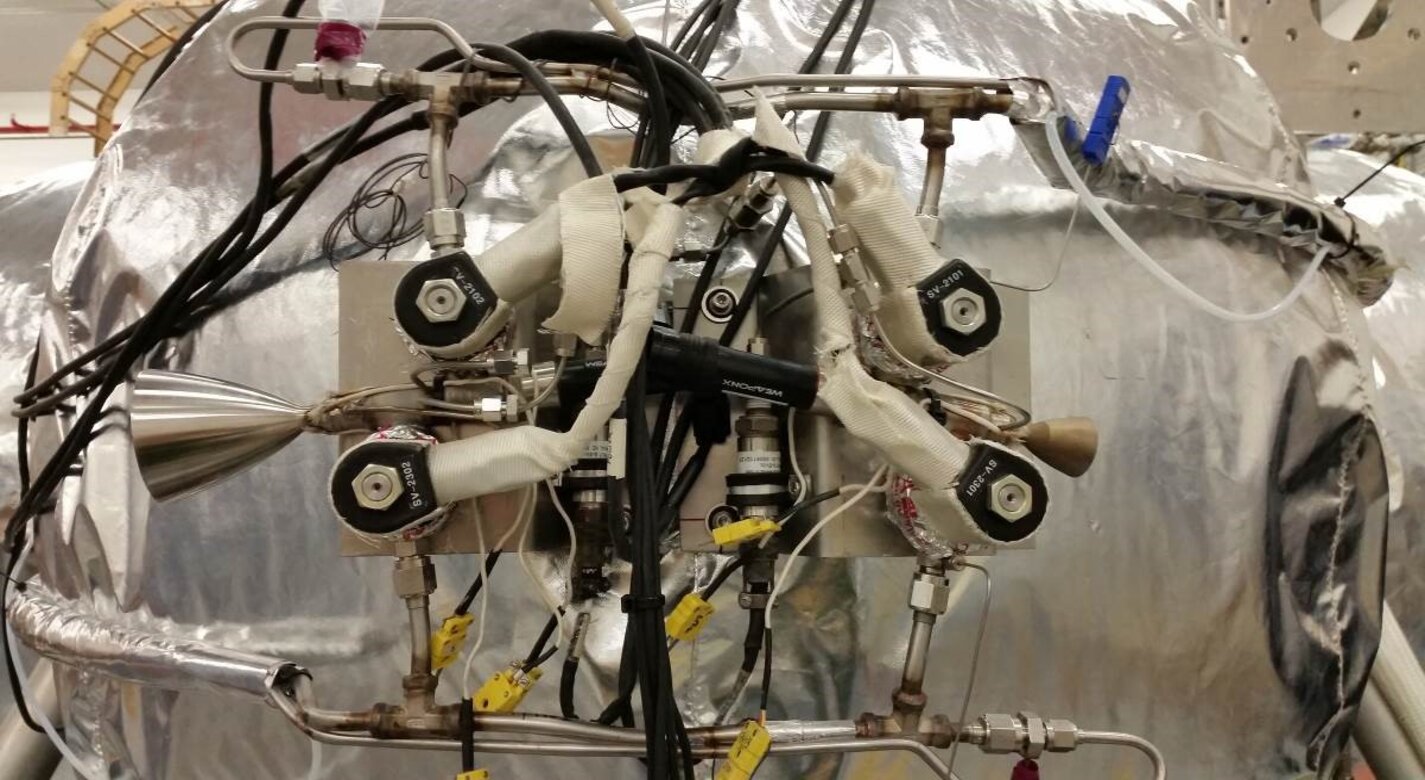
Benefits
- Compact: Design provides sparking energy at the point-of-use (directly to combustion chamber)
- Durable: Eliminates need for fragile-shielded and sealed high voltage conductors
- Low Mass: Reduces weighty exciter electronics and conductors
- Reliable: Low supply voltage operation reduces potential for corona discharge
Applications
- Thrusters: integrated cryogenic thruster development, testing, and spaceflight
- Burners: industrial flame-control systems and emissions-control flaring systems
Technology Details
Electrical and Electronics
MSC-TOPS-105
MSC-26893-1
Coil-On-Plug Ignition for LOX/Methane Liquid Rocket Engines in Thermal Vacuum Environments. 2017. AIAA. Melcher et al. (Link: https://ntrs.nasa.gov/citations/20170004966)
Tags:
|
|
Related Links:
|
Similar Results

High Efficiency Megawatt Motor
The HEMM is a is a wound-field partially superconducting machine that implements a combination of rotor superconducting and stator normal conductor elements, along with an integrated acoustic cryocooler, to achieve some of the benefits of a superconducting motor without the need for an external cryogenic system. The combination of the described elements allows a motor to be built which essentially operates like any other motor when viewed as a black box, but substantially enhanced performance can be achieved. The incorporation of superconductors on the rotor to create a high-level magnetic field results in a specific power and efficiency that could not be achieved any other way. The HEMM can achieve over 98% efficiency in a lightweight electric machine with an operating power greater than 1.4 MW, a specific power greater than 16 kW/kg (ratio to electromagnetic mass), and a rated operating speed of 6800 RPM. The HEMM can be used as both a motor or a generator, offering a wide range of applications including propulsion systems for hybrid aircraft, electric trains, hybrid cars, and turboelectric ships, as well as generator systems for wind turbines, power plants, or motors for other industrial machinery.

Premixed, High-Pressure, Multi-Fuel Burner
NASA Glenn's fully premixed burner design accomplishes the rapid mixing of the fuel and air flows while simultaneously providing backside impingement cooling to the burner face. This novel burner technology has been demonstrated to operate on hydrogen-air mixtures at pressures up to 30 bar, and at equivalence ratios (Phi) ranging from 0.15 to 5.0, but typically at equivalence ratios below 0.6 or above 2.0 for extended periods of time. It has also been demonstrated to work well with hydrogen-carbon monoxide fuel mixtures in a 1:1 mixture (by volume). The design provides a uniform zone of combustion products and temperatures, and is able to achieve complete and rapid mixing of the reactant gases over a distance as short as 5 mm, with the combustion products attaining a fully-reacted state within about 10 mm downstream of the burner face. Effectiveness of the mixing is not dependent on the use of hydrogen gas, therefore the system works well for other gaseous fuels such as methane, propane, or natural gas, in a fully premixed mode.
The design of the Glenn's burner is simple and straightforward to manufacture using conventional techniques. The modular design of the burner lends itself to scalability for larger power output applications. This burner is simple to operate and is robust for use in an industrial setting such as low-emissions stationary gas turbine engine, or for aircraft gas turbine engines.
ThermoArc Facilitates Low-Cost Li-Ion Battery Testing
For years, NASA and the battery industry have been improving passive propagation resistant (PPR) Li-ion battery cell technology by enhancing their material and design choices. These efforts help ensure that a single cell’s TR event does not overheat adjacent cells or the entire battery pack ultimately causing fire or explosion. To improve cell integrity, single cells within battery packs are triggered into TR so that the battery pack can be analyzed for its TR resistance.
ThermoArc operates by initiating a plasma arc, capable of delivering thermal energy up to 100W, to a very small (1mm diameter) section of the cell. The extremely localized high heat flux rapidly degrades a small section of the internal cell separator, resulting in a short circuit that leads to TR. This technology comprises several components: a high-turn-ratio step-up transformer capable of producing a minimum of 1,000 V upon the secondary winding, an H-bridge electronic circuit to drive the transformer on the primary side, two tungsten electrodes to deliver the plasma arc, and a power supply unit.
ThermoArc applications may exist in any Li-ion battery cell/pack testing application where TR must be induced in an individual cell. Such applications could include testing of PPR battery packs to ensure single cell runaway does not cause catastrophic damage, more general battery destructive testing designed to better understand battery failure states, or other experimental testing. Companies interested in licensing this innovation may include those that manufacture internal short-circuit (ISC) cells or other devices used to induce TR at the individual cell level, battery testing firms, and Li-ion battery manufacturers with a focus on Li-ion battery packs for critical applications.
ThermoArc is at a technology readiness level (TRL) 5 (component and/or breadboard validation in laboratory environment) and is now available for patent licensing. Please note that NASA does not manufacture products itself for commercial sale.

Anode Manifold Plug for Hall Effect Thrusters
Flow-restricting features in a Hall thruster anode manifold assembly, typically precision manufactured orifices, can contribute to significant flow non-uniformity if tolerances on the features are not properly controlled. Non-uniformity in flow distribution negatively impacts thruster performance. The anode assembly is usually a complex and expensive assembly to manufacture. Removing the flow restricting elements from the anode manifold structure in favor of modular insertable subcomponents (i.e., plugs) enables the use of more reliable and repeatable precision manufacturing techniques. The resulting components can be tested, characterized, and sorted for acceptance before being installed into the larger anode assembly (i.e., quality control can be performed at the subcomponent level). This may lead to increased performance and yield rate of the final assembly.
The flow restrictor plugs can be made in many different ways. The most basic flow restrictor takes the form of a precision hole machined into a cylinder, where the cylinder is then press fit into a hole drilled into the anode base. Alternate embodiments of the flow restrictor include precision machined nozzles, laminar flow elements, or sintered porous metal elements. The flow restrictor can also be made from a different material than the anode base, such as a precision ruby orifice contained in a metal carrier which is installed in a metal anode base. The plugs can be installed in a variety of ways, all of which create hermetic seals. Installation can include a press fit relying on plastic deformation or threading the plug component into the anode base. Welding on the top surface of the anode base can also be done to provide a robust hermetic seal.

High-Performance, Lightweight, Easy-to-Fabricate Heat Exchanger
Researchers at JPL have developed, built, and tested an innovative heat exchanger that offers reduced thermal expansion, increased structural strength, low pressure drop, and improved thermal performance while lowering the weight associated with typical heat exchangers. This innovation would benefit the commercial thermoelectric generator, aircraft, and industrial processing (i.e., glass, steel, petrochemical, cement, aluminum) industries by improving energy management/efficiency, reducing carbon dioxide emissions, and increasing system durability due to the reduced stress from thermal expansion.
The Problem
Thermoelectric generator systems require high-performance hot-side and cold-side heat exchangers to provide the temperature differential needed to transfer thermal energy while withstanding temperatures up to 650 °C. Because the hot-side heat exchangers must have a high heat flux, they are often made of metals such as stainless steel or Inconel® alloys. Although these materials can operate at high temperatures, resist corrosion, and are chemically stable, they also have several drawbacks: (1) Their lower thermal conductivity negatively affects their thermal performance. (2) Their higher thermal expansion leads to stresses that compromise system structural integrity. (3) Their high mass/volume reduces the power density of generator systems into which they are integrated. As a result, they are difficult to integrate into viable energy recovery systems. They also make the systems unreliable, non-durable, and susceptible to failures caused by thermal-structural expansion.
The Solution
JPL researchers chose to replace the metal in traditional heat exchangers with graphite, which offers an improved conductivity-to-density ratio in thermal applications as well as a low coefficient of thermal expansion. In addition, they used a mini-channel design to further increase thermal performance. Combining more advanced materials with the innovative thermal design has yielded significant improvements in performance. For example, a 200-cm3, 128-g version of JPL's exchanger successfully transported 1,100 W from exhaust at nearly 550 °C with approximately 20 W/cm2 thermal flux and a pressure drop of only 0.066 psi.
JPL's technology combines lightweight, high-strength graphite material with a mini-channel design that offers high thermal performance. Further development and testing are underway.
Inconel is a registered trademark of Special Materials Corporation.